Ảnh hưởng của một số tham số công nghệ đến chất lượng chi tiết hợp kim Niken DZ125l phục hồi bằng công nghệ tạo hình bằng tia laser
Tóm tắt: Bài báo sử dụng phương pháp thực nghiệm nghiên cứu sự ảnh hưởng
của một số tham số công nghệ đến chất lượng chi tiết hợp kim ni ken DZ125L được
phục hồi bằng công nghệ tạo hình bằng tia laser (LDMF). Thông qua nghiên cứu
quá trình tạo hình đường đơn và vật thể khối để tìm ra phạm vi tham số công nghệ
hợp lí nhằm nâng cao chất lượng của chi tiết sau khi phục hồi. Kết quả thí nghiệm
cho thấy chi tiết bị đứt ở phần vật liệu nền, điều đó chứng tỏ vùng liên kết giữa vật
liệu nền và vật liệu phục hồi có chất lượng tốt. Kết quả thử kéo phần vật liệu tạo
hình bằng tia laser cho thấy giới hạn bền của vật liệu tạo hình bằng công nghệ
LDMF lớn hơn giới hạn bền của vật liệu chế tạo bằng công nghệ đúc, đó là do đặc
điểm về tổ chức tế vi của vật liệu tạo hình bằng tia laser là tổ chức epitaxial dạng
tinh thể hình trụ rất nhỏ, dài, phát triển thẳng đứng xuyên qua các lớp vật liệu.
Tóm tắt nội dung tài liệu: Ảnh hưởng của một số tham số công nghệ đến chất lượng chi tiết hợp kim Niken DZ125l phục hồi bằng công nghệ tạo hình bằng tia laser
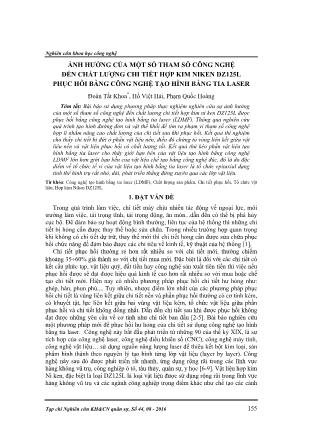
Nghiên cứu khoa học công nghệ Tạp chí Nghiên cứu KH&CN quân sự, Số 44, 08 - 2016 155 ẢNH HƯỞNG CỦA MỘT SỐ THAM SỐ CÔNG NGHỆ ĐẾN CHẤT LƯỢNG CHI TIẾT HỢP KIM NIKEN DZ125L PHỤC HỒI BẰNG CÔNG NGHỆ TẠO HÌNH BẰNG TIA LASER Đoàn Tất Khoa*, Hồ Việt Hải, Phạm Quốc Hoàng Tóm tắt: Bài báo sử dụng phương pháp thực nghiệm nghiên cứu sự ảnh hưởng của một số tham số công nghệ đến chất lượng chi tiết hợp kim ni ken DZ125L được phục hồi bằng công nghệ tạo hình bằng tia laser (LDMF). Thông qua nghiên cứu quá trình tạo hình đường đơn và vật thể khối để tìm ra phạm vi tham số công nghệ hợp lí nhằm nâng cao chất lượng của chi tiết sau khi phục hồi. Kết quả thí nghiệm cho thấy chi tiết bị đứt ở phần vật liệu nền, điều đó chứng tỏ vùng liên kết giữa vật liệu nền và vật liệu phục hồi có chất lượng tốt. Kết quả thử kéo phần vật liệu tạo hình bằng tia laser cho thấy giới hạn bền của vật liệu tạo hình bằng công nghệ LDMF lớn hơn giới hạn bền của vật liệu chế tạo bằng công nghệ đúc, đó là do đặc điểm về tổ chức tế vi của vật liệu tạo hình bằng tia laser là tổ chức epitaxial dạng tinh thể hình trụ rất nhỏ, dài, phát triển thẳng đứng xuyên qua các lớp vật liệu. Từ khóa: Công nghệ tạo hình bằng tia laser (LDMF), Chất lượng sản phẩm, Chi tiết phục hồi, Tổ chức vật liệu, Hợp kim Niken DZ125L. 1. ĐẶT VẤN ĐỀ Trong quá trình làm việc, chi tiết máy chịu nhiều tác động về ngoại lực, môi trường làm việc, tải trọng tĩnh, tải trọng động, ăn mòn...dẫn đến có thể bị phá hủy cục bộ. Để đảm bảo sự hoạt động bình thường, liên tục của hệ thống thì những chi tiết bị hỏng cần được thay thế hoặc sửa chữa. Trong nhiều trường hợp quan trọng khi không có chi tiết dự trữ, thay thế mới thì chi tiết hỏng cần được sửa chữa phục hồi chức năng để đảm bảo được các chỉ tiêu về kinh tế, kỹ thuật của hệ thống [1]. Chi tiết phục hồi thường rẻ hơn rất nhiều so với chi tiết mới, thường chiếm khoảng 3560% giá thành so với chi tiết mua mới. Đặc biệt là đối với các chi tiết có kết cấu phức tạp, vật liệu quý, đắt tiền hay công nghệ sản xuất tiên tiến thì việc nếu phục hồi được sẽ đạt được hiệu quả kinh tế cao hơn rất nhiều so với mua hoặc chế tạo chi tiết mới. Hiện nay có nhiều phương pháp phục hồi chi tiết hư hỏng như: ghép, hàn, phun phủ.... Tuy nhiên, nhược điểm lớn nhất của các phương pháp phục hồi chi tiết là vùng liên kết giữa chi tiết nền và phần phục hồi thường có cơ tính kém, có khuyết tật, lực liên kết giữa hai vùng vật liệu kém, tổ chức vật liệu giữa phần phục hồi và chi tiết không đồng nhất. Dẫn đến chi tiết sau khi được phục hồi không đạt được những yêu cầu về cơ tính như chi tiết ban đầu [2-5]. Bài báo nghiên cứu một phương pháp mới để phục hồi hư hỏng của chi tiết sử dụng công nghệ tạo hình bằng tia laser. Công nghệ này bắt đầu phát triển từ những 90 của thế kỷ XIX, là sự tích hợp của công nghệ laser, công nghệ điều khiển số (CNC), công nghệ máy tính, công nghệ vật liệu sử dụng nguồn năng lượng laser để thiêu kết bột kim loại, sản phẩm hình thành theo nguyên lý tạo hình từng lớp vật liệu (layer by layer). Công nghệ này sau đó được phát triển rất nhanh, ứng dụng rộng rãi trong các lĩnh vực hàng không vũ trụ, công nghiệp ô tô, tàu thủy, quân sự, y học [6-9]. Vật liệu hợp kim Ni ken, đặc biệt là loại DZ125L là loại vật liệu được sử dụng rộng rãi trong lĩnh vực hàng không vũ trụ và các ngành công nghiệp trọng điểm khác như chế tạo các cánh Cơ kỹ thuật & Kỹ thuật cơ khí động lực Đ. T. Khoa, H. V. Hải, P. Q. Hoàng, “Ảnh hưởng của một số tạo hình bằng tia laser.” 156 tuabin...[10, 11]. Việc phục hồi các chi tiết hư hỏng làm từ vật liệu này là một yêu cầu hết sức cấp thiết và có ý nghĩa quan trọng trong thực tiễn. 2. THÍ NGHIỆM 2.1. Thiết bị và vật liệu thí nghiệm Thí nghiệm được thực hiện tại phòng thí nghiệm trọng điểm quốc gia thuộc trường đại học Giao thông Tây An-Trung quốc. Máy tạo hình bằng tia lase như thể hiện trên hình 1, bao gồm: nguồn phát chùm tia laser Nd: YAG, số hiệu JK1002SM, công suất 1kW; tiêu cự 160 mm, đường kính hội tụ chùm laser 0,5 mm; máy cấp bột kim loại số hiệu DSPF-2; đầu phun cấp bột đồng trục với đầu phát tia laser; hệ thống điều khiển CNC 3 trục; hệ thống cấp khí trơ Argon và một số thiết bị trợ giúp khác. Các thiết bị thí nghiệm khác bao gồm kính hiển vi Keyence VH-8000 của Nhật, máy đo ứng suất kéo MTS Landmark. Hình 1. Hệ thống tạo hình LDMF; (a) sơ đồ nguyên lí; (b) thiết bị thí nghiệm. Vật liệu thí nghiệm: tấm nền sử dụng loại hợp kim ni ken DZ125L dạng tấm; vật liệu tạo hình sử dụng hợp kim ni ken DZ125L dạng bột, thành phần vật liệu hợp kim ni ken DZ125L như thể hiện trong bảng 1[12]. Bảng 1. Thành phần vật liệu hợp kim ni ken DZ125L (%). Thành phần C Cr Co Mo W Al Ti Ta B Ni Tấm nền 0,07 9,09 10,00 2,09 7,17 4,48 3,05 3,64 0,011 Cân bằng Bột 0,09 9,70 9,64 2,18 7,14 4,90 3,12 3,78 0,015 Cân bằng 2.2. Phương pháp thí nghiệm Để nghiên cứu ảnh hưởng của các tham số công nghệ đến chất lượng chi tiết sau khi phục hồi tiến hành như sau: giả sử chi tiết ban đầu bị hư hỏng, mất đi một phần kết cấu, nhiệm vụ là sử dụng công nghệ LDMF tạo hình phần kết cấu bị hư hỏng để khôi phục lại tình trạng ban đầu của chi tiết. Quá trình thí nghiệm như sau: sử dụng phương pháp quy hoạch thực nghiệm để tìm ra các tham số công nghệ hợp lí để nâng cao chất lượng đường đơn, làm cơ sở cho quá trình hình thành vật thể dạng khối. Sau đó tạo hình các mẫu để thử cơ tính của chi tiết sau khi phục hồi và của vật liệu tạo hình bằng công nghệ LDMF. Nghiên cứu khoa học công nghệ Tạp chí Nghiên cứu KH&CN quân sự, Số 44, 08 - 2016 157 3. KẾT QUẢ THÍ NGHIỆM VÀ PHÂN TÍCH 3.1. Ảnh hưởng của tham số công nghệ đến chất lượng đường đơn lớp phủ Trong quá trình phục hồi hư hỏng bằng công nghệ LDMF, đường đơn là đơn vị cơ bản để hình thành vùng chi tiết phục hồi. Các đặc trưng về kích thước, hình dáng hình học của đường đơn này ảnh hưởng trực tiếp đến chất lượng sản phẩm. Do đó, nghiên cứu quy luật ảnh hưởng của các tham số công nghệ đến các đặc trưng về kích thước mặt cắt ngang đường đơn, từ đó tìm ra phạm vi tham số công nghệ hợp lí. Căn cứ vào những kết quả nghiên cứu về công nghệ LDMF, các yếu tố ảnh hưởng tới các chỉ tiêu chất lượng tạo hình là công suất nguồn laser, tốc độ quét chùm laser, tốc độ cấp bột và khoảng cách đầu phun [11, 13]. Sử dụng phương pháp quy hoạch thực nghiệm ma trận trực giao để xác định các tham số công nghệ tối ưu, kết quả thí nghiệm như hình 2(a) thể hiện, sau đó các mẫu được cắt theo phương vuông góc với phương chiều dài đường đơn hình 2(b), các đặc trưng về kích thước mặt cắt ngang của mẫu được xác định trên kính hiển vi điện tử Keyence VH-8000, kết quả như thể hiện trong hình 2(c). Hình 2. Các mẫu thí nghiệm; (a) đường đơn; (b) mẫu cắt; (c) mặt cắt ngang. Căn cứ vào kết quả thí nghiệm, mức độ ảnh hưởng của các tham số công nghệ đến độ cao đường đơn lần lượt là công suất laser > tốc độ quét > khoảng cách giữa vị trí hội tụ dòng bột và vị trí vùng nóng chảy > lượng cấp bột; mức độ ảnh hưởng của các tham số công nghệ đến độ rộng đường đơn lần lượt là công suất laser > lượng cấp bột > khoảng cách giữa vị trí hội tụ dòng bột và vị trí vùng nóng chảy > tốc độ quét. Từ kết quả thực nghiệm thu được, qua phân tích và kết hợp với chỉ tiêu đặt ra là độ cao đường đơn khoảng 0,09÷0,11 mm, độ rộng đường đơn khoảng 0,5÷0,55 mm, phạm vi tham số công nghệ thỏa mãn yêu cầu trên được xác định như trong bảng 2. Bảng 2. Tham số công nghệ hợp lí. Tham số công nghệ Công suất laser P/(W) Tốc độ quét Vs/(mm/s) Lượng cấp bột Mp/(g/phut) Khoảng cách Zp/(mm) Giá trị 220÷230 8÷10 5,5÷6,5 -2 ÷ -1 3.2. Ảnh hưởng của tham số công nghệ đến chất lượng của bề mặt phục hồi Khi tạo hình một bề mặt lên vùng kim loại nền, để đảm bảo chất lượng liên kết và độ bằng phẳng bề mặt phục hồi thì phải đảm bảo khoảng cách giữa các đường quét ở một giá trị thích hợp. Hình 3 thể hiện mô hình ảnh hưởng của các giá trị khoảng cách đường quét khác nhau đến độ bằng phẳng bề mặt lớp phục hồi. Khi Cơ kỹ thuật & Kỹ thuật cơ khí động lực Đ. T. Khoa, H. V. Hải, P. Q. Hoàng, “Ảnh hưởng của một số tạo hình bằng tia laser.” 158 khoảng cách giữa các đường quét quá nhỏ hoặc quá lớn sẽ tạo ra bề mặt không bằng phẳng, ảnh hưởng đến lớp phủ tiếp theo. Hình 3. Ảnh hưởng của khoảng cách đường quét đến độ bằng phẳng bề mặt lớp phủ; (a) khoảng cách quá lớn; (b) khoảng cách hợp lí; (c) khoảng cách quá nhỏ. Để tìm ra giá trị khoảng cách hợp lí, thí nghiệm với các giá trị khoảng cách khác nhau, tham số công nghệ như thể hiện trong bảng 3, tạo hình 5 đường phủ, chiều dài 20 mm. Bảng 3. Tham số công nghệ. Tham số công nghệ Công suất laser P/(W) Tốc độ quét Vs/(mm/s) Lượng cấp bột Mp/(g/phút) Khoảng cách đầu phun Zp/(mm) Khoảng cách đường L/(mm) Giá trị 230 10 6,5 -1 0,25; 0,28; 0,31; 0,34; 0,37; 0,4; 0,43 Kết quả thí nghiệm như thể hiện trong hình 4, từ trái qua phải là kết quả khi mà thay đổi giá trị khoảng cách L từ 0,430,25 mm. Hình 4. Ảnh hưởng của khoảng cách đường quét tới chất lượng lớp phủ; (a) hình ảnh các mẫu; (b) khi phủ một lớp; (c) khi phủ hai lớp; (d) khi phủ năm lớp. Trên hình 4 có thể thấy khi khoảng cách đường quét nằm trong khoảng 0,340,37 mm thì bề mặt lớp phủ tương đối đồng đều và bằng phẳng khi số lớp phủ khác nhau. Khi khoảng cách đường quét giảm đi (nhỏ hơn 0,34 mm) thì chất lượng bề mặt lớp phủ không đồng đều, có xu hướng nhô cao ở giữa và chảy sang hai bên; khi khoảng cách đường quét lớn hơn 0,37 mm thì xuất hiện nhiều lồi lõm trên bề mặt, chiều rộng chi tiết tăng lên, không đảm bảo được độ cao của chi tiết theo tính toán. Do đó, khoảng cách đường quét hợp lí nằm trong khoảng 0,34-0,37 mm. 3.3. Thử cơ tính của mẫu sau khi được phục hồi Tấm nền chi tiết sử dụng một mẫu dạng thanh vật liệu hợp kim ni ken DZ125L chế tạo bằng phương pháp đúc có kích thước 10 8 30 mm như hình 5(a) thể hiện, sau đó sử dụng công nghệ tạo hình bằng tia laser để tạo hình lên trên bề mặt tấm Nghiên cứu khoa học công nghệ Tạp chí Nghiên cứu KH&CN quân sự, Số 44, 08 - 2016 159 nền một hình trụ có kích thước 6 30 mm (như hình 5(b) thể hiện), chế độ công nghệ khi phục hồi sử dụng các tham số tối ưu là kết quả trong các mục 3.1 và 3.2; cụ thể công suất nguồn laser là 230 W, tốc độ cấp bột 10 mm/s, lượng cấp bột 6,5 g/phút, khoảng cách đầu phun -1 mm, khoảng cách các đường 0,35 mm. Để thử cơ tính của vùng liên kết giữa vật liệu nền và vật liệu phục hồi, sử dụng phương pháp thử kéo, mẫu kéo dạng trụ theo tiêu chuẩn ASTM E8M-04 của Mỹ [14]. Các mẫu sau quá trình phục hồi được gia công thành các mẫu kéo đạt kích thước như hình 6 sao cho liên kết giữa hai vùng vật liệu nền và vật liệu phục hồi nằm giữa mẫu thử. Trong điều kiện phòng thí nghiệm, sử dụng máy đo ứng suất kéo MTS Landmark tiến hành đo các chỉ tiêu về cơ tính của các mẫu, các chỉ tiêu chủ yếu bao gồm: giới hạn bền, giới hạn chảy, độ giãn dài. Sau khi kéo, các mẫu bị đứt như hình 6 thể hiện, kết quả đo tương ứng như thể hiện trong bảng 4. Hình 5. Hình ảnh mẫu thử nghiệm; (a) mẫu nền; (b) mẫu sau khi phục hồi Hình 6. Các mẫu sau khi kéo; (a) mẫu số 1; (b) mẫu số 2; (c) mẫu số 3. Bảng 4. Các giá trị về cơ tính vật liệu của mẫu thử. Mẫu đo Giới hạn bền σb (MPa) Giới hạn chảy σ0.2 (MPa) Độ giãn dài δ (%) Mẫu số 1 1310 980 13,5 Mẫu số 2 1260 830 10,8 Mẫu số 3 1235 795 9,6 Trung bình 1268 868 11,3 Từ hình 6 có thể thấy, các mẫu đều bị gẫy ở vùng kim loại nền (tức là vùng kim loại đúc) mà không bị gẫy ở khu vực liên kết giữa hai vùng vật liệu. Điều này chứng tỏ: thứ nhất là liên kết giữa vùng kim loại nền và vùng kim loại phục hồi tốt, giới hạn bền lớn hơn giới hạn bền của vùng kim loại nền; thứ hai là giới hạn bền của của vùng kim loại phục hồi bằng công nghệ LDMF cũng lớn hơn giới hạn bền của vùng kim loại nền. 3.4. Đo giới hạn bền của vật liệu DZ125L tạo hình bằng công nghệ LDMF Chế tạo mẫu thí nghiệm: mẫu đo giới hạn bền được chế tạo theo công nghệ LDMF, hình dáng và kích thước căn cứ theo tiêu chuẩn về mẫu thí nghiệm ASTM E8M-04 của Mỹ [14]. Để đo lường và phân tích toàn diện cơ tính của vật liệu, thí Cơ kỹ thuật & Kỹ thuật cơ khí động lực Đ. T. Khoa, H. V. Hải, P. Q. Hoàng, “Ảnh hưởng của một số tạo hình bằng tia laser.” 160 nghiệm chế tạo ba mẫu như hình 7(a) thể hiện với các tham số công nghệ tối ưu như trong mục 3.3. Sau đó, căn cứ theo hình dáng, kích thước tiêu chuẩn sử dụng phương pháp cắt dây tia lửa điện (WEDM) để cắt thành các mẫu thí nghiệm như hình 7(b) thể hiện, kết quả đo tương ứng được thể hiện trong bảng 5. Hình 7. Mẫu thử; (a) mẫu tạo hình; (b) mẫu sau khi cắt. Hình 8. Tổ chức Epitaxial của vật liệu tạo hình bởi LDMF; (a) mặt cắt ngang; (b) mặt cắt đứng. Hình 9. Tổ chức tế vi vùng liên kết giữa hai vùng vật liệu. Bảng 5. Các giá trị về cơ tính vật liệu hợp kim ni ken DZ125L. Mẫu đo Giới hạn bền σb (MPa) Giới hạn chảy σ0.2 (MPa) Độ giãn dài δ (%) Mẫu số 1 1435 1020 6,8 Mẫu số 2 1416 995 5,4 Mẫu số 3 1398 987 5,3 Trung bình 1416 1000 5,8 Từ kết quả đo cho thấy, giới hạn bền trung bình của các mẫu là 1416 MPa, giới hạn chảy là 1000 MPa. So với công nghệ đúc điển hình vật liệu hợp kim DZ125L có giới hạn bền là 1315 MPa và giới hạn chảy là 990 MPa [12] thì chi tiết chế tạo bởi công nghệ LDMF có giới hạn bền và giới hạn chảy lớn hơn, do đó khi thử kéo mẫu bị đứt ở phần vật liệu đúc. Điều này có thể được lí giải thông qua đặc tính về tổ chức vật liệu của chi tiết chế tạo bằng công nghệ LDMF. 3.5. Tổ chức tế vi của vật liệu DZ125L tạo hình bằng công nghệ LDMF Hình 8 thể hiện hình ảnh về tổ chức tế vi của vật liệu hợp kim ni ken DZ125L tạo hình bằng tia laser, trong đó hình 8(a) thể hiện tổ chức tế vi của vật liệu theo mặt cắt ngang song song với phương quét chùm tia laser (vuông góc với phương thẳng đứng), hình 8(b) thể hiện hình ảnh tổ chức tế vi vật liệu theo phương mặt cắt bên vuông góc với phương quét chùm tia laser. Trên hình 8 có thể thấy đặc điểm quan trọng về tổ chức của vật liệu hợp kim ni ken DZ125L khi tạo hình bởi công Nghiên cứu khoa học công nghệ Tạp chí Nghiên cứu KH&CN quân sự, Số 44, 08 - 2016 161 nghệ LDMF là tổ chức epitaxial dạng tinh thể hình trụ rất nhỏ, dài, phát triển thẳng đứng (vuông góc với phương quét chùm tia laser). Đó là do quá trình kết tinh với tốc độ rất nhanh, thang độ nhiệt độ lớn, do đó mà tổ chức tinh thể nhỏ, đồng đều; mặt khác quá trình kết tinh diễn ra trên bề mặt biên giới giữa thể rắn và thể lỏng, điều này đảm bảo trong toàn bộ quá trình kết tinh pha lỏng và pha rắn luôn luôn tiếp xúc với nhau, tổ chức vật liệu này thuộc loại tổ chức epitaxial dạng tinh thể hình trụ điển hình. Trên hình 8(b) còn có thể thấy được liên kết giữa các lớp tạo hình liên tục, điều này không chỉ nâng cao cơ tính vật liệu mà còn đảm bảo cho tổ chức tế vi phát triển liên tục giữa các lớp. Hình 9 thể hiện tổ chức tế vi của vùng vật liệu nền và vùng vật liệu phục hồi. Trong quá trình phục hồi, chùm tia laser sẽ làm nóng chảy bột vật liệu tạo hình và một phần vật liệu nền, do đó vùng liên kết sẽ là sự pha loãng của hai vật liệu ở trạng thái nóng chảy, sau đó mới kết tinh. Chính vì vậy mà đảm bảo được chất lượng lực liên kết giữa hai vùng vật liệu. 4. KẾT LUẬN Thông qua nghiên cứu thực nghiệm, sử dụng công nghệ LDMF để phục hồi các chi tiết máy hư hỏng đối với loại vật liệu hợp kim ni ken DZ125L cho thấy: với các tham số công nghệ hợp lí có thể đạt được chất lượng liên kết giữa vật liệu nền và vật liệu phục hồi tốt; cơ tính của vật liệu phục hồi cao là do tổ chức tế vi của vùng vật liệu phục hồi bằng công nghệ LDMF là dạng tổ chức epitaxial dạng tinh thể hình trụ, dài, phát triển liên tục giữa các lớp phủ; do đó, mà tăng được giới hạn bền của vật liệu. Chi tiết vật liệu hợp kim ni ken DZ125L hư hỏng được phục hồi bằng công nghệ LDMF đảm bảo được chất lượng về cơ tính cho sản phẩm. TÀI LIỆU THAM KHẢO [1]. Nguyễn Trọng Hiệp., “Chi tiết máy”, NXB Giáo dục, 2010, trang 40-50. [2]. Nguyễn Thúc Hà., “Công nghệ Hàn”, NXB Khoa học và kỹ thuật, Hà nội, 2010, trang 30-34. [3]. Nguyễn Đức Thắng., “Đảm bảo chất lượng hàn”, NXB Khoa học và kỹ thuật, Hà nội, 2009, trang 7-10. [4]. Trần Minh Hoàng., “Công nghệ mạ điện”, NXB Khoa học và kỹ thuật, Hà nội, 1998, trang 70-72. [5]. Nguyễn Văn Thông., “Công nghệ phun phủ”, NXB Khoa học và kỹ thuật, Hà nội, 2012, trang 44-46. [6]. Chua C. K., Leong K. F., and Lim C. S. “Rapid prototyping Principle and Applications”, World Scientific, Singapore, 2003, pp. 178. [7]. Y. P. Kathuria. “Some aspects of laser surface cladding in the turbine industry”, Surface and Coatings Technology, 132 (2000), 262-269. [8]. Lei.Wang and Shuai.Wang. “Effects of precipitated phases on the crack propagation behaviour of a Ni-based superalloy”, International Journal of Fatigue, 62(2014), 210-216. [9]. Hao Nanhai., Lu Wei and Zuo TieZhuan. “Themal mechanical coupling FAE of temperature field in Laser cladding process”, Suface technology, 6(2004), 10-14. [10]. Feixue Yang, Enze Liu, “Influence of Ti content on microstructure, mechanical Cơ kỹ thuật & Kỹ thuật cơ khí động lực Đ. T. Khoa, H. V. Hải, P. Q. Hoàng, “Ảnh hưởng của một số tạo hình bằng tia laser.” 162 properties and castability of directionally solidified superalloy DZ125L”, Materials & Design, 61 (2014), 41-49 [11]. Li dichen, Lu Bingheng... “Effect of scanning methods on the cracking of the DZ125L superalloy in Laser Direct Metal Forming”, chinese journal of laser, 39 (2012), 1-8 [12]. “Handbook of new metallic Materials for Engineering applications”, Xian jiaotong university Press, 6 (2012). [13]. XuanTuoi Do, Dichen L, Anfeng Zhang, “Investigation on multi-track multi- layer epitaxial growth of columnar crystal in direct laser forming”, Journal of Laser Applications, 25 (2013), 12-19 [14]. “Standard Test Methods for Tension Testing of Metallic Materials”, ABSTRACT THE EFFECT OF PROCESSING THE PARAMETERS ON THE NICKEL BASE SUPPER-ALLOY DZ125L OF PRODUCT QUALITY REPAIRED BY LASER DIRECT METAL FORMING The effect of processing the parameters on the nickel-base supper-alloy DZ125L of product quality repaired by laser direct metal forming (LDMF) were studied by experiments. In order to enhance repairing quality of parts, the effect of process parameters on the quality of single-layer and solid parts were studied to find out reasonable parameters. The experiment results showed that the repairing of parts was broken at substrate material, which indicated the quality of binding force between substrate material and cladding material was relatively well. The parts formed by LDMF of test results showed that the tensile strength of LDMF part greater than the tensile strength of casting parts; because of microstructure of LDMF parts was epitaxial crystal, growth through cladding layers. Keywords: Laser Direct Metal Forming (LDMF), Ultimate tenacity strain, Nickel-base super alloy DZ125L, Cladding layer. Nhận bài ngày 10 tháng 12 năm 2015 Hoàn thiện ngày 27 tháng 06 năm 2016 Chấp nhận đăng ngày 17 tháng 08 năm 2016 Địa chỉ: Học viện Kỹ thuật quân sự- 236 Hoàng Quốc Việt, Bắc Từ liêm, Hà nội; *Email: doankhoactm@gmail.com.
File đính kèm:
anh_huong_cua_mot_so_tham_so_cong_nghe_den_chat_luong_chi_ti.pdf