Đề tài Nghiên cứu tổng hợp các chất hoạt động bề mặt để sản xuất chất tẩy rửa thân thiện với môi trường dùng trong xử lý vải sợi phục vụ cho công nghiệp dệt may
PHẦN 1. MỞ ĐẦU
Hiện nay, công nghiệp dệt may đang mang lại cho nền kinh tế nước ta một
nguồn lợi to lớn, nhất là trong thời kỳ hội nhập. Kim ngạch thu được cho ngân
sách nhà nước từ xuất khẩu dệt may hàng năm lên tới hàng tỷ USD. Tuy nhiên
hàng năm, nước ta phải nhập một lượng lớn hoá chất để xử lý làm sạch vải sợi
trước khi nhuộm mầu, in hoa và các công đoạn sản xuất vải tiếp theo. Trong số
hoá chất đó, các chất hoạt động bề mặt để tẩy dầu mỡ, chất béo, tạp chất trên
vải, chất giũ hồ, chất ngấm chiếm một lượng lớn. Có nhiều nguyên nhân để vải
sợi bị nhiễm bẩn dầu mỡ, tạp chất, nhưng thông thường là các lý do sau:
-Khi chuốt sợi, người ta phải cho parafin hoặc dầu vào để tránh cho sợi bị xù
lông và để các sợi không dính vào nhau trong quá trình dệt.
-Đối với các loại sợi poliamit, poliester do có khả năng sinh tĩnh điện cao nên
gây khó khăn cho quá trình dệt, để hạn chế hiện tượng này, khi dệt người ta
thường phải cho thêm chất bôi trơn là dầu khoáng.
-Khi dệt thông thường cho thêm hồ tinh bột.
-Trong sợi bông luôn có các tạp chất như chất béo, sáp, lignin, hợp chất chứa
nitơ, tro, pectin, các tạp chất cơ học do mảnh hạt lẫn vào.
-Dầu mỡ từ máy dệt có thể thâm nhập vào trong quá trình dệt, gây nhiễm bẩn
cục bộ cho sợi hoặc các tấm vải thành phẩm.
-Các chất bẩn từ môi trường bám dính vào vải và sợi trong quá trình dệt và vận
chuyển.
Đến công đoạn nhuộm mầu và in hoa, tất cả các chất bẩn nêu trên phải được tẩy
sạch; nếu không thì quá trình nhuộm sẽ không có hiệu quả do các loại chất này
ngăn cản sự thấm nước và mầu nhuộm, không cho thuốc nhuộm khuyếch tán
vào vải, gây loang mầu.
Hiện nay trong cả nước ta có khoảng 1000 nhà máy dệt lớn nhỏ với hơn
10.500 máy dệt. Lớn nhất là nhà máy dệt của Vinatex có công suất 3000 tấn vải/
ngày; nhỏ như xí nghiệp dệt nhuộm Trung thư cũng có đến 6-7 tấn vải /ngày.
Theo thống kê, trong một năm, trung bình nước ta sản xuất ra hơn 23 triệu tấn
vải. Lượng vải này cần đến khoảng 5000 tấn chất HĐBM để xử lý làm sạch.Tất
cả các chất HĐBM này đều phải nhập ngoại với giá không nhỏ: 2-3 USD/1Kg.
Như vậy ta sẽ không chủ động được về sản phẩm. Không những thế, các loại
hoá chất xử lý nhập ngoại cộng với lượng dư thừa thuốc nhuộm đã và đang gây
ô nhiễm môi trường trầm trọng. Nước thải của công nghiệp dệt nhuộm là một
trong những loại nước thải độc hại nhất ngày nay.
Trước đây trong công nghiệp dệt chủ yếu sử dụng các phương pháp tiền xử lý
vải sợi cơ học hoặc các loại hoá chất nhập ngoại không thân thiện môi trường.
Thông thường phải sử dụng 3 loại hóa chất trong quá trình sản xuất vải, đó là:
Chất tẩy dầu, chất giũ hồ, chất ngấm. Thông thường các hóa phẩm đó phải nhập
từ nước ngoài, chủ yếu của Hàn Quốc, Đài Loan. Một điểm đáng lưu ý là để sản
xuất vải thành phẩm, không thể thiếu bất kể thành phần nào trong số đó, tức là2
nếu nhập thiếu một trong 3 chất đó thì sẽ không thể hoàn thiện được qui trình.
Các xí nghiệp dệt nhuộm lại thiếu chủ động và phụ thuộc nơi cung cấp sản
phẩm.Giai đoạn nấu tẩy để giũ hồ phải thực hiện ở nhiệt độ tương đối cao, gây
tốn kém năng lượng và phức tạp trong công nghệ. Mỗi giai đoạn khác như tẩy
dầu, nhuộm đều phải thay đổi đơn phối chế vì các quá trình đó sử dụng các hóa
phẩm khác nhau. Bên cạnh đó, nước thải nhuộm khi sử dụng các chất truyền
thống cũ gây ô nhiễm trầm trọng
Tóm tắt nội dung tài liệu: Đề tài Nghiên cứu tổng hợp các chất hoạt động bề mặt để sản xuất chất tẩy rửa thân thiện với môi trường dùng trong xử lý vải sợi phục vụ cho công nghiệp dệt may
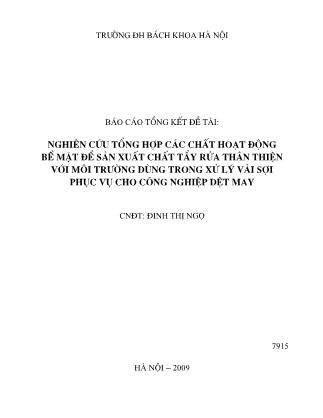
Tr−êng §H B¸ch khoa Hµ Néi B¸o c¸o tæng kÕt ®Ò tµi: Nghiªn cøu tæng hîp c¸c chÊt ho¹t ®éng bÒ mÆt ®Ó s¶n xuÊt chÊt tÈy röa th©n thiÖn víi m«i tr−êng dïng trong xö lý v¶i sîi phôc vô cho c«ng nghiÖp dÖt may Cn®t: §inh ThÞ Ngä 7915 Hà néi – 2009 MỤC LỤC Trang Mục lục Các chữ viết tắt Danh mục các bảng Danh mục các hình vẽ và đồ thị Báo cáo khoa học Phần 1. MỞ ĐẦU 1 Phần 2. NỘI DUNG KHOA HỌC Đà THỰC HIỆN Chương 1. Tổng quan lý thuyết 4 1.1 Tổng quan về các loại vải sợi 4 1.1.1 Giới thiệu chung về các loại vải sợi 4 1.1.2 Cấu trúc và tính chất hóa lý các loại vải sợi 6 1.1.3 Quy trình xử lý vải sau khi dệt 8 1.2 Chất tẩy rửa, chất hoạt động bề mặt 9 1.2.1 Thành phần chất tẩy rửa 10 1.2.2 Một số tính chất quan trọng của dung dịch chất tẩy rửa 21 1.2.3 Cơ chế tẩy rửa 22 1.2.4 Các loại chất tẩy rửa vải sợi thông dụng 26 1.3 Tổng quan về dầu thực vật 26 1.3.1 Dầu thực vật và tính hoạt động bề mặt 26 1.3.2 Giới thiệu về tinh dầu thông 27 1.3.3 Các phương pháp biến tính dầu thông 28 Chương 2. Thực nghiệm 31 2.1 Nghiên cứu tính chất hóa lý của bề mặt vải sợi 31 2.2 Lựa chọn và phân tích thành phần nguyên liệu 31 2.3 Tổng hợp chất hoạt động bề mặt từ dầu thông bằng phương pháp sunfat hóa 32 2.4 Tổng hợp chất hoạt động bề mặt từ dầu thông bằng phương pháp hydrát hóa 33 2.5 Tổng hợp chất hoạt động bề mặt từ dầu thông bằng phương pháp oxi hóa 33 2.6 Phối trộn chế tạo chất tẩy rửa 34 2.7 Xác định các thông số hóa lý của sản phẩm 35 2.8 Các phương pháp nghiên cứu 46 2.9 Thử nghiệm xử lý tẩy dầu tại nhà máy 50 Chương 3. Thảo luận kết quả 3.1 Nguyên nhân nhiễm bẩn dầu mỡ trong công nghiệp dệt 53 3.2 Xác định nhu cầu về xử lý vải sợi và nghiên cứu lựa 53 chọn dầu thực vật có hoạt tính bề mặt 3.3 Nghiên cứu tính chất hóa lý của bề mặt vải sợi và cơ chế nhiễm bẩn dầu mỡ 58 3.4 Nghiên cứu tổng hợp chất hoạt động bề mặt trên cơ sở dầu thông 69 3.4.1 Khái quát chung 69 3.4.2 Tổng hợp chất HĐBM từ DT bằng phương pháp sunfat hóa 72 3.4.3 Tổng hợp chất HĐBM từ DT bằng phương pháp hydrat hóa 83 3.4.4 Tổng hợp chất HĐBM từ DT bằng phương pháp oxi hóa 89 3.4.5 Nghiên cứu tổng hợp chất HĐBM trên thiết bị lớn 97 3.5 Chế tạo hỗn hợp chất tẩy rửa có hoạt tính cao 101 3.5.1 Chế tạo chất tẩy rửa từ dầu thông sunfat hóa 101 3.5.2 Chế tạo chất tẩy rửa từ dầu thông hydrat hóa 104 3.5.3 Quy trình tẩy trắng 112 3.6 Nghiên cứu cơ chế tẩy sạch vải sợi 115 3.7 Nghiên cứu thử nghiệm trong nhà máy 127 Phần 3. CÁC KẾT QUẢ Đà ĐẠT ĐƯỢC A Các sản phẩm “dạng I” 135 B Các sản phẩm “dạng II” 136 C Các sản phẩm “dạng III” 145 Kết luận khoa học 149 Kết luận theo nhiệm vụ đã ký kết 151 Hướng phát triển tiếp theo của Đề tài và Kiến nghị 152 Trang tài liệu tham khảo 153 Phụ lục Từ trang 161 CÁC CHỮ VIẾT TẮT TRONG BÁO CÁO - DT: Dầu thông. - CTR: Chất tẩy rửa. - DTBT: Dầu thông biến tính. - SCBM: Sức căng bề mặt. - St: Stốc. - cSt: Centistôc. - SEM: Kính hiển vi điện tử quét. - GC-MS: Sắc ký khí kết hợp khối phổ. - IR: Phổ hồng ngoại. - HĐBM: Chất hoạt động bề mặt. - NI: Chất hoạt động bề mặt không ion. - HLB: Chỉ số cân bằng tính ưa dầu – nước. - CMC: Nồng độ Mixen tới hạn. - ABS: Alkyl Benzen Sunfonat. - LAS: Linear Alkyl Benzen Sulfonat. - LES: Alkyl Ete Sulfat - TEA: Trietylamin. - COT : Vải coton - PES: Polyeste. - PET: Poly Ethylene Terephtalate, gọi là sợi PET - COT/PET : Vải pha giữa coton và polieste - APG: Alkylpoliglucosit - TWEEN Chất hoạt động bề mặt dạng sorbitan - EDTA Etylen Diamin Tetra-Axetic - MGDA Metyl Glycin Diaxetic Axit - KL Khối lượng - PTL Phân tử lượng DANH MỤC CÁC BẢNG TT Tên bảng Trang Bảng 1.1 Đặc tính của các loại sợi dệt khác nhau 6 Bảng 1.2 Thành phần xơ bông chín tính theo % chất khô tuyệt đối 7 Bảng 1.3 Mối quan hệ giữa khả năng phân tán trong nước và giá trị HLB 22 Bảng 1.4 Tính chất vật lý của các cấu tử chính trong dầu thông 27 Bảng 1.5 Tính chất vật lý của α -pinen và β -pinen 28 Bảng 2.1 Tính chuẩn số 48 Bảng 2.2 Tính giá trị tương ứng và chuẩn số Fisher 49 Bảng 2.3 Các thí nghiệm tại tâm 50 Bảng 3.1 Định tính về khả năng tẩy rửa của các loại dầu thực vật 54 Bảng 3.2 Kết quả nghiên cứu hoạt tính tẩy rửa của hỗn hợp dầu thông và dầu dừa 55 Bảng 3.3 Kết quả nghiên cứu hoạt tính tẩy rửa của hỗn hợp dầu thông và dầu cam quýt 55 Bảng 3.4 Kết quả nghiên cứu hoạt tính tẩy rửa của hỗn hợp dầu thông và dầu cám 56 Bảng 3.5 Kết quả nghiên cứu hoạt tính tẩy rửa của hỗn hợp dầu thông và dầu sở 56 Bảng 3. 6 Kết quả nghiên cứu ảnh hưởng của chất hoạt động bề mặt LAS 56 Bảng 3.7 Kết quả nghiên cứu hoạt tính tẩy rửa của hỗn hợp dầu thông và dầu cam quýt 57 Bảng 3.8 Kết quả nghiên cứu ảnh hưởng của axit sucinic 57 Bảng 3.9 Đường kính mao quản của xơ polyeste và xơ bông 68 Bảng 3.10 Đường kính động học phân tử của một số hợp chất hydrocacbon có trong dầu 69 Bảng 3. 11 Các thông số hóa lý của dầu thông 71 Bảng 3.12 Hoạt tính tẩy sạch đối với các loại vải khác nhau 71 Bảng 3.13 Ảnh hưởng của nồng độ axit H2SO4 đến phản ứng sunfat hóa dầu thông 72 Bảng 3.14 Ảnh hưởng của lượng H2SO4 đến phản ứng sunfat hóa dầu thông 73 Bảng 3.15 Ảnh hưởng của nhiệt độ trong phản ứng sunfat hóa dầu thông 74 Bảng 3.16 Ảnh hưởng của thời gian trong phản ứng sunfat hóa dầu thông 76 Bảng 3.17 So sánh hoạt tính tẩy sạch của các sản phẩm trong quá trình biến tính DT bằng axit sunfuric 82 Bảng 3.18 Nghiên cứu ảnh hưởng của nồng độ axit H2SO4 trong 83 phản ứng hydrat hóa dầu thông Bảng 3.19 Ảnh hưởng của nhiệt độ trong phản ứng hydrat hóa dầu thông 84 Bảng 3.20 Ảnh hưởng của thời gian phản ứng trong phản ứng hydrat hóa dầu thông 85 Bảng 3.21 Ảnh hưởng của lượng oxy đến phản ứng oxy hoá 90 Bảng 3.22 Ảnh hưởng của lượng H2O2 trong phản ứng oxy hoá dầu thông 90 Bảng 3.23 Ảnh hưởng của nhiệt độ trong phản ứng oxy hoá dầu thông 91 Bảng 3.24 Ảnh hưởng của thời gian phản ứng đến quá trình oxy hoá 92 Bảng 3.25 Ảnh hưởng của hàm lượng H2O trong phản ứng oxyt hoá dầu thông 93 Bảng 3.26 Các tính chất hoá lý của DT nguyên liệu và các sản phẩm biến tính 97 Bảng 3.27 Kết quả nghiên cứu ảnh hưởng của loại cánh khuấy đến độ ổn định nhũ tương khi tốc độ khuấy trộn nhỏ 98 Bảng 3.28 Kết quả nghiên cứu ảnh hưởng của loại cánh khuấy đến độ ổn định nhũ tương khi tốc độ khuấy trộn lớn 98 Bảng 3.29 Kết quả nghiên cứu tìm tốc độ khuấy trên thiết bị lớn 99 Bảng 3.30 Kết quả nghiên cứu tìm nhiệt độ thích hợp trên thiết bị lớn 100 Bảng 3.31 Kết quả nghiên cứu tìm thời gian thích hợp cho 1 mẻ trên thiết bị lớn 100 Bảng 3.32 Ảnh hưởng của hàm lượng axit oleic 101 Bảng 3.33 Ảnh hưởng của hàm lượng LAS 102 Bảng 3.34 So sánh các thông số của mẫu thực nghiệm và mẫu tính toán 104 Bảng 3.35 Ảnh hưởng của hàm lượng LAS đến hoạt tính của chất tẩy rửa từ DT hydrat hóa 105 Bảng 3.36 Ảnh hưởng của hàm lượng axit oleic đến hoạt tính của chất tẩy rửa từ DT hydrat hóa 106 Bảng 3.37 Ảnh hưởng của hàm lượng glyxerin đến hoạt tính của chất tẩy rửa từ DT hydrat hóa 107 Bảng 3.38 Ảnh hưởng của hàm lượng TEA đến hoạt tính của chất tẩy rửa từ DT hydrat hóa 108 Bảng 3.39 Ảnh hưởng của nhiệt độ ngâm mẫu đến hoạt tính của chất tẩy rửa từ DT hydrat hóa 109 Bảng 3.40 Ảnh hưởng của thời gian ngâm mẫu đến hoạt tính của chất tẩy rửa từ DT hydrat hóa 110 Bảng 3.41 Các điều kiện tối ưu để chế tạo CTR từ DT hydrta hoá 111 Bảng 3.42 Các đặc trưng hoá lý của các loại CTR 111 Bảng 3.43 Ảnh hưởng của nhiệt độ tẩy trắng đến độ trắng của vải 113 Bảng 3.44 Khảo sát ảnh hưởng của tốc độ khuấy trộn trong thiết bị lớn để chế tạo CTR 114 Bảng 3.45 Khảo sát ảnh hưởng của thời gian trong thiết bị lớn để chế tạo CTR 115 Bảng 3.46 Mối quan hệ giữa sức căng bề mặt và hoạt tính tẩy rửa 115 Bảng 3.47 Quan hệ giữa điện thế zeta và hoạt tính tẩy rửa 117 Bảng 3.48 Giá trị sức căng bề mặt ở các nồng độ CTR khác nhau 119 Bảng 3.49 Sự phụ thuộc của hoạt tính tẩy rửa vào hàm lượng chất hoạt động bề mặt LAS 120 Bảng 3.50 Chỉ số HLB và hoạt tính tẩy sạch của các sản phẩm 121 Bảng 3.51 Ảnh hưởng của nồng độ chất tẩy rửa đến độ mao dẫn của vải 122 Bảng 3.52 Chỉ số COD và BOD của hỗn hợp sau tẩy rửa trong môi trường đất 134 Bảng 3.53 Chi phí nguyên liệu để sản xuất 100 Kg chất tẩy rửa 135a Bảng a.1 Tính chất của các sản phẩm đã tổng hợp 135 Bảng b.1 Các sản phẩm “dạng II” đã đạt được 136 Bảng c.1 Các bài báo đã công bố 145 Bảng c.2 Danh sách Thạc sỹ đã hướng dẫn với nội dung của Đề tài 146 Bảng c.3 Danh sách Kỹ sư đã hướng dẫn với nội dung của Đề tài 146 Bảng c.4 Danh sách Tiến sỹ đang hướng dẫn với nội dung của Đề tài 148 DANH MỤC CÁC HÌNH VẼ VÀ ĐỒ THỊ TT Tên hình Trang Hình 1.1 Sự hình thành mixen 21 Hình 1.2 Xác định nồng độ tới hạn 21 Hình 1.3 Sự nhiễm bẩn dầu trên bề mặt sợi 22 Hình 1.4 Sự gột tẩy vết bẩn béo khỏi bề mặt sợi 23 Hình 1.5 Phương thức Rolling Up 24 Hình 1.6 Các hướng tạo sản phẩm trong quá trình oxy hóa pinen 30 Hình 2.1 Sơ đồ thiết bị phản ứng và chiết sản phẩm 32 Hình 2.2 Sơ đồ thiết bị xác định tỷ trọng 37 Hình 2.3 Thiết bị đo sức căng bề mặt 39 Hình 2.4 Sơ đồ thiết bị xác định độ nhớt 40 Hình 2.5 Dụng cụ đo độ điện di 41 Hình 3.1 Ảnh chụp SEM vải cotton sạch 59 Hình 3.2 Phổ hồng ngoại (IR) của vải cotton 60 Hình 3.3 Ảnh chụp SEM vải cotton nhiễm bẩn 61 Hình 3.4 Phổ IR của vải polieste 63 Hình 3.5 Bề mặt vải polyeste sạch 64 Hình 3.6 Lát cắt vải polyeste sạch 64 Hình 3.7 Bề mặt vải polyeste bị nhiểm bẩn dầu mỡ 65 Hình 3.8 Lát cắt vải polyeste bị nhiễm bẩn dầu mỡ 65 Hình 3.9 Ảnh chụp SEM mẫu vải pha sạch 66 Hình 3.10 Ảnh SEM về sợi và bề mặt vải pha bị nhiễm bẩn dầu mỡ 68 Hình 3.11 Lát cắt vải pha đã nhiễm bẩn dầu mỡ 68 Hình 3.12a Sắc ký đồ GC xác định thành phần của dầu thông nguyên liệu 70 Hình 3.12b Phổ MS xác định thành phần của dầu thông nguyên liệu 70 Hình 3.13 Mối quan hệ giữa khả năng tẩy rửa và nồng độ axit 73 Hình 3.14 Mối quan hệ giữa lượng axit và hoạt tính tẩy sạch 74 Hình 3.15 Mối quan hệ giữa hoạt tính tẩy sạch và nhiệt độ phản ứng 75 Hình 3.16 Mối quan hệ giữa thời gian phản ứng và hoạt tính tẩy sạch 76 Hình 3.17 Phổ IR của dầu thông nguyên liệu 77 Hình 3.18 Phổ IR của mẫu dầu thông sulfat hóa với axit H2SO4 50% 78 Hình 3.19 Phổ IR của mẫu dầu thông sulfat hóa với axit H2SO4 60% 78 Hình 3.20 Phổ IR của mẫu dầu thông sulfat hóa với axit H2SO4 70% 79 Hình 3.21 Phổ IR của mẫu dầu thông sulfat hóa với axit H2SO4 80 79 Hình 3.22 Ảnh hưởng của nồng độ axit sulfuric đến hoạt tính tẩy sạch 84 Hình 3.23 Ảnh hưởng của nhiệt độ phản ứng hydrat hóa đến hoạt tính tẩy sạch 85 Hình 3.24 Ảnh hưởng của thời gian phản ứng hydrat hóa đến hoạt tính tẩy sạch 86 Hình 3.25 Phổ GC-MS của dầu thông Hydrat hóa 87 Hình 3.26 Phổ hồng ngoại IR của dầu thông hydrat hóa 88 Hình 3.27 Mối quan hệ giữa hoạt tính tẩy sạch và tốc độ sục không khí 90 Hình 3.28 Mối quan hệ giữa hoạt tính tẩy sạch và lượng H2O2 91 Hình 3.29 Mối quan hệ giữa hoạt tính tẩy sạch và nhiệt độ oxy hoá 92 Hình 3.30 Mối quan hệ giữa khả năng tẩy sạch và thời gian phản ứng 93 Hình 3.31 Mối quan hệ giữa khả năng tẩy trắng và hàm lượng H2O 94 Hình 3.32 Phổ GC –MS của dầu thông oxy hóa 95 Hình 3.33 Phổ IR của dầu thông oxy hóa 95 Hình 3.34 Mối quan hệ giữa lượng axit oleic và hoạt tính tẩy rửa 102 Hình 3.35 Mối quan hệ giữa lượng LAS và hoạt tính tẩy sạch 103 Hình 3.36 Ảnh hưởng của hàm lượng LAS đến hoạt tính tẩy sạch từ DT hydrat hóa 106 Hình 3.37 Ảnh hưởng của hàm lượng axit oleic đến hoạt tính tẩy sạch từ DT hydrat hóa 107 Hình 3.38 Ảnh hưởng của hàm lượng glyxerin đến hoạt tính tẩy sạch từ DT hydrat hóa 108 Hình 3.39 Ảnh hưởng của hàm lượng TEA đến hoạt tính tẩy sạch từ DT hydrat hóa 109 Hình 3.40 Ảnh hưởng của nhiệt độ ngâm mẫu đến hoạt tính tẩy sạch từ DT hydrat hóa 110 Hình 3.41 Ảnh hưởng của thời gian ngâm mẫu đến hoạt tính tẩy sạch từ DT hydrat hóa 111 Hình 3.42 Ảnh hưởng của nhiệt độ tẩy trắng đến độ trắng của vải 113 Hình 3.43 Mối quan hệ giữa SCBM và hoạt tính tẩy rửa 116 Hình 3.44 Sự phụ thuộc của hoạt tính tẩy sạch vào điện thế 118 Zeta Hình 3.45 Quan hệ giữa SCBM và nồng độ dung dịch CTR 119 Hình 3.46 Mối quan hệ giữa nồng độ chất tẩy rửa và độ mao dẫn của vải 122 Hình 3.47 Mô hình cơ chế tẩy dầu mỡ theo cơ chế cuốn trôi với góc tiếp giáp θ > 900 125 Hình 3.48 Mô hình cơ chế tẩy dầu mỡ theo cơ chế cuốn trôi với góc tiếp giáp θ < 900 125 Hình b.1 Quy trình công nghệ tổng hợp chất hoạt động bề mặt anion bằng phương pháp sunfat hóa dầu thông 137 Hình b.2 Quy trình công nghệ tổng hợp chất hoạt động bề mặt không ion bằng phương pháp hydrat hóa dầu thông 138 Hình b.3 Quy trình công chế tạo chất tẩy rửa) 139 Hình b.4 Qui trình công nghệ xử lý vải mộc có hồ 142 Hình b.5 Qui trình công nghệ xử lý vải mộc không có hồ 144 1 PHẦN 1. MỞ ĐẦU Hiện nay, công nghiệp dệt may đang mang lại cho nền kinh tế nước ta một nguồn lợi to lớn, nhất là trong thời kỳ hội nhập. Kim ngạch thu được cho ngân sách nhà nước từ xuất khẩu dệt may hàng năm lên tới hàng tỷ USD. Tuy nhiên hàng năm, nước ta phải nhập một lượng lớn hoá chất để xử lý làm sạch vải sợi trước khi nhuộm mầu, in hoa và các công đoạn sản xuất vải tiếp theo. Trong số hoá chất đó, các chất hoạt động bề mặt để tẩy dầu mỡ, chất béo, tạp chất trên vải, chất giũ hồ, chất ngấm chiếm một lượng lớn. Có nhiều nguyên nhân để vải sợi bị nhiễm bẩn dầu mỡ, tạp chất, nhưng thông thường là các lý do sau: -Khi chuốt sợi, người ta phải cho parafin hoặc dầu vào để tránh cho sợi bị xù lông và để các sợi không dính vào nhau trong quá trình dệt. -Đối với các loại sợi poliamit, poliester do có khả năng sinh tĩnh điện cao nên gây khó khăn cho quá trình dệt, để hạn chế hiện tượng này, khi dệt người ta thường phải cho thêm chất bôi trơn là dầu khoáng. -Khi dệt thông thường cho thêm hồ tinh bột. -Trong sợi bông luôn có các tạp chất như chất béo, sáp, lignin, hợp chất chứa nitơ, tro, pectin, các tạp chất cơ học do mảnh hạt lẫn vào. -Dầu mỡ từ máy dệt có thể thâm nhập vào trong quá trình dệt, gây nhiễm bẩn cục bộ cho sợi hoặc các tấm vải thành phẩm. -Các chất bẩn từ môi trường bám dính vào vải và sợi trong quá trình dệt và vận chuyển. Đến công đoạn nhuộm mầu và in hoa, tất cả các chất bẩn nêu trên phải được tẩy sạch; nếu không thì quá trình nhuộm sẽ không có hiệu quả do các loại chất này ngăn cản sự thấm nước và mầu nhuộm, không cho thuốc nhuộm khuyếch tán vào vải, gây loang mầu. Hiện nay trong cả nước ta có khoảng 1000 nhà máy dệt lớn nhỏ với hơn 10.500 máy dệt. Lớn nhất là nhà máy dệt của Vinatex có công suất 3000 tấn vải/ ngày; nhỏ như xí nghiệp dệt nhuộm Trung thư cũng có đến 6-7 tấn vải /ngày. Theo thống kê, trong một năm, trung bình nước ta sản xuất ra hơn 23 triệu tấn vải. Lượng vải này cần đ ... nghệ chế tạo chất tẩy rửa Để phối trộn chế tạo chất tẩy rửa, cần các thành phần sau đây: Dầu thông sunfat hóa 90%, axit oleic 4,5%, chất hoạt động bề mặt LAS 3%, TEA 1%, glyxerin 0,5%; Phụ gia PG4 0,5%, hoạt tính tẩy sạch đạt 99% Trình tự pha chế để chế tạo chất tẩy rửa như sau: Cho dầu thông sunfat hóa với lượng đã tính toán vào thiết bị dung tích 100 lít; khuấy trộn ở nhiệt độ thường với tốc độ khuấy 700 vòng/phút. Tiếp theo cho hỗn hợp phụ gia PG4 và glyxerin vào, khuấy thêm 10 phút. Tiếp theo là LAS. Do LAS có độ nhớt lớn nên lúc này cần phải khuấy mạnh và thời gian là 15 phút cho LAS tan đều và phân phối khắp không gian thiết bị. Sau đó cho lượng axit oleic 4% vào. Tiếp đến là rượu iso-propylic và cuối cùng là TEA. Lượng TEA khoảng 1% thì dung dịch chất tẩy rửa sẽ có pH trung tính. Tổng thời gian khuấy trộn là 1 giờ. Với trình tự cho như vậy sẽ tạo một dung dịch đồng nhất, hỗn hợp pha trộn không toả nhiệt. Còn nếu cho theo trình tự khác thì sẽ xảy ra các vấn đề sau: izo propylic Glyxerin Axit oleic LAS DÇu th«ng biÕn tÝnh S¶n phÈm TEA 3 -Hỗn hợp toả nhiệt mạnh -Hỗn hợp có thể sẽ bị phân lớp sau khi để 1 đến 2 tuần -Hoạt tính tẩy rửa không cao -Hỗn hợp có độ nhũ hoá trong nước kém Sau khi hoàn tất quá trình pha trộn, sản phẩm được bơm sang thùng chứa trung gian. Tại đây mẫu được lấy đi phân tích các chỉ tiêu kỹ thuật. Nếu chưa đạt yêu cầu nào đó thì có thể điều chỉnh, gia giảm thành phần thêm chút ít. Sản phẩm chất tẩy rửa được đóng vào thùng phuy dung tích 100 lít để phục vụ cho khách hàng lớn như các nhà máy dệt nhuộm. Ngoài ra, chúng cũng được đựng trong can nhựa dung tích 50 lít, 20 lít, 10 lít, 5 lít và 2 lít. Tốt nhất nên dùng bao bì mầu sẫm. 1 QUI TRÌNH CÔNG NGHỆ CHẾ TẠO CHẤT TẨY RƯA TỪ DẦU THÔNG SUNFAT HÓA 1.Nguyên liệu đầu vào Nguyên liệu sử dụng là dầu thông đã được sunfat hóa ở công đoạn tổng hợp chất HĐBM, có các tính chất như sau: Các tính chất hoá lý của DT sunfat hóa Mẫu Tỷ trọng Sức căng bề mặt (mN/m) Độ nhớt (cSt) Độ bay hơi (g/m2.h) Hoạt tính tẩy sạch (% tẩy rửa) DT sunfat hoá 0,896 17,253 1,98 15,37.10-3 *91,9 với vải cotton *86,3 với vảiphaCot/Pes *84,03 với vải polieste Số liệu cho thấy, hoạt tính tẩy sạch vẫn chưa đạt tới 100%, vậy phải phối trộn với các thành phần khác để tạo ra chất tẩy rửa (CTR) có họat tính mong muốn. 2 2.Sơ đồ qui trình công nghệ chế tạo chất tẩy rửa ( CTR) Hình b.3. Quy trình công chế tạo chất tẩy rửa 1. Thiết bị khuấy trộn chế tạo chất tẩy rửa, 2. Thùng chứa trung gian, 3. Thùng chứa sản phẩm) 3.Thuyết minh qui trình công nghệ chế tạo chất tẩy rửa Để phối trộn chế tạo chất tẩy rửa, cần các thành phần sau đây: Dầu thông sunfat hóa 90%, axit oleic 4,5%, chất hoạt động bề mặt LAS 3%, TEA 1%, glyxerin 0,5%; Phụ gia PG4 0,5%, hoạt tính tẩy sạch đạt 99% Trình tự pha chế để chế tạo chất tẩy rửa như sau: Cho dầu thông sunfat hóa với lượng đã tính toán vào thiết bị dung tích 100 lít; khuấy trộn ở nhiệt độ thường với tốc độ khuấy 700 vòng/phút. Tiếp theo cho hỗn hợp phụ gia PG4 và glyxerin vào, khuấy thêm 10 phút. Tiếp theo là LAS. Do LAS có độ nhớt lớn nên lúc này cần phải khuấy mạnh và thời gian là 15 phút cho LAS tan đều và phân phối khắp không gian thiết bị. Sau đó cho lượng axit oleic 4% vào. Tiếp đến là rượu iso-propylic và cuối cùng là TEA. Lượng TEA khoảng 1% thì dung izo propylic Glyxerin Axit oleic LAS DÇu th«ng biÕn tÝnh S¶n phÈm TEA 3 dịch chất tẩy rửa sẽ có pH trung tính. Tổng thời gian khuấy trộn là 1 giờ. Với trình tự cho như vậy sẽ tạo một dung dịch đồng nhất, hỗn hợp pha trộn không toả nhiệt. Còn nếu cho theo trình tự khác thì sẽ xảy ra các vấn đề sau: -Hỗn hợp toả nhiệt mạnh -Hỗn hợp có thể sẽ bị phân lớp sau khi để 1 đến 2 tuần -Hoạt tính tẩy rửa không cao -Hỗn hợp có độ nhũ hoá trong nước kém Sau khi hoàn tất quá trình pha trộn, sản phẩm được bơm sang thùng chứa trung gian. Tại đây mẫu được lấy đi phân tích các chỉ tiêu kỹ thuật. Nếu chưa đạt yêu cầu nào đó thì có thể điều chỉnh, gia giảm thành phần thêm chút ít. Sản phẩm chất tẩy rửa được đóng vào thùng phuy dung tích 100 lít để phục vụ cho khách hàng lớn như các nhà máy dệt nhuộm. Ngoài ra, chúng cũng được đựng trong can nhựa dung tích 50 lít, 20 lít, 10 lít, 5 lít và 2 lít. Tốt nhất nên dùng bao bì mầu sẫm. QUI TRÌNH CÔNG NGHỆ TỔNG HỢP CHẤT HĐBM HYDRAT HÓA 1.Nguyên liệu đầu vào Nguyên liệu sử dụng là dầu thông Quảng Ninh có các tính chất như sau: 1.1.Thành phần hóa học (phân tích bằng phương pháp GC-MS) - α -pinen 73.185% - β - pinen 2.696 % - β-myrcene 0,739% - ∆3-caren 14.509% - Limonen 2.269% - γ-terpinene, 0,449% - α-terpinolene, 2,552% Như vậy, cấu tử chính trong dầu thông nguyên liệu là α -pinen (73.185% ), β - pinen (2.696 %), và ∆ 3-caren (14.509% ) có tổng hàm lượng đến 91%, là thành phần chính tạo nên hoạt tính bề mặt. 4 1.2.Tính chất hóa lý Các thông số hóa lý của dầu thông nguyên liệu Mẫu Tỷ trọng d SCBM (nM/m) Độ nhớt (cst) Hoạt tính tẩy sạch (%) Dầu thông 0,8633 25,461 2,32 42,7 Từ số liệu trong bảng cho thấy, dầu thông nguyên liệu cũng có hoạt tính tẩy sạch, tuy nhiên rất thấp. mặt khác, bản thân dầu này không tan trong nước nên cần phải biến tính để tạo thành chất HĐBM non-ion bằng phương pháp hydrat hóa. Sản phẩm có hoạt tính bề mặt cao, có khả năng tan tốt để dễ nhũ hóa trong nước. 2. Sơ đồ Qui trình công nghệ Hình b.2. Quy trình công nghệ tổng hợp chất hoạt động bề mặt không ion bằng phương pháp hydrat hóa dầu thông Nuíc th¶i Nuíc S¶n phÈmTrung hßa axit Dd Na2CO3Nuíc H2SO4, 15% DÇu th«ng Axeton 5 1. Thiết bị phản ứng, 2. Thiết bị lắng phân tách pha, 3,4,5 Thiết bị rửa, 6. Thiết trung hoà, 7. Thùng chứa trung gian, 8. Thùng chứa sản phẩm) 3.Thuyết minh qui trình công nghệ Cho dầu thông nguyên liệu theo lượng đã định vào thiết bị phản ứng 1. Vừa khuấy trộn, vừa nhỏ từ từ 45% lượng axit H2SO4 nồng độ 15% và 6% axeton vào dầu thông. Duy trì phản ứng hydrat hoá ở 85oC trong vòng 4 giờ. Thiết bị 1 là loại thùng khuấy có vỏ bọc đun nóng và làm lạnh bằng ống xoắn ruột gà đặt bên trong thiết bị. Tại đây xảy ra quá trình hydrat hóa dầu thông. Sau phản ứng hỗn hợp sản phẩm từ thiết bị 1 được bơm sang thiết bị lắng tách pha 2. Thiết bị này là loại thiết bị phân ly lỏng – lỏng. Dầu thông và sản phẩm dầu thông hydrat hoá nằm ở lớp trên và được chiết tách sang thiết bị rửa bằng nước 3, sau đó tiếp tục rửa bằng dung dịch Na2CO3 10%, cuối cùng được rửa lại nhiều lần bằng bằng nước cho đến môi trường trung tính (thử bằng giấy quì tím), thu được sản phẩm dầu thông hydrat hoá. Đưa sản phẩm này vào thùng chứa trung gian 7. Nếu phân tích các chỉ tiêu kỹ thuật của sản phẩm thấy đạt yêu cầu thì bơm sản phẩm này vào thùng chứa sản phẩm 8. Đóng gói vào bao bì theo mẫu mã đã định. Dung dịch nước nằm ở pha dưới của thiết bị 2 được đưa qua thiết bị trung hoà axit dư 7 bằng dung dịch xô đa, sau đó xử lý nước thải bằng phương pháp keo tụ đến hàm lượng COD, BOD đạt tiêu chuẩn nước thải rồi đưa vào nơi qui định. 1 QUI TRÌNH CÔNG NGHỆ XỬ LÝ VẢI MỘC CÓ HỒ *Qui trình này thường áp dụng đối với vải dệt thoi (chủ yếu là loại vải cotton) *Hồ sử dụng ngày nay phần lớn là loại hồ tổng hợp PVA. Qui trình giũ hồ này được thiết lập đối với loại hồ PVA. Thuyết minh qui trình xử lý vải mộc có hồ Trước tiên vải mộc cần xử lý được giũ hồ trong thiết bị với chất giũ hồ là CTR của đề tài. Giai đoạn này có mục đích tẩy sạch hết hồ, dầu khoáng bám dính trên bề mặt vải. Quá trình giũ hồ được tiến hành với điều kiện công nghệ như sau: - Lượng vải: 242,8 Kg (708 m) - Lượng nước: 2000 lít - Lượng chất tẩy rửa của đề tài (BK-NH1 pro): 3 Kg ( tưong đương 9 lít dung dịch chất tẩy rửa đã nhũ hóa) - Thực hiện trên máy BK - Thời gian thử nghiệm 2 giờ (tương đương với 8 vòng quay của lô cuốn) - Nhiệt độ tiến hành thử nghiệm 900C - Vải được giặt lại 3 lần sau khi giũ hồ Sau khi giũ hồ vải sẽ được tẩy trắng hoặc nấu tẩy tùy theo yêu cầu của sản phẩm, Quá trình tẩy trắng được thực hiện như sau: - Lượng vải: 218,5 Kg - Lượng nước: 2000 lít - Chất tẩy trắng được cho theo đơn ( đó là NaOH và H2O2) - Thực hiện trên máy Winch - Thời gian thử nghiệm 5 giờ - Nhiệt độ tiến hành thử nghiệm 980C - Vải được giặt lại 3 lần sau khi tẩy trắng Quá trình nấu tẩy trong điều kiện oxy hóa mạnh (H2O2 trong môi trường kiềm) với tác động của chất oxy hóa mạnh, các tạp chất cơ học bám trên bề mặt vải sẽ bị oxy hóa, thu được vải trắng và có độ mao dẫn lớn (tối đa đạt khoảng 120 mm, thông thường đạt từ 60-80 mm) Nếu mục đích sản xuất vải trắng (không cần nhuộm mầu) thì sau công đoạn này, vải được sấy khô và đưa vào kho chứa. Như vậy, sau quá trình nấu tẩy, độ mao dẫn của vải đã đạt rất lớn (60 -120 mm), đủ và vượt tiêu chuẩn để chuyển sang công đoạn tiếp theo là nhuộm và in hoa. 2 3 Công đoạn nhuộm phải theo yêu cầu với đơn pha chế thích hợp, thành phần đơn pha thuốc nhuộm gồm có: - Chất màu - Chất trợ nhuộm có vai trò làm cho đều màu (sử dụng CTR của Đề tài) - Chất ngấm (sử dụng CTR của Đề tài)) - Các phụ gia (tạo môi trường và làm tăng một số tính năng của vải như chống tái bám, tăng độ bóng) Trong các thành phần của đơn pha chế thuốc nhuộm thì có thể thay thế chất trợ nhuộm, chất ngấm bằng chất tẩy rửa của đề tài với hàm lượng tương đương nhưng cho hiệu quả kinh tế hơn (rẻ hơn và không gây ô nhiễm môi trường). Cuối cùng vải được sấy khô, cuối lô và lưu trữ trong kho chứa để phân phối cho khách hàng. Chú ý: Nếu là vải dệt kim thì thực hiện trên máy Z, có tốc độ vòng quay nhanh; còn vải dệt thoi thường thực hiện trên máy BK, có tốc độ vòng quay chậm QUI TRÌNH CÔNG NGHỆ XỬ LÝ VẢI KHÔNG CÓ HỒ Qui trình này áp dụng chủ yếu đối với vải dệt kim (thường là loại vải polieste) Qui trình chung để xử lý loại vải này gồm các công đoạn sau: a-Tẩy dầu: Để loại bỏ hết dầu khoáng bám dính trên bề mặt vải trong quá trình dệt. b-Tẩy trắng: Làm trắng vải đối với trường hợp sản xuất vải trắng và vải yêu cầu nhuộm màu nhạt (màu lơ). c- Nấu tẩy: Mục đích để làm trắng vải và tẩy sạch các tạp chất cơ học bám trên bề mặt vải vải (chủ yếu dùng cho vải cotton) trong môi trường oxy hóa mạnh. d- Nhuộm màu: Đây là công đoạn cuối cùng của quá trình sản xuất vải sợi để thu được vải có màu sắc như yêu cầu. Như vậy, so với loại trên thì công nghệ này không cần công đoạn giũ hồ. Thuyết minh qui trình công nghệ xử lý vải mộc không có hồ Đầu tiên vải mộc cần xử lý được tẩy dầu với chất tẩy dầu kết hợp tẩy trắng (chúng tôi chọn CTR của đề tài làm chất tẩy dầu) để tẩy sạch dầu khoáng bám dính trên bề mặt vải trong quá trình dệt. Quá trình tẩy trắng kết hợp tẩy dầu thực hiện như sau: Lượng vải: 218,5 Kg, Lượng nước: 2000 lít, Chất tẩy trắng được cho theo đơn, Thực hiện trên máy Winch, Thời gian thử nghiệm 5 giờ , Nhiệt độ tiến hành thử nghiệm 980C, Vải được giặt lại 3 lần sau khi tẩy trắng Sau đó vải có thể sẽ được nấu tẩy tùy theo yêu cầu của sản phẩm, Quá trình nấu tẩy được thực hiện trong điều kiện có chất oxy hóa mạnh (H2O2 trong môi trường kiềm). Với tác động của chất oxy hóa này, các tạp chất cơ học bám trên bề mặt vải sẽ được oxy hóa, kết quả thu được vải trắng hơn và có độ mao dẫn lớn (khoảng 120 mm). Tiếp theo, vải được nhuộm màu theo yêu cầu với đơn pha chế thích hợp, thành phần đơn pha thuốc nhuộm gồm có: Chất màu, Chất trợ nhuộm (chất làm cho đều màu), Chất ngấm, Các phụ gia (tạo môi trường và làm tăng một số tính năng của vải nhuộm như chống tái bám, tăng độ bóng, chống phai) Trong các thành phần của đơn pha chế thuốc nhuộm đối với loại vải này, chúng tôi cũng thay thế chất trợ nhuộm, chất ngấm bằng CTR của đề tài với hàm lượng tương đương nhưng hiệu quả thu được tốt hơn : độ mao dẫn cao hơn, giá thành thấp hơn, màu nhuộm và các tính chất khác tương đương. Cuối cùng vải được sấy khô, cuối lô và lưu trữ trong kho chứa để phân phối cho khách hàng. 1 QUI TRÌNH CÔNG NGHỆ TỔNG HỢP CHẤT HĐBM SUNFAT HÓA 1.Nguyên liệu đầu vào Nguyên liệu sử dụng là dầu thông Quảng Ninh có các tính chất như sau: 1.1.Thành phần hóa học (phân tích bằng phương pháp GC-MS) - α -pinen 73.185% - β - pinen 2.696 % - β-myrcene 0,739% - ∆3-caren 14.509% - Limonen 2.269% - γ-terpinene, 0,449% - α-terpinolene, 2,552% Như vậy, cấu tử chính trong dầu thông nguyên liệu là α -pinen (73.185% ), β - pinen (2.696 %), và ∆ 3-caren (14.509% ) có tổng hàm lượng đến 91%, là thành phần chính tạo nên hoạt tính bề mặt. 1.2.Tính chất hóa lý Các thông số hóa lý của dầu thông Mẫu Tỷ trọng d SCBM (nM/m) Độ nhớt (cst) Hoạt tính tẩy sạch (%) Dầu thông 0,8633 25,461 2,32 42,7 Từ số liệu trong bảng cho thấy, dầu thông nguyên liệu cũng có hoạt tính tẩy sạch, tuy nhiên rất thấp. mặt khác, bản thân dầu này không tan trong nước nên cần phải biến tính để tạo thành chất HĐBM anion có hoạt tính bề mặt cao, có khả năng tan tốt để dễ nhũ hóa trong nước. 2 2.Sơ đồ qui trình công nghệ Hình b.1. Quy trình công nghệ tổng hợp chất hoạt động bề mặt anion bằng phương pháp sunfat hóa dầu thông 1. Thiết bị phản ứng, 2. Thiết bị lắng phân tách pha, 3,4,5 Thiết bị rửa, 6. Thiết bị trung hoà, 7. Thùng chứa trung gian, 8. Thùng chứa sản phẩm. 3.Thuyết minh qui trình công nghệ Cho dầu thông (có tính chất đầu vào như đã nêu) theo lượng tính toán trước vào thiết bị phản ứng 1. Thiết bị 1 là loại thiết bị dạng thùng khuấy có vỏ bọc đun nóng. Nhỏ từ từ axit sunfuric nồng độ 70% với tỷ lệ đã định (7,5% theo khối lượng) vào thiết bị. Vừa nhỏ vừa khuấy trộn với tốc độ khuấy 600 vòng/phút. Duy trì nhiệt độ 30oC trong vòng 5 giờ (chú ý: nếu mùa đông, gia nhiệt nhẹ đến 30oC, mùa hè có thể không cần gia nhiệt. Sau đó làm lạnh bằng ống xoắn để bên trong thiết bị để khống chế nhiệt độ này). Sau phản ứng hỗn hợp từ thiết bị 1 được dẫn sang thiết bị trích ly 2. Tại đây, hỗn hợp sản phẩm được lắng tách thành hai pha: Dầu thông và sản phẩm dầu thông sunfat nằm ở lớp trên và được tách sang thiết bị rửa nước 3, rửa bằng dung dịch Na2CO3 10%, cuối cùng được rửa lại bằng nước cất đến khi hết kiềm (thử trên giấy quì tím), thu được sản phẩm chất HĐBM dạng dầu thông sunfat hóa. Bơm sản phẩm vào thùng chứa trung gian 7. Phân tích các chỉ tiêu kỹ thuật của sản phẩm như: hoạt tính tẩy sạch, hàm lượng nhóm sunfat, tỷ trọng, độ nhớt, độ bay hơi, sức căng bề mặt, nếu chưa đạt chất lượng mong muốn thì xử lý thêm rồi đưa vào bể DÇu th«ng H2SO4, 70% Nuíc Dd Na2CO3 Trung hßa axit S¶n phÈm Nuíc Nuíc th¶i 3 chứa sản phẩm. Từ đây, sản phẩm được đóng gói theo can và lọ nhựa dung tích 5 lít, 3 lít, 2 lít, 1 lít. Nếu để cho khách hàng lớn như các nhà máy dệt nhuộm, có thể dùng thùng phuy dung tích 100 lít. Dung dịch nước ở lớp dưới của thiết bị chiết tách 2 được đưa qua thiết bị trung hoà số 7. Nước thải này chứa một lượng axit không đáng kể và tạp chất được trung hoà sơ bộ bằng dung dịch xô đa, rồi xử lý bằng phương pháp keo tụ để làm sạch nước đến hàm lượng COD và BOD cho phép.
File đính kèm:
de_tai_nghien_cuu_tong_hop_cac_chat_hoat_dong_be_mat_de_san.pdf