Multi-Responses optimization of dry milling of SKD61 for low cutting power and surface roughness
ABSTRACT
Optimized process parameters play a significant role in improving the
energy efficiency and machined part quality. This paper systematically
investigates the nonlinear relationships between machining parameters and
responses, including cutting power Pc and surface roughness Ra of the dry milling
(DM) using the response surface model (RSM). Three process parameters
considered include the spindle speed S, depth of cut ap, and feed rate fz. A set of
physical experiments was carried out with SKD61 steel on a CNC milling machine
using the wiper insert. The target of the current complex optimization is to find
the low cutting power and surface roughness. Finally, an evolutionary algorithm
entitled non-dominated sorting genetic algorithm II (NSGA-II) was used to
generate a set of feasible optimal solutions and determine the best machining
conditions. The results show that an appropriate trade-off solution can be drawn
with regard to the low cutting power and surface roughness. Furthermore, the
integration of RSM model and NSGA-II can be considered as a powerful approach
for modeling and optimizing dry milling processes.
Tóm tắt nội dung tài liệu: Multi-Responses optimization of dry milling of SKD61 for low cutting power and surface roughness
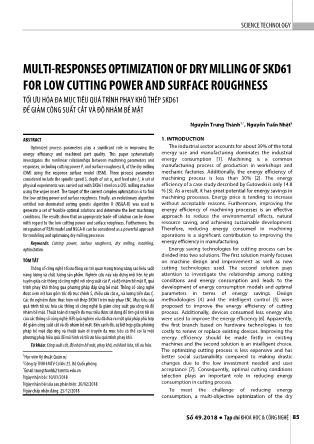
SCIENCE TECHNOLOGY Số 49.2018 ● Tạp chí KHOA HỌC & CÔNG NGHỆ 85 MULTI-RESPONSES OPTIMIZATION OF DRY MILLING OF SKD61 FOR LOW CUTTING POWER AND SURFACE ROUGHNESS TỐI ƯU HÓA ĐA MỤC TIÊU QUÁ TRÌNH PHAY KHÔ THÉP SKD61 ĐỂ GIẢM CÔNG SUẤT CẮT VÀ ĐỘ NHÁM BỀ MẶT Nguyễn Trung Thành1,*, Nguyễn Tuấn Nhật2 ABSTRACT Optimized process parameters play a significant role in improving the energy efficiency and machined part quality. This paper systematically investigates the nonlinear relationships between machining parameters and responses, including cutting power Pc and surface roughness Ra of the dry milling (DM) using the response surface model (RSM). Three process parameters considered include the spindle speed S, depth of cut ap, and feed rate fz. A set of physical experiments was carried out with SKD61 steel on a CNC milling machine using the wiper insert. The target of the current complex optimization is to find the low cutting power and surface roughness. Finally, an evolutionary algorithm entitled non-dominated sorting genetic algorithm II (NSGA-II) was used to generate a set of feasible optimal solutions and determine the best machining conditions. The results show that an appropriate trade-off solution can be drawn with regard to the low cutting power and surface roughness. Furthermore, the integration of RSM model and NSGA-II can be considered as a powerful approach for modeling and optimizing dry milling processes. Keywords: Cutting power, surface roughness, dry milling, modeling, optimization. TÓM TẮT Thông số công nghệ tối ưu đóng vai trò quan trọng trong nâng cao hiệu suất năng lượng và chất lượng sản phẩm. Nghiên cứu này xây dựng mối liên hệ phi tuyến giữa các thông số công nghệ với công suất cắt Pc và độ nhám bề mặt Ra quá trình phay khô thông qua phương pháp đáp ứng bề mặt. Thông số công nghệ được xem xét bao gồm tốc độ trục chính S, chiều sâu cắt ap, và lượng tiến dao fz. Các thí nghiệm được thực hiện với thép SKD61 trên máy phay CNC. Mục tiêu của quá trình tối ưu hóa các thông số công nghệ là giảm công suất gia công và độ nhám bề mặt. Thuật toán di truyền đa mục tiêu được sử dụng để tìm giá trị tối ưu của các thông số công nghệ. Kết quả nghiên cứu đã đưa ra một giải pháp phù hợp để giảm công suất cắt và độ nhám bề mặt. Bên cạnh đó, sự kết hợp giữa phương pháp bề mặt đáp ứng và thuật toán di truyền đa mục tiêu có thể coi là một phương pháp hiệu quả để mô hình và tối ưu hóa quá trình phay khô. Từ khóa: Công suất cắt, độ nhám bề mặt, phay khô, mô hình hóa, tối ưu hóa. 1Học viện Kỹ thuật Quân sự 2Công ty TNHH MTV Cơ khí 25, Bộ Quốc phòng *Email:trungthanhk21@mta.edu.vn Ngày nhận bài: 10/01/2018 Ngày nhận bài sửa sau phản biện: 20/02/2018 Ngày chấp nhận đăng: 25/12/2018 1. INTRODUCTION The industrial sector accounts for about 39% of the total energy use and manufacturing dominates the industrial energy consumption [1]. Machining is a common manufacturing process of production in workshops and mechanic factories. Additionally, the energy efficiency of machining process is less than 30% [2]. The energy efficiency of a case study described by Gutowski is only 14.8 % [3]. As a result, it has great potential for energy savings in machining processes. Energy price is tending to increase without acceptable reasons. Furthermore, improving the energy efficiency of machining processes is an effective approach to reduce the environmental effects, natural resource saving, and achieving sustainable development. Therefore, reducing energy consumed in machining operations is a significant contribution to improving the energy efficiency in manufacturing. Energy saving technologies for cutting process can be divided into two solutions. The first solution mainly focuses on machine design and improvement as well as new cutting technologies used. The second solution pays attention to investigate the relationship among cutting conditions and energy consumption and leads to the development of energy consumption models and optimal parameters in terms of energy savings. Design methodologies [4] and the intelligent control [5] were proposed to improve the energy efficiency of cutting process. Additionally, devices consumed less energy also were used to improve the energy efficiency [6]. Apparently, the first branch based on hardware technologies is too costly to renew or replace existing devices. Improving the energy efficiency should be made firstly in existing machines and the second solution is an intelligent choice. The optimizing cutting process is less expensive and has better social sustainability compared to making drastic changes due to the low investment needed and user acceptance [7]. Consequently, optimal cutting conditions selection plays an important role in reducing energy consumption in cutting process. To meet the challenge of reducing energy consumption, a multi-objective optimization of the dry CÔNG NGHỆ Tạp chí KHOA HỌC & CÔNG NGHỆ ● Số 49.2018 86 KHOA HỌC milling has considered in this paper. The material, namely SKD61 was chosen as the workpiece due to wide applications in molding, automotive, aerospace, and marine industrial. Moreover, the practical analysis indicated that machining parameters has complicated effects on the machining responses, such as cutting energy and surface roughness. Therefore, an effective approach for modeling dry cutting and optimizing process parameters is still urgent demand. This paper is expected as a significant contribution to exhibit the impacts of machining factors on the cutting power and surface roughness as well as help the DM operators select the appropriate conditions. 2. MATERIALS AND METHODS The systematic research procedure for experimental conductions and parameter optimization is depicted in Fig. 1. The Box-Behnken method was applied instead of the full- factorial in order to decrease the number of experiments and guarantee the predicting accuracy [8, 9]. Three machining parameters, including the spindle speed S, depth of cut ap, and feed rate fz with their levels were exhibited in Table 1. The parameter ranges were identified through machine tool characteristics as well as recommendations of cutting tool manufacturers and verified then using cutting trials. The output models considered of PC and Ra were developed with the aid of experimental data and RSM [10, 11]. A non-dominated sorting genetic algorithm II (NSGA-II) was used to solve the complicated problem with two objectives. In the NSGA-II, each objective parameter is treated separately. Standard genetic operation of mutation and crossover are performed on the designs. The selection process is based on two main mechanisms, including non-dominated and crowding distance sorting. By the end of the optimization run a Pareto set is constructed where each design has the best combination of objective values and improving one objective is impossible without sacrificing one or more of the other objectives. Table 1. Machining parameters and their values Symbol Parameters level-1 level 0 level +1 S Spindle speed (revolution/min) 2000 3000 4000 ap Depth of cut (mm) 0.2 0.6 1.0 fZ Feed per tooth (mm/tooth) 0.04 0.10 0.16 Fig. 1. Optimizing procedure for cutting power and surface roughness (a) Tool holder specifications (b) Wiper insert dimensions (c) CNC machine and workpiece (d) Control unit and PC (e) Surface roughness measurement Fig. 2. Experimental facilities SCIENCE TECHNOLOGY Số 49.2018 ● Tạp chí KHOA HỌC & CÔNG NGHỆ 87 The dimensions of the rectangular SKD61 plate used were 350 mm×150 mm×25 mm in the experiments. The tool holder namely EPO07R012M12.0-02 mounting two wiper inserts AOMT 070204PDPR-MJ of Tungaloy Corporation was used to perform machining runs. The total length, effective length, and effective diameter of the tool holder are 68 mm, 18 mm, and 12 mm, respectively. The detail data of the tool holder and cutting insert can be found in Figs. 2a and 2b, respectively. A new insert was adopted for each machining experiment to eliminate any possible interference during the cutting process. Table 2. Experimental results No. S (rpm) ap (mm) fz (mm/tooth) Pc (kW) Ra (µm) 1 4000 1.0 0.10 1.0695 0.94 2 3000 0.6 0.10 0.7243 0.71 3 3000 0.6 0.10 0.7319 0.73 4 3000 0.6 0.10 0.7206 0.73 5 3000 0.2 0.16 0.6196 1.13 6 4000 0.6 0.04 0.5811 0.51 7 3000 1.0 0.04 0.5848 0.93 8 3000 0.6 0.10 0.7300 0.73 9 3000 0.6 0.10 0.7187 0.73 10 3000 1.0 0.16 0.9801 1.51 11 2000 0.2 0.10 0.4752 0.73 12 2000 1.0 0.10 0.6897 1.13 13 2000 0.6 0.04 0.4554 0.7 14 4000 0.2 0.10 0.6116 0.52 15 2000 0.6 0.16 0.6724 1.29 16 3000 0.2 0.04 0.4055 0.53 17 4000 0.6 0.16 0.9947 0.99 The experiments were performed dry condition along the direction of the width of the specimen. The machining tests were performed on a SPINNER milling machine having spindle speed of 20.000 RPM and spindle power of 22 kW (Fig. 2c). The cutting forces were measured using the quartz three-component dynamometer KISTLER 9257B with control unit 5233A. These amplified signals are the acquired by the personal computer through the acquisition card. DynoWare software was used to process these signals and expresses the three force components (Fig. 2d). The cutting power was calculated using the following equation: 2 2 2 x y z cc c c F F F VF VP 60000 60000 (1) where Pc is the cutting power (kW). Vc is the cutting speed (m/min). Fx, Fy, and Fz are the cutting forces in x, y, and z direction (N), respectively. The surface roughness values were measured by a tester Mitutoyo SJ-301. The average response values were observed from repeated three times at different positions (Fig. 2e). 3. EXPERIMENTAL RESULTS In this paper, the significance of the models proposed and factors considered are evaluated using an analysis of variance (ANOVA). The confidence level of 95% was used and the factors with p-values less than 0.05 are considered as significant. The experimental results of the dry milling are given in Table 2. ANOVA results of the objective functions are presented in Table 3 and 4 respectively. As shown in Table 3, the R2 value of 0.9945 revealed that cutting power model was highly adequate to represent the experimental data. Additionally, the F-value of 141.79 indicated that the second quadratic model is significant. As a result, the S, ap, fz, Sap, Sfz, apfz and fz^2 are significant terms. The percentage contribution of 35.57% revealed that fz is the most effective factor with regard to the single term. The percentages of S and ap are 21.52% and 33.99%, respectively. The insignificant terms (S^2, ap^2) were eliminated in the design space in order to save the computational costs and time. The ANOVA results of the surface roughness model are presented in Table 4. The R2 value of 0.9980 indicated that proposed model was significantly adequate to represent the experimental data. The surface roughness model is significant due to the p-value of less than 0.0001. For this model, the single terms (S, ap, fz), quadratic terms (S2, ap^2, fz^2), and the interaction term (Sfz) were considered as the significant terms. The interaction terms (Sap, apfz) were found to be insignificant model terms. Especially, fz is the most effective parameter due to the highest contribution (50.17%). The percentages of S and ap are 25.28% and 8.28%, respectively. Additional, the percentages of fz^2, ap^2, and S2 were 10.08%, 5.74%, and 0.20%, respectively. Table 3. ANOVA results for cutting power Source Sum of Squares Mean Square F-value p-value Remark Contri. (%) Model 0.540732 0.060081 141.7965 < 0.0001 Significant S 0.116215 0.116215 274.2754 < 0.0001 Significant 21.51 ap 0.18368 0.18368 433.4976 < 0.0001 Significant 33.99 fz 0.192207 0.192207 453.6237 < 0.0001 Significant 35.57 Sap 0.014812 0.014812 34.95849 0.0006 Significant 2.74 Sfz 0.009658 0.009658 22.79388 0.0020 Significant 1.79 apfz 0.008215 0.008215 19.38913 0.0031 Significant 1.52 S^2 0.000231 0.000231 0.544303 0.4846 Insignificant 0.04 ap^2 0.001851 0.001851 4.368016 0.0750 Insignificant 0.34 fz^2 0.013483 0.013483 31.822 0.0008 Significant 2.50 R2 = 0.9945 Table 4. ANOVA results for surface roughness Source Sum of Squares Mean Square F-value p-value Remark Contri. (%) Model 1.258329 0.139814 392.2645 < 0.0001 Significant S 0.103513 0.103513 290.4158 < 0.0001 Significant 8.28 CÔNG NGHỆ Tạp chí KHOA HỌC & CÔNG NGHỆ ● Số 49.2018 88 KHOA HỌC ap 0.316013 0.316013 886.6082 < 0.0001 Significant 25.28 fz 0.6272 0.6272 1759.679 < 0.0001 Significant 50.17 Sap 0 0 0 1.0000 Insignificant 0.00 Sfz 0.003025 0.003025 8.486974 0.0226 Significant 0.24 apfz 2.5E-05 2.5E-05 0.07014 0.7988 Insignificant 0.00 S^2 0.002527 0.002527 7.090813 0.0323 Significant 0.20 ap^2 0.071706 0.071706 201.18 < 0.0001 Significant 5.74 fz^2 0.126017 0.126017 353.5543 < 0.0001 Significant 10.08 R2 = 0.9980 The response models (cutting power, surface roughness) were developed in terms of input parameters using response surface methodology. From the experimental data, the coefficients of the regression equations are calculated. The regression coefficients of insignificant terms were eliminated based on ANOVA results. Consequently, the regression response surface models showing the cutting power (Pc) and surface roughness (Ra) are expressed as follows: Pc = 0.37294-0.000097S-0.10917ap+2.13734fz +0.000152Sap+0.000819Sfz+1.88832apfz -0.13104ap 2 -15.71919fz 2 (2) Ra= 0.71039+0.000079S-0.47146ap-3.50694fz -0.000000025S 2 +0.81563ap 2 +48.05556fz 2 (3) (a) For cutting power (b) For surface roughness Fig. 3. Pareto chart To confirm the analyzed results, the Pareto charts of all terms were generated based on the F-values. The aim of the Pareto charts is to rank in descending order the effects of the machining parameters and their interactions on the technological outputs. The Pareto charts of Pc and Ra were shown in Fig. 3a and 3b, respectively. It can be stated that the Pareto charts are similar to the ANOVA results. The effects of process parameters on the responses were investigated using the contour plots. Figs. 4a and 4b showed that an increase of the spindle speed, depth of cut, and feed rate results in a higher cutting power. This phenomenon can be explained as follows. Increasing ap or fz increased the material removal volume in the same unit of time, thus resulting in a higher cutting force or power consumed. An improved spindle speed causes an increased cutting speed and a higher cutting power is observed. Fig. 4c and 4d exhibited that the surface roughness was also decreased with an increment of S. A reduction of cutting force can be observed at the higher spindle speed, resulting in a smoother surface. An increased cutting force or cutting power caused by a higher depth cut or feed rate results in a coarser surface roughness. (a) Pc versus S and ap (b) Pc versus fz and ap SCIENCE TECHNOLOGY Số 49.2018 ● Tạp chí KHOA HỌC & CÔNG NGHỆ 89 (c) Ra versus S and ap (d) Ra versus fz and ap Fig. 4. Interaction plots for machining responses 4. OPTIMIZATION RESULTS As a result, the inputs, including S, ap, and fz have complicated effects on the technological parameters, including cutting power and surface roughness. The optimizing issue can be described as follows: Find X = [S, ap, fz] Minimize cutting power Pc and surface roughness Ra Constraints: 2000 ≤ S ≤ 4000 (revolution/min), 0.2 ≤ ap ≤ 1.0 (mm), 0.04 ≤ fz ≤ 0.16 (mm/tooth). After building the statistical regression equations showing the relationship between process parameters and machining responses, these equations are used to find optimal parameters. The optimal parameters of the multi- objective optimization are selected from the Pareto front. The Pareto front generated by the NSGA-II algorithm was exhibited in Fig. 5, in which the blue points are feasible solutions. The optimal solution is determined as a blue point with the red crossed line. The optimal values of design variables and objective functions were presented in Table 5. Table 5. Optimal values of process parameters and responses Parameters S (rpm) ap (revolution/min) fz (mm/tooth) Pc (kW) Ra (µm) Optimal values 3996 0.2 0.04 0.4057 0.43 Initial values 3000 0.6 0.10 0.7243 0.71 - 44% - 39.44% Fig. 5. Pareto front for selecting optimal values As compared to initial values in the Table 5, the cutting power Pc is decreased approximately 44% and surface roughness Ra is reduced around 39.44%. 5. CONCLUSIONS This work addressed the process parameters optimization of the dry milling for low cutting power as well as surface roughness. A hybrid approach combining machining experiments, RSM model, and NSGA-II was proposed in order to develop predictive models and determine the optimal values. An ANOVA analysis was performed to evaluate the model adequacy and factor significance. The main conclusions from the research results of this work can be drawn as follows within parameter ranges: 1. The low process parameters were commented to decrease the cutting power, in which depth of cut and feed rate have the higher contribution, compared to the spindle speed. 2. The surface roughness values decrease with increased spindle speed and increase with higher depth of cut and feed rate. 3. The optimizing issue, in which the cutting power and surface roughness is practical and realistic in the dry milling processes, compared to single objective optimization (i.e. Minimizing surface roughness). CÔNG NGHỆ Tạp chí KHOA HỌC & CÔNG NGHỆ ● Số 49.2018 90 KHOA HỌC This work is expected as a significant contribution to improve the dry milling efficiency (i.e. Low energy consumed and surface roughness). The holistic optimization considering more objectives, such as material removal rate and tool wear will be addressed in the future work. ACKNOWLEDGMENT This research is funded by Vietnam National Foundation for Science and Technology Development (NAFOSTED) under grant number 107.04-2017.06 REFERENCES [1]. Viet Nam Ennergy Sector, Assessment, Strategy, and road map, https://www.adb.org/documents/viet-nam-energy-sector-assessment- strategy-and-road-map, 2015. [2]. S.H. Hu, 2012. Energy consumption characteristics of multiple-component of modern cnc machine tools. Chongqing University. [3]. Gutowski T.G., Branham M.S., Dahmus J.B., Jones A.J., Thiriez A., Sekulic D.P., 2009. Thermodynamic analysis of resources used in manufacturing processes. Environmental Science and Technology, 43 (5), pp. 1584-1590. [4]. ISO/TC 39/SC, Machine tools-environmental evaluation of machine tools-part 1: design methodology for energy-efficient machine tools, Draft International Standard ISO/DIS 14955-1, 2012. [5]. [6]. Zhongde, S., Shaoyan, Q., Qian, L., Feng, L., 2012. Key manufacturing technology & equipment for energy saving and emissions reduction in mechanical equipment industry. International Journal of Precision Engineering and Manufacturing 13(7), pp. 1095-1100. [7]. Pusavec, F., Krajnik, P., Kopac, J., 2010. Transitioning to sustainable production-part I: application on machining technologies. Journal of Cleaner Production 18 (2), pp. 174-184. [8]. C.F. Jeff, R. C. Z., Y. Lan, 2009. Experiment Design & Analyses and Parameters Optimization. Wiley. [9]. H. S. Park, T. T. Nguyen, X. P. Dang, 2016. Multi-objective optimization of turning process of hardened material for energy efficiency. International Journal of Precision Engineering and Manufacturing 17 (12), pp. 1623-1631. [10]. H. S. Park; T. T. Nguyen, 2017. Development of a new staking process for an automotive part. The International Journal of Advanced Manufacturing Technology 89 (1-4), pp. 1053-1068. [11]. H. S. Park, T. T. Nguyen, 2014. Optimization of injection molding process for car fender in consideration of energy efficiency and product quality. Journal of Computational Design and Engineering Vol. 1, No. 4, 256-265.
File đính kèm:
multi_responses_optimization_of_dry_milling_of_skd61_for_low.pdf