Design and installation of vibration testing system for spring mounted model of wing
ABSTRACT:
This paper presents the design and
installation of measuring vibration system in
wind tunnel area 1m x 1m. The theoretical
analysis of the spring structure in this model
help we possible to design a system for wind
tunnel by yourself with suitable area, wind
speed as well as survey wing model to obtain
results desire.
This system helps us to observe the
oscillation of wing survey by eyes, but to
know exactly how wing fluctuates, also the
pitching angle of wing, we use ultrasonic
sensors to measure the distance variation,
will be presented in more detail in the text. At
the same time, the article also shows how to
make a simple and durable wing model with
NACA 0015 airfoil - wing model will be
surveyed ranged in system above.
The aerodynamic phenomena affect to
the vibration of the wing are also mentioned
and overcome in the design of the wing.
Finally we process the data after
measured to see the similarities between the
experiment and the theoretical dynamics of
aviation.
Tóm tắt nội dung tài liệu: Design and installation of vibration testing system for spring mounted model of wing
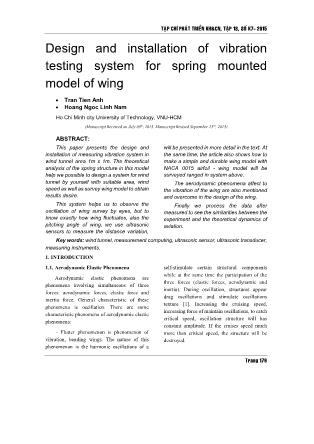
TAÏP CHÍ PHAÙT TRIEÅN KH&CN, TAÄP 18, SOÁ K7- 2015 Trang 179 Design and installation of vibration testing system for spring mounted model of wing Tran Tien Anh Hoang Ngoc Linh Nam Ho Chi Minh city University of Technology, VNU-HCM (Manuscript Received on July 08th, 2015, Manuscript Revised September 23rd, 2015) ABSTRACT: This paper presents the design and installation of measuring vibration system in wind tunnel area 1m x 1m. The theoretical analysis of the spring structure in this model help we possible to design a system for wind tunnel by yourself with suitable area, wind speed as well as survey wing model to obtain results desire. This system helps us to observe the oscillation of wing survey by eyes, but to know exactly how wing fluctuates, also the pitching angle of wing, we use ultrasonic sensors to measure the distance variation, will be presented in more detail in the text. At the same time, the article also shows how to make a simple and durable wing model with NACA 0015 airfoil - wing model will be surveyed ranged in system above. The aerodynamic phenomena affect to the vibration of the wing are also mentioned and overcome in the design of the wing. Finally we process the data after measured to see the similarities between the experiment and the theoretical dynamics of aviation. Key words: wind tunnel, measurement computing, ultrasonic sensor, ultrasonic transducer, measuring instruments. 1. INTRODUCTION 1.1. Aerodynamic Elastic Phenomena Aerodynamic elastic phenomena are phenomena involving simultaneous of three forces: aerodynamic forces, elastic force and inertia force. General characteristic of these phenomena is oscillation. There are some characteristic phenomena of aerodynamic elastic phenomena: - Flutter phenomenon is phenomenon of vibration, bending wings. The nature of this phenomenon is the harmonic oscillations of a self-stimulate certain structural components while at the same time the participation of the three forces (elastic forces, aerodynamic and inertia). During oscillation, structures appear drag oscillations and stimulate oscillations texture [1]. Increasing the cruising speed, increasing force of maintain oscillations, to catch critical speed, oscillation structure will has constant amplitude. If the cruises speed much more than critical speed, the structure will be destroyed. SCIENCE & TECHNOLOGY DEVELOPMENT, Vol 18, No.K7- 2015 Trang 180 - Buffeting phenomenon is shaking a certain structural components. The nature of this phenomenon is the forced oscillation structure, by vortex of broken gas line runs through the line as structural components in the front of the swirling effect (act of force excitation frequency) coincides with own oscillator frequency certain structural parts of aircraft will generate resonance and thus the structure was destroyed [3]. - Dynamic reaction phenomenon is phenomenon occurs when simultaneous effect of three structural forces and when flying through turbulence flow (often impact pulse or cycle) or by pulses collide when landing planes grounded. Due to such effect that might appear too large overload causing structural destruction. Figure 1. Experiment examined the aerodynamic phenomenon in wind tunnel of NASA. ( /WindTunnel.html) In this study, we just only care about two phenomena flutter and buffeting. To observe the phenomenon, we compute the natural frequencies of the system and the frequency of the external force, equal two this frequency to the resonance phenomenon occurs, will observe the phenomenon [2]. 1.2. Objectives The motivation of this thesis is design and installation a measuring vibration system in wind tunnel, along make an aircraft wing to put it inside that system. The aim is measured the vibration of wing by ultrasonic sensors (measure the distance). Data after being measured will be shows in excel format, base on that we process the data to find out the vibrate amplitude and swivel angle. 2. PARAMETERS OF SPRING MOUNTED MODEL 2.1 Vibration Natural Frequency To calculate the natural frequency, we put the wing into the model to simulate the oscillation as shown below: Figure 2. Wing model before oscillation Figure 3. Wing model during oscillation Applying Newton second law and moment theorem to the model showed above, we have the following dynamics equations: 2211 21 22 22 llxkllxkJ lxklxkxm o With: - m: weight of wing model - k: stiffness of the springs (four springs have the same stiffness) TAÏP CHÍ PHAÙT TRIEÅN KH&CN, TAÄP 18, SOÁ K7- 2015 Trang 181 - l1: distance from A to M - l2: distance from B to M - Jo: inertia moment of structure 2 2 2 121 21 22 24 llkxllkJ llkkxxm o 022 024 21 2 2 2 1 21 xllkllkJ llkkxxm o With tXx cos tcos Equations become: 0 0 22 24 2 2 2 1 2 21 21 2 X llkJllk llkkm o 022 24 det 2 2 2 1 2 21 21 2 llkJllk llkkm o Solutions of that equation deduce natural vibration frequency: o ooo mJ llmJllmJllmJ k 21 22 2 2 1 222 2 2 1 1 842 o ooo mJ llmJllmJllmJ 21 22 2 2 1 222 2 2 1 2 842 We can see that 021 (3). 2.2. The Frequency of the External Force Wing lift is given by equation [4]: ftAVctF 2sin 2 1 2 With: - f: Vortex shedding frequency - c: constant - : the density of fluid - V: characteristic velocity of fluid - A: the biggest area perpendicular to the direction of the velocity V Figure 4. Simulation of wing model section to specify the area A I will examine vortex shedding phenomenon occurs with wing model when put it into wind tunnel. Vortex shedding phenomenon is the phenomenon of fluids as water or air flow over an obstacle with certain velocity and depending size and shape of obstacles will split into two interleaved flows. Alternatively, vortex shedding frequency depends on the Strouhal number through the following equation [5]: V fdSt With: - f: vortex shedding frequency - d: max thickness of obstacle. In this wing model, d = 4cm - V: velocity characteristic of fluid. Max velocity of wind tunnel is 8m/s We know as Strouhal number is a dimensionless number, it depends on object’s shape and value of Reynolds number. In that Reynolds number is a dimensionless value, which is showed the relative magnitude between impacts caused by inertia and in friction (viscosity) to flow [6]. With: Vd Re SCIENCE & TECHNOLOGY DEVELOPMENT, Vol 18, No.K7- 2015 Trang 182 Including: - d: max thickness of wing model - : kinematic viscosity of air Figure 5. Strouhal number acts as function according Reynolds number for cylindrical. ( Figure 6. Value of Roshko number in graph link between Strouhal number and Reynolds number. In that, Roshko number is a dimensionless number described mechanism of flow when oscillate [7]. Ro = St x Re For different values of Reynolds number, flow over various objects also different. We choose the stiffness k so that vortex shedding frequency 2 2 f 2122221222221 2 842 11025 llmJllmJllmJ mJk ooo o 3. EXPERIMENTAL APARATUS 3.1. Design of Spring Mounted Model Figure 7. 3D design of model experiment As stated above theory, we will carry out the design of the pivotal portion size pilot based on oscillations of wing model. It is clamped tightly to 8 springs with stiffness k foresee mimicking wing oscillations which model will be implemented from the initial conditions to the active vibration and finally the oscillation combined vibrations on until wing model is destroyed when we turn change factors such as velocity in tunnel wind, angle of attack of experimental models to the following objectives: - Check the correctness of the initial theoretical calculations for model when the angle of attack of the wing by wing is 0. - Surveying the effects of the change to oscillation angle of attack of the model wing simultaneously drawing conclusions. Inside, wing model is hanging by 8 springs which have same stiffness k. Figure 8. Wing model is hanging by 8 springs which have same stiffness k TAÏP CHÍ PHAÙT TRIEÅN KH&CN, TAÄP 18, SOÁ K7- 2015 Trang 183 Accordingly, the wing model is attached to the rails by the structure as shown by below. Figure 9. Joints between the wing model and springs structure In that frame bar (4) is through a rectangular hole cut size 5cm × 8cm in mica plates (1) and mounted on the frame between the structure as above, connection with the above structure will facilitate the fitting, and to facilitate expanding upgrade later when we conducted experiments with the other model towards expanding as stated at the beginning of the thesis in all countries. Wing model fitted with 8 springs by structure of hooks (1) and screws fixed through it with bolts (2), it can be moved in the grooves between the vertical aluminum frames on the picture to change distance as the theoretical calculations above then connected to the springs (3). Three connected structures have the same idea. In that, hanger (1) hang on screws are screwed into the trench as shown above, and it can move back and forward by turning the screw loose to be able to sync move with the screw rod between the bottom frame, mounted on steel bars V3.5 donuts yellow donut plate as above, this is an important part bearing that have function to bear and fixed the frame rail experiment with structural model as Figure 12 below: Figure 10. Overall of bracket structure Figure 11. Structure of fixed the donut plate to the gudgeon In that, iron roller (1) screws fixed by screws (3) to the groove (2) is welded steel frame fixed to the above illustration, in which yellow donut plate is fixed to four edges of the iron frame as listed on four red rollers. This fixed structure makes donut plate is fixed but can be rotated to make the frame wing angle of incidence change from that implementation goal 2 of the experiment. Then the model is mounted to shield blanket: - One mica plate 1m×2m×10mm in size. - Three wood plates 1m×2m×8mm in size. After completing the design model with size of 2m x 1.4m x 1,62m placed on the rollers 10, is tightly coupled to the wind tunnel mouth 1m x 1m size to conduct experiments. SCIENCE & TECHNOLOGY DEVELOPMENT, Vol 18, No.K7- 2015 Trang 184 Figure 12. Realistic picture of the experimental model Accordingly experiment, we will calculate vortex shedding frequency given on the basis of theory. Followed that, we choose spring which have stiffness k that guaranteed to the separate oscillation frequency equal vortex shedding frequency, as calculated above to be able to observe the Flutter phenomenon of wing model in wind tunnel. 3.2. Wing Testing Model The experimental wing model was designed in standard of NACA 0015 for airfoil: Figure 13. 3D drawing of wing model In that, - Shield wingtips will be used to reduce the impact of the Horseshoe Vortex phenomenon on the wing (just like wing tip), 40cm x 16cm x 8mm in size. - Frames of NACA 0015 wing model make by wood 8mm. - Rib of wing model by wood 10mm. - Decal outer wing model. - The part fixed wing model with a stainless steel bar of diameter 25mm x 25mm. Figure 14. Preliminary wing models after assembled Figure 15. Wing model after completed 3.3. Ultrasonic Sensors and Devices Devices are used to measure in this experiment include: DC Power BK Precision: is a power supply device, voltage regulator suitable for the Ultrasonic sensor during measurement oscillator. Figure 16. DC Power BK Precision MC Measurement is a device to transmit measured data to PC, offers easy-to-use data acquisition and data logger hardware and software for test, measurement, and industrial applications. MC measurement computing is the market leader in the design, manufacture and distribution of value-priced data acquisition hardware, and test and measurement software TAÏP CHÍ PHAÙT TRIEÅN KH&CN, TAÄP 18, SOÁ K7- 2015 Trang 185 solutions for both programmers and non- programmers. Ultrasonic sensors: major device for measuring oscillations. In this experiment, we use two Sensick UM30-21-118. Our sensors have operating range about 30 to 250 mm, limiting range is 350 mm, so the measurement process must install additional shields in measuring range of sensors. Supply voltage about DC 9 to 30 V and power consumption less than 2.4 W. (UM30-2 ultrasonic sensors). Finally, we install all equipment together, ready for measurement. How to connection this circuit will be shown in DASYLab software of chapter 4. Figure 17. Assembly all equipment together 4. OSCILLATING MEASURE OF WING TESTING MODEL Results after measured as the difference of distance between two points A and B fitted with two sensors above the ground (x1 and x2), as proposing picture: Figure 18. Simulate the vibration of points A and B Figure 19. Result file after measurement In excel file after exporting, it has three main columns, the first column is the measurement time, here we adjust for the signal is taken every 0.01 seconds. The two columns after are about x1 and x2 fluctuations, the distance between A and B respectively to a fixed plane below. Then from the oscillation of two points A and B, we interpolate the vibration of the wing center - point M and the pitching angle of wing model. So that we will study the oscillation of wing axis, follow the equation: 2 21 xxx And the pitching angle of wing: 120 arctan x With the distance from wing axis to sensor is 120mm. Completed the preparation and measurement metrics, the following are the results of the process. Firstly, we examine the oscillation of wing with incidence angle =0. Once enough data, we marked all three columns and run scatter, results are as follows: SCIENCE & TECHNOLOGY DEVELOPMENT, Vol 18, No.K7- 2015 Trang 186 Figure 20. Chart of wing oscillation over time with =0 (4.6 m/s wind speed). In that, the blue line is the graph of the wing fluctuates, the red one is pitching angle of wing. We noticed that although the angle of incidence by 0, wing still fluctuating, it is due to error during installation. But it’s not oscillation too large due to wind velocity too small. Similarly, we gradually increase the wind speed until reaches the maximum allowed speed (about 8.5 m/s), then we change the angle of incidence and examine. Figure 21. Chart of wing oscillation over time with =12o (wind speed of 5.5m/s ) Figure 22. Chart of wing oscillation over time with =21o (wind speed of 4.6 m/s ) 5. CONCLUSIONS AND PERSPECTIVES 5.1. Achievements This thesis has achieved all of its goals. Firstly, we learned the structural how to make a wind tunnel; thereby we design a wing accordingly to it and installation of wing on it. During installation, it was generated some problems, but we had solved, such as the wind tunnel can’t open the door to get the wing model into it, position of the screws do not outsourcing exactly so the installation encounter a little difficult, ... This stage also helps us have more knowledge about machining with CNC cutting machine to manufacture wing model. Second, this thesis helps us to know and come into contact with the ultrasonic sensors – the expensive sensors. It also helps us to using Dasylab software a brief. Finally, the measurement and processing data stages help us to verify empirically with what they have learned in theory about the factors effect to wing when the airflow passing it. 5.2. Limitations and Further Research There are some limitations in this thesis: - Wind tunnel was outsourcing with some of the details have not exactly fetch to the installation of the associated have some difficulties. - The maximum allowable speed of the wind tunnel is not large enough to be able to observe the oscillation of wing model by eyes. - The maximum distance that the ultrasonic sensor can measure quite small, so we have to add some details to shorten the distance. For expand research, as presented at the domestic situation in the first research thesis, this is a subject that has wide applicability in the aviation, construction, architecture, etc. So in designing the model was optimized ability to install additional accessory devices to be able to TAÏP CHÍ PHAÙT TRIEÅN KH&CN, TAÄP 18, SOÁ K7- 2015 Trang 187 expand into different research directions on the same model in order to save costs still effective in studies. We have explained on aerodynamic theory of bending and twisting phenomenon of wing model aircraft when operating outside reality. However, wing model that we put in this thesis is symmetrical airfoil, in fact wings have symmetrical airfoil were no longer in use on airplane, but instead is the airfoil with the camber, wings were added with control surfaces as: slat, flap, aileron On both experimentally and theoretically demonstrated that modern wing models are designed according to the new theory can improve the shape of wings, wing curvature (degrees Camber) and new control surfaces help technological improvements to air a new altitude. An altitude that there can make available the non- engine aircraft but could fly for hours in the air just based on improvements in wing patterns and materials. Acknowledgements:This work was support ed by the research grant of AUN/SEED-Net over a total period of 2 years for Collaborative Research with Industry (CRI) project (Project No. HCMUT-CRI 1401).
File đính kèm:
design_and_installation_of_vibration_testing_system_for_spri.pdf