Vẽ kỹ thuật có hướng dẫn kỹ thuật Autocad (Phần 2)
§1.KHÁI NIỆM Cơ BẢN
Để truyền chuyển động quay từ trục này sang trục khác, trước kia người ta thường
dùng các bánh xe ma sát lắp trên hai trục, tiếp xúc nhau. Khi trục I quay thì nhờ lực ma
sát nên bánh xe thứ hai cũng quay theo, nên trục II cũng quay. Nhưng khi mômen xoắn
lớn quá thì thường có hiện tượng trượt nên sự truyền chuyển động quay không chính
xác. Do đó người ta nghĩ ra cách làm các răng trên hai bánh xe và cho các răng ăn khớp
xen kẽ nhau và từ đó hình thành bánh răng (hình 6 .1 ).
1.Tùy theo vị trí tương quan giữa hai trục mà người ta chia ra làm:
- bánh răng trụ (bánh xe ma sát là hình trụ) khi hai trục song song với nhau;
- bánh răng nón (bánh xe ma sát là hình nón cụt) khi hai trục cắt nhau;
- bánh vít và trục vít khi hai trục trực giao nhau;
- bánh răng xoắn khi hai trục chéo nhau.
2. Tùy theo hình dạng của răng mà người ta chia làm:
- răng thẳng, rẫng nghiêng, ràng chữ V, răng xoáy.
3. Tùy theo prôphin cùa răng (dườììg cong tạo ra mặt bên của răng) người ta chia
làm:
- răng thân khai đường tròn cơ sở;
- răng cyclôít (đầu răng là êpicyclôit và chân răng là hypôcyclôít);
- răng cung tròn (bánh răng Nỏvicốp)
Tóm tắt nội dung tài liệu: Vẽ kỹ thuật có hướng dẫn kỹ thuật Autocad (Phần 2)
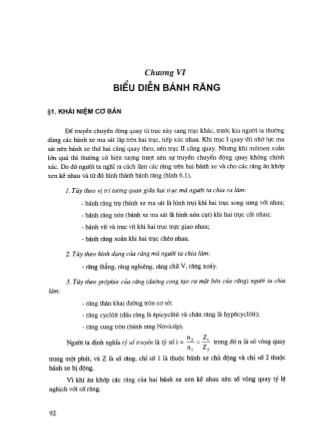
Chương VI BIỂU DIỄN BÁNH RĂNG §1.KHÁI NIỆM Cơ BẢN Để truyền chuyển động quay từ trục này sang trục khác, trước kia người ta thường dùng các bánh xe ma sát lắp trên hai trục, tiếp xúc nhau. Khi trục I quay thì nhờ lực ma sát nên bánh xe thứ hai cũng quay theo, nên trục II cũng quay. Nhưng khi mômen xoắn lớn quá thì thường có hiện tượng trượt nên sự truyền chuyển động quay không chính xác. Do đó người ta nghĩ ra cách làm các răng trên hai bánh xe và cho các răng ăn khớp xen kẽ nhau và từ đó hình thành bánh răng (hình 6 . 1 ). 1.Tùy theo vị trí tương quan giữa hai trục mà người ta chia ra làm: - bánh răng trụ (bánh xe ma sát là hình trụ) khi hai trục song song với nhau; - bánh răng nón (bánh xe ma sát là hình nón cụt) khi hai trục cắt nhau; - bánh vít và trục vít khi hai trục trực giao nhau; - bánh răng xoắn khi hai trục chéo nhau. 2. Tùy theo hình dạng của răng mà người ta chia làm: - răng thẳng, rẫng nghiêng, ràng chữ V, răng xoáy. 3. Tùy theo prôphin cùa răng (dườììg cong tạo ra mặt bên của răng) người ta chia làm: - răng thân khai đường tròn cơ sở; - răng cyclôít (đầu răng là êpicyclôit và chân răng là hypôcyclôít); - răng cung tròn (bánh răng Nỏvicốp). Người ta định nghĩa tỷ sô' truyền là tỷ số i = — = —- trong đó n là số vòng quay n, trong một phút, và z là số răng, chỉ số 1 là thuộc bánh xe chủ động và chỉ số 2 thuộc bánh xe bị động. Vì khi ăn khớp các răng của hai bánh xe xen kẽ nhau nên số vòng quay tỷ lệ nghịch vói số răng. 92 Nếu i > 1 thì truyền động là tăng íôc; Nếu i < 1 thì là giảm tốc; Nếu i = 1 thì số vòng quav không đổi, chỉ có chiều quay là đổi thôi, Hình 6.1 §2. BÁNH RĂNG TRỤ 1. Một số định nghĩa Trên hình chiếu theo hưóìig trục của bánh răng, mặt trụ đỉnh răng được chiếu thành một đường tròn dỉtth râng (d„ là dường kính), mặt trụ qua dáy của kẽ răng được chiếu thành đường tròn đáy răng với đường kính là d|. Giữa hai đường tròn này có một đường tròn nữa gọi là đường tròn chia với đường kính là d (còn gọi là đường tròn nguyên bản, đường tròn lăn). Chiều cao h của răng được tính theo hướng kính từ đỉnh răng đến chân răng, trong đó là chiều cao đầu răng và h| là chiều cao chán răng (xem hình 6 .2 a). Chiều dài của cung đường tròn chia giới hạn bởi hai mặt bên cùng phía của hai răng lân cận được gọi là bước răng P; chiều dày của răng là s và chiểu rộng kẽ răng là s'. Để đơn giản khi vẽ, thường cho s = s'. 2. Liên hệ giữa các kích thưóc cơ bản Chiều dài đường tròn chia là 7i.D„. Nhưng chiều dài đó cũng bằng z .p (Z sô' răng, 1 „ „ „ „ p _ , p p bước răng), vì vậy ta có đẳng thức 7T.D„ = z.p. Ta rút ra D„ = z. —. Tỷ số — được ký n * n 93 hiệu là m và gọi là môđiiyn của bánh rănạ. Thay vào ta có Dn = z.m . z và m là hai thông sô' cơ bản dùng để xác định một số kích thước của bánh răng. Môduyn m được tiêu chuẩn hóa bởi TCVN 2257-77. Sau đây là một số giá trị của m: 0 ,5 ; 0,6; 0 ,8 ; 1 ; 1,25; 1,5; 2 ; 2,5 ; 5 ; 6 ... Khi thiết kế người ta thường lấy = 1 m ; h| = 1,25 m (hoặc 1,2 m) theo hình 6 .2 a ta có liên hệ giữa các đường kính như sau: Ta đã có d = m.z. = d + 2h, = m.z + 2.m = 2.(Z + 2); df = d - 2 h| = m.z - 2(1,25 m) = m (Z - 2,5); a là góc ăn khớp, thường được lấy là « 20". Theo hình (6.2b) ta có: d(ị| = 0 |T | = d|COsa = d|Cos 20" = 0,94.d| doi là đường kính vòng tròn cơ sở tạo ra đường thân khai trên prôphin của răng. Từ vòng cơ sở cho tới đáy răng theo hướng kính là đoạn thẳng. Để tránh hiện tượng cắt chân răng khi gia công người ta thưòng lấy z > 17. Hai bánh răng ãn khớp nhau phải có cùng trị số của môđuyn. 3. Vẽ qui ước đơn giản bánh răng Bánh răng được vẽ qui ước như một khối trụ không có răng. Mặt đỉnh được vẽ bằng nét liền đậm, mặt chia bằng nét gạch chấm mảnh. Nói chung không vẽ mặt đáy trên hình chiếu, nhưng khi cần thì vẽ bằng nét liền mảnh (trên hình cắt lại là nét liền đậm) như trên các hình 6.3 và 6.4. 94 Hình 6.3 Khi cần có thể vẽ một vài răng, phần còn lại vẽ qui ước (hình 6.5). Hình dạng của răng được vẽ như hình 6 .6 . Hình 6.6 Khi vẽ hai bánh răng trụ ăn khớp nhau, cần lưu ý: a. Hai đường tròn chia phải tiếp xúc nhau (hình 6 .8 ); b. Giữa đỉnh răng bánh này và đáy răng bánh kia có một kẽ hở bằng 0,25 m; c. Tại vùng ăn khớp, trên mặt cắt dọc theo hai trục, cần nhớ là không kẻ vật liệu trên mặt cắt của răng và răng của bánh răng chủ động được vẽ là thấy và răng của bánh răng bị động được vẽ là khuất (hình 6.7). Hình 6.7 95 zz Z Z Z Ộ ^ §3. BÁNH RĂNG CÒN Khi vẽ bánh răng côn ta có các mặt côn chia, mật côn đỉnh và mặt côn đáy. Đường kính chia d được xác định ở trên mặt đáy lớn của mặt côn chia và d = m .z (hình 6.9). Nếu góc đỉnh côn chia là 2(p thì ta có quan hệ như sau: d = m .z da = m .z + 2 h, coscp = m (Z + 2 coscp) df = m .z - 2 hf coscp = m (Z - 2,5 cos(p) Chú ý rằng h, và hf được xác định theo đưòfng sinh của mặt côn phụ lớn. íTinh 6.9b là hình cắt đứng và hình chiếu cạnh của một bánh răng côn. Hình 6.8 Khi vẽ một cặp bánh răng côn cần lưu ý: a - Hai mặt côn chia tiếp xúc với nhau; b - Chiều cao răng và kẽ răng giảm dần về phía đỉnh chung của các hình côn; c - Mặt đầu của răng thì vuông góc với đường sinh của mặt côn chia ; d - Răng của bánh chủ động vẽ là thấy. Các dạng ăn khớp khác được vẽ tưcmg tự như trên. Hình 6.10 là hình vẽ bánh vít ăn khớp với trục vít. Cần lưu ý là mặt răng của bánh vít phải cong theo trục vít. Hình 6.11 là bánh răng ăn khớp với thanh răng. 96 Hinh6.11 Khi vẽ các bánh răng lắp trên trục thì cần lưu ý cách vẽ các then nằm giữa moay- ơ của bánh răng và trục như trên các hình 5.25 và 5.26. §4. VẼ QUI ƯỚC LÒ XO Theo hình dáng lò xo chia làm lò xo trụ, nón, lá xoắn, xoáy ốc, đĩa v.v. Theo chức năng làm việc người ta chia làm lò xo kéo, lò xo nén. Lò xo xoắn trụ nén được vẽ như ở hình 6.13. Các đường bao phức tạp của vòng xoắn được thay thế bằng các đoạn thẳng nối các mặt cắt của dây lò xo. Vài ba vòng xoắn đầu và Hình 6.12 97 cuối thì sát gần lại nhau để tạo ra các vòng tỳ ở hai đầu lò xo. Nếu mặt cắt dây xoắn nhỏ hơn 2,5 mm thì bôi đen mặt cắt như hình 6.12 và hình 6.15. Nếu nhỏ hơn 2 mm thì vẽ kiểu sơ đồ đơn giản như hình 6.18. Hinh 6.14 Lò xo kéo thì khi chưa làm việc các vòng xoắn xít vào nhau. Trên bản vẽ lắp, chỉ vẽ các mặt cắt của lò xo, và các đường nét của các chi tiết ở sau lò xo thì chỉ vẽ đến đường tâm của lò xo (hình 6.15). Hlnh 6.15 Hình 6.16 98 Hình 6.16 là hình cắt của lò xo cồn nén, hình 6.17 ià một cuộn iò xo lá xoáy ốc. Hinh 6.18 99 Chương VII DUNG SAI - LẮP GHÉP - ĐỘ NHÁM §1. DUNG SAI KÍCH THƯỚC e: i= o Đ ư ờ n g k h ô n g Trong một nền công nghiệp hiện đại, mỗi chi tiết máy đều được sản xuất đồng loạt một cách tương đối chính xác để sau này khi lắp ráp các chi tiết phải có tính chất đổi lẫn nhau. Dung sai là yếu tố cơ bản tượng trưng cho độ chính xác gia công. Ta xét qua một số định nghĩa. Kích thước danh nghĩa là kích thước thiết kế của một mối ghép lỗ - trục (mặt bao, mặt bị bao) tương ứng với đường không trên hình vẽ 7.1. Phần trên của đường không là giá trị dưcmg và phần dưới íà giá trị âm cùa các sai lệch kích thước, tức là độ sai lệch giữa kích thước thực tế đạt được so vói kích thước danh nghĩa. D, d là kích thước danh nghĩa; Dmax. là các kích thước giới hạn lớn nhất cho phép; Dmin> dmin là các kích thước giới hạn nhỏ nhất cho phép IT là khoảng dung sai nó, là hiệu giữa kích thước giới hạn lớn nhất và kích thước giới hạn nhỏ nhất; ES, es là các sai lệch trên của lỗ và trục; EI, ei là các sai lệch dưới; IT là một giá trị tuyệt đối, thể hiện phạm vi dao động cho phép của kích thước thưc tế. Hình 7.1 100 Tùy theo yêu cầu kv thuật neười ta có thể bố trí khu dung sai dao động quanh kích thước danh nghĩa (đường không) như trên hình 7.2. Chữ hoa là ký hiệu khu dung sai của lỗ và chữ thường là của trục. Khu dung sai H có HI = 0 tức là D,^ i„ = D là dung sai của lỗ cơ sở, còn h có es = 0 tức là = d là dung sai của trục cơ sở. h i i c u L ổ H c ố E Ỉ ~ O ị D ^ ^ = 0 1 go / /ã l ỗ c ơ sở LÓ J s cồ các sai lệch dối xứng ( E S - E i }. -i-cr Ị I ^ Í Ĩ Ỉ I J s Ả ọ Dưòng không a) - ĩ r ụ c h cố cs =0 ~ d) gọi là i r ụ c c ơ s à ■ Trục Ị S cố các sai lộch dổi xứng ( es ~ e i I u ^ ^ ...................... © Diiong k^ iTg_____q t' M IíL H - ^ T r ư c C O s ò b) Hình 7.2 Đối với một kích thước danh nahĩa nhất định, khoảng dung sai càng nhỏ thì cấp chính xác gia công càng lớn. Người ta chia ra làm 20 cấp chính xác, từ 01, 0, 1, 2... đến 18 theo thứ tự độ chính xác giảm dần. Cấp chính xác 01 đến 5 thường áp dụng cho việc chế tạo các dụng cụ đo, các chi tiết thật quan trọng; từ 6 đến 11 là phổ biến cho các chi tiết thông thưòng, còn từ 12 đến 18 là dùng cho các kích thước tự do (không tham gia vào khâu lắp ghép nào). Bảng 6 cho một số thí dụ về khoảng dung sai thông dụng. Bảng 6 Khoảng dung sai (IT) |j,ni \ p = d C â ^ 3-6 >6-10 >10-18 >18 -30 >30 -50 >50 -80 >80 -120 >120 -180 >180 -250 5 4 5 6 8 9 11 13 15 18 20 5 6 8 9 11 13 16 19 22 25 29 7 10 12 15 18 21 25 30 35 40 46 101 Bảng 6 {tiếp theo) \D = d c ấ p \ 3-6 >6-10 >10-18 >18 -30 >30 -50 >50 -80 >80 -120 >120 -180 >180 -250 8 14 18 22 27 33 39 46 54 63 72 9 25 30 36 43 52 62 74 87 100 115 '10 40 48 58 70 84 100 120 140 160 290 11 60 75 90 110 130 160 190 220 250 290 12 100 120 150 180 210 250 300 350 400 460 §2. LẮP GHÉP Khi lắp ghép lỗ với trục (hoặc mặt bao và mặt bị bao) người ta thường phân chia làm ba loại lắp ghép. a. Lắp lỏng : Kích thước lỗ lớn hơn kích thước của trục, nên hiệu số đó gọi là độ hở. b. Lắp c h ặ t: Kích thước của lỗ nhỏ hcín kích thước của trục và hiệu số kích thước gọi là độ dôi. Sau khi lắp các chi tiết bị biến dạng một chút. c. LÂp trung gian : Kích thước của lổ và trục xấp xỉ bằng nhau nên có thể có độ dôi hoặc độ hở tùy theo điều kiện gia công. Khu dung sai của lỗ là Js, K, M, N hoặc của trục là js, k, m, n. Các hệ thống cơ sở khi lắp ghép Hệ thống lỗ : Trong thiết kế nếu chọn miền dung sai H cho lỗ thì miển dung sai của trục sẽ thay đổi tùy theo kiểu lắp ghép mong muốn. a )/iể thông Lõ b ) H ê th ô n g fru c Hình 7.3 Hệ thống trục : Nếu chọn miềm dung sai h cho trục thì miền dung sai của lỗ thay đổi. Khi lắp một ổ bi vào thân máy thì phải chọn hệ trục vì đường kính ngoài của ổ bi là 102 cô' định rồi (không sửa đổi được), còn khi lắp rnột trục và vòiig trong của ổ bi thì lại phải chọn hệ lỗ cơ sở (hình 7.3). Bảng sau đây nêu các mối lắp ghép thông dụng. Bảng 7 Các lắp ghép chính Lỗ Trục H6 H7 H8 H9 H11 Trục lỗ có chuyển động tương đối Độ hở lớn: các chi tiết có dân nở. mặt tiếp xúc dài c 9 11 d 9 Quay trượt trong bạc, giá đỡ (có bôi trơn tốt) € 7 f 6 6-7 Dan hướng chính xác với biên độ nhỏ g 5 Trục lỗ không có chuyển động tương đối Tháo dễ không làm biến dạng chi tiết Mối ghép không truyền lực Lắp bằng tay h V js 6 Lắp dùng vổ k m Tháo sẽ làm hỏng chi tiết Mối ghép truyền lực Lắp ép p ■ vèV' Lắp ép hoặc gia nhiệt s 7 u 7 X 7 §3. CÁCH GHI DUNG SAI VÀ LẮP g hép 0 Xàm đưỏc ưu tịéh sửàạnỹ Trên bản vẽ người ta ghi các sai lệch của một kích thước bằng ba cách sau: 1 - Ghi ký hiệu miền dung sai và cấp chính xác (bằng một con số); 2 - Ghi cụ thể các sai lệch trên và sai lệch dưới của kích thước; 3 - Ghi cả ký hiệu và sai lệch. Thí dụ: 018H 7 hoặc hoặc 018 12e8 hoặc hoăc 12e8(:^;“ ị) trong đó con số trên là sai lệch trên và con số dưới là sai lệch dưới. Tương tự, trên bản vẽ lắp, tại mối ghép lỗ với trục thì ghi dạng phân số: tử số dành cho khu dung sai của lỗ và mẫu số cho khu dung sai của trục: 103 11 n 050H 7/p6 hoăc 0 5 0 — - hoăc 0 5 0 p6 + 0 ,0 2 5 +0,012 + 0 ^ 0 2 6 Sau đây bảng 6 cung cấp các miển dung sai của lỗ và cùa trục hay dùng. Chú ý trong bảng cho các giá trị bằng micromét nhưng khi ghi trên bản vẽ phải đổi chúng thành milimét thí dụ 25 |a.m thành 0,025 vì đơn vị thống nhất trên bản vẽ là milimét. §4. DUNG SAI HÌNH HỌC Sau khi gia công thì bề mặt thực tế đạt được không thể và cũng không cần hoàn toàn trùng với bề mặt danh nghĩa đã qui định. Do đó cũng cần phải qui định hai bề mặt giới hạn song song với bề mặt danh nghĩa để giới hạn bề mặt thực tế phải nằm trong đó (hình 7.4). Bê'măfg/ớròạn Bảng sau đây trình bày các dấu hiệu qui ước của các loại dung sai về hình dáng và vị trí. Bảng 8 Nhóm dung sai Dạng dung sai Dấu hiệu quy ưổc Dung sai độ thẳng Dung sai hình dạng Dung sai độ phẳng / / Dung sai độ tròn o Dung sai độ trụ Dung sai prôphin mặt cắt dọc — Dung sai hình dạng Dung sai hình dạng prôíin cho trước Dung sai hình dạng bề mặt cho trước 104 Bảng 8 (tiếp theo) Nhóm dung sai Dạng dung sai Dâu hiệu quy ước Dung sai đô song song / / Dung sai đố vuông góc JL Dung sai độ nghiêng z Dung sai vị trí - Dung sai độ đồng tâm, đồng trục @ Dung sai độ đối xứng — Dung sai vị trí 1 j Dung sai độ giao nhau của các đương tâm X Dung sai độ đảo hưóng kính, độ đảo mặt mút / Dung sai độ đảo Dung sai độ đảo hướng kính toàn phẩn độ đảo mặt mút toàn phần Sau đây là một số thí dụ vể cách ghi dung sai hình học: (các hình 7.5, 7.6, 7.7). ^-ịO\0.02\ Hỉnh 7.5 Dung sai độ tròn: Prôíin thực mỗi tiết diện thẳng của lỗ phải nằm giữa hai đường tròn đồng tâm có hiệu số các bẳn kính < 0,02 8H9 Mp.dối x ú n g ^■^ cuỡ^ ỉonh Dung sai đối xứng: Mặt phẳng đối xứng của rãnh then phải nằm giữa hai măt phẳng song song cách nhau không quá 0,04 mm và đối xứng nhau qua mặt phẳng A (A là mặt phẳng đối xứng của trục 024, được lấy làm chuẩn) Hình 7.6 105 ữ 1fí W ộuM - Dung sai độ vuông góc: Trục của mặt trụ 018 phải nằm trong giới hạn là hình trụ có đường kính không quá 0,02 mm và vuông góc với bề mặt gờ trục lấy làm chuẩn. Hình 7.7 §5. ĐỘ NHÁM BỀ MẶT Bề mặt sau khi được gia công đều còn lại các vết gia công, tức là có một độ nhám nhất định. Các thông số đánh giá độ nhám một bề mặt là Ra và R, được tính toán như sau: R = yi là sai lệch trung bình số học của đường prôphin “ n = (* I^ +--- + H |o) đường prôphin. R, và R, đểu tính theo micromét (|im) (hình 7.8). Hình 7.8 Bảng sau đây cho ta giá trị R, và R, của 14 cấp độ nhám, và nêu các phưcmg pháp gia công với độ nhám tương ứng đạt được. 106 N h á m b ẽ 'm ặ i Bảng 9: Trị số nhám (um) Chiểu dải Phương pháp gia công Cấp Ra Rz chuẩn (mm) ứng dụng 1 2 3 3 2 0 - 160 1 6 0 -8 0 8 0 -4 0 8 Tiện thô, khoan, cưa, giũa... Các bề mặt không tiếp xúc hay tiếp xúc không quan trọng như: chân máy, giá đỡ, nắp... 4 5 4 0 -2 0 20 - 10 2,5 Tiện tinh, giũa sạch Các bề mặt tiếp xúc tĩnh hay động như; mặt trục vít, 6 2 ,5 - 1,5 mặt mút bánh răng... 0,8 Bề mặt tiếp xúc động với 7 1 ,2 5 -0 ,6 3 Mài, vận tốc cao như mặt răng, 8 0 ,6 3 -0 ,3 2 đánh bóng mặt chốt côn, mặt 9 0 ,3 2 -0 ,1 6 píttỏng... Bề mặt nút van, bi, con 10 11 12 0,16-0,08 0,08-0,04 0,04-0,02 0,25 Mài tinh và các phương pháp khác iăn... 13 0,100-0,050 0,08 Bề mặt làm việc của các 14 0,050 - 0,025 dụng cụ đo, kiểm, mẫu Cách ghi độ nhám bể mặt Ký h ... nh tay của chạc 2 nhờ trục 7. Trục 7 một đầu có vành gờ ở giữa có một núm mỡ 6, dùng để bơm mỡ vào bên trong trục 7 và chui ra rãnh dọc theo trục để bôi trơn bề mặt tiếp xúc giữa trực 7 và bạc lót 11 của puli. Để chặn không cho trục 7 di chuyển theo chiều trục, người ta dùng tấm chắn 9 chèn vào rãnh của đầu trục 7 (xem hình chiếu đứng và hình cắt riêng phần ở hình chiếu cạnh) làm cho trục 7 không di chuyển theo chiểu trục được và cũng không xoay được. Tấm chặn được bắt chặt vào cánh tay của chạc nhờ hai đinh vít 5. Sờ dĩ người ta dùng bạc lót 11 để tiếp xúc với trục 7 vì sau này nếu bạc lót mòn thì có thể thay dễ dàng mà không phải thay puli và trục 7, như vậy kinh tế hơii. Bạc lót được cố định với puli bằng vít 10. Cuối cùng ta phải hình dung được giá đỡ puli gồm các chi tiết cụ thể như trên hình 9.4. Chú ý lỗ ren để lắp vít 10 đợc gia công khi lắp nên khi vẽ tách chi tiết 8 và chi tiết 11 thì không được vẽ một nửa lỗ rcn trên mỗi chi tiết đó. §2. VẼ TÁCH CHI TIẾT TỪ BẢN VẼ LẮP Vẽ tách chi tiết là lập bản vẽ chế tạo chi tiết của bản vẽ lắp thiết kế. Trước khi vẽ tách chi tiêt này thì ta phải đọc các hình biểu diễn có mặt chi tiết đó để cuối cùng tổng hợp lại ta mới hình dung được chính xác hình dáng của chi tiết. Trên mỗi hình biểu diễn của bản vẽ lắp ta chỉ biết được một phần nào đó về cấu tạo của chi tiết ấy. Vậy phải xem tất cả các hình biểu diễn liên quan đến chi tiết đó thì ta mới hình dung được chính xác cấu trúc của chi tiết. Nếu cần ta phác hình chiếu trục đo của nó để đối chiếu lại với bản vẽ lắp xem có phù hợp không . Nếu không thì phải chỉnh lý lại cho chính xác. Sau khi đã hiểu đầy đủ hình dạng và đặc điểm của chi tiết ta tiến hành như sau. 1. Dựa vào độ lớn của tiết máy ta chọn tỷ lệ bản vẽ và khổ giấy để vẽ chi tiết. 2. Dựa vào mức độ phức tạp của chi tiết ta chọn hình chiếu chính (hình chiếu đứng) và ấn định số lượng các hình chiếu, hình cắt, mặt cắt cần thiết. Trên bản vẽ lắp, đối tượng cần thể hiện là vật lắp, còn trên bản vẽ chế tạo chi tiết đối tượng là chi tiết, do đó hình biểu diễn chính của chi tiết trên bản vẽ lắp chưa chắc đã dùng làm hình chính 131 của chi tiết trên bản vẽ chế tạo chi tiết. Tất nhiên đôi lúc chúng cũng trùng nhau, nhưng nói chung phải quan sát cấu tạo của chi tiết mà chọn hình chiếu chính cho nó. 3. Nội dung của bản vẽ tách chi tiết đã được nêu đầy đủ ở bài bản vẽ chế tạo chi tiết, nghĩa là phải đầy đủ các hình biểu diễn để thể hiện được hình dạng của chi tiết, các kích thước có kèm theo sai lệch giới hạn, độ nhám bề mặt, v.v. để phục vụ cho quá trình chế tạo, kiểm tra sau này. o ^11 85 40 26 175 R15 t ” 26 t . 80 Bán kính góc lượn không ghi 2mm Ngày A.06.01 Giá Gang 1 8 - 3 6 Tỉlu' ló ^~sãiir Hỉnh 10.1 4. Sau đó phân bô' các hình biểu diễn trên bản vẽ và tiến hành như bản vẽ chế tạo chi tiết ở phần trên. Bây giờ ta hãy vẽ tách chi tiết giá đỡ 1 trên bản vẽ lắp puli định hớng ở hình 9.3. Sau khi đọc kỹ bản vẽ lắp rồi thì ta phải hình dung được cấu tạo các chi tiết của giá đỡ puli này như trên hình 9.4. Chi tiết 1 chỉ cần ba hình chiếu cơ bản và hai hình cắt riêng phần trên hình chiếu đứng là thể hiện được đầy đủ cấu tạo của nó. Vì không được ghi kích thước và độ nhám 132 vào các đường khuất nên phải cắt riêng phấn hai lỗ để ghi cho hợp lý (hình 10.1). ở đây chi tiêt được đặt ở tư thế làm việc, Thực ra nếu \'ẽ quay 180“ để gân trợ lực ở phía trên thì hai đường khuất ở hình chiếu bằng sẽ thành thấy. Bản vẽ chế tạo chi tiêt 2 (chạc treo) được thể hiện bằng ba hình chiếu cơ bản , một hình chiếu riêng phần A, ba hình cắt riêng phần và một hình phần tử phóng to B (hình trích). Hình chiếu A thể hiện chỗ vát phẳng ở bên ngoài của cánh tay đỡ. ở đây chỉ ghi kích thước xác định hình dáng hình học. Muốn ghi cả các sai lệch giới hạn nữa thì phải trở về bản vẽ lắp hình 9.3, ấn định các điều kiện chức năng rồi lập các chuỗi kích thước cho từng điều kiện chức năng rồi mới có thể tính toán phân bố khu dung sai cho các kích thước chức nãng của từng chuỗi (xem §6 chưcmg VIII) hình 8.2 là bản vẽ tách của chi tiết chạc treo 2 của puli định hướng (hình 9.3). - /4 Không vẽ chi ỉiế ĩ 1 65H9/19 Yêu cầu ky ĩhuật 1. Diện tich Ịiếp xúc giữa bạc với ĩhân và nắp không nhỏ hơn 50% 2. Đảm bảo ớộ hỏ giữa trục và bạc 0,05-0.OSmrr 3. Sau khi lẩp xong ổ írục môi gia công lồ và rãnh dầư 4. Áp lực trên bạc P<29,4PMa 3 Ỉ2 3 Ĩ 03 Th.in 1 G X Ì5 -3 2 7 A. 12.31.07 M .ina ló ! ƠUÓI 9 C j AÌ W F c3 6 / í . 12.31 06 Nủo ỉ G X ĩ 5 -3 2 5 A. 12 31 05 McirìQ lo l tiã n DC uAI ĩO Fe3 4 A 12.31.04 Onq c lìó l 4 C T34 3 A .1 2 .3 Ỉ 03 Dỉìi ốc M 12 -J C T38 Qu lủ /ìg M i. ìx I J J 2 C Ĩ3 8 1 A Ỉ2.31.01 Bắu ơắu 1 CT33 Só vl Kỷ h iệu Tên go i Sổ Ig Vặ! Iiéu G hi chú s Ơ]SIQ ỉh .k éKiếm Ui K ĨN C IKIIỈU. D uyé! ĩò liẽ i Ohũk Ổ Đ ỡ TRUC A .1 2 3 1 .0 0 D ả u k h . la ■ ỈI lũ Tớ S ó tờ ■ 1 Hình 10.1a 133 ứ n g d ụ n g AutoCAD Hình 10.1b VẼ BA CHIỀU H ìn h ba chiều giúp ta dễ h ìn h dung v ậ t thể, n h ấ t là k h i ta cần tạo mô h ình của v ậ t th ể đó. Vẽ h ình ba chiều trong AutoCAD là m ột đề tà i phong phú, p h ần hướng d ẫn tro n g tà i liệu này chỉ để cập đến m ột sô' v ấn đề cơ b ả n m à người mối n h ập m ôn cần nắm vững. Sau khởi động AutoCAD 2004 ta ở trong không gian vật thể, đây là không gian chủ yếu cho phép ta xây dựng mô hình của vật thể và được diễn tả bởi trang có nhãn Model (hình 10.2). tề -i « r © r A / - Nhãn Models/1 N K Ì1 AutoCAD Express Tools Menu ioaded,__ Command; [M Ì637Ĩ7Ĩ12148.Ó.OŨOr^ - = SN ^ I GRIDl ŨRTHG: PŨLARị ŨSNAP ilo TO C K LV/tỊỊ mi^ 134 Hình 10.2 Muốn vẽ một vật thể kỹ thuật ta sử dụng các lệnh tạo các khối đặc cơ bản và các lệnh kết hợp các khối đó làm thành vật thể đã cho. Dưới đây là phần hướng dẫn thực hành xây dựng mô hình 3 chiều của một vật thể. Giả sử ta cần vẽ hình chiếu trục đo vuông đều của chi tiết mặt bích cho ở hình 10.3. 060 040 20 Hình 10.3 12D Trong trang có nhãn Model trước hết ta thực hiện một số lệnh vẽ hai chiéu. Command: CIRCLE J Vẽ đường tròn đường kính 60 (hình 10.4). Specify center point for circle or [3P/2P/Ttr (tan tan radius)]: Chọn một điểm ở khoảng giữa màn hình làm tâm o của đường tròn. Speciíy radius of circle or [Diameter] : 30 J Command: J Vẽ đường tròn cíưctng kính 12. Specity center point for circle or [3P/2P/Ttr (tan tan radius)], FROM J Base point: CEN J of Chọn điểm P l. : @0,60 J Speciíy radius of circle or [Díameter]: 6 J Command: J Vẽ đường tròn bán kính 12. Speciíy center point for circle or [3P/2P/Ttr (tan tan radius)]: @ J Specity radius of circle or [Diameter]: 12 J Command: LINE J Vẽ tiếp tuyến đi qua điểm P4. Hinh 10.4 135 Specify first point: TAN J to Chọn điểm P2. Specify next point or [Undo]: TAN J to Chọn điểm P3. Speciíy next point or [Undo]: J Tưcmg tự, vẽ tiếp tuyến đi qua điểm P5. Command: MIRROR J Vẽ đối xứng (hình 10.5). Select objects: Chọn hai đường tròn đồng tâm ở phía bên trái và các tiếp tuyến đi qua P4 và P5. Select objects; J Specify first point of mirror line: CEN J of Chọn điểm P2. Speciíy second point of mirror line: @0,10 J Delete source objects? [Yes/No] : J Hình 10.5 Command: TRIM J cắt tỉa các đoạn thừa. Select cutting edges ... Select objects: Chọn 4 tiếp tuyến làm các cạnh cắt. Select objects: J Select object to trim or shitt-select to extend or [ProjecưEdge/Undo]: Chọn các cung tròn Pl, P2, P3, và P6. Select object to trim or shift-select to extend or [ProjecưEdge/Undo]: J Command: REGION J Tạo một miền đóng kín giới hạn bởi đường bao đi qua điểm P9. Select objects: Chọn các đoạn thẳng và cung tròn tạo thành miến đóng kín. Select objects: J Command; J Tạo một miền đóng kín giới hạn bởi đường tròn đi qua điểm P7. Select objects: Chọn điểm P7. Select objects: J Command: J Tạo một miền đóng kín giới hạn bởi đường tròn đi qua điểm P8, Select objects: Chọn điểm P8. Select objects: J Hình 10.6 136 Command: SUBTRACT J Khoét rỗng miền kín bằng hai miền tròn nhỏ. Select solids and regions to subtract from .. Select objects: Chọn điểm P9. Select objects: J Select solids and regions to subtract Select objects; Chọn lần lưgrt điểm P7 và P8. Select objects: J Miền được tạo thành diễn tả mặt dưới của phẩn đế chi tiết. Ta sẽ dùng lệnh EXTRUDE để quét miền này dọc theo trục z tạo thành đế của chi tiết. Để chuẩn bị cho việc hiển thị hình ảnh ba chiều được rõ ràng ta cần đặt trước giá trị của một số biến hệ thống như sau: Command: VIEVVRES J Do you want fast zooms? [Yes/No] : J Enter circle zoom percent (1-20000) : 20000 J Command: ISOLINES J Enter new value for ISOLINES : 2 J Command: DISPSILH J Enter new value for DISPSILH : 1 J Command: PACETRES J Enter new value for PACETRES : 2 J Hình 10.7 Để có thể quan sát vật thể theo ba chiều ta chọn điểm nhìn có toạ độ là (1,-1,1), đây là toạ độ của điểm nhìn cho ta hình chiếu trục đo vuông đều của chi tiết. Chọn điểm nhìn bằng lệnh VPOINT. Command: VPOINT J Current view direction: VIEWDIR=0.0000,0.0000 1.0000 Specify a view point or [Rotate] : J Xuất hiện biểu tượng của hệ trục toạ độ trong hình chiếu trục đo vuông đều (hình 10.7). Command: EXTRUDE J Tạo khối bằng cách quét (hình 10.8). Select objects: Chọn một điểm trên đường bao của miền vừa tạo thành (điểm P9). Select objects: J Specify height of extrusion or [Path]: 18 J Specity angle of taper for extrusion: J Hinh 10.8 137 Command: CYLINDER J Vẽ mặt trụ (j)60. Specify center point for base of cylinder or [Elliptical] : CEN J of Chọn điểm PIO. Specity radius for base of cylinder or [Diameter]: 30 J Speciíy height of cylinder or [Center of other end]; 35 J Command; J Vẽ mặt trụ cị)40. Speciíy center point for base of cylinder or [Elliptlcal] : CEN J of Chọn điểm P11. Speclty radius for base of cylinder or [Diameter]: 20 J Specity height of cylinder or [Center of other end]: - 53 J Command: UNION J Hợp nhất khối đế và khối trụ lớn. Select objects: Chọn điểm P11. Select objects: Chọn điểm P12. Select objects: J Command; SUBTRACT J Khoét rỗng vật thể bằng khối trụ c|)40. Select solids and regions to subtract from .. Select objects: Chọn điểm P11. Select objects; J Select solids and regions to subtract.. Select objects: Chọn điểm P13. Select objects: J Ta nhận được hình vẽ như ỏ hình 10.10. Bây giờ ta tiến hành vẽ một khối hình hộp để tạo rãnh xẻ ở đầu trên ống trụ của mặt bích. Command; BOX J Vẽ khối hộp. Speciíy corner of box or [CEnter]: Chọn điểm P14 ở một vị trí tuỳ ý trên màn hình. Speciíy corner or ỊCube/Length]: L J Specify length: 20 J Speciíy width; 60 J Specity height: 15 J Hình 10.9 Hình 10.11 138 Command: MOVE J Di chuyển khối hình hộp. Select objects: Chọn khối hình hộp (điểmP15). Select objects: J Specify base point or displacement: MID J of Chọn điểm P15. Speciíy second point of displacement or : QUA J of Chọn điểm P l l . Command: SUBTRACT J Khoét khối mặt bích bằng khối hình hộp. Select solids and regions to subtract from .. Select objects: Chọn khối mặt bích (điểm P12). Select objects: J Select solids and regions to subtract.. Select objects: Chọn khối hình hộp (điểm P16), Select objects: J Hình 10.12 Ta nhận được kết quả như ở hình 10.13, hình này trình bày tất cả các nét thấy và nét khuất, ta có thể dùng lệnh HIDE để dấu các nét khuất. Command: HIDE J Các nét khuất đươc dấu đi như ở trên hình 10.14. Muốn trở lại hình biểu diễn có các nét khuất, ta nhập lệnh REGEN. Command: REGEN J 139 Ta có thể tạo được hình ảnh của vật thể sau khi được tô bóng nhờ lệnh RENDER. Command; RENDER J Xuất hiện hộp thoại Render (hình 10.15), trong hộp thoại này ta nhập các lựa chọn như sau Rendering type: Photo Real Destination: Vievvport Sub Sampling 1:1 (Best) và đánh dấu vào các ô kiểm I I Smooth Shade 1 Apply Materials Eendeíing T>>pe: Photo Real xj ; Rendefb^ pfcx:edufe.... r * f lu e íy Í0f Selecưcrts ; f ~ C ro p ^ in d o v v ; r S ịs p R e n d e í D ia ỉog L ỉgh t Icon S caie: SnK>olhingAji^ e: 45 Rendeting O p tio n s ' ĩ ? Smoolh Shđde p Appiy Mâteíials r~ Shỏdows r~ R e n d e t£ ô c h e More O i^ions... S y b S a m p lin g ------- ịv ie w p 0ít W id lh ; 714 H e igh t ; 384 C o lã s ; 32-brts l . l ( B e s t ) 3 Ê a c k í^o u n d ... £ o g /T )e p th Cue... của mục Rendering Options. Sau khi nhấn nút Render ở phía dưới hộp thoại ta nhận được hình biểu diễn ba chiều có tô bóng như ở hình 10.16, nguồn sáng sử dụng ở đây là nguồn sáng mặc định. Đối với các vật thổ có hình dạng phức tạp hơn ta phải bố trí nguồn sáng thích hợp để làm rõ các chi tiết cần biểu diễn. Muốn trở lại hình biểu diỗn có các nét khuất như khi chưa tô bóng ta nhập lệnh REGEN. Render Cance! H d p Hình 10.15 Hình 10.16 140 TÀI LIỆU THAM KHẢO 1. Bài giảng vẽ cơ khí (1970) Phạm Văn Nhuần 2. Bản dịch tiêu chuẩn Quốc tế, (2002) Trần Hữu Quế, Nguyễn Văn Tuấn về vẽ kỹ thuật 3. Bài tập vẽ kỹ thuật Trần Hữu Quế, Nguyễn Văn Tuấn. 4. Bài tập vẽ kỹ thuật (2001) Trần Hữu Quế. 141 33 7 8 10 [0 11 12 14 19 21 MỌC LỤC Lời nói đầu Chương I. §1. Khái niệm chung §2. Vật liệu và dụng cụ vẽ §3. Cách sử dụna một số dụng cụ §4. Sử dụng vi tính trong thiết kế C hương II. §1. Qui cách trình bày bản vẽ §2. Khổ bản vẽ §3. Tỷ lệ §4. Chữ và chữ số §5. Các loại nét vẽ §6. Ký hiệu vật liệu trên mạt cắt §7. Ghi kích thước - ứng dụng AutoCAD C hương IU . Vẽ h ìn h học § 1. Chia đều đoạn thẳng \'à đường tròn ' §2. Độ dốc \'à độ côn §3. Vẽ nối tiếp §4. Các dưòng cong hình liọc thường gạp - ứng dụng AutoCAD C hương IV . C ác h ình biểu diẽn §1. Hình chiếu §2. Mặt cắt §3. Hình cắt §4. Hình chiếu có trục đo §5. Hình biểu diễn vật thể rỗng §6. Biểu diễn các mặt chuyển tiếp - ứng dụng AutoCAD Chương V. C ác m ôi ghép nôi §1. Ghép bằng ren §2. Ghép nối bằng then 142 32 32 33 37 53 57 59 63 70 72 72 76 8 7 §3. MỐI ỉỉhép bãii2 điiìh tán §4. MỐI ghép bãiia hàn C hương Vì. Biểu dién bánh rãng §1. Khái niệm cơ bản §2. Bánh răng trụ §3. Bánh rãna cỏn i^ 4. Vẽ qui Lrớc lò xo C hương VU. D ung sai - Láp ghép - Độ nhám §1. Dunti sai kích thước §2. Lắp ghép ^3. Cách ghi dung sai và lắp ghép §4. Dung sai hình học §5. Độ nhám bề mặt C hương VIII. Bản vẽ chi tiết §1. llhg dụng của bản vẽ chi tiết §2. Nội dung của bản vẽ chi tiết §3. Quvết định số lượng hình biểu diễn cho chi tiêì §4. Trình tự liến hành cụ thê §5. Ghi kích thước cho chi tiết §6. Ghi kích thước chức năng trên bản vẽ lắp C hương IX. Bản vẽ lắp §1. Nội dung và yêu cầu của bản vẽ lắp §.2 Trình tự tiến hành cụ thể §3. Cách đánh số vị trí clio các chi tiết máy §4. Một số qui ước đơn íỉiản hóa và một vài khái niệm về công nghệ chê' tạo máy - ứng dụng AutoCAD C hương X. Đọc bản vẽ lắp, vẽ tách chi tiết từ bản vẽ láp § 1. Đọc bản vẽ lắp §2. Vẽ tách chi tiết từ bản vẽ lắp - úhg dụng AutoCAD Tài liệu tham khảo 89 90 92 93 96 97 100 102 103 104 106 109 109 110 110 113 114 120 121 122 122 126 130 131 134 141 143
File đính kèm:
ve_ky_thuat_co_huong_dan_ky_thuat_autocad_phan_2.pdf