Sơn cầu thép và kết cấu thép quy trình thi công và nghiệm thu bộ giao thông vận tải
I. QUY ĐỊNH CHUNG
1.1. Tiêu chuẩn này áp dụng cho việc thi công các loại sơn bảo vệ dầm cầu thép, kết cấu xây dựng bằng thép trong điều kiện khí hậu nhiệt đới ngoài trời đối với các loại sơn sử dụng theo yêu cầu kỹ thuật bảo vệ các công trình giao thông.
1.2. Tất cả các loại sơn dùng bảo vệ cầu thép và kết cấu thép phải được lựa chọn thích hợp, đảm bảo chống ăn mòn đối với mức độ xâm thực của môi trường tương ứng.
1.3. Tiêu chuẩn này không áp dụng cho thi công sơn tàu biển và phun phủ bảo vệ bằng kim loại; các công nghệ thi công đặc biệt này phải phù hợp với hướng dẫn riêng của nhà sản xuất sơn.
1.4. Tổng chiều dày các lớp sơn sau khi kết thúc công tác sơn phải đạt ít nhất 180200m. Phải sơn ít nhất 4 lớp và chiều dày mỗi lớp không quá 50m.
II. CHUẨN BỊ BỀ MẶT TRƯỚC KHI SƠN
Làm sạch bề mặt:
2.1. Chuẩn bị bề mặt trước khi sơn là nhân tố quan trọng nhất trong quá trình thi công sơn.
Quá trình chuẩn bị bề mặt là tẩy sạch mọi hợp chất bẩn như muối hòa tan, gỉ, dầu mỡ, nước, bụi bản, vảy cán thép, lớp sơn cũ bám lỏng lẻo, sinh vật bám bẩn ra khỏi bề mặt thép để cho các lớp sơn bám chặt vào thép; tạo độ nhám cho bề mặt thép làm tăng khả năng bám dính của màng sơn sắp thi công.
2.2. Độ gỉ của bề mặt thép được phân thành 4 cấp như sau:
+ Cấp 1: Bề mặt thép đã chớm gỉ nhưng rất ít, tạo nên màu vàng nhạt trên mặt thép.
+ Cấp 2: Bề mặt thép đã bắt đầu bị gỉ đốm và xuất hiện gỉ mỏng, tạo nên màu vàng sẫm có vết đốm trên bề mặt thép.
+ Cấp 3: Bề mặt thép đã có vảy gỉ, có thể cạo bong được, tạo nên vài vết lõm nhỏ có thể nhìn được bằng mắt thường.
+ Cấp 4: Bề mặt thép đã có nhiều vảy gỉ, xuất hiện nhiều vết lõm nhỏ nhìn dễ dàng bằng mắt thường.
2.3. Bề mặt thép trước khi sơn được quy định theo 4 mức độ làm sạch (MS) như sau:
+ MS1: Bề mặt thép sau khi làm sạch vẫn còn gỉ bám chắc trên bề mặt, mới chỉ làm sạch các vảy cán thép, gỉ, sơn cũ, các vật lạ bám lỏng lẻo trên bề mặt thép. Sử dụng phương pháp làm sạch bằng thổi khí khô, thổi bằng ngọn lửa, hoặc dùng giấy mài và giẻ lau. Áp dụng cho bề mặt thép gỉ cấp 1, hoặc làm sạch cục bộ với diện tích nhỏ.
+ MS2: Bề mặt thép sau khi làm sạch có màu xám nhưng chưa đồng nhất, không còn các vảy cán thép gỉ, các vật lạ bám chặt. Sử dụng các phương pháp làm sạch bằng thủ công và cơ khí như gõ gỉ, bàn chải sắt hay máy mài, làm sạch bằng phun cát (hay các vật liệu mài mòn khô) cũng như làm sạch bằng phun chất mài mòn ướt hay bằng ngọn lửa. Áp dụng cho bề mặt thép gỉ cấp 1 và 2.
+ MS3: Bề mặt thép sau khi làm sạch có màu ánh sáng kim nhưng chưa đồng nhất, không còn vảy cán thép, gỉ, cũng như các tiểu phân lạ. Sử dụng phương pháp làm sạch bằng máy mài. Làm sạch bằng phun cát (hay các vật liệu mài mòn khô), làm sạch bằng phun chất mài mòn ướt hoặc ngâm axit. Áp dụng với các bề mặt gỉ cấp 1, 2 và 3; Với bề mặt gỉ cấp 4 theo yêu cầu của Chủ công trình.
+ MS4: Làm sạch khỏi bề mặt toàn bộ gỉ nghiền, gỉ cũng như các tiểu phân lạ. Khi đó bề mặt kim loại có màu ánh sáng kim đồng nhất.
Sử dụng phương pháp làm sạch bằng phun cát (hay các vật liệu mài mòn khô). Phun chất mài mòn ướt hoặc ngâm axít. Áp dụng cho các bề mặt gỉ cấp 1, 2, 3 và gỉ cấp 4 theo yêu cầu của Chủ công trình.
2.4. Đối với công trình cầu dầm thép mới xây dựng, bề mặt thép phải được làm sạch đạt mức độ MS3, MS4.
2.5. Đối với các công trình cầu thép cũ, đã đến giai đoạn sửa chữa thường xuyên và sửa chữa lớn, cần khảo sát mức độ gỉ của thép để làm sạch đạt mức độ sạch MS1 đến MS4 theo yêu cầu của Chủ công trình.
- Nếu lớp sơn phủ đã lão hóa, mà lớp sơn chống gỉ còn tốt, trên bề mặt thép không có các đốm gỉ xuất hiện, chỉ cần làm sạch lớp phấn hóa của sơn phủ rồi sơn tiếp một lớp sơn chống gỉ cách ly và lớp sơn phủ mới.
- Nếu trên dầm thép sơn còn tốt nhưng một số vùng đã xuất hiện gỉ cục bộ (với mức độ gỉ cấp 1, cấp 2 và diện tích gỉ < 30%)="" cho="" phép="" làm="" sạch="" đạt="" mức="" độ="" ms1,="" ms2="" trước="" khi="" sơn="" lại="" những="" khu="" vực="">
- Nếu dầm thép gỉ trên 50% diện tích, với cấp độ gỉ nào cũng phải làm sạch bề mặt thép đạt mức độ MS2 đến MS4 và sơn lại toàn bộ.
2.6. Việc đầu tiên của quá trình chuẩn bị bề mặt là phải tiến hành tẩy sạch dầu mỡ nhờn khỏi bề mặt thép.
Tẩy bằng dung môi (xăng dầu, dầu hỏa) hay dầu pha sơn chỉ nên sử dụng với những diện tích bị nhiễm bẩn nhỏ.
Đối với diện tích bị nhiễm bẩn lớn, phải dùng phương pháp vật lý để phá vỡ trạng thái nhiễm bẩn sau đó dùng chất làm sạch bằng nhũ là tốt nhất và cuối cùng phun rửa bằng nước sạch. (Xem Phụ lục 2.1).
2.7. Nếu bề mặt bị nhiễm muối hòa tan do môi trường ô nhiễm hay được hình thành từ thép bị gỉ phải tiến hành rửa bề mặt thép bằng nước áp suất cao (áp suất nước 8 atm), sau đó dùng khí khô để thổi khô bề mặt thép trước khi tiến hành các phương pháp làm sạch bề mặt khác.
Tóm tắt nội dung tài liệu: Sơn cầu thép và kết cấu thép quy trình thi công và nghiệm thu bộ giao thông vận tải
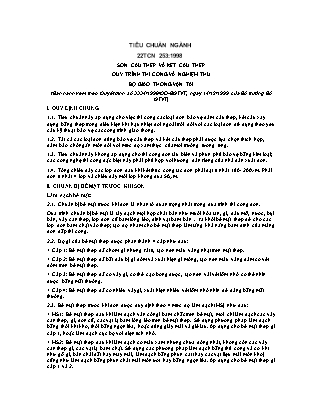
TIÊU CHUẨN NGÀNH 22TCN 253:1998 SƠN CẦU THÉP VÀ KẾT CẤU THÉP QUY TRÌNH THI CÔNG VÀ NGHIỆM THU BỘ GIAO THÔNG VẬN TẢI (Ban hành kèm theo Quyết định số 3334/1998/QĐ-BGTVT, ngày 14/12/1999 của Bộ trưởng Bộ GTVT) I. QUY ĐỊNH CHUNG 1.1. Tiêu chuẩn này áp dụng cho việc thi công các loại sơn bảo vệ dầm cầu thép, kết cấu xây dựng bằng thép trong điều kiện khí hậu nhiệt đới ngoài trời đối với các loại sơn sử dụng theo yêu cầu kỹ thuật bảo vệ các công trình giao thông. 1.2. Tất cả các loại sơn dùng bảo vệ cầu thép và kết cấu thép phải được lựa chọn thích hợp, đảm bảo chống ăn mòn đối với mức độ xâm thực của môi trường tương ứng. 1.3. Tiêu chuẩn này không áp dụng cho thi công sơn tàu biển và phun phủ bảo vệ bằng kim loại; các công nghệ thi công đặc biệt này phải phù hợp với hướng dẫn riêng của nhà sản xuất sơn. 1.4. Tổng chiều dày các lớp sơn sau khi kết thúc công tác sơn phải đạt ít nhất 180¸200mm. Phải sơn ít nhất 4 lớp và chiều dày mỗi lớp không quá 50mm. II. CHUẨN BỊ BỀ MẶT TRƯỚC KHI SƠN Làm sạch bề mặt: 2.1. Chuẩn bị bề mặt trước khi sơn là nhân tố quan trọng nhất trong quá trình thi công sơn. Quá trình chuẩn bị bề mặt là tẩy sạch mọi hợp chất bẩn như muối hòa tan, gỉ, dầu mỡ, nước, bụi bản, vảy cán thép, lớp sơn cũ bám lỏng lẻo, sinh vật bám bẩn ra khỏi bề mặt thép để cho các lớp sơn bám chặt vào thép; tạo độ nhám cho bề mặt thép làm tăng khả năng bám dính của màng sơn sắp thi công. 2.2. Độ gỉ của bề mặt thép được phân thành 4 cấp như sau: + Cấp 1: Bề mặt thép đã chớm gỉ nhưng rất ít, tạo nên màu vàng nhạt trên mặt thép. + Cấp 2: Bề mặt thép đã bắt đầu bị gỉ đốm và xuất hiện gỉ mỏng, tạo nên màu vàng sẫm có vết đốm trên bề mặt thép. + Cấp 3: Bề mặt thép đã có vảy gỉ, có thể cạo bong được, tạo nên vài vết lõm nhỏ có thể nhìn được bằng mắt thường. + Cấp 4: Bề mặt thép đã có nhiều vảy gỉ, xuất hiện nhiều vết lõm nhỏ nhìn dễ dàng bằng mắt thường. 2.3. Bề mặt thép trước khi sơn được quy định theo 4 mức độ làm sạch (MS) như sau: + MS1: Bề mặt thép sau khi làm sạch vẫn còn gỉ bám chắc trên bề mặt, mới chỉ làm sạch các vảy cán thép, gỉ, sơn cũ, các vật lạ bám lỏng lẻo trên bề mặt thép. Sử dụng phương pháp làm sạch bằng thổi khí khô, thổi bằng ngọn lửa, hoặc dùng giấy mài và giẻ lau. Áp dụng cho bề mặt thép gỉ cấp 1, hoặc làm sạch cục bộ với diện tích nhỏ. + MS2: Bề mặt thép sau khi làm sạch có màu xám nhưng chưa đồng nhất, không còn các vảy cán thép gỉ, các vật lạ bám chặt. Sử dụng các phương pháp làm sạch bằng thủ công và cơ khí như gõ gỉ, bàn chải sắt hay máy mài, làm sạch bằng phun cát (hay các vật liệu mài mòn khô) cũng như làm sạch bằng phun chất mài mòn ướt hay bằng ngọn lửa. Áp dụng cho bề mặt thép gỉ cấp 1 và 2. + MS3: Bề mặt thép sau khi làm sạch có màu ánh sáng kim nhưng chưa đồng nhất, không còn vảy cán thép, gỉ, cũng như các tiểu phân lạ. Sử dụng phương pháp làm sạch bằng máy mài. Làm sạch bằng phun cát (hay các vật liệu mài mòn khô), làm sạch bằng phun chất mài mòn ướt hoặc ngâm axit. Áp dụng với các bề mặt gỉ cấp 1, 2 và 3; Với bề mặt gỉ cấp 4 theo yêu cầu của Chủ công trình. + MS4: Làm sạch khỏi bề mặt toàn bộ gỉ nghiền, gỉ cũng như các tiểu phân lạ. Khi đó bề mặt kim loại có màu ánh sáng kim đồng nhất. Sử dụng phương pháp làm sạch bằng phun cát (hay các vật liệu mài mòn khô). Phun chất mài mòn ướt hoặc ngâm axít. Áp dụng cho các bề mặt gỉ cấp 1, 2, 3 và gỉ cấp 4 theo yêu cầu của Chủ công trình. 2.4. Đối với công trình cầu dầm thép mới xây dựng, bề mặt thép phải được làm sạch đạt mức độ MS3, MS4. 2.5. Đối với các công trình cầu thép cũ, đã đến giai đoạn sửa chữa thường xuyên và sửa chữa lớn, cần khảo sát mức độ gỉ của thép để làm sạch đạt mức độ sạch MS1 đến MS4 theo yêu cầu của Chủ công trình. - Nếu lớp sơn phủ đã lão hóa, mà lớp sơn chống gỉ còn tốt, trên bề mặt thép không có các đốm gỉ xuất hiện, chỉ cần làm sạch lớp phấn hóa của sơn phủ rồi sơn tiếp một lớp sơn chống gỉ cách ly và lớp sơn phủ mới. - Nếu trên dầm thép sơn còn tốt nhưng một số vùng đã xuất hiện gỉ cục bộ (với mức độ gỉ cấp 1, cấp 2 và diện tích gỉ < 30%) cho phép làm sạch đạt mức độ MS1, MS2 trước khi sơn lại những khu vực đó. - Nếu dầm thép gỉ trên 50% diện tích, với cấp độ gỉ nào cũng phải làm sạch bề mặt thép đạt mức độ MS2 đến MS4 và sơn lại toàn bộ. 2.6. Việc đầu tiên của quá trình chuẩn bị bề mặt là phải tiến hành tẩy sạch dầu mỡ nhờn khỏi bề mặt thép. Tẩy bằng dung môi (xăng dầu, dầu hỏa) hay dầu pha sơn chỉ nên sử dụng với những diện tích bị nhiễm bẩn nhỏ. Đối với diện tích bị nhiễm bẩn lớn, phải dùng phương pháp vật lý để phá vỡ trạng thái nhiễm bẩn sau đó dùng chất làm sạch bằng nhũ là tốt nhất và cuối cùng phun rửa bằng nước sạch. (Xem Phụ lục 2.1). 2.7. Nếu bề mặt bị nhiễm muối hòa tan do môi trường ô nhiễm hay được hình thành từ thép bị gỉ phải tiến hành rửa bề mặt thép bằng nước áp suất cao (áp suất nước ³ 8 atm), sau đó dùng khí khô để thổi khô bề mặt thép trước khi tiến hành các phương pháp làm sạch bề mặt khác. Các phương pháp làm sạch bề mặt: 2.8. Làm sạch bằng phương pháp thủ công bao gồm sử dụng bàn chải thép, máy mài hoặc các loại bàn chải khác. Phương pháp này được sử dụng để làm sạch những lớp gỉ nhỏ bám dính lỏng lẻo trên bề mặt thép với diện tích nhỏ hoặc những lớp sơn đã bị giảm chất lượng, những vị trí khó thi công bằng phương pháp phun. Trước khi làm sạch bằng phương pháp thủ công, các lớp gỉ nặng phải được làm sạch bằng cách gõ, nạo từng lớp một, các lớp dầu mỡ bụi bẩn nhìn thấy được bằng mắt thường cũng phải được làm sạch. 2.9. Làm sạch bằng chất mài mòn khô là phương pháp phổ biến nhất và hiệu quả nhất đối với việc làm sạch bề mặt thép. Phương pháp được thực hiện bằng cách phun chất mài mòn với áp lực cao lên bề mặt thép. Thường dùng cát làm chất mài mòn khô. Có thể thay thế cát bằng kim loại hoặc những chất silic như bi thép, đá mạt, xỉ kim loại, hạt mài kim loại. Công nghệ làm sạch bằng phun cát (xem Phụ lục 2.2). 2.10. Để khắc phục nhược điểm của phương pháp làm sạch bề mặt thép bằng phun nước ở áp suất cao người ta đưa thêm chất mài mòn (như cát) vào nước. Đó là phương pháp làm sạch bằng chất mài mòn ướt rất phù hợp với bề mặt thép bị nhiễm bẩn do các muối hòa tan. Hiệu quả hơn nếu phương pháp này được thực hiện bằng cách phun nước áp suất thấp sau đó phun khí nén áp suất cao có chứa cát lên bề mặt thép. Khi kết thúc quá trình làm sạch, trên bề mặt thép hình thành một lớp gỉ màng dạng bột (chủ yếu là ở dạng oxyt sắt). Để khắc phục, phải cho chất ức chế vào nước để ngăn cản sự hình thành lớp gỉ và sử dụng loại sơn lót phù hợp với chất ức chế sử dụng, hoặc trước khi sơn phải làm sạch gỉ tức thời bằng cách thổi khí nhẹ vào khô. 2.11. Chuẩn bị bề mặt bằng phương pháp sử dụng ngọn lửa oxy – axetylen hoặc oxy – propan ngang qua bề mặt thép. Hơi nóng đột ngột làm các gỉ nghiền và gỉ vảy bong ra khỏi bề mặt do sự dãn nở không đồng đều giữa lớp vảy gỉ và kim loại. Khi đó dùng bàn chải thép chải sạch gỉ và cuối cùng thổi khí khô làm sạch bề mặt thép lần cuối. Phương pháp này cho phép sử dụng ở bất kỳ giai đoạn nào, mọi nơi mọi chỗ. Có thể sử dụng với bề mặt có độ ẩm tương đối cao và trợ giúp cho bề mặt được khô hơn nhằm tăng tốc độ khô của lớp sơn lót. Chú ý: - Ngọn lửa không được đưa ngang qua bề mặt quá chậm vì những lớp gỉ không liên kết hoặc các vật lạ bên ngoài bay vào, cũng như những chỗ thép mỏng đã bị hỏng sẽ có nguy cơ gây hỏa hoạn. - Không sử dụng cho những bề mặt thép gần với chỗ nối bằng bulông cường độ cao. 2.12. Làm sạch bằng axit là phương pháp chuẩn bị bề mặt bằng cách ngâm nhúng thép trong bồn đựng axit sau đó cọ rửa bằng nước sạch. Phương pháp này được áp dụng cho quá trình làm sạch các loại axit, dầu, mỡ, sáp và các loại nhiễm bẩn khác trên bề mặt kim loại. Áp dụng trực tiếp trong công xưởng, trong những trường hợp không thể áp dụng được các phương pháp khác. Ghi chú: Phương pháp này phải được thực hiện dưới sự hướng dẫn của các cơ quan chuyên môn. 2.13. Đối với các mối liên kết hàn: Trước khi hàn phải làm sạch bề mặt thép. Sau khi hàn phải tiến hành làm sạch xỉ hàn và các chất lắng khác. Làm nhẵn bề mặt các mối hàn, kiểm tra chất lượng rồi mới tiến hành thiết kế sơn. 2.14. Để đánh giá nghiệm thu bề mặt thép được làm sạch, phải tuân theo quy định sau: + Kiểm tra độ sạch: - Kiểm tra độ sạch bụi, sơn, gỉ Trên bề mặt thép bằng cách dùng kính lúp có độ phóng đại 6 lần soi trên bề mặt bản thép để quan sát. Nếu không thấy bụi bẩn là đạt yêu cầu. - Kiểm tra độ sạch mỡ, dầu bằng cách nhỏ 2 – 3 giọt xăng lên bề mặt thép đã được làm sạch. Sau thời gian ít nhất 15 giây, dùng giấy lọc thấm xăng còn đọng lại trên mặt bản thép. Nhỏ xăng sạch lên mặt giấy lọc cùng loại để kiểm tra. Sau khi hai tờ giấy lọc đã bay hết xăng, nếu màu sắc của hai vết xăng đã bay hơi gồng nhau là đạt yêu cầu về độ sạch dầu mỡ. (Xăng dùng kiểm tra phải là xăng sạch, không lẫn tạp chất, không lẫn bẩn). + Đánh giá nghiệm thu: - Sau khi đã làm sạch một cấu kiện thép cần nghiệm thu ngay để phun sơn chống gỉ bảo vệ thép và ghi lại các kết quả nghiệm thu vào nhật ký thi công (Biểu 1 và Biểu 3 – Phụ lục 3). Thời gian phun lớp sơn chống gỉ thứ nhất không quá 4 giờ kể từ khi ngừng phun cát nếu thời tiết khô ráo. - Diện tích làm sạch đạt mức độ sạch yêu cầu ³ 95% mới được chấp thuận tiến hành thi công sơn. III. THI CÔNG SƠN 3.1. Đơn vị thi công sử dụng sơn theo yêu cầu của thiết kế và chỉ dẫn kỹ thuật của nhà chế tạo sơn cho từng công trình cầu thép. 3.2. Cần bố trí các cán bộ có chuyên môn về sơn để theo dõi giám sát chất lượng sơn cho công trình từ khi bắt đầu đến khi kết thúc. 3.3. Khi tiếp nhận sơn cần nhận đồng bộ các loại sơn (sơn chống gỉ, sơn phủ ), dung môi kèm theo các loại sơn và các phụ gia khác (nếu có). Tất cả các vật liệu sơn trên đều ở trạng thái bao bì nguyên bản, có đủ ký mã hiệu hàng hóa, nhà sản xuất, ngày tháng xuất xưởng của hàng hóa đó và kèm theo các phiếu kiểm tra đạt tiêu chuẩn ngành năm 1997, cũng như hướng dẫn của nhà sản xuất sơn. 3.4. Trước khi thi công sơn phải kiểm tra chất lượng bề mặt thép đã làm sạch và tư vấn giám sát đồng ý mới được tiến hành thi công sơn. 3.5. Thi công sơn tốt nhất bằng súng phun sơn dưới áp lực của khí nén, áp lực khí cho một đầu súng bình quân 3 atm. 3.6. Các trường hợp như sau cho phép dùng chổi quét sơn: + Mặt thép bị rỗ, nhiều điểm lồi lõm khác nhau. + Các vị trí có mối hàn, các góc cạnh của dầm thép. + Các vùng nối ghép của nhiều bản thép... + Khi thi công các loại sơn hệ một cấu tử có độ nhớt thấp (như sơn dầu), hoặc các sơn hệ hai cấu tử (như sơn epoxy). Những vị trí như trên phải dùng chổi quét sơn, quét và miết mạnh tay ngay từ lớp sơn chống gỉ đầu tiên lên mặt thép sao cho sơn được lấp kín các khe hở, sau đó mới tiến hành sơn theo thứ tự từng lớp một. 3.7. Thi công sơn bằng con lăn chỉ sử dụng khi đã tiến hành sơn lớp sơn dặm trước khi cần sơn thêm nhiều lớp để đạt độ dày ở bề mặt bằng phẳng. Tuyệt đối cấm sử dụng khi sơn ở những vị trí góc cạnh, những vị trí có đinh tán bulông. 3.8. Thi công sơn cần tuân thủ các điều kiện sau: + Khu vực phun sơn không có bụi bẩn, mặt bằng thoáng khí và cách ly hoàn toàn nguồn lửa. + Bề mặt thép đã được làm sạch theo yêu cầu. + Thời tiết khô ráo, nhiệt độ ngoài trời không nên quá 350C, độ ẩm không quá 80%. + Không sơn khi thời tiết sắp có mưa hoặc mưa đã hết nhưng không khí còn ẩm. + Không sơn khi có gió mạnh. + Thiết bị phun sơn cần đạt các chỉ tiêu kỹ thuật về độ sạch của khí nén và áp lực hơi. + Công nhân thi công sơn cần được huấn luyện về nghiệp vụ sơn và quy trình thi công sơn cầu thép. 3.9. Các công trình cầu thép xây mới hoặc duy tu bảo dưỡng sơn lại đều phải thực hiện các điều khoản quy định của công nghệ thi công sơn (xem Phụ lục 2.3). 3.10. Sau khi sơn xong toàn bộ số lớp sơn chống gỉ cần nghiệm thu đầy đủ các chỉ tiêu kỹ thuật (độ dính bám, tổng chiều dày các lớp sơn trên mặt thép), sau đó mới được chuyển sang sơn lớp sơn phủ (tất cả ghi theo biểu mẫu 2 – Phụ lục 3). 3.11. Đối với cầu thép làm mới, dầm thép chế sửa được sản xuất ở nhà máy, thì cần sơn đủ số lớp sơn chống gỉ và sơn tiếp từ 1 – 2 lớp sơn phủ để đảm bảo chống gỉ cho thép trong suốt thời gian thi công lắp ráp dầm thép. - Khi công trình cầu thép đã lắp xong, sơn nốt 1 – 2 lớp sơn phủ cuối cùng. Trước khi sơn lớp cuối cùng cần bổ khuyết đủ số lớp sơn bị xây sát, làm sạch bề mặt khỏi bụi bẩn và hơi nước, tốt nhất là lau lần cuối bằng dung môi pha sơn để tạo độ bám dính giữa lớp sơn cũ và lớp sơn mới. Chú ý: - Đối với công trình xây dựng mới mà thời gian thi công kéo dài, dầm thép đã sơn trên một năm mới lắp ráp thì cần phải sơn đủ số lớp sơn theo thiết kế. Sau khi đã lắp xong vẫn phải sơn thêm một lớp cuối cùng. - Những đường ống dẫn, hoặc các phụ kiện bằng thép đặt dưới gầm cầu phải sơn hoàn chỉnh trước khi đổ bê tông mặt cầu. 3.12. Việc nghiệm thu thi công sơn cần thực hiện: - Kiểm tra độ nhớt của sơn trước khi thi công (TCVN 2092-1993 – Phụ lục 1.2), pha khuấy sơn theo chỉ dẫn của nhà sản xuất. Nội dung kiểm tra ghi theo biểu mẫu số 4 – Phụ lục 3. - Kiểm tra độ sạch và áp lực khí nén, kiểm tra thao tác sơn. - Kiểm tra thời gian khô của sơn, thời gian sơn giữa các lớp sơn theo nhà sản xuất quy định. - Kiểm tra độ dày và độ bám dính của các lớp sơn chống gỉ (trước khi sơn lớp sơn phủ) và của toàn bộ các lớp sơn (sau khi kết thúc sơn phủ). (TCVN 2097-1993, Phụ lục 1.3). - Kiểm tra độ phủ của sơn trên các góc cạnh, đầu bulông, khe tiếp giáp nhiều lớp thép và các khuyết tật khác để hướng dẫn cho người thi công thực hiện đúng công nghệ sơn do nhà sản xuất quy định. 3.13. Công tác sơn cầu thép được thực hiện theo nhiều giai đoạn. Mội giai đoạn cần đánh giá chất lượng sơn và ghi vào hồ sơ thi công. - Giai đoạn thi công ở nhà máy. Phiếu đánh giá chất lượng được ghi theo Biểu mẫu 3 – Phụ lục 3. Trong đó thể hiện đầy đủ các loại sơn sử dụng, chỉ tiêu kỹ thuật của sơn (độ dính bám, chiều dày các lớp sơn), thời gian và thời tiết thi công. - Giai đoạn thi công tại hiện trường. Sản phẩm sơn gồm 2 phần: Sơn toàn bộ các bản nút, sơn bổ khuyết các vết xước và sơn phủ các lớp sơn cuối cùng cho toàn bộ dầm thép. Tất cả đều ghi theo Biểu mẫu 5 – Phụ lục 3. 3.14. Công tác sơn duy tu đối với cầu thép cũ nếu sơn lại toàn bộ thì nghiệm thu chất lượng thi công sơn giống như sơn dầm thép mới (tuân theo Biểu mẫu 5 – Phụ lục 3). Nếu sơn và từng phần, hỏng đâu sửa đó thì kiểm tra chất lượng sơn theo các hạng mục như sau: + Tên chi tiết sơn lại. + Mức độ sạch gỉ: % diện tích. + Loại sơn sử dụng: - Sơn chống gỉ: Ký mã hiệu; số lớp - Sơn phủ: Ký mã hiệu; số lớp + Độ dính bám của sơn trên thép. + Chiều dày tổng thể của các lớp sơn: - Sơn chống gỉ. - Sơn phủ. Các kết quả kiểm tra đều có ghi nhận của KCS, đơn vị thầu và tư vấn giám sát công trình. IV. AN TOÀN LAO ĐỘNG VÀ AN TOÀN GIAO THÔNG 4.1. Tất cả mọi hoạt động ảnh hưởng tới sức khỏe và sinh mạng con người phải được bảo đảm an toàn tuyệt đối. Nghiêm cấm công tác sơn khi chưa có biện pháp an toàn. 4.2. Khi tiếp xúc với hóa chất gây ăn mòn, tuyệt đối phải có găng tay cao su. 4.3. Khi tiếp xúc với hóa chất và vật liệu sơn, cần làm nơi thông thoáng, có khẩu trang. Trường hợp làm lâu dài thì phải thay ca, có biện pháp thông gió khi thi công. 4.4. Khi làm việc liên quan đến sơn nhất thiết phải có kính trắng bảo vệ mắt, có quần áo bảo hộ lao động. 4.5. Khi sơn bắn vào mắt cần đưa tới bệnh xá gần nhất, trường hợp xa bệnh xá phải rửa ngay mắt bằng nước sạch sau đó nhỏ dung dịch nước muối tinh khiết (NaCl) 5% và chuyển đi bệnh viện chuyên ngành. 4.6. Khi sơn rơi vào da phải nhanh chóng lau sạch bằng giẻ khi sơn còn ướt; sau đó rửa sạch bằng xà phòng. Trường hợp để quên hoặc không kịp lau có thể làm sạch bằng cách thấm giẻ vào dung môi pha sơn vắt khô lau đến khi hết sơn, sau đó rửa lại bằng xà phòng. 4.7. Khi làm việc với dung môi dễ cháy nổ, cần tuyệt đối đề phòng cháy nổ. Kho chứa sơn và dung môi phải tuyệt đối tránh xa nguồn lửa. 4.8. Nơi để sơn và dung môi phải có các thiết bị chữa cháy như cát, xẻng, bình chữa cháy đề phòng hỏa hoạn. Các thùng phải có nắp không để hơi rò rỉ. Khi có hỏa hoạn cần phải cắt ngay cầu dao điện. Dùng bình chữa cháy, cát dập tắt ngay ngọn lửa không để xảy ra cháy nổ và lây lan sang nơi khác. Báo ngay với cơ quan phòng cháy chữa cháy nếu đám cháy có nguy cơ lan rộng. 4.9. kiểm tra hệ thống điện bằng bút thử điện, kiểm tra lại đường dây, cầu dao điện đủ tải, đủ tiêu chuẩn chạy máy. 4.10. Kiểm tra thiết bị phun cát, bình khử, van an toàn, có khả năng đảm bảo an toàn khi hoạt động. Công việc này phải do cơ quan chuyên ngành kiểm tra và cấp giấy kiểm định. Nghiêm cấm sử dụng máy cũ mà không được sự chấp nhận của cơ quan có trách nhiệm. 4.11. Công việc vận hành máy phun cát phải là người được đào tạo nghiệp vụ. Thường xuyên sử dụng máy hoặc là người được hướng dẫn tỉ mỉ đã qua tập sự. 4.12. Người sử dụng thiết bị phun cát phải được trang bị thiết bị bảo hộ riêng theo quy định về an toàn lao động, như kính, mũ, khẩu trang 4.13. Khi thi công trên dầm thép cao phải có dây bảo hiểm, lưới đỡ, giàn giáo phải được chuẩn bị chắc chắn đúng như thiết kế. Có lưới dầy chắc không cho sơn rơi xuống phương tiện và người qua lại. 4.14. Khi thi công ở những nơi sông nước phải có thuyền và phao cứu sinh để phòng trường hợp xảy ra tai nạn. 4.15. Khu vực phun cát không được có người qua lại. Trường hợp những nơi có nhiều người qua lại cần tiến hành thi công ở thời điểm vắng người nhất, lựa chiều gió khi thi công, không để trường hợp cát bắn vào người và phương tiện qua lại. 4.16. Khu vực thi công phải có rào chắn, biển báo, đèn tín hiệu theo điều luật an toàn giao thông đường thủy, đường bộ. Rào chắn phải đúng thiết kế an toàn lao động, biển báo đèn tín hiệu phải đúng kích thước, kiểu cách về an toàn giao thông giúp cho mọi người có thể nhận biết từ xa. 4.17. Tất cả cán bộ công nhân viên thi công về sơn phải được huấn luyện về kỹ thuật sơn, có sức khỏe tốt, trong độ tuổi lao động, đặc biệt không dị ứng khi tiếp xúc với sơn. 4.18. Tất cả mọi hoạt động trong thi công không được ảnh hưởng xấu cho môi sinh khu vực. 4.19. Khi thi công xong các loại phế thải phải được gom lại cho xuống hố sâu lấp kín. 4.20. Trong quá trình thi công, không được đổ sơn thừa, dung môi, giẻ lau xuống sông gây ô nhiễm nguồn nước. V. PHẦN PHỤ LỤC PHỤ LỤC 1 DANH MỤC CÁC TIÊU CHUẨN LIÊN QUAN 1.1. 22 TCN 235-97: Sơn dùng cho cầu thép và kết cấu thép, yêu cầu kỹ thuật – phương pháp thử. 1.2. TCVN 2092-1993: Xác định độ nhớt. 1.3. TCVN 2097-1993: Xác định độ bám dính. 1.4. TCVN 2096-1993: Xác định thời gian khô. 1.5. 22 TCN 24-84: Quy trình thi công và nghiệm thu dầm cầu thép liên kết bằng bulông cường độ cao. PHỤ LỤC 2 2.1. Chất làm sạch loại nhũ sử dụng để tẩy dầu mỡ khỏi bề mặt thép bị nhiễm bẩn lớn, thường là các hỗn hợp trên cơ sở hydrocarbon có chứa tác nhân nhũ hóa. Có thể dùng công thức sau: - Dầu hỏa: 75% khối lượng. - Axit Cresylic: 10% khối lượng. - Axit Oleic: 10% khối lượng. - Natri hydroxit: 5% khối lượng. 2.2. Công nghệ làm sạch bằng phun cát: Dựa theo 22 TCN 24-84. 1. Cát dùng để phun phải là cát thạch anh, khô sạch. Độ ẩm của cát không lớn hơn 2%, cỡ hạt d < 2,5 mm (Nếu dùng cỡ hạt = 0,6 - 2 mm). Lượng hạt bụi trong cát có đường kính d < 0,5 mm không vượt quá 6% khối lượng. Hình 1. Sơ đồ thiết bị phun cát 1. Máy nén khí; 2. Thùng chứa nén khí; 3. Bộ phận lọc dầu, nước; 4. Thùng chứa cát; 5. Bộ phận trộn cát và khí; 6. Vòi phun cát. Hình 2. Biểu đồ lượng khí nén dùng trong thi công phụ thuộc vào áp lực không khí và đường kính vòi phun Hình 3. Vòi phun 2. Việc sấy khô cát dùng hệ thống lò quay đốt bằng nhiên liệu lỏng. Trong điều kiện thuận lợi nên phơi cát ngoài bãi (mùa hè hoặc mùa khô hanh) nhưng phải kiểm tra đảm bảo các yêu cầu ở Điều 1. 3. Các bộ phận chính của thiết bị phun cát (đưa ra Hình 1 – Phụ lục 2.1) gồm: Đầu phun cát, phễu chứa cát, thùng chứa khí nén, bộ phận lọc dầu, nước, ống dẫn, máy hơi ép các thiết bị này phải được chế tạo đảm bảo an toàn khi dùng áp lực tới 6 atm và phải được đăng ký, kiểm tra theo quy phạm kỹ thuật an toàn QPVN 2-75. 4. Căn cứ vào khối lượng công tác phun cát, có thể dùng các thiết bị có kích thước phù hợp như bình cát hai ngăn, một ngăn hoặc không có ngăn. 5. Để đảm bảo máy phun cát làm việc bình thường, khí nén cần có áp lực 3,5 – 5 atm. Trị số này tùy thuộc vào áp lực khí nén và đường kính vòi phun (Xem Biểu đồ Hình 2 – Phụ lục 2.1). Việc xác định lượng khí nén dùng trong thi công phun cát phụ thuộc vào áp lực không khí và đường kính vòi phun. 6. Dùng ống cao su có đường kính trong 25 mm để cấp khí nén vào bình phun cát và ống cao su có đường kính trong 32 mm để cấp hỗn hợp cát và khí vào vòi phun cát. 7. Để phun cát, có thể dùng các loại vòi phun bằng thép có cấu tạo hợp lý, bằng vật liệu sành sứ. Vật liệu làm chi tiết lõi vòi phun dùng các loại thép giàu mangan. 8. Trong quá trình phun cát, phải thường xuyên kiểm tra đường kính miệng vòi phun. Nếu đường kính trong của miệng vòi phun lớn hơn 10 mm phải thay thế vòi phun. 9. Khi gia công phun cát, miệng vòi phun cần đặt cách bề mặt phun khoảng cách D và nghiêng một góc a (Hình 3 – Phụ lục 2.1) theo quy định sau: - Khi phun tạo ma sát. D = 15 ¸ 30 cm. a = 750 ¸ 800 - Khi phun tẩy gỉ. D = 15 ¸ 30 cm. a = 450 ¸ 500 Phun cát tẩy gỉ trước, phun cát tạo ma sát sau. 10. Khí nén dùng trong máy phun cát phải được làm sạch dầu và nước để tránh làm giảm hệ số ma sát của bề mặt phun, bảo đảm sự làm việc bình thường của máy phun. Trong mỗi ca phun phải kiểm tra độ sạch của khí. Cách kiểm tra như sau: Hướng vòi phun có khí nén lên bề mặt tờ giấy có vạch nét chì. Sau một phút nếu giấy không bị ẩm và nét chì không bị mờ là độ sạch đảm bảo. Nếu không đạt phải kiểm tra bộ phận lọc dầu, nước của máy và bình hơi ép. 11. Tùy theo mức độ han gỉ của thép mà điều chỉnh tốc độ di chuyển vòi phun, sao cho cát bắn tới đâu gỉ sạch tới đó, bề mặt thép hiện lên ánh kim loại đồng nhất. 12. Khi phun cát làm sạch bề mặt xong một cấu kiện thép, cần ngừng phun cát và thổi khí nén trực tiếp lên bề mặt thép để làm sạch bụi sau đó chuyển ngay sang khu vực khác để làm thủ tục nghiệm thu và sơn. 13. Thời gian chuyển tiếp từ sau khi phun cát xong đến khi bắt đầu lớp sơn chống gỉ thứ nhất không quá 4 giờ kể từ khi ngừng phun cát theo cấu kiện đó. Nếu để lâu sẽ xuất hiện gỉ, khi đã xuất hiện gỉ thì phải phun cát lại mới được sơn. 14. Mặt bằng phun cát phải tương đối rộng. Bụi cát ở vùng phun cát không làm ảnh hưởng đến các cấu kiện đã phun cát sạch và chuẩn bị sơn. 15. Các thiết bị phun cát phải đảm bảo kỹ thuật an toàn. 16. Các vật liệu: Cát, khí nén, phải đạt tiêu chuẩn chất lượng. 17. Không phun cát khi trời mưa, không phun cát vào ban đêm ở ngoài trời có sương mùa, nên phun cát ở độ ẩm khí quyển < 70%. 18. Phải phun cát từ đầu trong một số trường hợp sau + Những dầm thép đang hoặc đã phun cát xong nhưng chưa kịp sơn, mà gặp phải mưa. + Những dầm thép đã sơn được 1 hoặc 2 lớp sơn chống gỉ, sau đó gặp mưa kéo dài. Khi hết mưa, trên mặt thép xuất hiện những đốm gỉ xen kẽ sơn, do lớp sơn chưa đủ độ dày để phủ kín mặt thép nên đã bị nước thấm vào và gây ra han gỉ rất nhanh. Vì vậy sau mỗi đợt mưa cán bộ kỹ thuật, KCS cần kiểm tra kỹ từng thanh dầm thép đang thi công phun cát, phun sơn, nếu phát hiện gỉ cần làm lại từ đầu. 2.3. Một số quy định trong thi công sơn. 1. Kiểm tra cỡ đầu phun và áp suất đầu ra (theo quy định của nhà sản xuất sơn). 2. Khoảng cách từ đầu súng phun đến bề mặt sơn cách nhau từ 30 – 35 cm và vuông góc với bề mặt cầu sơn (Hình 4 – Phụ lục 2). 3. Tốc độ đưa súng phải đều và theo thứ tự từng giải sơn một trên mặt thép. Mỗi giải sơn phun từ 50 – 100 cm. Sơn gối lên giải trước từ 25 – 50% để đảm bảo độ dày màng sơn. 4. Sơn đến đâu đạt độ phủ kín đến đó. Mặt sơn bóng đều, không có vết loang, không có vệt sơn bị chảy trên mặt thép. 5. Sơn từng lớp trên toàn bộ dầm thép hoặc trên một chi tiết. Sau đó để cho sơn khô hoàn toàn, kiểm tra chiều dày lớp sơn. Nếu sơn đã đạt chiều dày thì chuyển sang lớp tiếp sau. Nên phun lớp trước và lớp sau theo kiểu ngang dọc “Phun chữ thập” để có được màng sơn dày đều. Nếu lớp sơn chưa đạt chiều dày thì cần bổ khuyết ngay rồi mới được chuyển sang lớp tiếp sau. 1. Luôn luôn giữ súng phun chĩa vào bề mặt ở góc 900. 2. Luôn luôn giữ cùng một khoảng cách trong quá trình phun. Hình 4. Kỹ thuật phun đúng PHỤ LỤC 3 CÁC MẪU BIỂU NHẬT KÝ THI CÔNG 3.1. Mẫu biểu số 1: Nhật ký thi công các số liệu làm sạch bề mặt thép. 3.2. Mẫu biểu số 2: Nhật ký thi công sơn. 3.3. Mẫu biểu số 3: Phiếu nghiệm thu sơn dầm thép. 3.4. Mẫu biểu số 4: Nhật ký theo dõi pha sơn. 3.5. Mẫu biểu số 5: Kết quả kiểm tra chất lượng sơn phủ ngoài cùng. Mẫu biểu số 1 NHẬT KÝ THI CÔNG CÁC SỐ LIỆU LÀM SẠCH BỀ MẶT THÉP Ngày/tháng Tên chi tiết Ký mã hiệu dầm thép Thời tiết thi công Mức độ sạch gỉ, %S Xác nhận của KCS (1) (2) (3) (4) (5) (6) Mẫu biểu số 2 NHẬT KÝ THI CÔNG SƠN Ngày/tháng Lớp sơn Thời tiết Chiều dày (mm) Độ bám dính, %S Xác nhận của KCS (1) (2) (3) (4) (5) (6) Lớp 1 Lớp 2 Lớp 3 . Biểu mẫu số 3 CÔNG TY CẦU ------------- CỘNG HÒA XÃ HỘI CHỦ NGHĨA VIỆT NAM Độc lập – Tự do – Hạnh phúc ------------------- Số: /KCS Hà Nội, ngày . tháng . năm .. PHIẾU NGHIỆM THU SƠN DẦM THÉP Tên công trình: cầu . Tên chi tiết: Ký tên:.. Thời gian phun cát: NgàyTháng .Năm. Mức độ sạch gỉ......% sạch bụi bẩn, dầu mỡ ...% Phun sơn (lớp) Loại sơn Loại dung môi Thời gian ngày/tháng Thời tiết (nhiệt độ, 0C) Chiều dày Độ dính bám trên thép (%) Sơn chống gỉ Lớp thứ 1 Lớp thứ 2 Lớp thứ 3 Sơn phủ Lớp thứ 1 Lớp thứ 2 Nhận xét: Tổ phun cát Tổ phun sơn Phân xưởng Phòng KT và KCS Giám đốc N/M Giám sát Biểu mẫu số 4 NHẬT KÝ THEO DÕI PHA SƠN Tên công trình: . Đơn vị thi công: Ngày/tháng Loại vật liệu Số ký hiệu thùng sơn Độ nhớt, sec (nguyên bản) Lượng dung môi pha thêm Độ nhớt, sec (thi công) Người pha sơn ký Sơn Dung môi (1) (2) (3) (4) (5) (6) (7) (8) Mẫu biểu số 5 KẾT QUẢ KIỂM TRA CHẤT LƯỢNG SƠN PHỦ NGOÀI CÙNG - Tên công trình: Nhịp cầu - Thời gian thi công từ: đến: - Loại sơn sử dụng: ký hiệu: - Độ dính bám: - Số lớp: TT Tên cấu kiện do Tổng chiều dày các lớp sơn mm (tính bình quân) (1) (2) (3) 1 2 3 4 5 6 7 8 9 Khoang 1 Thanh đứng Thanh xiên . Dầm dọc Dầm ngang Mạ thượng Mạ hạ Khoang 2 Khoang 3 . Khoang 4 . Đơn vị thi công Giám sát công trình
File đính kèm:
son_cau_thep_va_ket_cau_thep_quy_trinh_thi_cong_va_nghiem_th.doc