Nghiên cứu cơ chế mòn dao gắn mảnh PCBN sử dụng tiện tinh thép 09CrSi qua tôi
1. Mở đầu
Từ nửa đầu của thập kỷ 70, tiện cứng (hard turning) được áp dụng để gia công vật liệu
(thường là thép qua tôi) có độ cứng từ 45 – 65 HRC. Tiện cứng được sử dụng rộng rãi trong
công nghiệp ô tô khi gia công các chi tiết như vành bánh răng, vòng ổ, dụng cụ và khuôn mẫu.
Đặc biệt tiện cứng được sử dụng khi gia công các chi tiết có hình dáng phức tạp và không cần sử
dụng dung dịch bôi trơn - làm nguội, gia công chính xác lần cuối (tiện tinh) các chi tiết máy có tỉ
số kích thước chiều dài trên đường kính nhỏ [1]. Tiện cứng cho phép đạt độ chính xác và nhám
bề mặt tương đương với mài nhưng đầu tư thấp hơn và có khả năng tạo nên trên lớp bề mặt ứng
suất dư nén làm tăng tuổi thọ về mỏi của chi tiết máy trong các tiếp xúc lăn [2]. Tuy nhiên, tiện
cứng đòi hỏi máy, hệ thống công nghệ có độ cứng vững và độ chính xác cao [3].
Khi gia công 4 loại thép tôi khác nhau, có độ cứng như nhau, Poulachon và đồng nghiệp
[1] đã kết luận rằng mòn mặt trước là dạng mòn phổ biến khi gia công thép đã tôi cứng, thép có
chứa các hạt các bít cứng với kích thước lớn sẽ có tính gia công (trên khía cạnh mòn dao) kém
hơn thép có cấu trúc mactensit đồng đều. Cơ chế mòn dụng cụ chủ yếu là khuếch tán kết hợp với
cào xước hoặc dính.
Kevin và đồng nghiệp [4], sử dụng hai loại mảnh dao CBN-H và CBN-L với chất liên
kết là TiN và một lượng nhỏ Co tiện thép AISI 52100 cho thấy mòn mặt sau tăng gần như tuyến
tính với chiều dài cắt và tốc độ mòn của mảnh dao CBN-H cao hơn. Mòn xuất hiện trên cả mặt
trước và sau kèm theo hiện tượng dính của VLGC trên bề mặt các vùng mòn (materials
transfer). Các hạt CBN bị tách ra khỏi mảnh dao đặc biệt khi tăng vận tốc cắt. Tương tác của
VLGC với pha thứ hai của VLDC là nguyên nhân trực tiếp làm yếu liên kết của các hạt CBN
với nền và bị cuốn đi.
Tóm tắt nội dung tài liệu: Nghiên cứu cơ chế mòn dao gắn mảnh PCBN sử dụng tiện tinh thép 09CrSi qua tôi
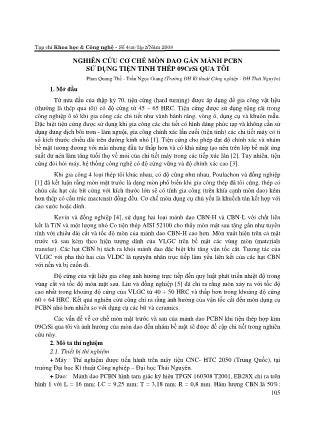
T¹p chÝ Khoa häc & C«ng nghÖ - Sè 4(48) Tập 2/N¨m 2008 105 NGHIÊN CỨU CƠ CHẾ MÒN DAO GẮN MẢNH PCBN SỬ DỤNG TIỆN TINH THÉP 09CrSi QUA TÔI Phan Quang Thế - Trần Ngọc Giang (Trường ĐH Kĩ thuật Công nghiệp - ĐH Thái Nguyên) 1. Mở đầu Từ nửa đầu của thập kỷ 70, tiện cứng (hard turning) được áp dụng để gia công vật liệu (thường là thép qua tôi) có độ cứng từ 45 – 65 HRC. Tiện cứng được sử dụng rộng rãi trong công nghiệp ô tô khi gia công các chi tiết như vành bánh răng, vòng ổ, dụng cụ và khuôn mẫu. Đặc biệt tiện cứng được sử dụng khi gia công các chi tiết có hình dáng phức tạp và không cần sử dụng dung dịch bôi trơn - làm nguội, gia công chính xác lần cuối (tiện tinh) các chi tiết máy có tỉ số kích thước chiều dài trên đường kính nhỏ [1]. Tiện cứng cho phép đạt độ chính xác và nhám bề mặt tương đương với mài nhưng đầu tư thấp hơn và có khả năng tạo nên trên lớp bề mặt ứng suất dư nén làm tăng tuổi thọ về mỏi của chi tiết máy trong các tiếp xúc lăn [2]. Tuy nhiên, tiện cứng đòi hỏi máy, hệ thống công nghệ có độ cứng vững và độ chính xác cao [3]. Khi gia công 4 loại thép tôi khác nhau, có độ cứng như nhau, Poulachon và đồng nghiệp [1] đã kết luận rằng mòn mặt trước là dạng mòn phổ biến khi gia công thép đã tôi cứng, thép có chứa các hạt các bít cứng với kích thước lớn sẽ có tính gia công (trên khía cạnh mòn dao) kém hơn thép có cấu trúc mactensit đồng đều. Cơ chế mòn dụng cụ chủ yếu là khuếch tán kết hợp với cào xước hoặc dính. Kevin và đồng nghiệp [4], sử dụng hai loại mảnh dao CBN-H và CBN-L với chất liên kết là TiN và một lượng nhỏ Co tiện thép AISI 52100 cho thấy mòn mặt sau tăng gần như tuyến tính với chiều dài cắt và tốc độ mòn của mảnh dao CBN-H cao hơn. Mòn xuất hiện trên cả mặt trước và sau kèm theo hiện tượng dính của VLGC trên bề mặt các vùng mòn (materials transfer). Các hạt CBN bị tách ra khỏi mảnh dao đặc biệt khi tăng vận tốc cắt. Tương tác của VLGC với pha thứ hai của VLDC là nguyên nhân trực tiếp làm yếu liên kết của các hạt CBN với nền và bị cuốn đi. Độ cứng của vật liệu gia công ảnh hưởng trực tiếp đến quy luật phát triển nhiệt độ trong vùng cắt và tốc độ mòn mặt sau. Liu và đồng nghiệp [5] đã chỉ ra rằng mòn xảy ra với tốc độ cao nhất trong khoảng độ cứng của VLGC từ 40 ÷ 50 HRC và thấp hơn trong khoảng độ cứng 60 ÷ 64 HRC. Kết quả nghiên cứu cũng chỉ ra rằng ảnh hưởng của vận tốc cắt đến mòn dụng cụ PCBN nhỏ hơn nhiều so với dụng cụ các bít và ceramics. Các vấn đề về cơ chế mòn mặt trước và sau của mảnh dao PCBN khi tiện thép hợp kim 09CrSi qua tôi và ảnh hưởng của mòn dao đến nhám bề mặt sẽ được đề cập chi tiết trong nghiên cứu này. 2. Mô tả thí nghiệm 2.1. Thiết bị thí nghiệm + Máy : Thí nghiệm được tiến hành trên máy tiện CNC- HTC 2050 (Trung Quốc), tại trường Đại học Kĩ thuật Công nghiệp – Đại học Thái Nguyên. + Dao: Mảnh dao PCBN hình tam giác ký hiệu TPGN 160308 T2001, EB28X chỉ ra trên hình 1 với L = 16 mm; I.C = 9,25 mm; T = 3,18 mm; R = 0,8 mm. Hàm lượng CBN là 50%; Héi th¶o Khoa häc toµn quèc C«ng nghÖ vËt liÖu vµ bÒ mÆt - Th¸i Nguyªn 2008 106 chất dính kết TiC; cỡ hạt: 2µm. γ = - 11°; α = 22°; λ = - 11° (góc tạo thành khi kẹp mảnh dao vào thân dao và lên máy). Thân dao: Kiểu MTENN 2020 K16-N (hãng CANELA) Hình 1. Mảnh dao PCBN sử dụng trong nghiên cứu + Phôi Thép 09CrSi là thép hợp kim dụng cụ thường sử dụng chế tạo các dụng cụ cắt với vận tốc thấp và các chi tiết có yêu cầu về khả năng chịu ma sát, mòn cao. Phôi thép hợp kim 09CrSi sử dụng trong thí nghiệm có chiều dài: L = 300mm, đường kính: ∅62, tôi thể tích đạt độ cứng 56-58 HRC. Thành phần hoá học của phôi được xác định bằng phương pháp phân tích quang phổ tại Nhà máy Z159 cho trên bảng 1. Các kết quả phân tích cấu trúc của phôi thép trên hai mặt phẳng song song (a) và vuông góc (b) với trục của phôi trên kính hiển vi quang học AXOVOC-100 của Nhật cho thấy các hạt các bít (FeCr)3C đường kính đến 3µm phân bố với mật độ cao trong thép chỉ ra trên hình 2. Bảng 1. Thành phần hoá học của phôi thép 09CrSi C Si P Mn Ni Cr Mo 0,823 1,2351 0,0241 0,5862 0,0332 1,113 0,0192 V Cu W Ti Al Fe 0,1499 0,2876 0,1768 0,0299 0,0011 95,447 Hình 2. Hình ảnh cấu trúc của phôi thép 09CrSi sử dụng trong thí nghiệm trên mặt cắt song song (a) và vuông góc với trục (b) phóng đại 1000 lần. + Thiết bị đo nhám bề mặt Sử dụng máy đo nhám Mitutoyo SJ - 201 của Nhật Bản với các thông số kĩ thuật cơ bản sau: - Hiển thị LCD. Tiêu chuNn DIN, ISO, JIS, ANSI. - Thông số đo được: Ra, Rz, Rt, Rq, Rp, Ry, Pc, S, Sm. - Độ phân giải: 0,03µm/300µm; 0,08µm/75µm; 0,04µm/9,4µm. (a) (b) T¹p chÝ Khoa häc & C«ng nghÖ - Sè 4(48) Tập 2/N¨m 2008 107 + Thiết bị sử dụng phân tích bề mặt Sử dụng kính hiển vi điện tử TM-1000 Hitachi, Nhật Bản có độ phóng đại tới 10000 lần, tại phòng thí nghiệm Vật lí trường Đại học Sư phạm Thái Nguyên. + Chế độ công nghệ Vận tốc cắt: v = 180 m/p; lượng chạy dao: s = 0,1 mm/vòng; chiều sâu cắt: t = 0,12 mm. 2.2. Trình tự thí nghiệm Phôi thép 09CrSi sau khi được tiện thô bằng mảnh dao hợp kim cứng K01 đảm bảo độ côn không vượt quá 0,05 mm/ 100 mm chiều dài phôi. Sau đó sử dụng mảnh dao PCBN tiện tinh qua một lượt trước khi tiến hành thí nghiệm và trước mỗi lần thay mảnh dao mới. 5 mảnh dao được sử dụng để tiện tinh phôi thép 09CrSi, nhám bề mặt được đo sau 5 khoảng thời gian cắt nhất định: 2,61 phút; 5,19 phút; 7,69 phút; 10,09 phút; 12,36 phút tương ứng với chiều dài cắt trên phôi là: 250 mm; 500 mm; 750 mm; 1000 mm; 1250 mm. Các mảnh dao sau đó được tháo ra, quan sát và phân tích trên kính hiển vi điện tử TM-1000. 3. Kết quả thí nghiệm 3.1. Mòn dụng cụ Kết quả quan sát các mảnh dao sau khi tiện tinh trên kính hiển vi điện tử cho thấy các mảnh dao đều bị mòn cả mặt trước và mặt sau. Sau 2,61 phút cắt, tương ứng với chiều dài cắt là 250 mm, dọc theo lưỡi cắt chính xuất hiện vòng cung mòn với chiều rộng xấp xỉ 10 µm. Trên vùng mòn mặt trước này không nhìn thấy hình ảnh của các hạt CBN như vùng chưa bị mòn, lớp bề mặt có cấu trúc sóng chỉ ra trên Hình 3(a) và 3(b). Đây là hình ảnh mòn vật liệu dòn theo cơ chế biến dạng dẻo bề mặt do hạt cứng “cày” trên bề mặt dưới tác dụng của ứng suất pháp rất lớn ở vùng lưỡi cắt gây ra. Sau 5,19 phút cắt, tương ứng với chiều dài cắt là 500 mm, bản chất mòn trên mặt trước không thay đổi tuy chiều dài cung mòn trên lưỡi cắt chính tăng lên nhưng chiều rộng của vùng mòn vẫn giữ không đổi khoảng 10 µm. Sau thời gian cắt 7,69 phút, tương ứng với chiều dài cắt là 750 mm, vùng mòn trên lưỡi cắt chính lan rộng gần đến đỉnh nhưng vẫn giữ chiều rộng khoảng 10 µm. Sau 10,09 phút cắt, tương ứng với chiều dài cắt là 1000 mm, vùng mòn mặt trước phát triển đến đỉnh cung tròn của lưỡi cắt và chiều rộng vùng cắt đạt tới 20 µm. Sau thời gian cắt 12,36 phút tương ứng với chiều dài cắt là 1250 mm, hiện tượng mòn mặt trước thay đổi căn bản như trên Hình 3(c) với chiều rộng vùng mòn tới 120 µm, không còn hiện tượng dính của VLGC trên bề mặt vùng mòn mà chỉ có vùng mòn rất gồ ghề. Từ Hình 3(d) có thể thấy những mảnh vật liệu dụng cụ bong ra khỏi mặt trước theo cơ chế của mòn dính hoặc dính kết hợp với mỏi. Mòn trên mặt sau được thể hiện trên Hình 4(a) sau 7,69 phút, Hình 4(b) sau 10,09 phút cắt và Hình 5(a) sau 12,36 phút cắt. Kết quả quan sát trên kính hiển vi điện tử cho thấy vùng mòn mặt sau phát triển chậm từ khi bắt đầu cắt đến 7,69 phút đạt chiều cao mòn mặt sau hs ≈ 50 µm với bề mặt tương đối bằng phẳng và VLGC dính nhẹ trên bề mặt mòn này. Sau 10,09 phút cắt thì chiều cao mòn mặt sau cũng chỉ đạt tới hs ≈ 60 µm. Hình ảnh VLGC dính trên vùng mòn mặt sau chỉ ra trên Hình 4(c). Tuy nhiên trên mặt sau xuất hiện hai mảng dạng vNy nằm ngay phía dưới vùng giao của cạnh tự do của phoi khi thoát khỏi mặt trước với các lưỡi. Héi th¶o Khoa häc toµn quèc C«ng nghÖ vËt liÖu vµ bÒ mÆt - Th¸i Nguyªn 2008 108 Hình 3.(a) Hình ảnh mòn mặt trước của mảnh dao PCBN sau khi tiện 2,61 phút với các vết biến dạng dẻo bề mặt; (b) Hình ảnh phóng to của (a); (c) Mòn mặt trước của mảnh dao PCBN sau khi tiện 12,36 phút cho thấy bề mặt bị mòn rất gồ ghề; (d) Hình ảnh cơ chế mòn mặt trước với sự bóc tách của các lớp vật liệu dụng cụ do dính - mỏi. Hình 4. (a) Mòn mặt sau của mảnh dao PCBN sau khi tiện 7,69 phút cho thấy VLGC dính trên vùng mòn tương đối phẳng; (b) Ảnh mòn mặt sau, sau 10,09 phút gia công; (c) Ảnh phóng to VLGC bám lên vùng mòn mặt sau (b); (d) Góc mòn bên trái của (b). (a) (b) (c) (d) (a) (b) (c) (d) T¹p chÝ Khoa häc & C«ng nghÖ - Sè 4(48) Tập 2/N¨m 2008 109 Hình 5. (a) Mòn mặt sau của mảnh dao PCBN sau khi tiện 12,36 phút cho thấy hình ảnh gồ ghề của vùng mòn. (b) Hình ảnh phóng to của (a). Hình ảnh phóng to của khối bên trái thể hiện trên hình 4(d). Đến 12,36 phút gia công thì trên toàn bề mặt sau của dụng cụ bị biến dạng theo một kiểu rất đặc biệt với các mảng vật liệu dụng cụ dạng vNy (hình 5(a) và 5(b)). Vật liệu dụng cụ bị dồn nén tạo tên các mảng vNy nhẵn, rộng với chiều cao hs ≈ 750 µm và VLGC dính trên bề mặt mòn là không đáng kể. 3.2. Nhám bề mặt gia công Kết quả đo nhám bề trong mặt phẳng thẳng đứng chứa đường tâm của phôi và dọc theo một đường sinh của mặt trụ cho trên bảng 2. Giá trị Ra của nhám bề mặt sau khi cắt 10,09 phút tăng 23% so với sau khi cắt 7,69 phút và tương ứng là sự gia tăng 15% giá trị Rz. Sự gia tăng đột biến của độ nhám sau 10,09 phút cắt liên quan đến sự phát triển của chiều rộng vùng mòn mặt trước đến 50% và chiều cao vùng mòn mặt sau tới 20% với sự xuất hiện hai mảng dạng vNy trên vùng mặt sau. Kết quả đo nhám bề mặt gia công thể hiện trên bảng 2. Đồ thị biểu diễn sự biến thiên của nhám bề mặt theo thời gian thể hiện trên hình 6. Bảng 2. Nhám bề mặt sau những khoảng thời gian gia công khác nhau Mảnh dao số Chiều dài cắt (mm) Thời gian cắt (phút) Trung bình Ra (Rz) [µm] 01 250 2,61 0,53 (2,84) 02 500 5,19 0,56 (3,01) 03 750 7,69 0,60 (3,16) 04 1000 10,09 0,74 (3,63) 05 1250 12,36 0,78 (3,87) Hình 6. Đồ thị biểu diễn sự biến thiên của nhám bề mặt theo thời gian cắt 4. Phân tích kết quả và thảo luận Theo Trent và Wight [6], khi gia công bằng dao CBN hiện tượng biến dạng lưỡi cắt không xảy ra, mòn mặt trước và mặt sau đồng thời tồn tại, vùng mòn mặt trước rất gần lưỡi cắt. Trong nghiên cứu này, mòn dụng cụ xuất hiện cả trên mặt trước và mặt sau chỉ sau 2,61 phút gia công. Tuy nhiên vùng mòn mặt trước không nằm gần lưỡi cắt mà phát triển từ lưỡi cắt tạo thành mặt trước phụ tương đối phẳng và phát triển dần theo hướng thoát phoi như trên hình 3(a). Trên (a) (b) 0 1 2 3 4 5 0 5 10 15 Ra Rz µm Phút Héi th¶o Khoa häc toµn quèc C«ng nghÖ vËt liÖu vµ bÒ mÆt - Th¸i Nguyªn 2008 110 vùng mòn nhiều hạt PCBN bị tách ra khỏi bề mặt do tương tác của VLGC làm yếu pha thứ hai của VLDC theo như kết quả nghiên cứu của Kevin và đồng nghiệp [4]. Tuy nhiên, cơ chế mòn do khuếch tán kết hợp với cào xước do Poulachon và đồng nghiệp [1] đề xuất dường như không phù hợp với các kết quả của nghiên cứu này. Hình ảnh các rãnh biến dạng dẻo trên vùng mòn mặt trước trên Hình 3(b) khẳng định biến dạng dẻo bề mặt do các hạt cứng (các bít (FeCr)3C) và các ôxít khác trong thép 09CrSi dưới tác dụng của ứng suất pháp rất lớn ở vùng gần lưỡi cắt gây nên là cơ chế mòn chính trên mặt trước. Tuy nhiên sau thời gian cắt đủ lớn, khi mòn phát triển dần vào phía trong vùng mặt trước theo hướng thoát phoi, ứng suất pháp trên mặt trước giảm đi nhanh chóng, hiện tượng dính trở nên phổ biến ở vùng phoi thoát khỏi mặt trước thì cơ chế mòn do mỏi kết hợp với dính là nguyên nhân mòn ở vùng này gây bóc tách từng mảnh VLDC ra khỏi vùng bề mặt như trên Hình 3(d). Đây là một phát hiện mới về cơ chế mòn mặt trước trong tiện tinh cứng. Hơn nữa từ Hình 3(c) có thể thấy khi mòn mặt trước phát triển trên hầu hết diện tích tiếp xúc giữa phoi và mặt trước thì cơ chế mòn do bóc tách các mảnh vật liệu trở nên chiếm ưu thế thay cho cơ chế mòn do cào xước làm cho mòn mặt trước phát triển với tốc độ cao hơn. Bề mặt vùng mòn trở nên gồ ghề và không nhẵn như bề mặt vùng mòn mặt trước thông thường. Điều này có thể giải thích do cơ tính của PCBN ít bị suy giảm bởi nhiệt độ cao trong vùng cắt, tuy nhiên tác dụng có chu kỳ của các hạt cứng trong thép lên bề mặt kết hợp với dính đã làm cho bề mặt của dụng cụ bị phá hủy theo cơ chế dính mỏi kết hợp sau một thời gian gia công nhất định. Mòn mặt sau cũng phát triển theo quy luật thông thường trong cắt kim loại cho đến 7,69 phút (Hình 4(a)). Cơ chế mòn mặt sau tương đối phù hợp với kết quả nghiên cứu của Kenvin [4] như trên Hình 4(c). Tuy nhiên, sau 10,09 phút gia công trên mặt sau xuất hiện hai mảng dạng vNy cục bộ (Hình 4(b)). Đây là vùng tương ứng với các rãnh mòn sâu trên dụng cụ khi cắt các hợp kim có nhiệt độ nóng chảy cao và theo Shaw [7], thì các rãnh mòn sâu trên mặt trước và sau ở vùng này có liên quan đến tác dụng truyền nhiệt mạnh ở hai bên rìa của phoi vào bề mặt dụng cụ cắt. Đây là hiện tượng mòn phức tạp liên quan nhiều đến nhiệt độ cao. Theo Trent [6] nhiệt độ cao kết hợp với biến cứng của phoi, tác dụng của ôxy trong môi trường môi trường cắt đã tạo nên các rãnh mòn sâu ở vùng này trên dao tiện các bít khi tiện thép. Khi thời gian cắt tăng lên đến 12,36 phút các mảng dạng vNy này phát triển trên toàn mặt sau và một số mảng bong ra tạo nên mòn. Đây cùng là một phát hiện mới về cơ chế mòn mặt sau trong tiện tinh cứng. Từ các kết quả đo nhám bề mặt có thể thấy cho đến 7,69 phút cắt, Ra gần như không thay đổi Ra = 0,53 ÷ 0,60 µm, những khi thời gian cắt đạt tới 10,09 phút có sự thay đổi đột biến về nhám bề mặt, Ra tăng xấp xỉ 23%, sau đó Ra giữ gần như không thay đổi tới 12,36 phút cắt. Nhám bề mặt tăng nhanh khi mòn mặt trước và mặt sau đạt tới một mức độ nào đó và sau đó giữ gần như không đổi. Điều này có thể liên quan trực tiếp tới sự phát triển bề rộng của vùng mòn trên mặt trước tới 20 µm và sự xuất hiện các mảng dạng vNy trên mặt sau như đã phân tích ở phần trên. Có thể thấy rằng nếu như mòn trên mặt trước và sau phát triển theo cơ chế khuếch tán, suy yếu pha thứ hai dẫn đến bóc tách các hạt CBN như các nghiên cứu mới đây thì tuổi bền của mảnh dao CBN có thể sẽ cao hơn nhiều lần so với thực tế. Hiện tượng bong từng mảng VLDC T¹p chÝ Khoa häc & C«ng nghÖ - Sè 4(48) Tập 2/N¨m 2008 111 trên mặt trước, tạo thành dạng vNy và bong từng mảng VLDC trên mặt sau là nguyên nhân cơ bản làm rút ngắn tuổi bền của dụng cụ. Các cơ chế mòn này có thể liên quan đến nhiệt, số chu kì cào xước của hạt cứng trong VLGC và dính trên bề mặt tiếp xúc của mặt trước và mặt sau cũng như kết hợp với tác dụng ôxi hóa của ôxi từ môi trường. 5. Kết luận Các kết quả của nghiên cứu cho thấy khi tiện tinh thép 09CrSi bằng dao PCBN mòn mặt trước và mặt sau là hai dạng mòn chủ yếu. Trong giai đoạn đầu, cơ chế mòn mặt trước chủ yếu là biến dạng dẻo do tác dụng cào xước của các hạt cứng trong thép và sự tách ra khỏi bề mặt của các hạt CBN. Cơ chế mòn mặt sau là quá trình bóc tách của các hạt CBN do pha thứ hai của VLDC bị yếu đi khi tương tác với VLGC. Trong giai đoạn sau, cơ chế mòn mặt trước là do mỏi dính với sự bóc tách của từng mảng vật liệu trên mặt trước. Cơ chế mòn mặt sau có thể liên quan đến nhiệt, số chu kì cào xước của hạt cứng và dính kết hợp với tác dụng ôxi hóa của ôxi từ môi trường tạo nên các mảng dạng vảy và bong ra khỏi mặt sau Tóm tắt Đặc điểm của quá trình tạo phoi, lực cắt, nhiệt cắt và mòn trong quá trình tiện cứng đã được đề cập nhiều trong nhiều nghiên cứu mới đây, tuy nhiên cơ chế mòn dụng cụ PCBN khi tiện tinh vẫn chưa được nghiên cứu đầy đủ. Kết quả nghiên cứu của các tác giả khi tiện tinh thép 09CrSi qua tôi bằng dao gắn mảnh PCBN cho thấy mòn mặt trước và sau là hai dạng mòn chính. Cơ chế mòn trên mặt trước liên quan đến tác dụng cào xước của hạt cứng trong vật liệu gia công (VLGC) và mòn do mỏi-dính của các lớp bề mặt. Mòn mặt sau của dụng cụ không đơn thuần là sự bong ra của các hạt CBN mà có thể liên quan đến hiện tượng phức tạp của nhiệt, tương tác giữa VLGC và vật liệu dụng cụ (VLDC) kết hợp với hiện tượng ôxy hóa. Mòn ảnh hưởng trực tiếp đến nhám bề mặt chi tiết gia công. Summary A study of wear mechanisms of PCBN cutting tools used in precision turning of hardened 09crsi steel The features of chip formation, cutting temperature and wear in hard turning are addressed in recent studies but the wear mechanism of PCBN cutting tool in precision turning has not been realli understood. The research results of the authors in turning hardened 09CrSi steel using PCBN cutting tools shows that rake face and flank face wear were the two main types of wear. The mechanism of the rake face wear involved with the abrasion wear caused by hard particles in the steel and wear of surface layers based on adhesion - fatigue. The flank face wear was not normalli the detachments of CBN particles but might be involving directli with heat, frictional interactions between work and tool materials in a combination with oxidation phenomenon. Wear of cutting tool had directli affected surface roughness of the machined element. Héi th¶o Khoa häc toµn quèc C«ng nghÖ vËt liÖu vµ bÒ mÆt - Th¸i Nguyªn 2008 112 Tài liệu tham khảo [1]. Diniz.A.E, Ferreira.J.R, Filho.F.T. (2003), “Influence of Refrigeration/ Lubrication Condition on SAE 52100 Hardened Steel Turning at Several Cutting Speeds”, International Journal of Machine Tools and Manufacturing, Vol. 43, pp. 317-326. [2]. Guo.Y.B, Sahni. J.(2004), “A Comparative Study of Hard Turned and Cylindricalli Ground White Layers”, International Journal of Machine Tools and Manufacturing, Vol. 44, pp. 135-145. [3]. Kevin Chou.Y, Evans.C.J, Barash.M.M. (2002), “Experimental Investigation on CBN Turning of Hardened AIAI 52100 Steel”, Journal of Materials Processing Technology, Vol.124, pp. 274-283. [4]. Liu.X.L, Wen.D.H, Li.Z.J, Xiao.L, Yan.F.G. (2002), “Cutting Temperature and Tool Wear of Hard Turning Hardened Bearing Steel”, Journal of Materials Processing Technology, Vol. 129, pp. 200-206. [5]. Poulachon.G, Bandyopadhyay.B.P, Jawahir.I.S, Pheulpin.S, Seguin.E. (2004), “Wear Behavior of CBN while Turning Various Hardened Steels”, Wear, Vol. 256, pp.302-310. [6]. Shaw M.C. (1989), Metal Cutting Principles, Oxford University Press, New York. [7]. Trent E.M and Wight P.K. (2000), Metal Cutting, Butterworth-Heinemann USA.
File đính kèm:
nghien_cuu_co_che_mon_dao_gan_manh_pcbn_su_dung_tien_tinh_th.pdf