Bài giảng Kỹ thuật ô tô
1.1. Tổng quan về ôtô.
1.1.1. Lịch sử phát triển ôtô
1.1.2. Phân loại ôtô.
a. Theo năng lƣợng chuyển động:
1. Động cơ xăng
2. Động cơ diesel
3. Động cơ lai (Hybrid)
4. Xe năng lượng điện
5. Động cơ lai loại tế bào
nhiên liệu
Hình 1.1. Các loại ô tô dùng năng lượng chuyển động
Xe sử dụng động cơ xăng
Loại xe ôtô này hoạt động bằng động
cơ sử dụng nhiêu liệu xăng. Do động
cơ xăng tạo ra công suất lớn đồng
thời nó có kích thước nhỏ gọn, nên
chúng được sử dụng rộng rãi trên
các loại xe du lịch. Ngoài ra người ta
còn sử dụng động cơ CNG, động cơ LPG
và động cơ chạy bằng cồn, chúng sử dụng các loại nhiên liệu khác nhau. CNG: Khí ga
nén tự nhiên, LPG: Khí ga hoá lỏng.
1. Động cơ, 2. Bình nhiên liệu
Xe sử dụng động cơ diesel
Hình 1.2. Ô tô dùng động cơ xăng2
Loại xe ôtô này hoạt động bằng
động cơ sử dụng nhiêu liệu diesel.
Do động cơ diesel tạo ra mômen
xoắn lớn và có tính kinh tế nhiên
liệu tốt, nên chúng được sử dụng
rộng rãi trên các loại xe tải và xe
đa dụng kiểu thể thao (SUV).
1. Động cơ, 2. Bình nhiên liệu.
Xe sử dụng động cơ lai (Hybrid)
Tóm tắt nội dung tài liệu: Bài giảng Kỹ thuật ô tô
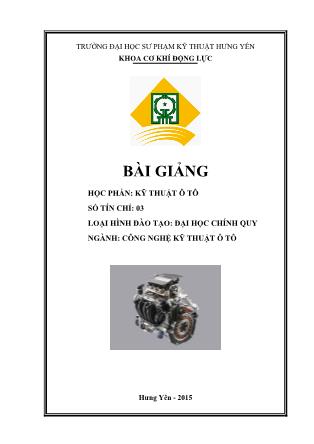
TRƯỜNG ĐẠI HỌC SƯ PHẠM KỸ THUẬT HƯNG YÊN KHOA CƠ KHÍ ĐỘNG LỰC BÀI GIẢNG HỌC PHẦN: KỸ THUẬT Ô TÔ SỐ TÍN CHỈ: 03 LOẠI HÌNH ĐÀO TẠO: ĐẠI HỌC CHÍNH QUY NGÀNH: CÔNG NGHỆ KỸ THUẬT Ô TÔ Hưng Yên - 2015 TRƯỜNG ĐẠI HỌC SƯ PHẠM KỸ THUẬT HƯNG YÊN KHOA CƠ KHÍ ĐỘNG LỰC ĐỀ CƯƠNG BÀI GIẢNG HỌC PHẦN: KỸ THUẬT Ô TÔ SỐ TÍN CHỈ: 03 LOẠI HÌNH ĐÀO TẠO: ĐẠI HỌC CHÍNH QUY NGÀNH: CÔNG NGHỆ KỸ THUẬT Ô TÔ Hưng Yên, năm 2015 1 CHƢƠNG 1: CẤU TẠO CHUNG CỦA ÔTÔ 1.1. Tổng quan về ôtô. 1.1.1. Lịch sử phát triển ôtô 1.1.2. Phân loại ôtô. a. Theo năng lƣợng chuyển động: 1. Động cơ xăng 2. Động cơ diesel 3. Động cơ lai (Hybrid) 4. Xe năng lượng điện 5. Động cơ lai loại tế bào nhiên liệu Hình 1.1. Các loại ô tô dùng năng lượng chuyển động Xe sử dụng động cơ xăng Loại xe ôtô này hoạt động bằng động cơ sử dụng nhiêu liệu xăng. Do động cơ xăng tạo ra công suất lớn đồng thời nó có kích thước nhỏ gọn, nên chúng được sử dụng rộng rãi trên các loại xe du lịch. Ngoài ra người ta còn sử dụng động cơ CNG, động cơ LPG và động cơ chạy bằng cồn, chúng sử dụng các loại nhiên liệu khác nhau. CNG: Khí ga nén tự nhiên, LPG: Khí ga hoá lỏng. 1. Động cơ, 2. Bình nhiên liệu Xe sử dụng động cơ diesel Hình 1.2. Ô tô dùng động cơ xăng 2 Loại xe ôtô này hoạt động bằng động cơ sử dụng nhiêu liệu diesel. Do động cơ diesel tạo ra mômen xoắn lớn và có tính kinh tế nhiên liệu tốt, nên chúng được sử dụng rộng rãi trên các loại xe tải và xe đa dụng kiểu thể thao (SUV). 1. Động cơ, 2. Bình nhiên liệu. Xe sử dụng động cơ lai (Hybrid) Xe ôtô sử dụng năng lượng điện (EV) Loại xe ôtô này sử dụng nguồn điện của ắc quy để vận hành môtơ điện thay vì sử dụng nhiên liệu, ắc quy cần được nạp lại điện. Loại xe này mang lại nhiều lợi ích, như không gây ô nhiễm và phát ra tiếng ồn thấp khi hoạt động. Hệ thống dẫn động bánh xe dùng điện 290V. 1. Bộ điều khiển công suất 2. Môtơ điện, 3. Ắc quy Động cơ Bộ đổi điện Hộp số Bộ chuyển đổi Ắc quy Hình 1.3. Ô tô dùng động cơ diesel Hình 1.4. Ô tô dùng động cơ lai Hình 1.5. Ô tô dùng động cơ điện 3 Xe sử dụng động cơ lai loại tế bào nhiên liệu (FCHV) Loại xe ôtô này sử dụng năng lượng điện tạo ra khi nhiên liệu hyđrô phản ứng với ôxy trong không khí sinh ra nước. Do nó chỉ thải ra nước, nó được coi là tốt nhất trong những loại xe có mức ô nhiễm thấp, và nó được tiên đoán sẽ trở thành nguồn năng lượng chuyển động cho thế hệ ôtô tiếp theo. Sơ đồ mô tả hệ thống Hybrid tế bào nhiên liệu của Toyota. 1. Bộ điều khiển công suất; 2. Mô tơ điện; 3. Bộ tế bào nhiên liệu 4. Hệ thống lưu hyđrô; 5. Ắc qui phụ b. Theo phƣơng pháp dẫn động Chủ yếu được chia thành các loại sau đây: • FF (Động cơ đặt trước – Bánh trước chủ động) • FR (Động cơ đặt trước – Bánh sau chủ động) • 4WD (4 bánh chủ động) • MR (động cơ đặt giữa - cầu sau chủ động). c. Có nhiều kiểu thân xe khác nhau: 1. Sedan: Đây là kiểu thân xe có ba khoang riêng biệt, 4 cửa, 4-5 chỗ ngồi. 2. Coupe: Đây là dòng xe 2 cửa thể thao, có 4 chỗ ngồi, luôn thể hiện được sức mạnh của động cơ. * (Roadster: là xe 2 cửa, 2 chỗ ngồi) 3. Lift back (Hatch back) Về cơ bản nó giống với coupe, là sự kết hợp khoang hành khách và khoang hành lý. Lắp cốp đồng thời là cửa sau. 4. Hardtop: Cơ bản giống Sedan, nhưng không có khung cửa sổ, và cộ trụ cửa. 5. Convertible: Đây là một kiểu Sedan hoặc Coupe, nhưng nó có khả năng thu gọn mui lại thành một chiếc mui trần. Hình 1.6. Ô tô sử dụng động cơ lai tế bào 4 2. Pickup: Đây là một loại xe tải nhỏ, có khoang máy kéo dài về phía trước ghế người lái. 7. Van and wagon: Kiểu xe này là sự kết hợp khoang hành khách và khoang hành ký, nó chứa được nhiều người và hành lý. Khoang hành khách thông với khoang hành lý. 1.2. Đặc điểm cấu tạo chung của ôtô 1. Động cơ (xăng hoặc Diesel) 2. Hệ thống truyền lực 3. Hệ thống lái 4. Hệ thống treo 5. Hệ thống phanh 6. Hệ thống điện (điện động cơ và điện thân xe) 7. Khung vỏ Hình 1.7. Các dạng kiểu xe theo hình dáng 5 CHƢƠNG 2: HỆ THỐNG TRUYỀN LỰC 2.1. Tổng quan về hệ thống truyền lực. Hệ thống truyền lực ( HTTL) của ôtô là hệ thống tất cả các cơ cấu nối từ động cơ tới bánh xe chủ động, bao gồm các cơ cấu truyền, cắt, đổi chiều quay, biến đổi các giá trị mô men truyền. Hiện nay, thường gặp các loại ôtô có động cơ đều là động cơ đốt trong sau hơn một thế kỉ từ khi ra đời và nhất là trong giai đoạn sau năm 1975 đến nay. Động cơ đốt trong đã không ngừng được hoàn thiện dẫn tới kết cấu của HTTL có biến động đáng kể. Những chỉ tiêu chính có thể kể đến là: Giảm tiêu hao nhiên liệu, tăng công suất, giảm độ ồn, tăng tốc độ lớn nhất của động cơ. Ảnh hưởng nhiều tới HTTL nhất là việc tăng tốc độ và tăng công suất của động cơ. Do đòi hỏi tăng tốc độ ô tô và những thát triển vượt bậc của kĩ thuật động cơ nên đã làm tăng tính đa dạng trong kết cấu HTTL . 2.1.1. Cấu tạo chung hệ thống truyền lực của ô tô. Hình 2.1. Cấu tạo hệ thống truyền lực ô tô 6 Hình 2.2. Cấu tạo một số hệ thống truyền lực trên ô tô 7 Thƣờng hệ thống truyền lực gồm các bộ phận sau: 1. Ly hợp 2. hộp số 3. Trục các đăng 4. Bộ vi sai 5. bán trục 6. Bánh xe chủ động 2.1.2. Phân loại hệ thống truyền lực Tuỳ theo các cách phân loại mà có các hệ thống truyền lực khác nhau, nhưng chủ yếu có mấy loại cơ bản sau: Theo vị trí đặt động cơ và cầu chủ động: - Loại FF : động cơ đặt trước, bánh trước chủ động - Loại FR : động cơ đặt trước, bánh sau chủ động - Loại hộp số thường - Loại hộp số tự động - Loại 4WD : hai cầu chủ động - Loại MR : động cơ đặt giưa cầu sau chủ động Theo loại ô tô: - Hệ thống truyền lực ô tô con - Hệ thống truyền lực ô tô khách - Hệ thống truyền lực ô tô tải a. Các hệ thống truyền lực của xe con: HL§ C C§C§ HL§ C H L § C HL§ C Hình 2.3. Hệ thống truyền lực ô tô con 8 H L DCC H L C CD HL P C C CD CD CD HL CD K C C DC DC DC Hình 2.4. Hệ thống truyền lực ô tô con có bộ chia công suất b. Hệ thống truyền lực ô tô khách Hình 2.4. Hệ thống truyền lực ô tô khách 9 c. Hệ thống truyền lực ô tô tải Hình 2.6. Hệ thống truyền lực ô tô tải 2.1.2.1. Hệ thống truyền lực với hộp số thƣờng. Cấu tạo chung: Hình 2.7. Cấu tạo chung hệ thống truyền lực thường 10 2.1.2.2. Hệ thống truyền lực tự động. Cấu tạo chung: Hình 2.8 . Cấu tạo chung hệ thống truyền lực tự động Hình 2.9. Các phương án hệ thống truyền lực tự động 11 2.2. Hệ thống truyền lực với hộp số thƣờng. 2.2.1. Ly hợp ( côn ) 2.2.1.1. Chức năng, yêu cầu và phân loại a. Chức năng - Ly hợp dùng để truyền mô men quay từ động cơ đến HTTL và đảm bảo đóng ngắt êm dịu, nhằm giảm tải trọng động và thực hiện trong thời gian ngắn nhất. - Khi chịu tải quá lớn, ly hợp đóng vai trò như là một cơ cấu an toàn nhằm tránh quá tải cho HTTL và động cơ. - Khi có hiện tượng cộng hưởng, ly hợp có khả năng dập tắt nhằm nâng cao chất lượng truyền lực. b. Phân loại Phân loại ly hợp dựa theo cách truyền mômen từ trục động cơ đến trục sơ cấp hộp số. Ly hợp được chia thành các loại như sau: Ly hợp ma sát: mômen truyền nhờ các bề mặt ma sát. Ly hợp thủy lực: mômen truyền nhờ chất lỏng. Ly hợp điện từ: mômen truyền nhờ tác dụng của từ trường nam châm điện. Ly hợp liên hợp: mômen truyền nhờ các loại liên kết trên. Tuỳ theo hình dạng và số lượng của đĩa ma sát mà chia ra các loại sau: Ly hợp một đĩa hay nhiều đĩa ma sát. Ly hợp hình nón. Ly hợp hình trống . Ly hợp hình côn. * Theo phương pháp phát sinh lực ép trên đĩa mà chia ra: Ly hợp lò xo gồm các lò xo trụ đặt ở xung quanh, lò xo đặt ở trung tâm, lò xo đĩa. Ly hợp ly tâm: Lực ép phát sinh ra do lực li tâm của khối trọng phụ ép vào. Ly hợp nửa li tâm: Lực ép phát sinh do lò xo cộng với lực li tâm của khối trọng quay. Theo kết cấu cần ly hợp thường đóng và ly hợp thường mở. c. Yêu cầu 12 Ly hợp phải đảm bảo: Truyền được hết mômen quay lớn nhất của động cơ trong mọi điều kiện sử dụng. Đóng ly hợp phải êm dịu, mômen quán tính phần bị động phải nhỏ để giảm hết tải trọng va đập lên các bánh răng của hộp số khi sang số. Mở ly hợp dứt khoát và nhanh để việc gài số êm dịu. Đảm bảo cho hệ thống truyền lực khi bị quá tải. Điều khiển dễ dàng, lực tác dụng lên bàn đạp mở ly hợp phải nhỏ. Các bề mặt ma sát thoát nhiệt tốt đảm bảo sự làm việc bình thường. Kết cấu đơn giản dễ điều chỉnh, bảo dưỡng dễ dàng 2.2.1.2. Cấu tạo, hoạt động của ly hợp ma sát khô và dẫn động ly hợp Ly hợp ma sát được hình thành trên cơ sở truyền lực qua các bề mặt ma sát. Muốn tạo nên lực ma sát cấu tạo của ly hợp phải có bộ phận lực ép giữa các bề mặt ma sát . Lực ma sát truyền từ bề mặt chủ động sang bề mặt bị động. Do vậy các bộ phận chính có tên là: Phần chủ động, bị động của, bộ phận tạo lực ép, bộ phận dẫn động điều khiển. a. Cấu tạo của ly hợp ma sát khô thƣờng đóng Hình 2.10. Cấu tạo ly hợp 1.Bánh đà 2.Bi đầu trục 3.Đĩa bị động 4.Cụm đĩa ép 2.Bu lông 7.Bi mở 8. Đòn Bánh đà của động cơ vừa là chi tiết của động cơ vừa là chi tiết của bộ phận chủ động. Bánh đà được bắt chặt trục khuỷu nhờ các bu lông lệch tâm, trên bề mặt có được gia công nhẵn làm bề mặt tựa của ly hợp. Mép ngoài của mặt bánh đà có các lỗ để bắt với vỏ ly hợp đồng thời có các chốt lệch tâm đảm bảo đồng tâm giữa bánh đà và vỏ, đảm bảo 13 khả năng truyền tốt mô men. Bánh đà thường làm bằng gang có khả năng truyền nhiệt tốt. Phần lõm phía trong có lỗ thoát dầu, mỡ, bụi các lỗ được khoan xiên tạo điều kiện cho dầu mỡ thoát ra ngoài theo lực ly tâm. Vỏ ly hợp làm bằng thép dập các lỗ để định tâm với bánh đà. Trên vỏ có các gờ lồi lõm để liên kết với đĩa ép, nhưng vẫn cho đĩa ép di chuyển dọc trục. Lỗ trong của vỏ có gờ nhỏ để giữ vòng lò xo, nhằm cố định lò xo ép dạng đĩa. Đĩa ép làm bằng gang có khả năng dẫn nhiệt tốt, mặt tiếp giáp với đĩa bị động được gia công nhẵn, mặt đối diện có các gờ lồi, một số gờ tạo nên các điểm tựa cho lò xo ép, một số gờ khác tạo nên các điểm truyền mô men xoắn giữa vỏ và đĩa ép. Đĩa bị động gồm moay ơ, các tấm ma xát trong, xương đĩa, giảm chấn, tấm ma sát, đinh tán. Đĩa bị động có kích thước và trọng lượng nhỏ. Hình 2.11. Đĩa ma sát. Moay ơ nằm trong vùng có then hoa di trượt trên trục bị động, phần ngoài của moay ơ có dạng hoa thị. Trên các phần trống có chổ để lắp lò xo trụ giảm chấn. Bên ngoài là hai vành thép lá, hai vành này được tán chặt trên xương đĩa nhờ các đinh tán bằng thép, nhưng cho phép dịch chuyển nhỏ đối với moay ơ. Giữa các vành thép và moay ơ có các tấm ma sát ép chặt nhờ đinh tán. Trên các vành thép có các ô cửa sổ nhỏ lồng vào đó và các lò xo giảm chấn. Một đầu của lõ xo giảm chấn tì vào moay ơ, đầu kia tì vào cửa sổ. Dịch chuyển nhỏ giữa moay ơ và các vành thép chỉ được thực hiện nhờ các lò xo bị biến dạng tiếp và đủ lớn để thắng lực ma sát giữa các tấm ma sát và vành thép. 14 Xương đĩa làm bằng thép đàn hồi, phần trong được tán với vành thép, phần ngoài tán với tấm ma sát của ly hợp. Xương đĩa được chế tạo bằng thép lá, được uốn vênh làn sóng, tạo điều kiện có thể biến dạng dọc trục nhỏ khi làm việc. Nhờ cấu trục như vậy, xương đĩa có khả năng đàn hồi dọc trục và theo chiều xoắn. Tấm ma sát làm bằng vật liệu chịu mài mòn và có hệ số ma sát ổn định, được tán vào xương đĩa nhờ hai hàng đinh tán bằng đồng. Trên bề mặt tấm ma sát có các rãnh hướng tâm và vòng tròn tăng khả năng tiếp xúc, tạo nên các rãch có khả năng tiếp bụi bẩn, thoát nhiệt ra ngoài. Bộ giảm chấn xoắn bao gồm: các lò xo trụ đặt trong các ô cửa sổ với lực ép ban đầu nhất định, các tấm ma sát ở vành trong bị ép giữa hai mặt của moay ơ và các vành thép nhờ đinh tán thép. Như vậy moay ơ và xương đĩa được nối đàn hồi và có thể nối cứng moay ơ và xương đĩa thì độ cứng của HTTL ở đây nhỏ hơn, tần số dao động riêng của hệ thống giảm đi, hạn chế được khả năng xuất hiện cộng hưởng ở tần số cao. Vì giới hạn của kích thước ở ô cửa sổ và đảm bảo truyền mômen xoắn nên không thể giảm thấp độ cứng của các lò xo giảm chấn, hiện tượng cộng hưởng ở tần số thấp được giảm nhiều nhờ các tấm ma sát ở vành trong moay ơ. Các tấm ma sát dịch chuyển tương đối với moay ơ và biến động năng thành nhiệt năng toả ra môi trường. Lò xo ép dạng màng được chế tạo bằng thép đàn hồi phần phía trong có các rãnh dài xẻ hướng tâm và được kết thúc bằng các lỗ tròn tạo điều kiện cho lò xo có khả năng biến dạng tốt, đồng thời tiếp xúc đều với ổ bi tì mở ly hợp. Đầu trong của lò xo được mài lõm tạo lên rãnh tròn nhằm giảm diện tích tiếp xúc với ổ bi mở và tạo điều kiện kiểm tra độ mòn của mép trong lò xo sau một thời gian làm việc nhất định. Vòng ngoài của lò xo được liên kết với đĩa ép nhờ vòng khoá bằng lò xo. Phần giữa lò xo liên kết với vỏ ly hợp cho phép lò xo làm việc như đòn có điểm tựa giữa. Lò xo ép ở trạng thái tự do có dạng hình nón, ở trạng thái lắp đã bị biến dạng để gây lên lực ép. Do trạng thái của vỏ và đĩa ép lên lò xo luôn luôn có xu hướng ép đĩa ép vào bánh đà. Khi mở ly hợp ổ bi tỳ ép đầu trong của lò xo làm tăng biến dạng đối với lò xo, nhưng lại kéo đầu ngoài của ly hợp vào với vỏ, như vậy đĩa ép có thể dịch chuyển ra tách các bề mặt làm việc. Lò xo bố trí như thế được gọi là lò xo màng dạng ép. 15 Lò xo trụ: tương tự như lò xo xupáp. Bề mặt sau của mâm ép là bề mặt có các lò xo trụ và đòn bẩy được gắn với cần ly hợp. Trong suốt quá trình hoạt động của ly hợp mâm ép di chuyển về phía trước và sau bên trong của ly hợp. Còn đòn bẩy thì được lắp bên trong mâm ép, nó được nâng lên và dịch chuyển bề mặt mâm ép ra xa so với bánh đà b. Nguyên lý làm việc của ly hợp một đĩa ma sát a. b. Hình 2.12. Nguyên lý làm việc của ly hợp lò xo màng. a.Trạng thái đóng ly hợp. b. Trạng thái mở ly hợp. 1.Bánh đà 2.Đĩa bị động 3.Đĩa ép 4.Lò xo màng 5.Bạc mở - Trạng thái đóng là trạng thái thường xuyên làm việc của ly hợp. Dưới tác dụng của lò xo ép : Đĩa ép, đĩa bị động và bánh đà động cơ bị ép sát vào nhau. Khi đó bánh đà, đĩa bị động (đĩa ma sát), đĩa ép, lò xo ép, vỏ ly hợp quay thành một khối. Mômen xoắn truyền từ động cơ tới bánh đà, qua các bề mặt ma sát truyền tới moay ơ đĩa bị động tới trục bị động ly hợp thực hiện chức năng truyền mô men xoắn từ động cơ tới hộp số. - Trạng thái mở là trạng thái làm việc không thường xuyên. Khi người lái tác dụng lên cơ cấu điều khiển. Đòn mở dịch chuyển bi mở đến tác dụng vào đĩa ép, bề mặt đĩa ép đẩy ra khỏi đĩa ly hợp, tách rời đĩa ma sát ra khỏi bánh đà. Do đó trục khuỷu động cơ có thể quay mà không làm quay đĩa ly hợp ở đầu vào trục hộp số. - Giữa các quá trình đóng mở, lược ép của lò xo thay đổi, xuất hiện trượt tương đối giữa cácề mặt ma sát. Quá trình này diễn ra tuy thời gian rất ngắn nhưng phát nhiệt rất lớn. Sự trượt quay gây nên mài mòn các bề mặt ma sát, đốt nóng các chi tiết ly hợp và có thể dẫn tới hư hỏng ly hợp. 16 c. Ly hợp dùng 2 đĩa ma sát. Khi cần 1 ly hợp làm việc với công suất lớn hơn như ... th¼ng ®øng cña xe t-¬ng øng. Dùa vµo hai th«ng sè ®ã, ng-êi ta so s¸nh víi ®å thÞ chuÈn xem xe thÝ nghiÖm ®¹t ®-îc ®é ªm dÞu chuyÓn ®éng ë thang bùc nµo. ThÝ dô trªn mét ®o¹n ®-êng nhÊt ®Þnh ta ®o ®-îc i=10 lÇn va ®Ëp/km; gia tèc th¼ng ®øng J = 4m/s2, trªn ®å thÞ ta x¸c ®Þnh ®-îc ®iÓm A, nh- vËy 242 xe thÝ nghiÖm cã møc ®é ªm dÞu chuyÓn ®éng theo chØ tiªu trªn cho ta ®-îc kÕt qu¶ nhanh, tuy nhiªn ch-a thËt chÝnh x¸c v× theo ph-¬ng ph¸p nµy ch-a tÝnh tíi thêi gian t¸c ®éng cña gia tèc th¼ng ®øng J. 9.2.2. Gia tốc dao động và thời gian tác động Khi ngåi l©u trªn « t«, ®Æc biÖt lµ ®èi víi ng-êi l¸i, dao ®éng sÏ lµm cho ng-êi mÖt mái dÉn ®Õn gi¶m n¨ng suÊt lµm viÖc hoÆc ¶nh h-ëng l©u dµi tíi søc khoÎ. C¸c thÝ nghiÖm kÐo dµi trong 8 giê liÒn cho thÊy nh¹y c¶m h¬n ®èi víi ng-êi lµ d¶i tÇn sè 4-8Hz. Trong d¶i tÇn sè nµy c¸c gi¸ trÞ cho phÐp cña toµn ph-¬ng gia tèc nh- sau: DÔ chÞu : 0,1 m/s2; G©y mÖt mái : 0,315 m/s2; G©y ¶nh h-ëng tíi søc khoÎ : 0,63 m/s2. 9.3. Khái niệm tính năng cơ động của ôtô TÝnh n¨ng c¬ ®éng cña « t« ®-îc hiÓu lµ kh¶ n¨ng chuyÓn ®éng cña chóng trong nh÷ng ®iÒu kiÖn ®-êng x¸ khã kh¨n vµ ®Þa h×nh phøc t¹p. Tïy theo ý ®å sö dông, ng-êi ta thiÕt kÕ « t« cã møc ®é kh¸c nhau vÒ tÝnh n¨ng c¬ ®éng. VÒ ph-¬ng diÖn nµy th× yªu cÇu thÊp nhÊt cho nh÷ng « t« sö dông chñ yÕu trong thµnh phè vµ trªn ®-êng quèc lé (®a sè « t« du lÞch vµ « t« chë kh¸ch) vµ yªu cÇu cao nhÊt cho nh÷ng « t« lµm viÖc trong lÜnh vùc n«ng nghiÖp, l©m nghiÖp vµ quèc phßng. TÝnh n¨ng c¬ ®éng cã ¶nh h-ëng quyÕt ®Þnh tíi mét trong nh÷ng chØ tiªu sö dông c¬ b¶n ®ã lµ n¨ng suÊt. TÝnh n¨ng c¬ ®éng phô thuéc vµo nhiÒu nh©n tè, trong ®ã chñ yÕu lµ chÊt l-îng kÐo - b¸m vµ c¸c th«ng sè h×nh häc cña « t«. Ngoµi ra nh÷ng ®Æc ®iÓm vÒ cÊu t¹o cña c¸c côm riªng biÖt cña « t« vµ tr×nh ®é thµnh th¹o nghÒ nghiÖp cña ng-êi l¸i còng cã ¶nh h-ëng tíi tÝnh n¨ng c¬ ®éng. 9.4. Các nhân tố ảnh hưởng đến tính năng cơ động của ôtô 9.4.1. Ảnh hưởng của các thông số hình học a) Kho¶ng s¸ng gÇm xe §ã lµ kho¶ng c¸ch gi÷a ®iÓm thÊp nhÊt cña gÇm xe víi mÆt ®-êng, ®-îc ký hiÖu lµ K. Kho¶ng c¸ch nµy ®Æc tr-ng cho ®é nhÊp nh« lín nhÊt cña mÆt ®-êng mµ xe cã thÓ v-ît qua ®-îc. ë nh÷ng « t« cã tÝnh n¨ng c¬ ®éng thÊp, K = 175210 mm (víi « t« du 243 lÞch) vµ K = 240275 mm (víi « t« t¶i). ë nh÷ng « t« cã tÝnh n¨ng c¬ ®éng cao, kho¶ng s¸ng nµy th-êng lín h¬n so víi « t« cã tÝnh n¨ng c¬ ®éng thÊp tõ 2050 mm vµ ë nh÷ng xe ®Æc biÖt kho¶ng s¸ng gÇm xe cã thÓ ®¹t tíi 400 mm hoÆc cao h¬n (xem h×nh 8.1). H×nh 9.2 : C¸c th«ng sè h×nh häc vÒ tÝnh n¨ng c¬ ®éng cña « t« b) B¸n kÝnh c¬ ®éng däc vµ c¬ ®éng ngang §Æc tr-ng cho h×nh d¹ng cña ch-íng ng¹i vËt mµ xe cã thÓ kh¾c phôc ®-îc. §©y lµ b¸n kÝnh cña nh÷ng vßng trßn tiÕp xóc víi c¸c b¸nh xe vµ ®iÓm thÊp nhÊt cña gÇm xe trong mÆt ph¼ng däc vµ ngang (h×nh 8.1). B¸n kÝnh c¬ ®éng däc 1 vµ b¸n kÝnh c¬ ®éng ngang 2 cµng nhá th× tÝnh n¨ng c¬ ®éng cña xe cµng tèt. ë nh÷ng « t« cã c«ng thøc b¸nh xe 4x2, b¸n kÝnh c¬ ®éng däc th-êng n»m trong giíi h¹n sau : §èi víi « t« du lÞch lo¹i nhá tõ 2,5 ®Õn 3,5 m ; lo¹i trung b×nh tõ 3,5 ®Õn 5,5 m vµ lo¹i lín tõ 5,5 ®Õn 8,5 m. §èi víi « t« t¶i, t¶i träng nhá 1 tõ 2,5 ®Õn 3,5 m ; t¶i träng trung b×nh tõ 3,0 ®Õn 5,5 m vµ t¶i träng lín tõ 5,0 ®Õn 6,0 m. ë nh÷ng « t« cã tÝnh n¨ng c¬ ®éng cao, b¸n kÝnh c¬ ®éng däc nhá h¬n so víi lo¹i « t« t-¬ng tù nh-ng cã tÝnh n¨ng c¬ ®éng thÊp ; trong ®a sè c¸c tr-êng hîp b¸n kÝnh nµy kh«ng v-ît qu¸ gi¸ trÞ 1 tõ 2,0 ®Õn 3,6 m. c) Gãc c¬ ®éng tr-íc vµ gãc c¬ ®éng sau Khi « t« cÇn ph¶i v-ît qua nh÷ng ch-íng ng¹i vËt lín nh- ®-êng hµo, gß ®èng, bê ruéng, cÇu phµ ... th× nh÷ng phÇn nh« ra sau giíi h¹n chiÒu dµi c¬ së cña xe cã thÓ va quÖt 244 vµo c¸c vËt c¶n. TÝnh n¨ng c¬ ®éng cña « t« ®Ó v-ît qua nh÷ng ch-íng ng¹i vËt nµy phô thuéc vµo trÞ sè cña c¸c gãc c¬ ®éng tr-íc vµ gãc c¬ ®éng sau (h×nh 8.1). §Ó n©ng cao tÝnh n¨ng c¬ ®éng cña xe ng-êi ta mong muèn lµm thÕ nµo ®Ó c¸c gãc nµy cã gi¸ trÞ lín theo kh¶ n¨ng cã thÓ. ë nh÷ng « t« hiÖn nay, c¸c gãc c¬ ®éng vµ cã nh÷ng gi¸ trÞ sau: Lo¹i xe ¤ t« du lÞch cã tÝnh n¨ng c¬ ®éng thÊp 2030 1520 ¤ t« t¶i cã tÝnh n¨ng c¬ ®éng thÊp 4050 2040 ¤ t« cã tÝnh n¨ng c¬ ®éng cao, kh«ng nhá h¬n 4550 3540 9.4.2. Ảnh hưởng của các thông số kết cấu a) ¶nh h-ëng cña b¸nh xe chñ ®éng tr-íc C¸c b¸nh xe bÞ ®éng tr-íc kh¾c phôc nh÷ng ch-íng ng¹i vËt th¼ng ®øng kÐm h¬n nhiÒu so víi c¸c b¸nh xe chñ ®éng. §iÒu nµy ®-îc gi¶i thÝch lµ c¸c b¸nh xe bÞ ®éng tú vµo ch-íng ng¹i vËt cßn b¸nh chñ ®éng cã xu h-íng kh¾c phôc nã. Trªn h×nh 8.2a biÓu thÞ s¬ ®å c¸c lùc t¸c dông lªn b¸nh xe bÞ ®éng phÝa tr-íc khi kh¾c phôc ch-íng ng¹i vËt th¼ng ®øng cã ®é cao h. C¸c lùc t¸c dông lªn b¸nh xe: T: Lùc ®Èy tõ khung tíi b¸nh xe R: Ph¶n lùc cña ch-íng ng¹i Z vµ X: Thµnh phÇn th¼ng ®øng vµ n»m ngang cña ph¶n lùc R Tõ ®iÒu kiÖn c©n b»ng cña b¸nh xe ta cã: Z = Gb , X = T 245 Gb bG AA X Z R 1 TT RZ X 1 00 r h CC P k k P' k P'' a) b) k M H×nh 9.3: S¬ ®å lùc t¸c dông lªn c¸c b¸nh xe tr-íc khi kh¾c phôc trë ng¹i th¼ng ®øng a) B¸nh xe bÞ ®éng, b) B¸nh xe chñ ®éng Theo s¬ ®å lùc trªn h×nh IX.2 ta cã: Z = X.tg 1 = T.tg 1; Gb = T.tg 1 hoÆc 1 tg G T b X¸c ®Þnh gi¸ trÞ tg 1 tõ tam gi¸c AOC: 2 1 ..2 hhr hr CA OC tg ; Do ®ã: hr hhr G tg G T b b 2 1 ..2 . ; Tõ c«ng thøc võa x¸c ®Þnh ®-îc chóng ta they r»ng khi h = r, lùc T = , cã nghÜa lµ khi gÆp ch-íng ng¹i vËt cã ®é cao h = r th× « t« kh«ng thÓ v-ît ®-îc, ngay c¶ khi c¸c b¸nh xe chñ ®éng phÝa sau cã lùc kÐo cùc ®¹i. Khi c¸c b¸nh xe tr-íc lµ b¸nh chñ ®éng, ngoµi lùc T vµ Gb, trªn b¸nh xe cßn cã m«men Mk do ®ã xuÊt hiÖn lùc Pk. Tõ Pk ta cã P’k vµ P’’k. Do t¸c ®éng cña lùc T vµ Gb ë ®iÓm tiÕp xóc A ph¸t sinh c¸c ph¶n lùc X vµ Z. Khi chiÕu tÊt c¶ c¸c lùc lªn trôc n»m ngang vµ th¼ng ®øng chóng ta nhËn ®-îc: T = X - P’k vµ Gb = Z + P”k Do sù n¶y sinh lùc phô P”k nªn cho phÐp b¸nh xe chñ ®éng dÔ dµng kh¾c phôc ®-îc nh÷ng ch-íng ng¹i cã ®é cao b»ng b¸n kÝnh b¸nh xe; cßn lùc P’k sÏ lµm gi¶m lùc c¶n chuyÓn ®éng X. 246 b) ¶nh h-ëng cña kÕt cÊu vi sai Vi sai cho phÐp c¸c b¸nh xe chñ ®éng quay víi tèc ®é kh¸c nhau. Tr-êng hîp ma s¸t trong nhá, cã thÓ xem nh- vi sai ph©n bè cho mçi b¸n trôc mét nöa gi¸ trÞ m«men xo¾n mµ nã nhËn ®-îc. Gi¸ trÞ cña m«men nµy l¹i bÞ giíi h¹n bëi sù tr-ît quay cña b¸nh xe chñ ®éng n»m trªn ®Êt cã hÖ sè b¸m nhá. Nh- vËy, vi sai d¬n gi¶n ë cÇu chñ ®éng lµm xÊu rÊt nhiÒu tÝnh n»n c¬ ®éng cña « t« v× trÞ sè cña lùc kÐo tiÕp tuyÕn ë c¸c b¸nh xe chñ ®éng ®-îc x¸c ®Þnh bëi c¸c b¸nh xe cã lùc b¸m rÊt nhá víi ®Êt, do ®ã, lùc kÐo tiÕp tuyÕn cã thÓ kh«ng ®ñ ®Ó kh¾c phôc lùc c¶n chuyÓn ®éng. Vi sai ph©n bè m«men xo¾n gi÷a c¸c b¸nh xe chñ ®éng nh- sau: M1 = 0,5.(M + Mr) M2 = 0,5.(M - Mr) ë ®©y: M1 vµ M2: m«men xo¾n cña b¸nh xe chñ ®éng quay chËm vµ nhanh; Mr: M«men ma s¸t trong vi sai, n¶y sinh khi cã sù chuyÓn ®éng t-¬ng ®èi cña c¸c chi tiÕt trong nã; M: M«men xo¾n ë b¸nh xe bÞ ®éng cña truyÒn lùc chÝnh. Theo quan ®iÓm vÒ tÝnh n¨ng c¬ ®éng th× ma s¸t trong vi sai lµ cã lîi, bëi v× nã cho phÐp truyÒn m«men lín cho b¸nh xe kh«ng tr-ît vµ nhá cho b¸nh xe bÞ tr-ît, nhê ®ã mµ cã thÓ kh¾c phôc ®-îc sù tr-ît quay. Lùc kÐo tiÕp tuyÕn tæng céng ë c¶ hai b¸nh xe chñ ®éng trong tr-êng hîp nµy ®¹t ®-îc gi¸ trÞ cùc ®¹i nh- sau: b r k r M PP minmax .2 ë ®©y: P min: Lùc kÐo ë b¸nh xe cã lùc b¸m nhá rb: B¸n kÝnh cña b¸nh xe chñ ®éng Ma s¸t trong vi sai ®¬n gi¶n kh«ng lín, v× vËy lùc kÐo tæng céng chØ t¨ng 4%6%. Trong c¸c vi sai cam vµ trôc vÝt cã bè trÝ trªn c¸c « t« cã tÝnh n¨ng c¬ ®éng cao, ma s¸t trong cña chóng lín h¬n nªn lùc kÐo tiÕp tuyÕn tæng céng cã thÓ t¨ng 10%15%. 247 Trªn c¸c lo¹i xe cÇn tÝnh n¨ng c¬ ®éng cao ng-êi ta còng th-êng sö dông nh÷ng vi sai cã ma s¸t trong lín. KÕt cÊu cña mét trong nh÷ng lo¹i nµy trªn h×nh IX.3a. Nã cã hai l y hîp ma s¸t: C¸c ®Üa 9 nèi víi c¸c b¸nh r¨ng b¸n trôc, c¸c ®Üa 10 nèi víi vá vi sai. C¸c ®Üa ly hîp ®-îc Ðp mét c¸ch tù ®éng nhê lùc chiÒu trôc, v× trªn c¸c trôc 7 cña vi sai vµ c¸c ®Üa Ðp 4 ®Òu cã mÆt nghiªng (gãc ). TrÞ sè cña lùc chiÒu trôc phô thuéc vµo m« men truyÒn qua vi sai. Ly hîp ma s¸t c¶n trë sù thay ®æi vËn tèc gãc cña mét trong hai b¸nh xe chñ ®éng, cßn m«men ma s¸t cña vi sai phô thuéc vµo: m«men truyÒn tíi nã, sè l-îng ®Üa ma s¸t vµ gãc nghiªng trªn c¸c trôc cña vi sai vµ ®Üa Ðp. Khi « t« chuyÓn ®éng th¼ng m«men xo¾n ®-îc truyÒn tíi c¸c b¸n trôc b»ng hai ®-êng: qua c¸c b¸nh r¨ng c«n cña vi sai vµ qua c¶ hail y hîp ma s¸t, ë tr-êng hîp nµy m«men ë c¸c b¸n trôc lµ b»ng nhaukhi lùc c¶n ë hai b¸nh xe chñ ®éng lµ nh- nhau (M1=M2). Khi « t« quay vßng (gi¶ sö quay vßng ph¶i) hoÆc khi chuyÓn ®éng trªn mÆt ®-êng cã hÖ sè b¸m ë b¸nh xe chñ ®éng bªn ph¶i lín h¬n bªn tr¸i th× cã sù ph©n bè l¹i m«men (h×nh IX.3c) vµ m«men truyÒn cho b¸n trôc bªn ph¶i lín h¬n bªn tr¸i (M2>M1). 1 2 3 4 5 6 7 10 9 8 A 6 M + M1 2 2M M1 21M + M M2 1M Nh×n theo A a) b) c) H×nh 9.4: CÊu t¹o cña vi sai cã ma s¸t trong lín nhê ly hîp ma s¸t vµ s¬ ®å ph©n bè m«men cho c¸c b¸n trôc a) CÊu t¹o vi sai: 1. vá hép vi sai; 2. b¸nh r¨ng hµnh tinh; 8. b¸nh r¨ng b¸n trôc; 9. ®Üa Ðp cña ly hîp; 5. b¸nh r¨ng bÞ ®éng cña truyÒn lùc chÝnh; 6. nh÷ng mÆt nghiªng trªn trôc vi sai vµ ®Üa Ðp; 7. trôc vi sai; 8. n¾p ®Ëy; 9. c¸c ®Üa ma s¸t cã then hoa trong; 10. c¸c ®Üa ma s¸t cã then hoa ngoµi. b) Khi xe chuyÓn ®éng th¼ng (M1 = M2). 248 Trªn mét sè « t« ng-êi ta cßn sö dông lo¹i vi sai gµi c-ìng bøc, viÖc gµi cøng vi sai víi c¸c b¸n trôc chØ ®-îc thùc hiÖn khi cã sù chªnh lÖch qu¸ lín vÒ hÖ sè b¸m gi÷a b¸nh xe chñ ®éng bªn ph¶i vµ bªn tr¸i. Trªn mÆt ®-êng tr¬n lÇy lo¹i vi sai nµy cho phÐp t¨ng ®¸ng kÓ lùc kÐo cña « t«. Sau khi ®· kh¾c phôc ®-îc nh÷ng chç tr¬n lÇy th× cÇn ph¶i më bé phËn gµi cøng ®Ó tr¸nh hiÖn t-îng tuÇn hoµn c«ng suÊt vµ h¹n chÕ sù mµi mßn lèp. 9.4.3. Ảnh hưởng của số cầu của ôtô Trong nh÷ng biÖn ph¸p kh¸c nhau ®-îc sö dông ®Ó n©ng cao chÊt l-îng kÐo - b¸m cña « t«, th× ®èi víi nh÷ng xe cÇn cã tÝnh n¨ng c¬ ®éng cao, ng-êi ta sö dông biÖn ph¸p t¨ng sè cÇu chñ ®éng. Víi c¸ch bè trÝ nµy, chÊt l-îng kÐo - b¸m cña « t« sÏ t¨ng rÊt nhiÒu nhê viÖc tËn dông tíi møc tèi ®a träng l-îng sö dông cña xe ®Ó biÕn thµnh träng l-îng b¸m. §Ó ®¬n gi¶n cho viÖc nghiªn cøu ta xÐt lo¹i xe bè trÝ theo s¬ ®å 4x9. §éng lùc häc kÐo cña xe cã 4 b¸nh chñ ®éng nh- trªn phô thuéc vµo s¬ ®å dÉn ®éng tíi c¸c trôc chñ ®éng, bëi v× cÊu tróc cña hÖ thèng dÉn ®éng cã ¶nh h-ëng tíi viÖc ph©n bè lùc kÐo gi÷a c¸c b¸nh xe tr-íc vµ sau. HiÖn nay ng-êi ta sö dông hai lo¹i dÉn ®éng: dÉn ®éng cøng vµ dÉn ®éng vi sai (h×nh 8.4). Lo¹i dÉn ®éng thø nhÊt ®-îc biÓu thÞ trªn s¬ ®å 8.4a. C¶ hai trôc cña « t« ®-îc nèi ®éng häc cøng víi nhau qua hép ph©n phèi 1, do ®ã mèi quan hÖ ®· x¸c ®Þnh gi÷a vËn tèc gãc cña chóng lµ kh«ng ®æi trong qu¸ tr×nh lµm viÖc. Lo¹i dÉn ®éng thø hai ®-îc biÓu thÞ trªn s¬ ®å 8.4b. Thay vµo vÞ trÝ cña hép ph©n phèi 1 lµ hép vi sai 2, do kÕt qu¶ t¸c ®éng cña hiÖu øng vi sai nªn mèi quan hÖ gi÷a vËn tèc gãc cña hai trôc cã thÓ thay ®æi trong qu¸ tr×nh lµm viÖc. §Æc tÝnh kh¸c nhau vÒ mèi quan hÖ ®éng häc gi÷a c¸c trôc còng g©y nªn sù kh¸c nhau trong viÖc ph©n bè m«men chñ ®éng cho chóng. 249 ë nh÷ng « t« cã dÉn ®éng cøng cña hai trôc chñ ®éng th× hÇu nh- lu«n lu«n cã sù kh«ng t-¬ng øng ®éng häc gi÷a c¸c b¸nh xe tr-íc vµ sau. Khi chuyÓn ®éng th¼ng trªn mÆt ®-êng ph¼ng, sù kh«ng t-¬ng øng ®éng häc ®-îc biÓu thÞ ë chç: tèc ®é vßng lý thuyÕt cña c¸c b¸nh tr-íc vµ sau cã thÓ kh¸c nhau, trong khi c¸c trôc cña chóng l¹i ®-îc g¾n chÆt víi khung xe vµ ph¶i di chuyÓn víi cïng mét vËn tèc tÞnh tiÕn. §¶m b¶o sù ®ång bé tuyÖt ®èi vËn tèc vßng cña c¸c b¸nh xe tr-íc vµ sau thùc tÕ lµ kh«ng thÓ thùc hiÖn ®-îc, v× b¸n kÝnh cña c¸c b¸nh xe cã thÓ sai lÖch so víi tÝnh to¸n do nhiÒu nguyªn nh©n g©y nªn nh-: sai sè chÕ t¹o, ®é mµi mßn cña lèp, ¸p suÊt kh«ng khÝ trong lèp, sù dao ®éng cña t¶i träng th¼ng ®øng t¸c ®éng lªn b¸nh xe, Hép sè 1 a) b) Hép sè 1 2 H×nh 9.5: S¬ ®å dÉn ®éng c¸c trôc chñ ®éng a) DÉn ®éng cøng; b) DÉn ®éng vi sai Trªn ®-êng vßng, sù kh«ng t-¬ng øng ®éng häc ®-îc t¹o nªn ë chç: khi « t« chuyÓn ®éng trªn ®-êng cong th× mçi trôc cña chóng ph¶i cïng lóc ®i ®-îc nh÷ng qu·ng ®-êng kh¸c nhau, nh-ng hai trôc cña xe ®-îc xem nh- g¾n víi khung l¹i di chuyÓn víi cïng mét vËn tèc tÞnh tiÕn. 9.5. Các biện pháp nâng cao tính năng cơ động của ôtô §Ó n©ng cao tÝnh n¨ng c¬ ®éng cña « t«, hiÖn nay ng-êi ta sö dông c¸c biÖn ph¸p sau ®©y: a) N©ng cao chÊt l-îng ®éng lùc häc cña « t« 250 ChÊt l-îng ®éng lùc häc cã liªn quan chÆt chÏ víi kh¶ n¨ng kh¾c phôc nh÷ng ®é dèc vµ nh÷ng ®o¹n ®-êng cã lùc c¶n l¨n lín, v× vËy nh÷ng xe cã tÝnh n¨ng c¬ ®éng cao cÇn ph¶i cã nh÷ng trÞ sè lùc kÐo t-¬ng øng ë c¸c b¸nh xe chñ ®éng. §Ó n©ng cao chÊt l-îng ®éng lùc häc cÇn n©ng cao c«ng suÊt riªng cña xe, t¨ng tû sè truyÒn cùc ®¹i cña hÖ thèng truyÒn lùc, sö dông lo¹i hÖ thèng truyÒn lùc cho phÐp chuyÓn sè mµ kh«ng cÇn ng¾t dßng c«ng suet truyÒn ®Õn c¸c b¸nh xe chñ ®éng. b) Gi¶m ¸p suÊt riªng phÇn lªn bÒ mÆt ®-êng Do « t« lo¹i nµy th-êng ph¶i di chuyÓn trªn nh÷ng mÆt tùa mÒm, ë ®ã c¸c phÇn tö ®Êt cã mèi liªn kÕt yÕu, lùc c¶n l¨n lín vµ lùc b¸m nhá. V× vËy khi t¨ng ¸p suÊt riªng cña « t« lªn bÒ mÆt tùa sÏ lµm t¨ng vÕt lón cña b¸nh xe, lùc c¶n l¨n cµng t¨ng vµ dÉn ®Õn t×nh tr¹ng xe cã thÓ bÞ sa lÇy. BiÖn ph¸p gi¶m ¸p suÊt riªng lªn bÒ mÆt tùa lµ: Ph©n bè hîp lý träng l-îng cña xe lªn c¸c trôc, t¨ng sè trôc, sö dông nh÷ng lèp cã kÝch th-íc vµ profin t-¬ng øng, gi¶m ¸p suet kh«ng khÝ trong lèp hoÆc ®iÒu chØnh ®-îc ¸p suet trong khi xe ch¹y tïy theo ®iÒu kiÖn ®-êng x¸. C«ng tiªu hao cho c¸c b¸nh xe cña « t« khi xe chuyÓn ®éng trªn ®Êt mÒm tû lÖ víi ®é biÕn d¹ng d- cña ®Êt, cã nghÜa lµ phô thuéc vµo bÒ réng vµ ®é s©u cña c¸c vÕt lón cña b¸nh xe. ChÝnh v× vËy mµ ®é trïng cña c¸c vÕt b¸nh cã ý nghÜa quan träng ®èi víi c«ng tiªu hao cho sù di chuyÓn cña « t«. §é biÕn d¹ng nhá nhÊt cña ®Êt sÏ nhËn ®-îc khi cã ®é trïng chÝnh x¸c cña c¸c vÕt b¸nh sau vµ b¸nh tr-íc. c) N©ng cao chÊt l-îng b¸m cña « t« Trªn nh÷ng mÆt ®-êng tr¬n tr-ît, tÝnh n¨ng c¬ ®éng cña xe phô thuéc rÊt nhiÒu vµo kh¶ n¨ng b¸m cña c¸c b¸nh xe chñ ®éng víi bÒ mÆt tùa. V× vËy ®Ó n©ng cao chÊt l-îng b¸m ng-êi ta th-êng ph¶i sö dông c¸c lo¹i lèp cã d¹ng hoa lèp ®Æc biÖt vµ nh÷ng trang bÞ kh¸c ®Ó chèng l¹i sù tr-ît cña c¸c b¸nh xe, sö dông nh÷ng cumk vi sai cã ma s¸t trong lín, côm vi sai tù ®éng gµi hoÆc gµi cøng c-ìng bøc thay cho côm vi sai th«ng th-êng vµ cuèi cïng lµ t¹o nªn nh÷ng xe cã nhiÒu cÇu chñ ®éng ®Ó sö dông tèi ®a träng l-îng cña xe thµnh träng l-îng b¸m. d) T¹o ra c¸c th«ng sè h×nh häc thÝch hîp Nh÷ng « t« cã tÝnh n¨ng c¬ ®éng cao th-êng ph¶i lµm viÖc trªn nh÷ng lo¹i ®Þa h×nh phøc t¹p, v× vËy chóng cÇn ph¶i cã nh÷ng th«ng sè h×nh häc vÒ tÝnh n¨ng c¬ ®éng ®Ó khi di chuyÓn kh«ng bÞ va quÖt vµo nh÷ng ch-íng ng¹i vËt trªn ®-êng.
File đính kèm:
bai_giang_ky_thuat_o_to.pdf