Giáo trình Điện công nghiệp
TRANG BỊ ĐIỆN MÁY CẮT KIM LOẠI
Máy cắt kim loại được dùng để gia công các chi tiết kim loại bằng cách
cắt bớt các lớp kim loại thừa, để sau khi gia công có hình dáng gần đúng
yêu cầu (gia công thô) hoặc thoả mãn hoàn toàn yêu cầu đặt hàng với độ
chính xác nhất định về kích thước và độ bóng cần thiết của bề mặt gia công
(gia công tinh).
1.1. Các yêu cầu chính và những đặc điểm công nghệ đặc trưng của
trang bị điện và tự động hoá các máy cắt kim loại
Máy cắt kim loại theo số lượng và chủng loại chiếm vị trí hàng đầu trong
tất cả các máy công nghiệp.
1.1.1. Phân loại máy cắt kim loại
Máy cắt kim loại gồm nhiều chủng loại và rất đa dạng trong từng nhóm
máy, nhưng có thể phân loại chúng dựa trên các đặc điểm sau:
Phân loại máy cắt kim loại theo như hình 1.1
- Tùy thuộc vào quá trình công nghệ đặc trưng bởi phương pháp gia công,
dạng dao , đăc tính chuyển động v.v , các máy cắt được chia thành các
máy cơ bản: tiện, phay; bào, khoan – doa, mài và các nhóm máy khác như
gia công răng, ren vít v.v
- Theo đặc điểm của quá trình sản xuất, có thể chia thành các máy vạn
năng, chuyên dùng và đặc biệt. Máy vạn năng là các máy có thể thực hiện
được các phương pháp gia công khác nhau như tiện, khoan, gia công răng
v.v để gia công các chi tiết khác nhau về hình dạng và kích thước. Các
máy chuyên dùng là các máy để gian công các chi tiết có cùng hình dáng4
nhưng có kích thước khác nhau. Máy đặc biệt là các máy chỉ thực hiện gia
công các chi tiết có cùng hình dáng và kích thước.
- Theo kích thước và trọng lượng chi tiết gia công trên máy, có thể chia
maý cắt kim loại thành các máy bình thường (<10.000kg), các="" máy="" cỡ="">10.000kg),>
(<30.000kg), các="" máy="" cỡ="" nặng="">30.000kg),><100.000kg) và="" các="" máy="" rất="">100.000kg)>
(>100.000kG)
- Theo độ chính xác gia công, có thể chia thành máy có độ chính xác bình
thường, cao và rất cao.
Tóm tắt nội dung tài liệu: Giáo trình Điện công nghiệp
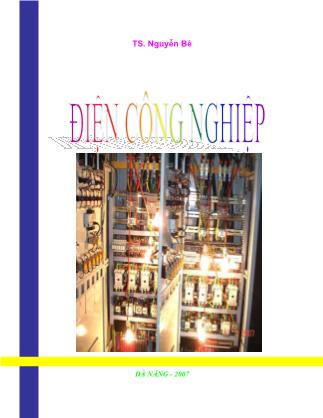
TS. NguyӉn Bê ĈÀ N̼NG - 2007 194 MỤC LỤC Chương 1: TRANG BỊ ĐIỆN CÁC MÁY CẮT GỌT KIM LOẠI 1.1. Các yêu cầu chính và những đặc điểm đặc trưng của trang bị điện và tự động hoá các máy cắt kim loại 3 1.2. Chọn hệ truyền động và tính chọn công suất động cơ truyền động của các máy cắt gọt kim loại 7 1.3. Điều chỉnh tốc độ động cơ trong các máy cắt gọt kim loại 13 1.4. Điều khiển chương trình số các máy cắt gọt kim loại 16 Chương 2: TRANG BỊ ĐIỆN NHÓM MÁY TIỆN 2.1. Đặc điểm công nghệ 24 2.2. Phụ tải của cơ cấu truyền động chính và ăn dao 25 2.4. Phương pháp chọn công suất động cơ truyền động chính của máy tiện 27 2.4. Những yêu cầu và đặc điểm đối với truyền động điện và trang bị điện của máy tiện 29 2.5. Một số sơ đồ điều khiển máy tiện điển hình 33 Chương 3: TRANG BỊ ĐIỆN MÁY BÀO GIƯỜNG 3.1 Đặc điểm công nghệ 45 3.2. Phụ tải và phương pháp xác đinh công suất động cơ truyền động chính 48 3.3. Các yêu cầu đối với hệ thống truyền động điện và trang bị điện của máy bào giường 54 3.4. Một số sơ đồ điều khiển máy bào giường điển hình 57 Chương4: TRANG BỊ ĐIỆN MÁY DOA 4.1. Đặc điểm làm việc, yêu cầu về truyền động điện và trang bị điện 73 4.2. Sơ đồ điều khiển máy doa ngang 2620 74 4.3. Sơ đồ truyền động máy doa toạ độ 2A450 79 Chương5: TRANG BỊ ĐIỆN MÁY MÀI 5.1. Đặc điểm công nghệ 83 5.2. Các đặc điểm về truyền động điện và trang bị điện máy mài 85 5.3. Sơ đồ điều khiển máy mài 3A161 85 Chương 6: TRANG BỊ ĐIỆN MÁY CÁN THÉP 6.1. Khái niệm chung về công nghệ cán thép 89 6.2. Các thông số cơ bản đặc trưng cho công nghệ cán thép 93 6.3. Tính mômen truyền động trục cán 97 6.4. Trang bị điện máy cán nóng quay thuận nghịch 99 195 Chương7: TRANG BỊ ĐIỆN CÁC MÁY NÂNG - VẬN CHUYỂN 7.1. Khái niệm chung 105 7.2. Phân loại các máy nâng - vận chuyển 105 7.3. Đặc điểm đặc trưng cho chế độ làm việc của hệ truyền động máy nâng - vận chuyển 108 7.4. Các hệ truyền động dùng trong các máy nâng - vận chuyển 109 Chương 8 TRANG BỊ ĐIỆN CẦU TRỤC 8.1. Khái niệm chung 111 8.2. Chế độ làm việc các động cơ truyền động các cơ cấu của cầu trục 112 8.3. Tính chọn công suất động cơ truyền động các cơ cấu chính của cầu trục 114 8.4. Các thiết bị điện chuyên dùng trong cầu trục 116 8.5. Một số sơ đồ khống chế cầu trục điển hình 124 Chương 9 TRANG BỊ ĐIỆN THANG MÁY 9.1. Khái niệm chung 132 9.2. Trang thiết bị của thang máy 134 9.3. Các thiết bị chuyên dùng của thang máy 136 9.4. Đặc tính và thông số của thang máy và máy nâng 138 9.5. Tính chọn công suất động cơ truyền động thang máy và máy nâng 139 9.6. Ảnh hưởng của tốc độ, gia tốc và độ giật đối với hệ truyền động thang máy 142 9.7. Dừng chính xác buồng thang 143 9.8. Các hệ truyền động dùng trong thang máy và máy nâng 146 9.9. Một số sơ đồ khống chế thang máy điển hình 147 9.10 Những thiết bị đặc biệt dùng trong các thang máy hiện đại 151 Chương 10 TRANG BỊ ĐIỆN MÁY XÚC 10.1 Khái niệm chung 156 10.2 Kết cấu và cấu tạo của máy xúc 158 10.3 Các yêu cầu cợ bản đối với hệ truyền động các cợ cấu của máy xúc 160 10.4 Biểu đồ phụ tải của các cơ cấu chính của máy xúc 162 10.5 Tính chọn công suất động cơ truyền động các cơ cấu chính của máy xúc 166 10.6 Một số sơ đồ khống chế máy xúc điển hình 173 Chương 11 TRANG BỊ ĐIỆN CÁC THIẾT BỊ VẬN TẢI LIÊN TỤC 11.1 Khái niệm chung 182 11.2 Cấu tạo và thông số kỹ thuật của một số thiết bị vận tải liên tục 182 11.3 Các yêu cầu chính đối với hệ chuyển động các thiết bị vận tải liên tục 187 196 11.4 Tính chọn công suất động cơ truyền động các thiết bị vận tải liên tục 187 11.5 Một số sơ đồ khống chế điển hình 190 Mục lục 194 Tài liệu tham khảo 197 197 TÀI LIỆU THAM KHẢO 1. Nguyễn Mạnh Tiến – Vũ Quang Hồi. Trang bị điện - Điện tử máy gia công kim loại. NXB Giáo dục 2003 2. Vũ Quang Hồi - Nguyễn Văn Chất - Nguyễn Thị Liên Anh. Trang bị điện - Điện tử máy công nghiệp dùng chung. NXB Giáo dục 2003 3. Nguyễn Văn Chất Giáo trình trang bị điện NXB Giáo dục 2004 4.Nguyễn Đắc Lộc – Tăng Huy Điều khiển số và công nghệ trên máy điều khiển số CNC. NXB KHKT – Hà Nội 2000 2 Các ký hiệu sử dụng để giải thích hoạt động sơ đồ: 1- A(x) = 1: phần tử A ở dòng thứ x có điện (nếu là cuộn dây) hoặc đóng lại (nếu là tiếp điểm) 2- A(x) = 0: phần tử A ở dòng thứ x mất điện (nếu là cuộn dây) hoặc mở ra (nếu là tiếp điểm) 3- A(x,y): phần tử A ở giữa hai dòng x và y hoặc hai điểm x,y. 4- A(đl): phần tử A trên mạch động lực Ví dụ: - ĐG(đl) = 1: tiếp điểm ĐG ở mạch động lực đóng (tr 33) - K2(đl) = 0 : tiếp điểm K2 ở mạch động lực mở (tr33). - Ấn nút M1(22) → LĐT(22) = 1, → LĐT(17) = 1, + LĐT(22,23) = 1: khi ấn nút M1 ở dòng 22 thì cuộn dây rơle LĐT ở dòng 22 có điện làm cho tiếp điểm LĐT ở dòng 17 đóng, đồng thời tiếp điểm LĐT giữa dòng 22 và 23 đóng.(tr36) - R8(15-13) = 1, + R8(1-3) = 1, → Rω(5-9): tiếp điểm R8 ở giữa điểm 15 và 13 đóng lại, đồng thời tiếp điểm R8 ở giữa điểm 1 và 3 cũng đóng làm cho điện trở Rω(5-9) (tr40) 3 Chương 1 TRANG BỊ ĐIỆN MÁY CẮT KIM LOẠI Máy cắt kim loại được dùng để gia công các chi tiết kim loại bằng cách cắt bớt các lớp kim loại thừa, để sau khi gia công có hình dáng gần đúng yêu cầu (gia công thô) hoặc thoả mãn hoàn toàn yêu cầu đặt hàng với độ chính xác nhất định về kích thước và độ bóng cần thiết của bề mặt gia công (gia công tinh). 1.1. Các yêu cầu chính và những đặc điểm công nghệ đặc trưng của trang bị điện và tự động hoá các máy cắt kim loại Máy cắt kim loại theo số lượng và chủng loại chiếm vị trí hàng đầu trong tất cả các máy công nghiệp. 1.1.1. Phân loại máy cắt kim loại Máy cắt kim loại gồm nhiều chủng loại và rất đa dạng trong từng nhóm máy, nhưng có thể phân loại chúng dựa trên các đặc điểm sau: Phân loại máy cắt kim loại theo như hình 1.1 MÁY CẮT KIM LOẠI QUÁ TRÌNH CÔNG NGHỆ QUÁ TRÌNH SẢN XUẤT TRỌNG LƯỢNG KÍCH THƯỚC ĐỘ CHÍNH XÁC GIA CÔNG TIỆN PHAY BÀO MÀI KHOAN THƯỜNG CHUYÊN DÙNG RẤT CAO THƯỜNG LỚN NẶNG RẤT NẶNG CAO VẠN NĂNG ĐẶC BIỆT Hình 1.1 Sơ đồ phân loại các máy cắt kim loại - Tùy thuộc vào quá trình công nghệ đặc trưng bởi phương pháp gia công, dạng dao , đăc tính chuyển động v.v, các máy cắt được chia thành các máy cơ bản: tiện, phay; bào, khoan – doa, mài và các nhóm máy khác như gia công răng, ren vít v.v - Theo đặc điểm của quá trình sản xuất, có thể chia thành các máy vạn năng, chuyên dùng và đặc biệt. Máy vạn năng là các máy có thể thực hiện được các phương pháp gia công khác nhau như tiện, khoan, gia công răng v.v để gia công các chi tiết khác nhau về hình dạng và kích thước. Các máy chuyên dùng là các máy để gian công các chi tiết có cùng hình dáng 4 nhưng có kích thước khác nhau. Máy đặc biệt là các máy chỉ thực hiện gia công các chi tiết có cùng hình dáng và kích thước. - Theo kích thước và trọng lượng chi tiết gia công trên máy, có thể chia maý cắt kim loại thành các máy bình thường (<10.000kG), các máy cỡ lớn (<30.000kG), các máy cỡ nặng (<100.000kG) và các máy rất nặng (>100.000kG) - Theo độ chính xác gia công, có thể chia thành máy có độ chính xác bình thường, cao và rất cao. 1.1.2 Các chuyển động và các dạng gia công điển hình trên MCKL Trên MCKL, có hai loại chuyển động chủ yếu: chuyển động cơ bản và chuyển động phụ Chuyển động cơ bản là chuyển động tương đối của dao cắt so với phôi để đảm bảo quá trình cắt gọt. Chuyển động này chia ra: chuyển đông chính và chuyển động ăn dao - Chuyển động chính (chuyển động làm việc) là chuyển động thực hiện quá trình cắt gọt kim loại bằng dao cắt. - Chuyển động ăn dao là các chuyển động xê dịch của dao hoặc phôi để tạo ra một lớp phôi mới. Chuyển động phụ là những chuyển động không liên quan trực tiếp đến quá trình cắt gọt, chúng cần thiết khi chuẩn bị gia công, nâng cao hiệu suất và chất lương gia công, hiệu chỉnh máy v.v Ví dụ như di chuyển nhanh bàn hoặc phôi trong máy tiện, nới siết xà trên trụ trong máy khoan cần, nâng hạ xà trong dao trong máy bào giường, bơm dầu của hệ thống bôi trơn, bơm nước làm mát v.v Các chuyển động chính, ăn dao có thể là chuyển động quay hoặc chuyển động tịnh tiến của dao hoặc phôi. Trên hình 1-2 biểu diễn các dạng gia công điển hình được thực hiện trên các MCKL. - Gia công trên máy tiện (hình 1-2a): n - tốc độ quay của chi tiết (chuyển động chính); v - vận tốc xê dịch của dao cắt vào chi tiết (chuyển động ăn dao). - Gia công trên máy khoan (hình 1-2b): n- tốc độ quay của mũi khoan (chuyển động chính); v- chuyển động tịnh tiến của mũi khoan vào chi tiết (chuyển động ăn dao). - Gia công trên máy phay (hình 1-2c): n- tốc độ quay của dao phay (chuyển động chính); v- chuyển động tịnh tiến của phôi (chuyển động ăn dao). - Gia công trên máy mài tròn ngoài (hình 1.2d): n- tốc độ quay của đá mài (chuyển động chính); v- chuyển động tịnh tiến của đá mài vào chi tiết (chuyển động ăn dao). 5 - Gia công trên máy bào giường (hình 1-2e): vt, vn- chuyển động qua lại của bàn (chuyển động chính), chuyển động di chuyển của dao theo chiều ngang của bàn (chuyển động ăn dao). Hình 1-2 Các dạng gia công kim loại trên các máy cắt kim loại a) Tiện b) Khoan c) Phay d) Mài e) Bào 1.1.3. Các thiết bị điện chuyên dụng dùng trong các máy cắt gọt kim loại. 1. Nam châm điện: thường dùng để điều khiển các van thuỷ lực, van khí nén, điều khiển đóng cắt ly hợp ma sát, ly hợp điện từ và dùng để hãm động cơ điện. Nam châm điện dùng trong các máy cắt gọt kim loại là nam châm điện xoay chiều có lực hút từ 10N đến 80N với hành trình của phần ứng (lõi nam châm) từ 5 đến 15mm. Hình 1-3 Cấu tạo nam châm điện 1.Mạch từ; 2. Cuộn dây của nam châm; 3. Thanh dẫn hướng; 4. Phần ứng lõi nam châm; 5. Vòng ngắn mạch δ F Hình 1-4 Đặc tính cơ của nam châm điện 6 Nguyên lý làm việc của nam châm điện như sau: khi cấp nguồn cho cuộn dây 2 sẽ xuất hiện từ thông khép kín theo mạch từ 1. Sự tác dụng tương hỗ giữa từ thông và dòng điện trong cuộn dây sẽ sinh ra một lực kéo hút phần ứng 4 vào sâu trong nam châm điện. Thanh dẫn hướng 3 có chức năng giảm hệ số ma sát giữa phần ứng và mạch từ, đảm bảo cho phần ứng không bị hút lệch. Đặc tính quan trọng nhất của nam châm điện là đặc tính cơ (đặc tính lực kéo). Nó biểu diễm sự phụ thuộc giữa lực kéo sinh ra của nam châm điện và hành trình của phần ứng F = f(δ). Đặc tính đó được biểu diễn trên hình 1-4. 2. Bàn từ: dùng để cặp chi tiết gian công trên các máy mài mặt phẳng (hình 1.5). Cấu tạo của bàn từ gồm: hộp sắt non 1 với các cực lõi 2, cuộn dây 3, bàn từ 4 có lót các tấm mỏng 5 bằng vật liệu không nhiễm từ. Khi cấp nguồn 1 chiều cho cuộn dây, bàn sẽ trở thành cam châm với nhiều cặp cực: cực bắc N và cực nam S Bàn từ được cấp nguồn 1 chiều (trị số điện áp có thể là 24, 48, 110 và 220V với công suất từ 100 ÷ 3000W) từ các bộ chỉnh lưu dùng điột bán dẫn. Sau khi gia công xong, muốn lấy chi tiết ra khỏi bàn phải khử từ dư của bàn từ, thực hiện bằng cách đảo cực tính nguồn cấp cho bàn từ. 3.Khớp ly hợp điện từ: dùng để điều chỉnh tốc độ quay, điều khiển động cơ truyền động: khởi động, đảo chiều, điều chỉnh tốc độ và hãm. Khớp ly hợp điện từ là khâu trung gian nối động cơ truyền động với máy công tác cho phép thay đổi tốc độ máy công tác khi tốc độ động cơ không đổi, thường dùng trong hệ truyền động ăn dao của các máy cắt kim loại. Đối với hệ truyền động ăn dao của các máy cắt gọt kim loại, yêu cầu duy trì mômen không đổi trong toàn dải điều chỉnh tốc độ. Về cấu tạo và nguyên lý hoạt động, người ta phân biệt hai loại khớp ly hợp điện từ: khớp ly hợp điện từ ma sát và khớp ly hợp điện từ trượt. H1-6. Khớp ly hợp điện từ ma sát a) Khớp ly hợp điện từ ma sát, cấu tạo như trên hình 1-6 gồm: thân khớp ly hợp 3, cuộn dây 4, các đĩa ma sát 8 và 9, đĩa ép 10 và giá kẹp 11. Tất cả các phần tử kể trên được gá lắp trên bạc lót 2 làm từ vật liệu không nhiễm từ và bạc lót được lắp trên trục vào 1 (trục gắn với trục của động cơ truyền đông). Nguồn cấp cho cuộn dây của ly hợp được cấp 7 như sau: cực âm của nguồn được nối với thân của ly hợp 3, cực dương của nguồn được cấp qua chổi than 7 và vành trượt tiếp điện 6, còn 5 là vành cách điện giữa cực dương của nguồn và thân ly hợp. Nguyên lý làm việc của khớp ly hợp ma sát như sau: khi cuộn dây 4 được cấp nguồn, sẽ tạo ra một từ trường khép kín qua các đĩa ma sát. Từ trường đó tạo ra một lực hút kéo đĩa ma sát 9 về thân ly hợp 3. Các đĩa ma sát 8 và 9 ăn khớp nhau. Đĩa ma sát 9 nối với trục 1 (trục động cơ truyền động), còn đĩa ma sát 8 nối với trục 12 (trục máy công tác). b) Khớp ly hợp điện từ trượt. Cấu tạo của nó được biểu diễn trên hình 1-7. Hình 1-7 Khớp ly hợp điện từ trượt Cấu tạo của nó gồm hai phần chính: Phần ứng 1 được gắn với trục của động cơ truyền động 2 (trục chủ động) và phần cảm 3 của cuộn dây kích thích 4 được nối với trục của máy công tác (trục thụ động). Nguồn cấp cho cuộn dây kích thích 4 là nguồn 1 chiều tiếp điện bằng chổi than 5 và vành trượt 7 lắp trên trục 6. Nguyên lý làm việc của khớp ly hợp điện từ trượt như sau: Khi cho động cơ truyền động quay và cấp nguồn cho cuộn kích thích, trong phần ứng sẽ xuất hiện sức điện động cảm ứng, sức điện động đó sẽ sinh ra dòng điện xoáy (dòng Fucô). Sự tác dụng tương hỗ giữa dòng điện trong phần ứng và từ thông của phần cảm sẽ sinh ra mômen điện từ làm cho phần cảm quay theo cùng chiều với phần ứng. Hệ số trượt của khớp ly hợp phụ thuộc vào trị số dòng điện trong cuộn kích thích và mômen của phụ tải. Bởi vậy, với mômen tải không đổi, khi ta thay đổi dòng điện trong cuộn dây kích thích sẽ thay đổi được tốc độ của máy công tác. 1.2 Chọn hệ truyền động và tính chọn công suất động cơ truyền động của máy cắt gọt kim loại 1.2.1. Các hệ truyền động thường dùng trong máy cắt gọt kim loại 1. Đối với chuyển động chính của máy tiện, khoan, doa, máy phay với tần số đóng cắt điện không lớn, phạm vi điều chỉnh tốc độ không rộng 8 thường dùng hệ truyền động với động cơ không đồng bộ rôto lồng sóc. Điều chỉnh tốc độ trong các máy đó thực hiện bằng phương pháp cơ khí dùng hộp tốc độ. 2. Đối với một số máy khác như: máy tiện Rơvonve, máy doa ngang, máy sọc răng yêu cầu phạm vi điều chỉnh tốc độ rộng hơn, hệ truyền động trục chính dùng hệ truyền động với động cơ không đồng bộ hai hoặc ba cấp tốc độ. Quá trình thay đổi tốc độ thực hiện bằng cách thay đổi sơ đồ đấu dây quấn stato của động cơ để thay đổi số đôi cực với công suất duy trì không đổi. 3. Đối với một số máy như: máy bào giường, máy mài tròn, máy doa toạ độ và hệ truyền động ăn dao của một số máy yêu cầu: - Phạm vi điều chỉnh tốc độ rộng. - Đảo chiều quay liên tục. - Tần số đóng cắt điện lớn. Thường dùng hệ truyền động một chiều (hệ máy phát - động cơ điện một chiều F - Đ, hệ máy điện khuếch đại - động cơ điện 1 chiều MĐKĐ - Đ, hệ khuếch đại từ động cơ điện 1 chiều KĐT - Đ và bộ biến đổi tiristo - động cơ điện một chiều T-Đ) và hệ truyền động xoay chiều dùng bộ biến tần. 1.2.2 Các tham số đặc trưng cho ch ... mӝt mҥch vòng khép kín 2, trên nó có gá lҳp tҩt cҧ các gàu xúc 5, vҳt qua bánh hoa cúc hoһc tang quay 1 Phҫn chuyӇn ÿӝng cӫa băng gàu ÿѭӧc che kín bҵng hӝp che bên ngoài 3 và thành bên trong cӫa hӝp ÿұy có cѫ cҩu dүn hѭӟng 4. Ĉӕi vӟi băng gàu tӕc ÿӝ cao vӟi tӕc ÿӝ di chuyӇn v = (0,8 ÷ 3,5)m/s, năng suҩt tӟi 80m3 và chiӅu cao nâng tӟi 40m, băng gá các gàu xúc thѭӡng dùng băng cao su có bӕ vҧi bên trong. Ĉӕi vӟi băng gàu năng suҩt cao tӟi 400m3/h, tӕc ÿӝ di chuyӇn chұm dѭӟi 1,5m/s thѭӡng dùng băng có ÿӝ cӭng cao hѫn ÿӇ gá các gàu xúc. Tang chӫ ÿӝng (hoһc bánh xe hoa cúc) 1 ÿѭӧc nӕi vӟi ÿӝng cѫ truyӅn ÿӝng 10 qua 185 hӝp tӕc ÿӝ 9 (hình 11-2b). HӋ thӕng truyӅn ÿӝng cӫa băng gàu lҳp ӣ vӏ trí trên cùng cӫa băng gàu, trong mӝt sӕ trѭӡng hӧp có dùng phanh hãm ÿiӋn tӯ ÿӇ hãm ÿӝng cѫ khi dӯng. Cѫ cҩu tҥo sӭc căng cho băng kéo 7 thѭӡng lҳp ӣ tang thө ÿӝng phía dѭӟi cӫa băng gàu. Vұt liӋu cҫn vұn chuyӇn ÿѭӧc ÿә vào các gàu tӯ ӕng nhұn 6 và ÿә tҧi ӣ ӕng 8. Năng suҩt cӫa băng gàu ÿѭӧc tính theo biӇu thӭc sau: 3600... v l iQ g J< [m3] (11-5) Trong ÿó: i - thӇ tích cӫa mӛi gàu xúc, m3; h - hӋ sӕ lҩp ÿҫy cӫa gàu, có trӏ sӕ tӯ 0,4 ÿӃn 0,8 tuǤ thuӝc vào loҥi vұt liӋu cҫn vұn chuyӇn; Ȗ - khӕi lѭӧng thӇ tích cӫa vұt liӋu, tҩn/m3; lg - cӵ ly gián cách giӳa các gàu, m; v - tӕc ÿӝ di chuyӇn, m/s. 3.Ĉ˱ͥng cáp treo Ĉѭӡng cáp treo thѭӡng ÿѭӧc chӃ tҥo theo hai kiӇu: ÿѭӡng cáp treo có mӝt ÿѭӡng cáp và ÿѭӡng cáp treo có hai ÿѭӡng cáp kéo nӕi thành mӝt ÿѭӡng vòng kép kín (hình 11-3) Hình 11-3. Ĉѭӡng cáp treo có hai ÿѭӡng cáp kéo Trong ÿó mӝt ÿѭӡng là vұn chuyӇn hàng trên các toa, còn ÿѭӡng thӭ hai là ÿѭӡng hӗi vӅ cӫa các toa hàng (có hàng hoһc không có hàng). Các bӝ phұn chính cӫa ÿѭӡng cáp treo gӗm có: ga nhұn hàng 7 và ga trҧ hàng 2, giӳa hai ga ÿó là hai ÿѭӡng cáp nӕi lҥi vӟi nhau: ÿѭӡng cáp mang 4 và ÿѭӡng cáp kéo 3. ĈӇ tҥo ra lӵc căng cӫa cáp, tҥi nhà ga trҧ hàng 2 có lҳp ÿһt cѫ cҩu kéo căng cáp 1. Ӣ khoҧng giӳa hai nhà ga có các giá ÿӥ cáp mang trung gian 5. Cáp kéo 3 ÿѭӧc thiӃt kӃ thành mӝt mҥch kín liên kӃt vӟi cѫ cҩu truyӅn ÿӝng 186 8. Ĉӝng cѫ truyӅn ÿӝng cáp kéo 9 ÿѭӧc lҳp ÿһt tҥi nhà ga nhұn hàng. Các toa hàng 6 di chuyӇn theo ÿѭӡng cáp mang 4. Năng suҩt cӫa ÿѭӡng cáp treo ÿҥt tӟi 400 tҩn/h, ÿӝ dài cung ÿѭӡng giӳa hai nhà ga có thӇ ÿҥt tӟi hàng trăm km. Năng suҩt cӫa ÿѭӡng cáp ÿѭӧc tính theo biӇu thӭc: t GQ .3600 [tҩn/h] (11-6) Trong ÿó: t - thӡi gian gián cách hai toa hàng, s; G- trӑng tҧi hӳu ích cӫa mӝt toa hàng, tҩn. 4.Thang chuy͉n Thang chuyӅn là mӝt loҥi cҫu thang vӟi các bұc chuyӇn ÿӝng dùng ÿӇ vұn chuyӇn hành khách trong các nhà ga cӫa tàu ÿiӋn ngҫm, các toà thӏ chính, các siêu thӏ, vӟi tӕc ÿӝ di chuyӇn tӯ 0,4 ÿӃn 1m/s. KӃt cҩu cӫa mӝt thang chuyӅn ÿѭӧc giӟi thiӋu trên hình 11-4 Hình 11-4 KӃt cҩu cӫa thang chuyӅn Ĉӝng cѫ truyӅn ÿӝng 6, lҳp ӣ phҫn trên cӫa thang chuyӅn truyӅn lӵc cho trөc chӫ ÿӝng 5 qua cѫ cҩu truyӅn lӵc - hӝp tӕc ÿӝ. Trөc chӫ ÿӝng 5 có hai bánh xe hoa cúc và dҧi băng vòng có các bұc thang 4 khép kín vӟi bánh hoa cúc 2 lҳp ӣ phҫn dѭӟi cӫa thang chuyӅn. Ӣ trөc thө ÿӝng 2 có lҳp cѫ cҩu tҥo lӵc căng cho dҧi băng vòng. ĈӇ ÿҧm bҧo an toàn cho hành khách, hai bên thành cӫa thang chuyӅn có tay vӏn 3 di chuyӇn ÿӗng tӕc vӟi các bұc thang cӫa thang chuyӅn. Năng suҩt cӫa thang chuyӅn ÿѭӧc tính theo biӇu thӭc: 3600...1 Uvm m Q k b [ngѭӡi/h] (11-7) Trong ÿó: m 1 - sӕ bұc thang trên mӝt ÿѫn vӏ mét dài cӫa thang chuyӅn; 187 mk- sӕ lѭӧng khách trên mӝt bұc thang; ȡ - hӋ sӕ lҩp ÿҫy khách cӫa thang chuyӅn; v - tӕc ÿӝ di chuyӇn cӫa thang chuyӅn, m/s. HӋ sӕ lҩp ÿҫy ȡ có thӇ tính theo công thӭc kinh nghiӋm: ȡ = 1,2 – 0,6v = 0,6(2-v) 11-3. Các yêu c̯u chính ÿ͙i vͣi h͏ chuy͋n ÿ͡ng các thi͇t b͓ v̵n t̫i liên tͭc ChӃ ÿӝ làm viӋc cӫa các thiӃt bӏ vұn tҧi liên tөc là chӃ ÿӝ dài hҥn vӟi phө tҧi hҫu nhѭ không ÿәi. Theo yêu cҫu công nghӋ cӫa hҫu hӃt các thiӃt bӏ vұn tҧi liên tөc không yêu cҫu ÿiӅu chӍnh tӕc ÿô. Trong mӝt sӕ trѭӡng hӧp,cҫn tăng nhӏp ÿӝ làm viӋc trong các phân xѭӣng sҧn xuҩt theo dây chuyӅn, các băng chuyӅn phөc vө trong dây chuyӅn sҧn xuҩt yêu cҫu phҥm vi ÿiӅu chӍnh tӕc ÿӝ là D = 2:1. Ĉӝng cѫ truyӅn ÿӝng và các thiӃt bӏ ÿiӅu khiӇn hӋ truyӅn ÿӝng phҧi chӑn làm viӋc ӣ chӃ ÿӝ dài hҥn. HӋ truyӅn ÿӝng các thiӃt bӏ vұn tҧi liên tөc là hӋ truyӅn ÿӝng xoay chiӅu vӟi ÿӝng cѫ không ÿӗng bӝ rôto lӗng sóc và rôto dây quҩn. Phҫn lӟn các thiӃt bӏ vұn tҧi liên tөc lҳp ÿһt ngoài trӡi, nѫi có môi trѭӡng làm viӋc khҳc nghiӋt, nên ÿӇ ÿҧm bҧo khӣi ÿӝng ÿѭӧc ÿҫy tҧi, các ÿӝng cѫ truyӅn ÿӝng phҧi có mômen mӣ máy lӟn. Mômen khӣi ÿӝng các thiӃt bӏ vұn tҧi liên tөc yêu cҫu tӟi trӏ sӕ Mkÿ = (1,6 ÷ 1,8)Mÿm. Bӣi vұy thѭӡng chӑn loҥi ÿӝng cѫ có hӋ sӕ trѭӧt lӟn, rãnh stato sâu ÿӇ có mômen mӣ máy lӟn. Nguӗn cҩp cho ÿӝng cѫ truyӅn ÿӝng phҧi có dung lѭӧng ÿӫ lӟn, ÿһc biӋt là ÿӕi vӟi nhӳng ÿӝng cѫ truyӅn ÿӝng có công suҩt lӟn hѫn 30kW. Ĉӕi vӟi băng tҧi, băng gàu di ÿӝng, khi cҩp ÿiӋn tӯ nguӗn ÿӃn ÿӝng cѫ, cҫn kiӇm tra tәn thҩt ÿiӋn áp trên ÿѭӡng cáp cҩp ÿiӋn, ÿӇ ÿiӋn áp ӣ cuӕi ÿѭӡng dây không ÿѭӧc thҩp hѫn 0,85Uÿm. Khi tính chӑn ÿӝng cѫ cҫn phҧi tiӃn hành kiӇm tra trӏ sӕ gia tӕc cӫa hӋ truyӅn ÿӝng khi tăng tӕc và khi hãm dӯng. Ĉӕi vӟi hӋ truyӅn ÿӝng ÿѭӡng cáp treo và thang chuyӅn, quá trình mӣ máy và hãm dӯng phҧi xҧy ra êm, trӏ sӕ gia tӕc không ÿѭӧc vѭӧt quá 0,7m/s2. 11-4. Tính ch͕n công sṷt ÿ͡ng c˯ truy͉n ÿ͡ng các thi͇t b͓ v̵n t̫i liên tͭc 1. Băng t̫i: khi tính chӑn công suҩt ÿӝng cѫ truyӅn ÿӝng băng tҧi cҫn tính ÿӃn các thành phҫn công suҩt sau: a) Công suҩt ÿӇ dӏch chuyӇn vұt liӋu P1. b) Công suҩt ÿӇ khҳc phөc tәn hao do ma sát trong các ә ÿӥ cӫa các con lăn, ma sát khi băng di chuyӇn P2. c) Công suҩt cҫn ÿӇ nâng vұt liӋu P3 (nӃu băng tҧi di chuyӇn theo mһt phҷng nghiêng). 188 Gӑi: įb - khӕi lѭӧng mét băng tҧi, kg/m; į - khӕi lѭӧng vұt liӋu trên 1m băng tҧi, kg/m. Lӵc cҫn thiӃt ÿӇ dӏch chuyӇn vұt liӋu bҵng: F1 = Lįcosȕk1.Ȗ = L’įk1g [N] (11-8) Trong ÿó: L - chiӅu dài cӫa băng tҧi, m; k1- hӋ sӕ có tính ÿӃn lӵc cҧn khi dӏch ȕ - góc nghiêng cӫa băng tҧi; g - gia chuyӇn vұt liӋu, thѭӡng lҩy k1 = 0,05. tӕc trӑng trѭӡng, m/s2. uyӇn v ó: v là tӕc ÿӝ di chuyӇn c ҧi có thӇ tính theo n Công suҩt cҫn thiӃt ÿӇ dӏch ch ұt liӋu: P1 = F1.v = L’įk1v.g (11-9) Trong ÿ ӫa băng tҧi, m/s. Khӕi lѭӧng cӫa vұt liӋu trên mӝt mét dài cӫa băng t ăng suҩt cӫa băng tҧi: vQ 3 G 6, ҫn dӏch chuy Hình 11-5 Sѫ ÿӗ tính toán ÿӇ xác ÿӏnh công suҩt truyӅn ÿӝng băng tҧiKhi ÿó công suҩt c ÿӇ Ӈn vұt liӋu bҵng: gQL v gvQLP 05,0.1 '0139,06,3 .. (11-10) ӵc cҧn trong các ә ÿӥ các con lăn và ÿӝng trên các con lăn ÿѭӧc tính theo biӇu th ông tҧi. (11-12) . d L lӵc cҧn do ma sát khi băng chuyӇn ӭc: F2 = L2įbcosȕk2g = 2L’.įb.k2.g (11-11) Trong ÿó: k2 - hӋ sӕ có tính ÿӃn lӵc cҧn khi kh Công suҩt cҫn thiӃt ÿӇ khҳc phөc tәn hao công suҩt do lӵc cҧn ma sát bҵng: P2 = F2.v = 2L’įb.k2.g Lӵc cҫn thiӃt ÿӇ nâng vұt liӋu ÿѭӧc tính bҵng: F3 = ± Lįsinȕg = ± į.H.g (11-13) Trong ÿó: H - là chiӅu cao nâng cӫa băng tҧi, m Dҩu (+) trong biӇu thӭc tѭѫng ӭng khi băng tҧi vұn chuyӇn vұt liӋu ÿi lên; ҩu (-) khi vұn chuyӇn vұt liӋu ÿi xuӕng. Công suҩt cҫn ÿӇ nâng vұt liӋu bҵng: P = ± F .v = ± į.H.g QHg v QHvgr3 3 278,0r (11-14) ҵng: c 1 2 3 įbk2 ± 0,278QH) 6,3 Công suҩt cҧn tƭnh cӫa băng tҧi b P = k(P + P + P ) = kg(0,0139QL’ + 2L’ (11-15) 189 Hình 11-6. Sѫ ÿӗ tính toán ÿӇ xác ÿӏnh công suҩt ÿӝng cѫ truyӅn H ҩt phө do lӵc ma sát trong các con lă Trong ÿó: k - hӋ sӕ có tính ÿӃn tәn th n dүn hѭӟng k= (1 ÷ 1,25). Công suҩt cӫa ÿӝng cѫ truyӅn ÿӝng băng tҧi ÿѭӧc tính theo biӇu thӭc: ÿӝng băng gàu Kdc kP . (11cP -16) rong ÿó: k - hӋ sӕ d trӳ (k = 1,2 ÷ 1,25); Ș - hiӋu su t cӫa hӋ truyӅn ÿӝng. ông suҩt ÿ rên lӵc cҧn và lӵc căng cӫa các n tang th ng ÿó: ng (1000 ÷ 2000)N 1,07 , k2 = (4 ÷ 5)kgm/kg; ӫa băng (tҥi ÿiӇm 4) ÿѭ [N] (11-17) T ӵ ҩ 2. Băng gàu C ÿӝng cѫ truyӅn ÿӝng băng gàu ѭӧc tính dӵa t hánh băng kéo các gàu xúc ( hình 11-6) Lӵc kéo cӫa nhánh kéo lên cӫa băng là tәng lӵc kéo tҥi các ÿiӇm 1,2,3 và lӵc cҧn trên ө ÿӝng và lӵc cҧn khi di chuyӇn các gàu xúc. Fkl= k1F1 +k2įg + (į + į0)H.g [N] (11-17) Tro F1 - lӵc kéo tҥi ÿiӇm 1 thѭӡng lҩy bҵ k1 - hӋ sӕ có tính ÿӃn lӵc ma sát trên tang quay, k1 = 1,05 ÷ į - khӕi lѭӧng vұt liӋu trên mӝt mét dài cӫa băng, kg; k2 - hӋ sӕ có tính ÿӃn lӵc cҫn vұn chuyӇn 1 kg vұt liӋu į0- khӕi lѭӧng 1 mét băng. Lӵc kéo cӫa nhánh kéo xuӕng c ӧc tính bҵng: Fkx = F1 + į0Hg Tәng lӵc kéo ÿһt lên tang chӫ ÿӝng cӫa băng gàu bҵng: 95,0 F ( kxkl FF [N] (11-18) C ă P ông suҩt cҧn tƭnh cӫa b ng gàu bҵng: c = F.v u bҵng:Công suҩt ÿӝng cѫ truyӅn ÿӝng băng gà KF kP ð cP (11-19) rong ÿó: k - hӋ sӕ dT ӵ trӳ, k = (1,2 ÷ 1,25) 11-5. M͡t s͙ s˯ ÿ͛ kh͙ng ch͇ ÿi͋n hình 190 1. S˯ ÿ͛ kh͙ng ch͇ h͏ th͙ng băng t̫i mӝt nguyên lý chung khi thiӃt kӃ sѫ tín hiӋu hoá. g nút bҩm và công tҳc tѫ thӕng băng tҧi. Khi thiӃt kӃ hӋ thӕng ÿiӅu k thӕng băng tҧi ÿѭӧc trình bày trên hình 11-7. ĺ băng tҧ T6 và ÿә vào thùng chӭa T2. ÷ ĈB6 hiӇn thӏ trҥng thái làm viӋc cӫa sáu băng tҧi tѭѫng ӭng. ӏ trҥng thái làm viӋc cӫa các van, cӫa hai th báo Ĉ g nhҩp nháy, còn khi các băng tҧi ÿã khӣi ÿ cho hӋ thӕng ÿèn chiӃu sáng (hình 11-7c). ĈiӅu khiӇn băng tҧi và băng gàu có cùng ÿӗ ÿiӅu khiӇn, các mҥch liên ÿӝng và Khi mӝt băng tҧi hoһc băng gàu làm viӋc ÿӝc lұp, không liên quan vӟi các thiӃt bӏ khác, ÿiӅu khiӇn hӋ truyӅn ÿӝng bҵng hӋ thӕn lҳp trong tӫ ÿiӋn cӫa băng tҧi. Khi có nhiӅu tuyӃn vân tҧi vұt liӋu, trong ÿó có nhiӅu máy công tác, sӵ liên hӋ giӳa các máy công tác ÿó là hӋ hiӇn hӋ thӕng băng tҧi trên phҧi tuân thӫ các nguyên tҳc sau: - Thӭ tӵ khӣi ÿӝng các ÿӝng cѫ truyӅn ÿӝng băng tҧi ngѭӧc chiӅu vӟi dòng vұn chuyӇn vұt liӋu. - Dùng băng tҧi bҩt kǤ nào ÿó chӍ ÿѭӧc phép khi băng tҧi trѭӟc nó ÿã dӯng. Sѫ ÿӗ ÿiӅu khiӇn hӋ HӋ thӕng băng tҧi có ba tuyӃn vұn chuyӇn vұt liӋu: + TuyӃn 1: băng tҧi BT1 ĺ thùng phân phӕi TP1 ĺ băng tҧi BT2 i BT3 và ÿә vào thùng chӭa T1. + TuyӃn 2: băng tҧi BT1 ĺ thùng phân phӕi TP1 ĺ băng tҧi BT4 ĺ thùng phân phӕi TP2 ĺ băng tҧi B + TuyӃn 3: băng tҧi BT1 ĺ thùng phân phӕi TP1 ĺ băng tҧi BT4 ĺ thùng phân phӕi TP2 ĺ băng tҧi BT5 và ÿә vào thùng chӭa T3. Chӑn tuyӃn vұn chuyӇn vұt liӋu bҵng ba bӝ chuyӇn mҥch CM1, CM2, CM3. HӋ thӕng ÿèn báo bao gӗm: + ĈB1 + Ĉèn báo ĈV1 ÷ ĈV4 hiӇn th ùng phân phӕi TP1 và TP2. Khi vұn chuyӇn vұt liӋu theo tuyӃn 1, ÿèn V1 sáng, còn khi vұn chuyӇn vұt liӋu theo tuyӃn 2, ÿèn báo ĈV2, ĈV4 sáng, còn khi vұn chuyӇn theo tuyӃn 3, ÿèn báo ĈV2 và ĈV3 sáng. HӋ thӕng ÿèn báo có hai chӃ ÿӝ hiӇn thӏ: - ĈӇ kiӇm tra tuyӃn vұn chuyӇn ÿã chӑn, các ÿèn báo ÿѭӧc ÿҩu vào nguӗn Ng1 (hình 11-7c), ÿèn báo sán ӝng xong, các ÿèn báo ÿѭӧc ÿҩu vào nguӗn Ng2 (hình 11-7c), các ÿèn báo sáng әn ÿӏnh. + Xét nguyên lý làm viӋc cӫa hӋ thӕng băng tҧi khi cҫn vұn chuyӇn vұt liӋu theo tuyӃn 3. - Ĉóng công tҳc chuyӇn mҥch CTO (hình 11-7b), rѫle trung gian RĈB(2) =1, cҩp nguӗn 191 b) c) 3 4 RHV1CM1 CM2 CM3 8 6 RK1 10 RTh 12 14RTh RK1 RK3 16 D M RK2 RK4 RK4 20 RK1 RK2 RK3 RHV1 RTr1 26 30RTr2RHV1 RTr4 34 RTr5 38RHV3 RTr6 40 K1 42CT1RKT4 NCV2 RKT2 NCV1 60RHV2 RHV3 64RHV3 1 1CT0 2RċB RHV2 RHV3 RK2 RK2 RK2 18 RHV2 RHV3 24 28 RK4 C 22 32RTr3 RHV2 RHV3 36 RHV2 RTr1 44 46CT2RKT3 NCV1 RTr2 48CT3 RTr3 K2 K3 RN3 RN2 RN1 K4 50CT4RKT5 NCV3 RKT6 NCV4 RTr4 52 54CT5NCV3 RTr5 RTr6 K5 RN5 RN4 56CT6NCV4 K6 RN6 58 RHV1 NCV1 66 RHV4 NCV2 NCV3 NCV4 62 TP1 BT1 BT2 BT3 BT4 S1 S3 S2 BT5 BT6 TP2 ĈB1 ĈB2 ĈB3 ĈB4 ĈB5 ĈB6 RHV1 RHV2 RHV3 RTr1 RDB Ĉ1 RTr1 K1 RHV1 RTr2 Ĉ2 RTr2 K2 RHV1 RTr3 Ĉ3 RTr3 K3 RHV2 RHV3 RTr4 Ĉ4 RTr4 K4 RHV3 RTr5 Ĉ5 RTr5 K5 RHV2 RTr6 Ĉ6 RTr6 K6 RHV1 NCV1 ĈV1 NCV1 RHV2 NCV2 ĈV2 RHV3 NCV2 RHV3 NCV3 ĈV3 NCV3 RHV2 NCV4 ĈV4 NCV4 0 5 7 9 11 13 15 17 19 21 23 25 27 29 31 33 35 37 39 41 43 45 47 49 V1 V2 V3 V4 Ng1 Ng2 1 23 a) Hình 11-8 Sѫ ÿӗ ÿiӅu khiӇn hӋ thӕng băng tҧi a)Sѫ ÿӗ công nghӋ b) sѫ ÿӗ nguyên lý mҥch ÿiӅu khiӇn c) HӋ thӕng ÿèn báo 192 - Quay chuyӇn mҥch CM3 sang bên phҧi, rѫle hѭӟng vұn chuyӇn RHV3(8) =1. TiӃp ÿiӇm cӫa nó sӁ ÿóng ÿӇ chuҭn bӏ cҩp nguӗn cho các rѫle trung gian và các cuӝn nam châm sau: ̅ RHV3(26) =1, cҩp nguӗn cho các rѫle RTr1. ̅ RHV3(36) =1, chuҭn bӏ cҩp nguӗn cho rѫle RTr4. ̅ RHV3(38) =1, chuҭn bӏ cҩp nguӗn cho rѫle RTr5. ̅ RHV3(62) =1, chuҭn bӏ cҩp nguӗn cho cuӝn dây nam châm NCV2. ̅ RHV3(64) =1, chuҭn bӏ cҩp nguӗn cho cuӝn dây nam châm NCV3. ̅ RHV3 cҩp cho các ÿèn báo ĈB1(7), ĈB2(39), ĈB3(43), ĈB4(17), ĈB5(25) vào nguӗn Ng2. Các ÿèn báo sӁ sáng nhҩp nháy cho phép chúng ta kiӇm tra tính ÿúng ÿҳn cӫa tuyӃn ÿѭӡng vұn chuyӇn vұt liӋu ÿã chӑn. ĈӇ khӣi ÿӝng các ÿӝng cѫ truyӅn băng tҧi, ҩn nút mӣ máy M, ĺ RK1(10) =1,ĺ RK1(16) =1 [duy trì], RK1(20) =1ĺ RK4(20) =1 ĺ RK4(22) =1 ĺ chuông ÿiӋn Ch(22) kêu báo hiӋu hӋ thӕng băng tҧi chuҭn bӏ làm viӋc. Sau thӡi gian chӍnh ÿӏnh (5 ÷ 10)s, tiӃp ÿiӇm thѭӡng mӣ ÿóng chұm RTh(14) =1, ĺ RK2(14) =1 ĺ RK2(16) = 1, RK2(12) = 0 ĺ cҳt nguӗn cҩp cho RTh(12), ĺ RK2(20) = 0 ĺ RK4(20) =0 ĺ cҳt nguӗn chuông Ch(22); RK2(18) = 1ĺ RK3(18) = 1 ĺ RK3(1-3) ÿóng nguӗn cho dòng 26 ÷ 70. Khi RK3(1-3) =1ĺ K5(54) = 1ĺ BT5 khӣi ÿӝng. Khi tӕc ÿӝ ÿҥt ÿѭӧc tӕc ÿӝ ÿӏnh mӭc, RKT5(50) = 1ĺ K4((52) =1ĺ BT4 khӣi ÿӝng. Khi tӕc ÿӝ băng tҧi 4 ÿҥt tӕc ÿӝ ÿӏnh mӭc, RKT(42) = 1ĺ K1(42) =1 ĺ BT1 khӣi ÿӝng, quá trình khӣi ÿӝng các ÿӝng cѫ truyӅn ÿӝng băng tҧi kӃt thúc. Khi muӕn dӯng hӋ thӕng băng tҧi, ҩn nút dӯng máy “D”. Khi các băng tҧi khӣi ÿӝng xong, các tiӃp ÿiӇm cӫa các công tҳc tѫ K1 ÷ K6 (hình 11-8c) ÿóng lҫn lѭӧt các ÿèn báo ĈB1 ÷ ĈB6 vào nguӗn cҩp Ng1, ÿèn báo sáng әn ÿӏnh báo hiӋu quá trình khӣi ÿӝng các băng tҧi kӃt thúc. Công tҳc CT1 ÷ CT6 dùng ÿӇ cҳt ÿiӋn tӯng băng tҧi trong trѭӡng hӧp cҫn sӱa chӳa. 2. S˯ ÿ͛ kh͙ng ch͇ ÿ˱ͥng cáp treo Khi thiӃt kӃ và chӑn sѫ ÿӗ ÿiӅu khiӇn hӋ truyӅn ÿӝng ÿѭӡng cáp treo chӫ yӃu dӵa vào chӃ ÿӝ làm viӋc cӫa nó. ChӃ ÿӝ làm viӋc cӫa ÿӝng cѫ truyӅn ÿӝng ÿѭӡng cáp treo thay ÿәi phө thuӝc vào ÿӝ nghiêng (ÿӝ dӕc) cӫa tuyӃn ÿѭӡng và phө tҧi cӫa các toa hàng. Trong trѭӡng hӧp chuyӇn ÿông ÿi lên, hӋ truyӅn ÿӝng làm viӋc ӣ chӃ ÿӝ ÿӝng cѫ, còn khi chuyӇn ÿӝng ÿi xuӕng ÿӝng cѫ làm viӋc ӣ chӃ ÿӝ máy phát, thӵc hiӋn hãm tái sinh có trҧ năng lѭӧng vӅ lѭӟi. Sѫ ÿӗ khӕng chӃ hӋ truyӅn ÿӝng ÿѭӡng cáp treo ÿѭӧc giӟi thiӋu trên hình 11-9. 193 Hình 11-9 Sѫ ÿӗ nguyên lý hӋ truyӅn ÿӝng ÿѭӡng cáp treo Ĉӝng cѫ truyӅn ÿӝng Ĉ truyӅn ÿӝng kéo ÿѭӡng cáp dùng ÿӝng cѫ không ÿӗng bӝ rôto dây quҩn. Khӣi ÿӝng ÿӝng cѫ thӵc hiӋn bҵng cách loҥi trӯ dҫn ÿiӋn trӣ phө trong mҥch rôto cӫa ÿӝng cѫ theo hàm thӡi gian gӗm tám cҩp nhӡ các rѫle thӡi gian 1RG ÷ 8RG. ĈiӅu khiӇn ÿӝng cѫ bҵng bӝ khӕng chӃ tӯ KC có tám tiӃp ÿiӇm K1 ÷ K8. Hҥn chӃ dùng khӣi ÿӝng cӫa ÿӝng cѫ bҵng rѫle dòng RD lҳp trong mҥch stato cӫa ÿӝng cѫ. - Bҧo vӋ quá dòng bҵng rѫle dòng ÿiӋn cӵc ÿҥi RDC và bҧo vӋ quá tӕc ÿӝ bҵng rѫle kiӇm tra tӕc ÿӝ RKT. - Hãm dӯng ÿӝng cѫ bҵng cѫ cҩu phanh hãm ÿiӋn tӯ NCH. - Bҧo vӋ ÿiӋn áp thҩp bҵng rѫle ÿiӋn áp RĈA .
File đính kèm:
giao_trinh_dien_cong_nghiep.pdf