Bài giảng Kỹ thuật gia công cơ khí
1. Mục đích, yêu cầu và vị trí môn học
1.1. Mục đích của môn học
- Cung cấp kiến thức cơ bản về các phương pháp gia công kim loại trong cơ khí.
- Làm quen với một số thiết bị cơ bản của các phương pháp gia công kim loại.
- Biết và có thể lập một số quy trình gia công đơn giản, là cơ sở cho môn học công nghệ chế
tạo, công nghệ sửa chữa.
1.2. Yêu cầu của môn học
- Nắm được bản chất, đặc điểm và phạm vi áp dụng của từng phương pháp gia công kim loại.
- Biết vận dụng vào quá trình sản xuất thực tế:
+ Chọn được phương pháp gia công.
+ Chọn được thiết bị gia công.
+ Thiết lập được trình tự gia công.
1.3. Vị trí môn học
Kỹ thuật gia công cơ khí là môn tiếp theo của môn vật liệu học và chỉ ra các phương pháp gia
công làm cơ sở cho các môn chuyên ngành.
2. Nội dung môn học
Kỹ thuật gia công cơ khí là môn học nghiên cứu khái quát quá trình sản xuất, tính chất và
phương pháp gia công kim loại và hợp kim để chế tạo các chi tiết hoặc các kết cấu trong các máy
móc hoặc các công trình công nghiệp.
- Sản xuất đúc.
- Gia công kim loại bằng áp lực.
- Hàn và cắt kim loại.
- Gia công kim loại bằng cắt gọt.
- Gia công trên máy CNC.
3. Một số khái niệm cơ bản
3.1. Một số định nghĩa cơ bản trong quá trình sản xuất cơ khí
- Chi tiết máy là bộ phận nhỏ nhất không tháo rời được và đảm nhiệm một công dụng nhất
định.
- Phôi chỉ vật phẩm ở đầu của một quá trình sản xuất hoặc một quá trình công nghệ.16
- Quá trình công nghệ là một phần của quá trình sản xuất cơ khí, thực hiện một nhiệm vụ xác
định.
- Sản phẩm là vật phẩm đầu ra của quá trình sản xuất hoặc một qúa trình công nghệ.
3.2. Quá trình sản xuất cơ khí
- Quá trình sản xuất cơ khí là một quá trình tác động của con người vào vật liệu thông qua các
công cụ lao động nhằm tạo ra các sản phẩm theo yêu cầu
Tóm tắt nội dung tài liệu: Bài giảng Kỹ thuật gia công cơ khí
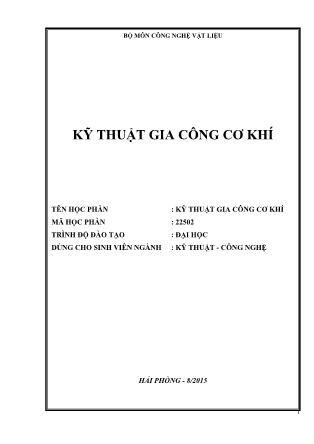
1 BỘ MÔN CÔNG NGHỆ VẬT LIỆU KỸ THUẬT GIA CÔNG CƠ KHÍ TÊN HỌC PHẦN : KỸ THUẬT GIA CÔNG CƠ KHÍ Mà HỌC PHẦN : 22502 TRÌNH ĐỘ ĐÀO TẠO : ĐẠI HỌC DÙNG CHO SINH VIÊN NGÀNH : KỸ THUẬT - CÔNG NGHỆ HẢI PHÒNG - 8/2015 2 MỤC LỤC STT NỘI DUNG TRANG Bài mở đầu 12 1. Mục đích, yêu cầu và vị trí môn học 12 2. Nội dung môn học và tài liệu tham khảo 12 3. Một số khái niệm cơ bản 12 Phần I. Chế tạo phôi 15 Chương 1. Khái niệm cơ bản về sản xuất đúc 15 1.1. Bản chất, đặc điểm, công dụng và phân loại sản xuất đúc 15 1.2. Nguyên lý thiết kế chi tiết đúc 16 1.3. Đúc các hợp kim 17 Chương 2. Đúc trong khuôn cát 24 2.1. Các bộ phận cơ bản của khuôn đúc 24 2.2. Quá trình sản xuất vật đúc trong khuôn cát 25 2.3. Hỗn hợp làm khuôn và lõi 25 2.4. Các phương pháp làm khuôn và lõi 29 2.5. Thiết kế và chế tạo lõi 33 2.6. Chọn hòm khuôn 35 2.7. Hệ thống rót 35 Chương 3. Các phương pháp đúc Đặc biệt 43 3.1. Đúc trong khuôn kim loại 43 3.2. Đúc dưới áp lực 44 3.3. Đúc ly tâm 46 3.4. Đúc mẫu chảy 47 3.5. Đúc liên tục 48 3.6. Kiểm tra khuyết tật vật đúc 49 Chương 4. Các khái niệm cơ bản về gia công áp lực 51 4.1. Thực chất và đặc điểm của gia công áp lực 51 4.2. Các định luật cơ bản dùng trong gia công áp lực 51 4.3. Nung kim loại trước khi gia công áp lực 53 4.4. Làm nguội sau khi gia công áp lực 57 Chương 5. Các phương pháp gia công kim loại bằng áp lực 59 3 5.1. Cán kim loại 59 5.2. Kéo kim loại 61 5.3. Ép kim loại 64 5.4. Rèn tự do 65 5.5. Rèn khuôn - rập khối, rập thể tích 68 5.6. Rập tấm - rập nguội 70 Chương 6. Các khái niệm cơ bản về hàn và cắt kim loại 77 6.1. Bản chất, đặc điểm và phân loại các phương pháp hàn 77 6.2. Qúa trình luyện kim khi hàn nóng chảy 78 6.3. Tổ chức kim loại mối hàn khi hàn nóng chảy 79 Chương 7. Hàn hồ quang tay 82 7.1. Khái nịêm 82 7.2. Nguồn điện hàn, điện cực hàn và máy hàn 83 7.3. Phân loại hàn hồ quang 88 7.4. Công nghệ hàn 89 7.5. Các chuyển động của que hàn và kỹ thuật hàn 93 7.6. Hàn và cắt kim loại bằng hồ quang dưới nước 97 Chương 8. Hàn tự động 98 8.1. Khái niệm, đặc điểm và lĩnh vực áp dụng hàn tự động 98 8.2. Các phương pháp hàn tự động 99 8.3. Thiết bị hàn tự động 101 8.4. Chế độ hàn tự động dưới lớp thuốc 104 Chương 9. Hàn và cắt kim loại bằng ngọn lửa khí 106 9.1. Thực chất và đặc điểm hàn kim loại 106 9.2. Khí hàn 106 9.3. Thiết bị hàn khí 107 9.4. Ngọn lửa hàn khí 107 9.5. Cắt kim loại bằng ngọn lửa khí 111 Chương 10. Tính hàn của kim loại và hợp kim 114 10.1. Khái niệm chung 114 10.2. Hàn các kim loại và hợp kim 114 Chương 11. Biến dạng và ứng suất khi hàn các dạng khuyết tật hàn và các phương pháp kiểm tra 119 4 11.1. Sự tạo thành ứng suất khi hàn 120 11.2. Các biện pháp giảm ứng suất và biến dạng khi hàn 121 11.3. Các dạng khuyết tật mối hàn và các phương pháp kiểm tra 122 Phần II. Gia công cắt gọt kim loại 127 Chương 12. Khái niệm cơ bản về gia công cắt gọt kim loại 127 12.1. Thực chất, đặc điểm và công dụng của gia công cắt gọt 127 12.2. Các chuyển động cơ bản trong gia công cắt gọt 127 12.3. Một số dạng tạo hình cơ bản 128 12.4. Các phương pháp gia công cắt gọt cơ bản 129 12.5. Cấu tạo và các thông số hình học của dụng cụ cắt 340 12.6. Các thông số hình học của lớp phoi cắt 132 12.7. Sự tạo thành phoi và các dạng của phoi 133 12.8. Cơ sỏ vật lý của quá trình cắt gọt 134 Chương 13. Phương pháp xác định chế độ cắt 140 13.1. Các khái niệm cơ bản 140 13.2. Thông số chế độ cắt 140 13.3. Quan điểm lựa chọn chế độ cắt 142 13.4. Các phương pháp xác định chế độ cắt 142 Chương 14. Gia công trên nhóm máy tiện 146 14.1. Bản chất, đặc điểm và công dụng của gia công tiện 146 14.2. Máy tiện và dao tiện 146 14.3. Những công việc tiến hành trên máy tiện 150 Chương 15. Gia công trên nhóm máy phay 157 15.1. Bản chất, đặc điểm và công dụng của phay 157 15.2. Các phương pháp phay cơ bản 157 15.3. Máy phay và dao phay 159 15.4. Những công việc tiến hành trên máy phay 160 Chương 16. Gia công lỗ 162 16.1. Bản chất, đặc điểm và công dụng 162 16.2. Các phương pháp gia công lỗ 162 Chương 17. Gia công trên nhóm máy mài 166 17.1. Bản chất, đặc điểm và công dụng 166 17.2. Cấu tạo của đá mài 166 5 17.3. Phân loại và phương pháp lựa chọn đá mài khi gia công 167 17.4. Những công việc cơ bản tiến hành trên máy mài 169 6 ĐỀ CƯƠNG CHI TIẾT Tên học phần: Kỹ thuật gia công cơ khí Mã HP: 22502 a. Số tín chỉ: 3 TC BTL ĐAMH b. Đơn vị giảng dạy: Bộ môn Công nghệ vật liệu c. Phân bổ thời gian: - Tổng số (TS): 50 tiết. - Lý thuyết (LT): 34 tiết. - Thực hành (TH): 10 tiết. - Bài tập (BT): 4 tiết. - Hướng dẫn BTL/ĐAMH (HD): 0 tiết. - Kiểm tra (KT): 2 tiết. d. Điều kiện đăng ký học phần: Đăng ký học sau học phần Vật liệu kỹ thuật e. Mục đích, yêu cầu của học phần: Kiến thức: Cung cấp kiến thức cơ bản về các phương pháp gia công kim loại trong ngành cơ khí -Quá trình sản xuất đúc; -Công nghệ hàn tay và hàn tự động; -Các phương pháp gia công trong gia công áp lực; - Các phương pháp gia công trong gia công cắt gọt. Kỹ năng: Hướng dẫn cho sinh viên nắm được các kỹ năng: -Nguyên tắc bố trí, tính toán khuôn đúc, nguyên lý thiết kế vật đúc; -Tính toán các hệ thống gia công áp lực: cán, kéo, rập; -Tính toán các thông số công nghệ khi hàn; -Tính toán thông số chế độ cắt khi tiện, phay -Kỹ năng thực hành gia công trên máy cắt gọt, kiểm tra khuyết tật mối hàn; Thái độ nghề nghiệp: Có tinh thần cố gắng trong học tập , có ý thức trong vận hành máy gia công cắt gọt, máy siêu âm mối hàn, chịu khó tìm hiểu các kiến thức liên quan đến thực tế nhằm trang bị kiến thức tốt để phục vụ cho chuyên môn sau khi ra trường f. Mô tả nội dung học phần: Học phần Kỹ thuật gia công cơ khí bao gồm những nội dung kiến thức: Giới thiệu về các phương pháp gia công kim loại, hợp kim cơ bản trong gia công cơ khí bao gồm: sản xuất đúc; gia công kim loại bằng áp lực; hàn cắt kim loại và gia công kim loại bằng 7 cắt gọt để chế tạo các chi tiết hoặc các kết cấu trong các máy móc hoặc các công trình công nghiệp. g. Người biên soạn: Nguyễn Anh Xuân - Bộ môn Công nghệ vật liệu h. Nội dung chi tiết học phần: TÊN CHƯƠNG MỤC PHÂN PHỐI SỐ TIẾT TS LT BT TH HD KT Chương 1. Khái niệm cơ bản về sản xuất đúc 2 2 1.1. Bản chất, đặc điểm, công dụng và phân loại sản xuất đúc 0,5 0,5 1.2. Nguyên lý thiết kế chi tiết đúc 0,5 0,5 1.3. Đúc các hợp kim 1 1 Tự học (4t) -Đọc thêm về quá trình sản xuất cơ khí; -Tìm hiểu qui trình sản xuất các chi tiết theo sơ đồ sản xuất cơ khí; -Xem lại bản chất các loại vật liệu như thép, gang, hợp kim đồng, nhôm , đánh giá tính đúc của những hợp kim này. Chương 2. Đúc trong khuôn cát 6,5 2,5 1 3 2.1. Các bộ phận cơ bản của khuôn đúc 0,5 0,5 2.2. Quá trình sản xuất vật đúc trong khuôn cát 0,5 0,5 2.3. Hỗn hợp làm khuôn và lõi 0,5 0,5 2.4. Các phương pháp làm khuôn và lõi 0,5 0,5 2.5. Thiết kế hòm khuôn và lõi 0,5 0,5 Thực hành 3 3 Bài tập thiết kế đúc 1 1 Tự học (5t) -Xem lại kiến thức chương 1; -Tự đọc phần các phương pháp làm khuôn trên máy 8 -Tìm hiểu thêm những chi tiết có thể sử dụng phương pháp đúc trong khuôn cát ; -Tự đưa ra bản vẽ chi tiết đúc và tính toán thông số khuôn đúc Chương 3. Các phương pháp đúc đặc biệt 2,5 2,5 3.1. Đúc trong khuôn kim loại 0,5 0,5 3.2. Đúc dưới áp lực 0,5 0,5 3.3. Đúc ly tâm 0,5 0,5 3.4. Đúc mẫu chảy 0,5 0,5 3.5. Đúc liên tục 0,5 0,5 Tự học (5t) -Tìm hiểu thêm các chi tiết đúc có thể đúc bằng các phương pháp đúc đặc biệt ở trên; -Tìm hiểu thêm các phương pháp đúc đặc biệt khác như đúc mẫu cháy, đúc bán lỏng Chương 4. Các khái niệm cơ bản về gia công áp lực 2 2 4.1. Thực chất và đặc điểm của gia công áp lực 0,5 0,5 4.2. Các định luật cơ bản trong gia công áp lực 0,5 0,5 4.3. Nung kim loại trước khi gia công áp lực 0,5 0,5 4.4. Làm nguội sau khi gia công áp lực 0,5 0,5 Tự học (4t) -Xem lại ký hiệu mác thép, cách tính nhiệt độ gia công theo giản đồ trạng thái; -Tự đưa ra các mác thép và thực hiện tính khoảng nhiệt độ gia công cho thép đó Chương 5. Các phương pháp gia công kim loại bằng áp lực 5 3 1 1 5.1. Cán kim loại 0,5 0,5 5.2. Kéo kim loại 0,5 0,5 9 5.3. Ép kim loại 0,5 0,5 5.4. Rèn tự do 0,5 0,5 5.5. Rèn khuôn( rập khối, rập thể tích) 0,5 0,5 5.6. Rập tấm - rập nguội 0,5 0,5 Bài tập gia công áp lực 1 1 Kiểm tra 1 1 Tự học (6t) -Xem lại phần bản chất đặc điểm gia công áp lực; -Tìm hiểu các chi tiết, sản phẩm được gia công bằng các phương pháp trên. Chương 6. Các khái niệm cơ bản về hàn và cắt kim loại 2 2 6.1. Bản chất, đặc điểm và phân loại các phương pháp hàn 1 1 6.2. Qúa trình luyện kim khi hàn nóng chảy 0,25 0,25 6.3. Tổ chức kim loại mối hàn khi hàn nóng chảy 0,75 0,75 Tự học(4t) -Xem lại trước giản đồ trạng thái Fe-C; -Nguyên tắc vẽ tổ chức austenit, peclit, ferit. Chương 7. Hàn hồ quang tay 4,5 3,5 1 7.1. Khái niệm 0,5 0,5 7.2. Nguồn điện hàn, điện cực hàn và máy hàn 0,5 0,5 7.3. Phân loại hàn hồ quang 0,5 0,5 7.4. Công nghệ hàn 1,5 1,5 7.5. Hàn và cắt kim loại bằng hồ quang dưới nước 0,5 0,5 Bài tập tính toán chế độ hàn hồ quang tay 1 1 Tự học(7t) -Tự đọc phần cách gây hồ quang; -Tự đọc phần các loại máy hàn dùng dòng điện một 10 chiều, xoay chiều. Chương 8. Hàn tự động 1,5 1,5 8.1. Khái niệm, đặc điểm và lĩnh vực áp dụng hàn tự động 0,25 0,25 8.2. Các phương pháp hàn tự động 0,5 0,5 8.3. Thiết bị hàn tự động 0,25 0,25 8.4. Chế độ hàn tự động 0,5 0,5 Tự học (3t) -Tìm hiểu các phương pháp hàn tự động trong đóng tàu Chương 9. Hàn và cắt kim loại bằng ngọn lửa khí 1,5 1,5 9.1. Thực chất và đặc điểm 0,25 0,25 9.2. Khí hàn 0,25 0,25 9.5. Phân loại phương pháp hàn khí 0,5 0,5 9.6.Chế độ hàn khí 0,25 0,25 9.7. Cắt kim loại bằng ngọn lửa khí 0,25 0,25 Tự học (3t) -Tự đọc phần 9.3 thiết bị hàn khí và 9.4 ngọn lửa hàn khí -Tìm hiểu các thiết bị hàn khí dùng trong ngành đóng tàu Chương 10. Tính hàn của kim loại và hợp kim 1,5 1,5 10.1. Khái niệm chung 0,5 0,5 10.2. Hàn các kim loại và hợp kim 1 1 Tự học(3t) -Xem lại ký hiệu mác thép; -Đưa ra một số mang thép và đánh giá tính hàn. Chương 11. Biến dạng và ứng suất khi hàn các dạng khuyết tật hàn và các phương pháp kiểm tra 5 2 3 11 11.1. Sự tạo thành ứng suất khi hàn 0,5 0,5 11.2. Các biện pháp giảm ứng suất và biến dạng khi hàn 0,5 0,5 11.3. Các dạng khuyết tật mối hàn và các phương pháp kiểm tra 1 1 Thực hành 3 3 Tự học (4t) -Đọc trước các dạng khuyết tật mối hàn, tìm hiểu nguyên nhân; -Tìm hiểu nguyên lý kiểm tra khuyết tật mối hàn Chương 12. Khái niệm cơ bản về gia công cắt gọt kim loại 2 2 12.1. Thực chất, đặc điểm và công dụng của gia công cắt gọt 0,5 0,5 12.2. Các chuyển động cơ bản trong gia công cắt gọt và các phương pháp gia công cắt gọt cơ bản 0,5 0,5 12. 3. Cấu tạo và các thông số hình học của dụng cụ cắt 0,5 0,5 12.4. Cơ sở vật lý của quá trình cắt gọt 0,5 0,5 Tự học(4t) -Tự đọc các dạng bề mặt gia công; -Tìm hiểu thêm các loại dao cắt trong gia công; Chương 13. Phương pháp xác định chế độ cắt 2 1 1 13.1. Thông số chế độ cắt 0,5 0,5 13.2. Quan điểm lựa chọn chế độ cắt 0,25 0,25 13.3. Các phương pháp xác định chế độ cắt 0,25 0,25 Bài tập tính toán chế độ gia công cắt gọt 1 1 Tự học (2t) -Sử dụng phần mềm của bộ môn tính chế độ cắt 12 Chương 14. Gia công trên nhóm máy tiện 4 2 2 14.1. Bản chất, đặc điểm và công dụng của gia công tiện 0,5 0,5 14.2. Máy tiện và dao tiện 0,5 0,5 14.3. Những công việc tiến hành trên máy tiện 1 1 Thực hành 2 2 Tự học (4t) -Đọc các dụng cụ phụ trên máy tiện ; -Tự đọc cách gá kẹp phôi trên máy tiện. Chương 15. Gia công trên nhóm máy phay 3 2 1 15.1. Bản chất, đặc điểm và công dụng của phay 0,5 0,5 15.2. Các phương pháp phay cơ bản 0,5 0,5 15.3. Máy phay và dao phay 0,5 0,5 15.4. Những công việc tiến hành trên máy phay 0,5 0,5 Thực hành 1 1 Tự học (4t) -Đọc các dụng cụ phụ trên máy phay ; -Tự đọc cách gá kẹp phôi trên máy phay. Chương 16. Gia công lỗ 3,5 1,5 1 1 16.1. Bản chất, đặc điểm và công dụng 0,5 0,5 16.2. Các phương pháp gia công lỗ 1 1 Thực hành 1 1 Kiểm tra 1 1 Tự học (3t) -Tìm hiểu các loại dụng cụ gia công lỗ tại bộ môn ; -So sánh khả năng công nghệ của các phương pháp gia công lỗ. Chương 17. Gia công trên nhóm máy mài 1,5 1,5 13 17.1. Bản chất, đặc điểm và công dụng 0,5 0,5 17.2. Cấu tạo của đá mài 0,25 0,25 17.3. Phân loại và phương pháp lựa chọn đá mài khi gia công 0,25 0,25 17.4. Những công việc cơ bản tiến hành trên máy mài 0,5 0,5 Tự đọc (3t) -Tìm hiểu về tiêu chuẩn độ bóng bề mặt sau khi gia công; -Tự đọc các phương pháp mài khôn, mài nghiền i. Mô tả cách đánh giá học phần: Điều kiện để được dự thi cuối học kỳ: Điều kiện để được dự thi cuối học kỳ: Sinh viên phải có mặt trên lớp 75% tổng số tiết của học phần; 1. X1 :Điểm ý thức, thái độ trên lớp; X1 4; 2. X2: Điểm kiểm tra kiến thức tự học; X2 4. 3.X3: Điểm kiểm tra vận dụng kiến thức; X3 4 4. X4: Điểm thực hành; X4 4 Điểm X=0,2X1+0,2X2+0,3X3+0,3X4 Hình thức thi viết, 90 phút, rọc phách; Y – điểm thi kết thúc học phần, Y>=2; nếu Y<2 thì Z=0 Điểm đánh giá học phần : Z = 0,5X + 0,5Y. Thang điểm A+, A, B+, B, C+, C, D+, D, F k. Giáo trình: 1. Bộ môn Công nghệ vật liệu. Kỹ thuật gia công cơ khí . Trường ĐH Hàng Hải. l. Tài liệu tham khảo: 1. Trần Hữu Tường. Công nghệ kim loại.- Nhà xuất bản ĐH và TH chuyên nghiệp,1972; 2. Phạm Đình Sùng. Công nghệ gia công kim loại. Nhà xuất bản xây dựng,1998; 3. Phạm Quang Lộc. Kỹ thuật đúc. Nhà xuất bản Thanh niên, 2000; 4. Ngô Lê Thông. Công nghệ hàn . Nhà xuất bản Khoa học kỹ thuật, 2007; 5. Bành Tiến Long. Nguyên lý gia công vật liệu. Nhà xuất bản Khoa học kỹ thuật, 2001; 14 6. Trần Thế San - Thực hành cơ khí tiện - phay - bào mài - Nxb. Th. phố Hồ Chí Minh ,2000; m. Ngày phê duyệt: 5/10./2015 n. Cấp phê duyệt: Viện trưởng Trưởng bộ môn Người biên soạn PGS.Ts. Lê Văn Điểm Ths.Nguyễn Thị Thu Lê Ths. Nguyễn Anh Xuân 15 BÀI MỞ ĐẦU 1. Mục đích, yêu cầu và vị trí môn học 1.1. Mục đích của môn học - Cung cấp kiến thức cơ bản về các phương pháp gia công kim loại trong cơ khí. - Làm quen với một số thiết bị cơ bản của các phương pháp gia công kim loại. - Biết và có thể lập một số quy trình gia công đơn giản, là cơ sở cho môn học công nghệ chế tạo, công nghệ sửa chữa. 1.2. Yêu cầu của môn học - Nắm được bản chất, đặc điểm và phạm vi áp dụng của từng phương pháp gia công kim loại. - Biết vận dụng vào quá trình sản xuất thực tế: + Chọn được phương pháp gia công. + Chọn được thiết bị gia công. + Thiết lập được trình tự gia công. 1.3. Vị trí môn học Kỹ thuật gia công cơ khí là môn tiếp theo của môn vật liệu học và chỉ ra các phương pháp gia công làm cơ sở cho các môn chuyên ngành. 2. Nội dung môn học Kỹ thuật gia công cơ khí là môn học nghiên cứu khái quát quá trình sản xuất, tính chất và phương pháp gia công kim loại và hợp kim để chế tạo các chi tiết hoặc các ... ph¼ng b»ng dao phay mÆt ®Çu hay dao phay ngãn. ë mét sè m¸y phay ®øng trôc chÝnh m¸y cã thÓ xoay nghiªng 1 gãc tuú ý so víi bµn m¸y. - M¸y phay n»m ngang: lµ lo¹i m¸y phay cã trôc n»m ngang so víi mÆt bµn m¸y. - M¸y phay gi-êng: M¸y phay gi-êng cã lo¹i 1 trôc chÝnh, 2 trôc chÝnh, 3 hoÆc 4 trôc chÝnh. M¸y phay gi-êng kh¸c c¸c lo¹i m¸y phay trªn ë chç bµn m¸y phay chØ thùc hiÖn 1 chuyÓn ®éng däc, cßn chuyÓn ®éng ngang vµ lªn xuèng th× do ®Çu m¸y phay thùc hiÖn. M¸y phay gi-êng th-êng sö dông ®Ó phay c¸c vËt cã träng l-îng vµ kÝch th-íc lín hoÆc ®Ó phay ®ång thêi nhiÒu chi tiÕt cïng mét lÇn trªn bµn m¸y. MÆt kh¸c m¸y phay gi-êng cã nhiÒu ®Çu dao bè trÝ vu«ng gãc nhau, cïng mét lóc nã cã thÓ phay nhiÒu mÆt ph¼ng kh¸c nhau trªn mét chi tiÕt, do ®ã n¨ng suÊt cña m¸y phay gi-êng cao h¬n nhiÒu so víi lo¹i m¸y phay kh¸c. - M¸y phay chÐp h×nh: M¸y phay nµy dïng ®Ó phay c¸c mÆt ®Þnh h×nh phøc t¹p theo mét d-ìng chÐp h×nh, hoÆc mÉu cã s½n. M¸y phay chÐp h×nh dïng kiÓu chÐp h×nh c¬ khÝ, thuû lùc, ®iÖn – thuû lùc, quang häc - M¸y phay chuyªn dïng: Lµ m¸y phay ®-îc thiÕt kÕ vµ chÕ t¹o nh»m phôc vô cho mét môc ®Ých nhÊt ®Þnh. ThÝ dô m¸y phay r·nh then chuyªn dïng chØ ®Ó phay c¸c r·nh then, hoÆc m¸y phay r·nh r« to cña tuabin C¸c m¸y chØ dïng trong s¶n xuÊt hµng lo¹t lín vµ hµng khèi. - Sơ đồ cấu tạo máy phay đứng 2. Trục chính của máy 3. Động cơ trục chính 4. Nòng gá dao 5. Dao cắt 6. Thiết bị kẹp phôi 7. Bàn máy Hình 15.4. Máy phay đứng 1 2 3 4 5 6 7 163 Trục chính cho phép dao dịch chuyển lên xuống để tạo chiều sâu cắt trong qúa trình cắt gọt. Bàn máy (7) và ê tô (6) có thể dịch chuyển trong mặt phẳng của nó. Công dụng: thường gia công các chi tiết có kích thước nhỏ, hình dáng phức tạp và gia công các tổ hợp lỗ. - Sơ đồ của máy phay ngang vạn năng: là máy phay có trục chính theo phương nằm ngang 1. Thân máy 2. Động cơ trục chính 3. Đầu gá dao 4. Tâm trục chính 5. Dao phay 6. Trục gá dao 7. Phôi gia công 8. Ê tô 9. Bàn mày 10. Vít me lên xuống của bàn máy Hình 15.5. Máy phay ngang vạn năng 15.3.2. Dao phay +Dao phay mặt đầu: các lưỡi cắt chính được bố trí trên mặt đầu của dao, có 2 loại là dao phay mặt đầu răng liền và dao phay mặt đầu răng chắp, được dùng cho máy phay đứng và máy phay chuyên dùng + Dao phay mặt trụ: các lưỡi cắt được bố trí theo mặt trụ của dao, có 2 loại dao phay mặt trụ răng thẳng và dao phay mặt trụ răng nghiêng +Dao phay ngón: có thể có từ 2 đến 8 lưỡi cắt + Dao phay rãnh then + Dao phay định hình + Dao phay đĩa + Dao phay góc + Dao phay lăn răng mô đun 15.4. Những công việc tiến hành trên máy phay - Phay mặt phẳng: Gia công được các mặt phẳng ngang, mặt phẳng nghiêng, mặt phẳng đứng,sử dụng dao phay mặt trụ, dao phay ngón, dao phay mặt đầu. - Phay rãnh then và trục then hoa thường dùng dao phay đĩa hoặc dao phay ngón - Phay định hình bằng dao phay định hình 1 3 4 5 6 7 2 8 9 10 164 H t n h - Phay biên dạng bằng dao phay ngón - Gia công lỗ trên máy phay Câu hỏi ôn tập: Câu 1. Bản chất, đặc điểm và công dụng của gia công phay Câu 2. Các phương pháp phay cơ bản 165 ]ph/m[ 1000 n.D. vc 2 dD t CHƯƠNG 16. GIA CÔNG LỖ 16.1. Bản chất, đặc điểm và công dụng 16.1.1. Bản chất Gia công lỗ là phương pháp để gia công lỗ mới hoặc mở rộng lỗ nâng cao chất lượng bề mặt của lỗ đã có sẵn. Chuyển động chính là chuyển động quay của dụng cụ cắt, chuyển động chạy dao là chuyển động dọc trục mang dao, phôi được kẹp chặt và cố định. Chế độ cắt: + Tốc độ cắt: D: Đường kính mũi khoan,dao doa, mũi khoét Sz: Lượng chạy dao của một lưỡi cắt + Chiều sâu cắt: Khi phôi đặc: )( 2 mmt D Khi phôi đã có lỗ sẵn với đường kính d : )( 2 mmt dD + Lượng chạy dao: S = Sz . z = 2 . Sz Sz là lượng chạy dao của một lưỡi cắt của dao Z là số lưỡi cắt cúa dao 16.1.2. Đặc điểm - Các nguyên công trong gia công lỗ rất đa dạng (khoan, khoét, doa, ta rô . . .). - Số lượng lưỡi cắt nhiều (ít nhất là 2 lưỡi cắt) do đó chất lượng bề mặt tốt và năng suất cao. - Độ đồng tâm của lỗ gia công cao do phôi được định vị và kẹp chặt ổn định. - Thường sử dụng các máy gia công chuyên dùng. 16.1.3. Công dụng - Tạo lỗ mới (thông hoặc không thông). - Mở rộng lỗ có sẵn. - Nâng cao chất lượng bề mặt lỗ. - Tạo ren cho lỗ. 16.2. Các phương pháp gia công lỗ 16.2.1. Khoan - Sơ đồ khoan: 166 Hình 16.1. Sơ đồ khoan - Cấu tạo của mũi khoan: I: Cắt chính II: Cắt cạnh và sửa bóng III: Cổ mũi khoan IV: Chuôi mũi khoan Hình 16.2. Cấu tạo của mũi khoan Khả năng công nghệ của khoan: Khoan thường sử dụng gia công các lỗ trên các phôi đặc. Khi khoan có thể gia công các lỗ có đường kính từ 0,1 đến 80 mm, phổ biến là các lỗ có đường kính từ 35mm trở xuống. Khi khoan thường dùng dao là mũi khoan ruột gà Độ chính xác gia công khoan nói chung là thấp chỉ đạt độ chính xác 12 đến 13 và độ bóng bề mặt Ra=3,2÷12,5 m Đối với lỗ có đường kính lớn nên khoan trước lỗ nhỏ rồi khoan thành nhiều lần để giảm chiều sâu cắt khi khoan. Khoan các lỗ lớn và sâu nên dùng phương án chi tiết quay đồng thời sử dụng các loại mũi khoan lòng súng hoặc mũi khoan sâu - Mũi khoan và máy khoan: Có các loại mũi khoan như mũi khoan ruột gà, mũi khoan sâu, mũi khoan nòng súng II IV III I Lưỡi cắt chính Lưỡi cắt phụ Mặt sau Rãnh thoátphoi Lưỡi cắt ngang 2 D t a b S n 167 - Máy khoan có các loại: - Máy khoan bàn: là loại máy khoan nhỏ, công suất thấp, đường kính mũi khoan lớn nhất max = 12 mm. Đặc điểm là độ cứng vững không cao do đó chỉ dùng gia công các lỗ có đường kính và chiều sâu nhỏ, yêu cầu về độ đồng tâm không quá cao. - Máy khoan đứng: là máy khoan có chiều cao lớn hơn nhiều kích thước của bàn máy, trục chính chỉ chuyển động dọc trục của nó. Đặc điểm là có công suất lớn, độ đồng tâm cao vì vậy thường dùng để gia công lỗ có đường kính ≤50mm. - Máy khoan cần: là loại máy khoan mà trục dao ngoài khả năng dịch chuyển dọc trục còn có thể dịch chuyển lên xuống , ra vào và xoay quanh thân máy,có thể khoan lỗ trên bất kỳ tọa độ nào, phù hợp để gia công các chi tiết lớn . Đặc điểm là năng suất cao nhưng độ cứng vững thấp nên chất lượng lỗ không cao. - Máy khoan nhiều trục: là máy có khả năng khoan đồng thời nhiều lỗ nhờ một đầu dao có gá nhiều mũi khoan, phù hợp trong sản xuất hàng loạt - Máy khoan sâu: là loại chuyên dùng có trục chính nằm ngang, dùng để gia công các lỗ có chiều sâu lớn 16.2.2. Khoét - Sơ đồ khoét: Hình 16.3. Sơ đồ khoét - Cấu tạo của mũi khoét: t a b S n 168 Hình 16.4. Cấu tạo của mũi khoét Khả năng công nghệ của khoét: - Khoét chủ yếu để mở rộng và nâng cao độ bóng lỗ sau khi khoan. Khoét đạt độ chính xác cấp 9 đến cấp 12 và độ bóng đạt Ra=1,6 đến 12,5 m - Dao khoét thường có số lượng lưỡi cắt cao hơn so với mũi khoan thường số lưỡi cắt của mũi khoét z = 4 6. 16.2.3. Doa Khả năng công nghệ của doa -Doa là nguyên công gia công tinh các lỗ đã được khoan hoặc khoét - Số lượng lưỡi cắt của mũi doa lớn z = 8 12. -Độ chính xác đạt cấp 7 đến cấp 9, độ bóng có thể đạt được Ra=1,6 6,3 m - Lượng dư gia công nhỏ vì vậy không sửa được sai lệch hình học của lỗ. 16.2.4. Ta rô Khả năng công nghệ của taro - Mục đích là tạo ra các lỗ có ren, vì vậy ta rô là nguyên công thực hiện sau khi khoan. - Chọn mũi khoan khi ta rô: Ví dụ: M10 x 1,5 chọn mũi khoan 8,5 Câu hỏi ôn tập: Câu 1. Khái niệm chung về các phương pháp gia công lỗ, các yếu tố của chế độ cắt khi khoan Câu 2, Khả năng công nghệ của khoan, khoét, doa II IV I I 1 2 3 4 5 I: Cắt chính II: Cắt cạnh và sửa bóng III: Cổ mũi khoan IV: Chuôi mũi khoan 1: Rãnh thoát phoi 2: Lưỡi cắt chính 3: Mặt đầu 4: Mặt lưỡi cắt 5: Lưỡi cắt phụ 169 CHƯƠNG 17. GIA CÔNG TRÊN NHÓM MÁY MÀI 17.1. Bản chất, đặc điểm và công dụng 17.1.1. Bản chất Mài là phương pháp gia công cắt gọt sử dụng dụng cụ cắt đặc biệt là đá mài. đá mài là tổ hợp vô số các hạt mài, mỗi hạt mài được coi là một lưỡi cắt và có các thông số hình học không xác định. Chuyển động chính trong qúa trình mài là chuyển động quay tròn của đá, còn chuyển động chạy dao có thể là chuyển động tịnh tiến hoặc chuyển động quay tròn của phôi. 17.1.2. Đặc điểm - Tốc độ cắt khi mài rất lớn, khoảng (10 80) m/s. - Nhiệt cắt sinh ra rất lớn, trong quá trình mài bao giờ cũng phải có dung dịch trơn nguội. - Số lượng lưỡi cắt trong qúa trình mài rất lớn do đó độ bóng bề mặt của chi tiết gia công đạt rất cao - Lượng dư gia công khi mài thường rất nhỏ do kích thước các lưỡi cắt rất nhỏ. - Năng suất của qúa trình mài cao, đặc biệt khi mài mặt phẳng và mặt trụ. Vì vậy: gia công mài thường là khâu gia công cơ cuối cùng của các chi tiết máy. 17.1.3. Công dụng - Gia công tinh các dạng mặt phẳng, đặc biệt là các đồ gá trong gia công cơ khí. - Gia công lần cuối đối với các chi tiết máy đòi hỏi độ chính xác cao đặc biệt là các bộ đôi lắp ghép. - Dùng để mài và chỉnh sửa các dụng cụ cắt khi đã bị mòn. - Gia công một số bề mặt khác nhau như mặt phẳng, mặt trụ trong, mặt trụ ngoài, các mặt côn, các bề mặt định hình 17.2. Cấu tạo của đá mài 17.2.1. Cấu tạo chung Đá mài được sản xuất từ các hạt mài và chất dính kết trộn đều với nhau sau đó đem tạo hình để tạo thành đá mài. Hạt mài, chất dính kết Trộn đều Tạo hình dưới áp lực cao Áp lực yêu cầu của đá Tỷ lệ % hạt mài và chất dính kết Thiêu kết Đá mài 170 Tổ chức tế vi: có ba pha cơ bản là hạt mài, chất dính kết và pha khí (lỗ hổng trong đá mài). - Hạt mài: trực tiếp tham gia vào qúa trình cắt gọt. Mỗi một hạt mài là một lưỡi cắt đơn lẻ. Khi số lượng hạt mài tăng lên, làm tăng năng suất cắt gọt. Số lượng hạt mài có giới hạn cụ thể với từng loại đá. - Chất dính kết: để liên kết các hạt mài với nhau và tạo ra hình dáng bên ngoài của viên đá, nó quyết định độ cứng của đá mài. Độ cứng của đá mài là khả năng tách các hạt mài ra khỏi liên kết của đá và để xuất hiện một lớp hạt mài mới tham gia vào qúa trình cắt gọt, khả năng tách hạt mài càng tăng thì độ cứng càng giảm và ngược lại. Vì vậy, độ cứng được quyết định bởi chất dính kết. - Pha khí: là các lỗ hổng xuất hiện trong tổ chức của đá mài. Pha khí quyết định độ xốp của đá mài, do đó được dùng để chọn đá khi gia công thô hoặc gia công tinh. 17.2.2. Vật liệu chế tạo đá mài 17.2.2.1. Vật liệu hạt mài: bao gồm các loại ôxít và cácbít có độ cứng cao, độ hạt nhỏ. Để phân loại hạt mài theo cấp hạt người ta sử dụng hệ thống rây tiêu chuẩn: hạt mài (5 3200) m. - Ôxít nhôm Al2O3 : độ cứng và nhiệt độ nóng chảy cao, độ hạt khó đồng đều, sản xuất gặp nhiều khó khăn do đó thường sử dụng cho đá mài loại tốt. - Ôxít crôm Cr2O3 : độ cứng cao và tính trơ cao, độ hạt đồng đều và là vật liệu lý tưởng để sản xuất hạt mài nhưng đắt tiền, khó sản xuất do đó thường sử dụng cho đá mài đặc biệt như mài khôn và mài nghiền. - Các bít si líc SiC : có độ cứng cao, độ hạt đồng đều và dễ sản xuất nhưng dễ bị phân huỷ khi nhiệt độ cao do đó thường sử dụng để sản xuất đá mài thô, độ hạt tương đối lớn 750 m. - Các bít Bo : B4C : có độ cứng thấp nhất trong các vật liệu hạt mài, độ hạt đều và rẻ tiền do đó được sử dụng nhiều thay cho SiC trong sản xuất các loại đá mài thô. 17.2.2.2. Chất dính kết: bao gồm nhóm vật liệu vô cơ, nhóm vật liệu hữu cơ và nhóm vật liệu kim loại. - Nhóm vật liệu vô cơ: chủ yếu dùng cho đá mài có độ cứng cao, như ceramich, nước thuỷ tinh, vuncalit. - Nhóm vật liệu hữu cơ: dùng cho đá có độ mềm cao, như bakêlit, cao su. - Nhóm vật liệu kim loại: dùng cho các đá mài đặc biệt, như coban, niken. 17.3. Phân loại đá mài và phương pháp lựa chọn đá mài khi gia công 17.3.1. Phân loại: đá mài được phân loại theo độ cứng 171 Ký hiệu Độ cứng M (M1, M2) Đá mềm - thường dùng để mài thép sau khi tôi CM (CM1, CM2) Đá mềm vừa - mài chi tiết sau gia công cơ C (C1, C2, C3) Đá trung bình - mài chi tiết sau gia công cơ T (T1, T2, T3, T4) Đá cứng - mài thép sau khi ủ và thường hoá BT (BT1, BT2) Đá rất cứng - mài hợp kim màu ЧT (ЧT1, ЧT2) Đá cực kỳ cứng - mài tinh hoặc siêu chính xác 17.3.2. Phương pháp lựa chọn đá mài khi gia công Nguyên lý chung: - Vật liệu mềm chọn đá cứng để tiết kiệm đá. - Vật liệu cứng chọn đá mềm để các hạt mài mới tham gia vào qúa trình cắt gọt. Yêu cầu về ký hiệu đá mài: - Cho biết được kích thước cơ bản của đá. - Độ cứng của đá. -Vật liệu chất dính kết của đá. - Cỡ và vật liệu hạt mài. - Tốc độ cắt lớn nhất cho phép của đá mài. Ví dụ: - Đường kính ngoài: D = 400 mm - Đường kính trong: d = 40 mm - Chiều dày đá: B = 42 mm - CM1: đá mềm vừa - K: chất dính kết ceramic - A: ôxit nhôm Al2O3 - 12: cỡ hạt mài - 35 m/s: tốc độ cắt lớn nhất cho phép của đá mài. 17.3.3. Một số kiểu đá mài Mục đích: để gia công được nhiều kiểu biên dạng khác nhau. 400x40x42 CM1 K A 12 35 m/s d D 172 Hình 17.1. Các kiểu đá mài a, Đá mài mặt trụ, dùng để gia công mặt phẳng, mặt trụ b & c, Đá mài định hình, dùng gia công mặt trong của các rãnh d, Đá mài hình cốc, dùng gia công mặt trụ trong có kích thước nhỏ e, Đá mài cắt f, Đá mài vành chân g, Đá mài mặt côn, dùng gia công những bề mặt côn định hình h, Đá mài để sửa bề mặt tinh của bánh răng i, Đá mài mặt đầu 17.4. Những công việc cơ bản tiến hành trên máy mài 17.4.1. Mài mặt phẳng Khi mài mặt phẳng có thể sử dụng đá mài mặt trụ hoặc đá mài mặt đầu. Sơ đồ mài mặt phẳng sử dụng đá mài mặt trụ: Hình 17.2. Mài mặt phẳng B D a, c, b, e, f, g, h, d, i, d 173 Đá mài chuyển động quay tròn, bàn máy mang chi tiết chuyển động thẳng theo chiều dọc để cắt hết chiều rộng chi tiết. Đặc điểm: mài mặt phẳng bằng đá mài mặt trụ cho độ chính xác và đọ bóng bề mặt cao vì thoát phoi, thoát nhiệt và tưới dung dịch trơn nguội vào khu vực gia công được dễ dàng. 17.4.2. Mài tròn 17.4.2.1. Mài có tâm: trong qúa trình mài tâm của đá và tâm của chi tiết cố định. Chiều quay của đá và chi tiết ngược nhau, vận tốc góc của đá lớn hơn rất nhiều so với vận tốc góc của chi tiết (khoảng 100 lần). Hình 17.3. Mài tròn có tâm Đặc điểm: - Cho năng suất tương đối cao. - Chất lượng tốt. - Gá lắp khó, độ cứng vững không cao. 17.4.2.2. Mài vô tâm: không cố định tâm của chi tiết, sau khi mài sẽ ổn định kích thước và tâm của chi tiết. Hình 17.4. Mài tròn vô tâm Đặc điểm: - Độ cứng vững cao. - Năng suất không cao. 1: Đá mài 2: Đá dẫn 3: Giá đỡ chi tiết 4: Chi tiết h: Khoảng lệch tâm d16h d: Đường kính chi tiết (cm) Đá mài n1 n2 Chi tiết n1 n2 2 h 3 1 4 174 17.4.2.3. Mài nghiền: là phương pháp sử dụng bột mài trộn với dầu nhờn, mỡ bò để mài, được dùng để mài tinh cho bề mặt truyền lực của bánh răng. 17.4.2.4. Mài khôn: là qúa trình mài tương tự như mài nghiền nhưng dụng cụ mài là các thỏi đa được gọi là đầu khôn. Câu hỏi ôn tập: Câu 1. Bản chất, đặc điểm và công dụng của gia công mài Câu 2. Cấu tạo của đá mài Câu 3. Những công việc cơ bản tiến hành trên máy mài 175
File đính kèm:
bai_giang_ky_thuat_gia_cong_co_khi.pdf