Giáo trình Điều khiển lập trình cơ nhỏ (Phần 1)
1.Tổng quát về điều khiển lập trình.
* Định nghĩa, khái niệm điều khiển nối cứng và điều khiển lập trình.
- Hệ thống điều khiển công nghiệp được tạo ra từ một nhóm gồm các thiết
bị điện và điện tử, nó mang đến sự chính xác, hiện đại và tránh được các hư hại
trong sản xuất. Hệ thống điều khiển bao gồm nhiều dạng khác nhau, khác từ
nguồn năng lượng sử dụng, cách thức vận hành cho đến máy móc thiết bị. Hệ
thống điều khiển nối cứng là hệ thống sử dụng những bộ điểm tiếp rơle vào việc
điều khiển quá trình tự động vận hành các máy móc thiết bị, kèm theo đó là việc
sử dụng dây điện để kết nối chúng với nhau trong bảng điều khiển.
Do đó, hệ thống điều khiển nối cứng có nhiều nhược điểm như sau :
- Tốn khá nhiều công sức cho việc kết nối dây điện.
- Khó khăn cho việc thay thế và sửa chữa.
- Khó xác định lỗi nhanh chóng, muốn vậy đòi hỏi người thợ phải có kỹ
năng tay nghề cao.
- Khi có sự cố về điện, phải tạm ngưng sản xuất để xác định lỗi và tiến
hành sửa chữa.
- Nhu cầu về một bộ điều khiển dễ sử dụng, linh hoạt và có giá thành thấp
đã thúc đẩy sự phát triển những hệ thống điều khiển lập trình (programmable
control systems) – hệ thống sử dụng bộ vi xử lý (CPU) và bộ nhớ để điều khiển
máy móc hay quá trình. Bộ điều khiển lập trình ra đời nhằm thay thế hệ thống
điều khiển truyền thống dùng rơ-le và thiết bị rời cồng kềnh. Nó tạo ra khả năng
điều khiển thiết bị dễ dàng và linh hoạt dựa trên việc sử dụng các lệnh logic cơ
bản. Ngoài ra, các bộ lập trình còn có thể thực hiện những tác vụ khác như định3
thời, đếm làm tăng khả năng điều khiển cho những hoạt động phức tạp, ngay
cả với các bộ điều khiển lập trình nhỏ nhất.
Thiết bị điều khiển lập trình đầu tiên (Programmable Controller) đã được
những nhà thiết kế cho ra đời năm 1968 (công ty General Motor - Mỹ). Tuy
nhiên, hệ thống này còn khá đơn giản và cồng kềnh, người sử dụng gặp nhiều
khó khăn trong việc vận hành hệ thống . Vì vậy các nhà thiết kế từng bước cải
tiến hệ thống làm cho hệ thống đơn giản, gọn nhẹ, dễ vận hành. Nhưng việc lập
trình cho hệ thống còn khó khăn do lúc này không có các thiết bị lập trình
chuyên dùng hỗ trợ cho công việc lập trình. Để đơn giản hóa việc lập trình, hệ
thống điều khiển lập trình cầm tay (Programmable Controller Handle) đầu tiên
được ra đời vào năm 1969. Điều này đã tạo ra sự phát triển thực sự cho kỹ thuật
điều khiển lập trình. Các nhà thiết kế đã từng bước chuẩn hóa ngôn ngữ lập
trình, đó là ngôn ngữ lập trình dùng các khối hàm (FBD) và giản đồ hình thang
(Ladder Diagram). Các nhà sản xuất liên tục đưa ra các công cụ (cả phần mềm
và thiết bị) hỗ trợ cho việc lập trình, giám sát và gỡ rối.
Tóm tắt nội dung tài liệu: Giáo trình Điều khiển lập trình cơ nhỏ (Phần 1)
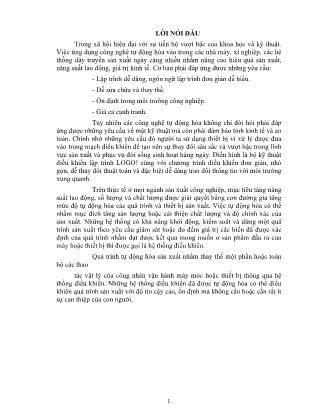
1 LỜI NÓI ĐẦU Trong xã hội hiện đại với sự tiến bộ vượt bậc của khoa học và kỹ thuật. Việc ứng dụng công nghệ tự động hóa vào trong các nhà máy, xí nghiệp, các hệ thống dây truyền sản xuất ngày càng nhiều nhằm nâng cao hiệu quả sản xuất, năng suất lao động, giá trị kinh tế. Cơ bản phải đáp ứng được những yêu cầu: - Lập trình dễ dàng, ngôn ngữ lập trình đơn giản dễ hiểu. - Dễ sửa chữa và thay thế. - Ổn định trong môi trường công nghiệp. - Giá cả cạnh tranh. Tuy nhiên các công nghệ tự động hóa không chỉ đòi hỏi phải đáp ứng được những yêu cầu về mặt kỹ thuật mà còn phải đảm bảo tính kinh tế và an toàn. Chính nhờ những yêu cầu đó người ta sử dụng thiết bị vi xử lý được đưa vào trong mạch điều khiển để tạo nên sự thay đổi sâu sắc và vượt bậc trong lĩnh vực sản xuất và phục vụ đời sống sinh hoạt hàng ngày. Điển hình là bộ kỹ thuật điều khiển lập trình LOGO! cùng với chương trình điều khiển đơn giản, nhỏ gọn, dễ thay đổi thuật toán và đặc biệt dễ dàng trao đổi thông tin với môi trường xung quanh. Trên thực tế ở mọi ngành sản xuất công nghiệp, mục tiêu tăng năng suất lao động, số lượng và chất lượng được giải quyết bằng con đường gia tăng mức độ tự động hóa các quá trình và thiết bị sản xuất. Việc tự động hóa có thể nhằm mục đích tăng sản lượng hoặc cải thiện chất lượng và độ chính xác của sản xuất. Những hệ thống có khả năng khởi động, kiểm soát và dừng một quá trình sản xuất theo yêu cầu giám sát hoặc đo đếm giá trị các biến đã được xác định của quá trình nhằm đạt được kết quả mong muốn ở sản phẩm đầu ra của máy hoặc thiết bị thì được gọi là hệ thống điều khiển. Quá trình tự động hóa sản xuất nhằm thay thế một phần hoặc toàn bộ các thao tác vật lý của công nhân vận hành máy móc hoặc thiết bị thông qua hệ thống điều khiển. Những hệ thống điều khiển đã được tự động hóa có thể điều khiển quá trình sản xuất với độ tin cậy cao, ổn định mà không cần hoặc cần rất ít sự can thiệp của con người. 2 BÀI 1: GIỚI THIỆU CHUNG VỀ BỘ ĐIỀU KHIỂN LẬP TRÌNH CƠ NHỎ 1.Tổng quát về điều khiển lập trình. * Định nghĩa, khái niệm điều khiển nối cứng và điều khiển lập trình. - Hệ thống điều khiển công nghiệp được tạo ra từ một nhóm gồm các thiết bị điện và điện tử, nó mang đến sự chính xác, hiện đại và tránh được các hư hại trong sản xuất. Hệ thống điều khiển bao gồm nhiều dạng khác nhau, khác từ nguồn năng lượng sử dụng, cách thức vận hành cho đến máy móc thiết bị. Hệ thống điều khiển nối cứng là hệ thống sử dụng những bộ điểm tiếp rơle vào việc điều khiển quá trình tự động vận hành các máy móc thiết bị, kèm theo đó là việc sử dụng dây điện để kết nối chúng với nhau trong bảng điều khiển. Do đó, hệ thống điều khiển nối cứng có nhiều nhược điểm như sau : - Tốn khá nhiều công sức cho việc kết nối dây điện. - Khó khăn cho việc thay thế và sửa chữa. - Khó xác định lỗi nhanh chóng, muốn vậy đòi hỏi người thợ phải có kỹ năng tay nghề cao. - Khi có sự cố về điện, phải tạm ngưng sản xuất để xác định lỗi và tiến hành sửa chữa. - Nhu cầu về một bộ điều khiển dễ sử dụng, linh hoạt và có giá thành thấp đã thúc đẩy sự phát triển những hệ thống điều khiển lập trình (programmable control systems) – hệ thống sử dụng bộ vi xử lý (CPU) và bộ nhớ để điều khiển máy móc hay quá trình. Bộ điều khiển lập trình ra đời nhằm thay thế hệ thống điều khiển truyền thống dùng rơ-le và thiết bị rời cồng kềnh. Nó tạo ra khả năng điều khiển thiết bị dễ dàng và linh hoạt dựa trên việc sử dụng các lệnh logic cơ bản. Ngoài ra, các bộ lập trình còn có thể thực hiện những tác vụ khác như định 3 thời, đếmlàm tăng khả năng điều khiển cho những hoạt động phức tạp, ngay cả với các bộ điều khiển lập trình nhỏ nhất. Thiết bị điều khiển lập trình đầu tiên (Programmable Controller) đã được những nhà thiết kế cho ra đời năm 1968 (công ty General Motor - Mỹ). Tuy nhiên, hệ thống này còn khá đơn giản và cồng kềnh, người sử dụng gặp nhiều khó khăn trong việc vận hành hệ thống . Vì vậy các nhà thiết kế từng bước cải tiến hệ thống làm cho hệ thống đơn giản, gọn nhẹ, dễ vận hành. Nhưng việc lập trình cho hệ thống còn khó khăn do lúc này không có các thiết bị lập trình chuyên dùng hỗ trợ cho công việc lập trình. Để đơn giản hóa việc lập trình, hệ thống điều khiển lập trình cầm tay (Programmable Controller Handle) đầu tiên được ra đời vào năm 1969. Điều này đã tạo ra sự phát triển thực sự cho kỹ thuật điều khiển lập trình. Các nhà thiết kế đã từng bước chuẩn hóa ngôn ngữ lập trình, đó là ngôn ngữ lập trình dùng các khối hàm (FBD) và giản đồ hình thang (Ladder Diagram). Các nhà sản xuất liên tục đưa ra các công cụ (cả phần mềm và thiết bị) hỗ trợ cho việc lập trình, giám sát và gỡ rối. 2. Cấu trúc của một bộ điều khiển LOGO. 2.1 Khái niệm về Logo: - Logo là module logic thế hệ mới của Siemens , là bộ điều khiển có khả năng lâp trình đơn giản có sẵn đầu vào và ra được ứng dụng cho các quy trình tự động hoá cỡ nhỏ. - Loại có màn hình LCD : Có màn hiển thị bằng LCD và các nút để thao tác cho phép lập trình bằng tay trực tiếp ngay trên Logo hoặc qua phần mềm lầp trình trên máy tính. - Loại không có màn hình LCD : Không có màn hiển thị và các nút để thao tác . Dùng phần mềm lập trình trên máy tính và nạp vào Logo để chạy, logo có thể nối thêm các module mở rộng. tới 4 đầu vào và 8 đầu ra. Logo có hai loại vói nguồn điện cung cấp 24V và 230V: - Loại bình thường có 6 đầu vào 4 đầu ra. - Loại lớn có 12 đầu vào 8 đầu ra. - Loại LB11 có 12 đầu vào 8 đầu ra có thể mở rông thêm 4 vào- 4 ra. 2.2 Sơ đồ khối bộ điều khiển LOGO. Thông thường, một bộ Logo thường có một số khối sau: 1. Nguồn 2. Đầu vào 3. Đầu ra 4. Module với nắp bao phủ 5. Panel điều khiển ( các khóa ) 6. Màn hiển thị LCD 4 7. AS kết nối giao diện. * Bảng thông số kỹ thuật của các họ Logo. B ản g 1.1: Thông số đặc tính của các họ LOGO 5 * Khả năng mở rộng của LOGO * Đối với version LOGO! 12/24 RC/RCo và LOGO! 24/24o: Khả năng mở rộng: 4 modul digital và 3 modul analog: Bản g 1.2: Thông số đặc tính mở rộng của các họ LOGO * Đối với version LOGO! 24 RC/RCo và LOGO! 230 RC/Rco: Khả năng mở rộng: 4 modul digital và 4 modul analog: B ảng 1.3: Thông số đặc tính mở rộng của các họ LOGO *Phương pháp kết nối LOGO. - Kết nối đầu vào số * Cách đấu dây họ LOGO!230: Hình 1.2: Sơ đồ đấu dây của họ LOGO!230. Việc đi dây cho các đầu vào được chia thành hai nhóm, mỗi nhóm 4 đầu vào. Các đầu vào trong cùng một nhóm chỉ có thể cấp cùng một pha điện áp. Các đầu vào trong hai nhóm có thể cấp cùng pha hoặc khác pha điện áp. * Cách đấu dây họ LOGO! AM2: 6 Hình 1.3: Sơ đồ đấu dây của họ LOGO! AM2 * Cách đấu dây họ LOGO! AM2 PT100 Hình 1.4: Sơ đồ đấu dây của họ LOGO! AM2 PT100 - Kết nối đầu ra số: * Đối với đầu ra dạng relay: Ta có thể kết nối nhiều dạng tải khác nhau vào đầu ra. Ví dụ: đèn, motor, contactor, relay Tải thuần trở: tối đa 10A Tải cảm: tối đa 3A. Sơ đồ kết nối như sau: 7 Hình 1.5: Sơ đồ đấu dây đầu ra relay của LOGO * Đối với đầu ra dạng transistor: Tải kết nối vào đầu ra của LOGO phải thoả điều kiện sau: dòng điện không vượt quá 0.3 A. Sơ đồ kết nối như sau: Hình 1.6: Sơ đồ đấu dây đầu ra Transistor của LOGO *Kết nối với modul analog output LOGO! AM 2 Hình 1.7: Sơ đồ đấu dây ra Analog của LOGO 8 BÀI 2 : CÁC CHỨC NĂNG CƠ BẢN CỦA LOGO. 1. Các cổng logic cơ bản. 1.1 Cổng AND – VÀ. * Sơ đồ nối thể hiện bằng tiếp diểm * Biểu tượng của hàm: * Bảng trạng thái: I1 I2 I3 Q 0 0 0 0 0 0 1 0 0 1 0 0 0 1 1 0 1 0 0 0 1 0 1 0 1 1 0 0 1 1 1 1 * Kết luận: - Đầu ra = 1 khi tất cả các đầu vào bằng 1. 9 - Đầu ra = 0 khi có một đầu vào = 0 1.2 Cổng OR – HOẶC . *Sơ đồ nối biểu hiện bằng tiếp điểm *Biểu tượng của hàm 10 * Bảng trạng thái : I1 I2 I3 Q 0 0 0 0 0 0 1 1 0 1 0 1 0 1 1 1 1 0 0 1 1 0 1 1 1 1 0 1 1 1 1 1 * Kết luận: - Đầu ra =1 khi có một trong các đầu vào =1. - Đầu ra =0 khi tất cả các đầu vào = 0 11 1.3 Cổng NOT – ĐẢO. *Sơ đồ nối biểu hiện bằng tiếp điểm * Biểu tượng của hàm * Bảng trạng thái. I Q 0 1 1 0 * Kết luận. - Đầu ra =1 khi đầu vào = 0 - Đầu ra =0 khi đầu vào =1 12 1.4 Cổng NAND – VÀ ĐẢO. *Sơ đồ nối biểu hiện bằng tiếp điểm. * Biểu tượng của hàm. * Bảng trạng thái : I1 I2 I3 Q 0 0 0 1 0 0 1 1 0 1 0 1 0 1 1 1 1 0 0 1 1 0 1 1 1 1 0 1 1 1 1 0 13 Hàm = 0 khi tất cả các dầu vào bằng 1. Hàm =1 khi có ít nhất một đầu vào của hàm =0 1.5 Cổng HOẶC- ĐẢO ( NOR ) * Sơ đồ nối biểu hiện bằng tiếp điểm. * Biểu tượng của hàm 14 * Bảng trạng thái: I1 I2 I3 Q 0 0 0 1 0 0 1 0 0 1 0 0 0 1 1 0 1 0 0 0 1 0 1 0 1 1 0 0 1 1 1 0 Hàm = 0 khi ít nhất có một đầu vào =1 Hàm =1 khi tất cả các đầu vào = 0. 15 1.6 Cổng HOẶC- LOẠI TRỪ ( XOR ). * Sơ đồ nối biểu hiện bằng tiếp điểm. * Biểu tượng của hàm. * Bảng trạng thái: I1 I2 Q 0 0 0 0 1 1 1 0 1 1 1 0 * Kết luận: Hàm = 0 khi các đầu vào có cùng giá trị 0 hoặc 1. 16 Hàm =1 khi các đầu vào có giá trị khác nhau. 1.7 Cổng AND with edge evaluation (Cổng AND lấy cạnh xung lên). *Biểu tượng của hàm. * Giản đồ thời gian. 17 Đầu vào không sử dụng ta có thể sử dụng ký hiệu x (x=1). Đầu ra bằng 1 trong 1 chu kỳ quét tại thời điểm đầu tiên mà tất cả các đầu vào cùng bằng 1. 18 1.8 Cổng NAND with edge evaluation (Cổng NAND lấy cạnh xung lên) *Biểu tượng của hàm. * Giản đồ thời gian. Đầu ra của cổng NAND lấy cạnh xung lên bằng 1 trong 1 chu kỳ máy tại thời điểm đầu tiên mà một trong các đầu vào bằng 0. 19 2. Các bài tập áp dụng * Kết nối cổng AND – OR. Bước1: Sơ đồ nguyên lý ( hình 2.1 ). Hình 2.1 Sơ đồ nguyên lý mạch AND-OR. * Quy trình làm việc - CT1 đóng – CT2 đóng → Đ sáng - CT1 đóng – CT2 Mở → Đ Tắt - CT3 đóng – CT4 đóng → Đ sáng - CT5 đóng – CT6 Mở → Đ Tắt - CT3 đóng – CT6 đóng → Đ sáng 20 - CT5 đóng – CT4 Mở → Đ Tắt Bước2:* Khai báo địa chỉ. - Địa chỉ đầu vào: I1 : CT1 ( công tắc ) I2 : CT2 I3 : CT3 I4 : CT4 I5 : CT5 I6 : CT6 - Địa chỉ đầu ra: Q1 : Đ (Đèn chiếu sáng) Bước 3: * Chương trình điều khiển. Bước 4:* Thuyết minh sơ đồ mạch LOGO I1 và I2 tác động Q1 tác động ( đèn sáng ). I3 và I4 tác động Q1 tác động ( đèn sáng ). I5 và I6 tác động Q1 tác động ( đèn sáng ). I1 , I5và I3 Không tác động Q1 không tác động ( đèn không sáng ). Bước 5: Download, chạy thử. 21 Bài tập số 1: Viết chương trình điều khiển mạch đèn chiếu sáng cầu thang nhà 2 tầng. Bước1: Sơ đồ nguyên lý ( hình 2.2 ). Hình 2.2. Sơ đồ nguyên lý mạch đèn cầu thang. * Quy trình làm việc. - Các công tắc CT1 và CT2 thao tác ở cùng vị trí đèn sáng. - Các công tắc CT1 và CT2 thao tác ở khác vị trí đèn tắt. Bước2:* Khai báo địa chỉ. - Địa chỉ đầu vào: I1 : CT1 ( công tắc tầng 1 ) I2 : CT2 ( công tắc tầng 2 ) 22 - Địa chỉ đầu ra: Q1 : Đ ( đèn chiếu sáng ) Bước 3: * Chương trình điều khiển. Bước 4:* Thuyết minh sơ đồ mạch LOGO. I1 tác động , I2 không tác động - Q1 tác động ( đèn sáng ) I1 không tác động , I2 tác động - Q1 tác động ( đèn sáng ) I1 tác động , I2 tác động - Q1 không tác động ( đèn tắt ) Bước 5: Download, chạy thử. Bài tập số 2: Viết chương trình điều khiển mạch đóng mở cổng. 23 Bước1: * Sơ đồ nguyên lý. Bước2:* Khai báo địa chỉ. - Địa chỉ đầu vào: I1 : Nút ấn điều khiển mở cổng. I2 : Nút ấn điều khiển dừng. I3 : Công tắc hành trình cuối mở cổng. I4 : Công tắc hành trình cuối đóng cổng. I5 : Nút dừng tổng. - Địa chỉ đầu ra: Q1 : Công tắc tơ điều khiển mở cổng. Q2 : Công tắc tơ điều khiển đóng cổng. Bước 3: * Chương trình điều khiển. Bước 4:* Thuyết minh sơ đồ mạch LOGO. - Ấn nút điều khiển mở cổng →I1 tác động , I2 không tác động - Q1 tác động ( đèn sáng ), → động cơ chạy thuận truyền động cho bộ phận mở cổng. Khi cổng chạy đến cuối hành trình thì cơ cấu cơ khí chạm vào công tắc hành trình cuối mở cổng → Q1 ngừng tác động ( đèn tắt) → động cơ ngừng→ cổng dừng tại chỗ. - Ấn nút điều khiển đóng cổng → I2 tác động , I1 không tác động - Q1 mất điện, Q2 tác động ( đèn sáng ) → động cơ chạy ngược truyền động cho bộ phận đóng cổng. Khi cổng chạy đến cuối hành trình thì cơ cấu cơ khí chạm vào công tắc hành trình cuối đóng cổng → Q2 ngừng tác động ( đèn tắt) → động cơ ngừng→ cổng dừng tại chỗ. 24 - Trong quá trình cổng đang đóng hoặc mở, nếu muốn dừng tại chỗ hoặc điều khiển bằng tay ta ấn nút dừng tổng → I5 tác động → Q1, Q2 mất điện ( đèn tắt ) → động cơ ngừng→ cổng dừng tại chỗ. Bước 5: Download, chạy thử. 25 26 BÀI 3: CÁC CHỨC NĂNG ĐẶC BIỆT CỦA LOGO. 1. Chức năng của các rơ le. 1.1 Rơle ON- delay. * Sơ đồ mạch và biểu tượng trong Logo. Trong đó: - Trg ( Input): Khởi động thời gian của on- delay. - T: Thời gian đặt để đầu ra chuyển trạng thái. - Q (Đầu ra):Tín hiệu tác động ở đầu ra tương ứng với thời gian đặt. Giản đồ thời gian ON DELAY. Hình 2.1: Giản đồ thời gian ON-DELAY Đặt thời gian cho ON-delay: 27 * Nguyên lý hoạt động. - Nếu kích hoạt đầu vào của ON-delay, thì rơle thời gian ON-delay bắt đầu hoạt động. Thời gian Ta được khởi động khi đầu vào Trg chuyển từ 0 lên 1. (Ta: thời gian hiện hành của LOGO). Nếu trạng thái đầu vào Trg duy trì mức 1 trong suốt khoảng thời gian T thì đầu ra Q được lên mức 1. Nếu đầu vào chuyển từ 1 xuống 0. Nếu trong khoảng thời gian T mà đầu vào chuyển từ 1 xuống 0 thì thì đầu ra cũng xuống 0 và timer bị reset. Nếu tính năng retentive không đươc set thì khi mất nguồn, đầu ra Q và thời gian Ta bị reset. 1.2 Rơle OFF- delay. *Sơ đồ mạch và biểu tượng trong logo. 28 Chức năng: Trg : Đầu vào khởi động thời gian Off- delay, tác động sườn âm của tín hiệu đầu vào Trg( chuyển trạng thái Trg từ 1 xuống 0). R : Tín hiệu reset bộ Off-delay và đặt đầu ra Q = 0 Par: Parameter, là khoảng thời gian đặt trễ T. Q : Đầu ra, sẽ chuyển từ mức logic 1 xuống 0 sau thời gian T kể từ khi đầu vào Trg xuống 0. Ta có giản đồ thời gian mô tả nguyên tắc làm việc của rơ le thời gian như sau Hình 2.2: Giản đồ thời gian của rơ le thời gian Off-delay Thời gian Ta được khởi động khi đầu vào Trg chuyển từ 1 xuống 0. ( Ta: thời gian hiện hành của LOGO). Nếu trong khoảng thời gian T mà có tín hiệu reset R thì cả Q và Ta đều xuống mức 0. Q Ta TT R Trg Q Trg R T 29 1.3 Rơle ON-OFF- delay. * Biểu tượng trong Logo. * Đặt thời gian trễ. Giản đồ thời gian ON-OFF DELAY. Hình 2.3: Giản đồ thời gian ON-OFF DELAY * Nguyên lý hoạt động: Thời gian TH được khởi động khi đầu vào Trg chuyển từ 0 lên 1. Nếu ngõ Trg được giữ cho đến hết thời gian TH thì đầu ra Q sẽ được set lên 1. Thời gian TH sẽ bị reset khi đầu vào Trg chuyển xuống mức 0 khi chưa hết thời gian TH. Sự chuyển mức từ 1 xuống 0 sẽ khởi động TL . Nếu ngõ Trg được giữ cho đến hết thời gian TL thì đầu ra Q sẽ được reset về 0. 30 Thời gian TL sẽ bị reset khi đầu vào Trg chuyển lên mức 1 khi chưa hết thờigian TL. Nếu tính năng retentive không đươc chọn thì khi mất nguồn, đầu ra Q và thờigian TH, TL bị reset. 1.4 Latching relay. * Sơ đồ mạch và biểu tượng trong ... 1, K và KY có mức logic là 1, K là 0. Sau một thời gian, K chuyển từ 0 sang 1, KY chuyển từ 1 sang 0. Khi ấn D hoặc RN, tín hiệu của chúng chuyển từ 1 sang 0 dẫn đến K, KY, K chuyển từ 1 sang 0. Vì vậy, ta có giản đồ thời gian quan hệ các tín hiệu M, D, RN, K, KY, K như hình 4.30. Hình 4.30: Giản đồ thời gian biểu diễn quan hệ giữa các đại lượng + Quan hệ logic của tín hiệu đầu vào và đầu ra như sau: Từ giản đồ thời gian hình 4.30ta thấy: khi tín hiệu đầu vào D bằng 1 and RN bằng 1 and M bằng 1 thì tín hiệu ra K và KY bằng 1. Tuy nhiên, tín hiệu M là không chắc chắn, chỉ là 1 trong khi ấn M và khi dừng ấn thì trở về 0. Nên tín hiệu ra K được dùng để hỗ trợ cho tín hiệu M. Vậy hàm thuật toán logic của biến đầu ra K là: .( ).KF D M K RN Khi K có mức lô gic là 1 thì lệnh tạo thời gian trễ Rth bắt đầu đếm, nên hàm logic của biến tạo thời gian trễ là: FRth = K Sau thời gian trễ T thì lệnh tạo thời gian trễ Rth tác động, dẫn đến KY chuyển từ 0 sang 1. Vậy hàm logic của biến đầu ra KY là: .KYF K Rth Đồng thời, khi Rth tác động thì Khi tín hiệu K∆ chuyển từ 0 sang 1. Vậy hàm logic của biến đầu ra K∆ là: KF Rth * Bước 2: Khai báo địa chỉ đầu vào- đầu ra. 85 - Địa chỉ đầu vào I1 : M1 ( nút ấn mở máy, thường mở. ) I2 : D ( nút dừng động cơ – Thường đóng ) I3 : RN ( tiếp điểm thường đóng của rơle nhiệt để bảo vệ quá tải động cơ ) - Địa chỉ đầu ra Q1 : K1 ( cuộn dây của công tắc tơ K ) Q2 : K2 ( cuộn dây của công tắc tơ KY ) Q3 : K3 ( cuộn dây của công tắc tơ K∆ ) * Bước 3 : Chương trình điều khiển mạch điều khiển. Trên cơ sở Quy trình làm việc, giản đồ thời gian và địa chỉ vào/ra ta tiến hành viết chương trình trên phần mềm Logo ! soft như sau: - Phương pháp 1 : sử dụng các hàm cơ bản. - Phương pháp 2: sử dụng các hàm cơ bản và hàm ghi xóa. 86 * Bước 4: Kết nối cơ cấu chấp hành, nạp chương trình chạy cơ cấu chấp hành. Với Logo ! có các tín hiệu vào 220V xoay chiều, cổng ra rơ le, ta kết nối với cơ cấu chấp hành theo sơ đồ sau. Hình 4.31: Kết nối Logo ! với cơ cấu chấp hành . K1 Q1 K3 Q3 220V L AI2I4 K2 I1 I3 Q4 AI1 RN 0V 220V M 0V I5M Q2 D I2 I6 87 Mạch kết nối với ngoại vi : + Đầu vào nút ấn thưởng mở M , nút ấn thường kín D , tiếp điểm thường kín RN. + Đầu ra nối tới 3 cuộn dây công tắc tơ K1, K2, K3. - Nạp chương trình chạy cơ cấu chấp hành Sau khi thực hiện việc kết nối Logo ! với ngoại vi, ta tiến hành down load chương trình đã viết trên máy tính xuống Logo ! và chạy cơ cấu chấp hành . 2.3.4. Mạch điều khiển 2 động cơ 3 pha làm việc theo trình tự. D1. Mạch điều khiển hai động cơ làm việc tuần tự bằng bộ nút bấm. * Bước 1: Phân tích quy trình làm việc. - Xác định quy trình làm việc của phụ tải : Chúng ta xác định quy trình làm việc của phụ tải thông qua mạch động lực và điều khiển 2 động cơ 3 pha làm việc tuần tự, dùng nút bấm như sau : Hình 4.32: Mạch động lực, điều khiển 2 động cơ làm việc tuần tự bằng bộ nút bấm. - Quy trình làm việc được mô tả như sau : + Ấn M1 (3;5) Công tắc tơ K1 (7;4) có điện, tiếp điểm thường mở K1(3;5) đóng lại duy trì, tiếp điểm thường mở K1 (9;11) đóng chuẩn bị cấp nguồn cho CTT K2. Các tiếp điểm K1 (2;8), (4;10), (6;12) trên mạch động lực đóng lại cấp nguồn cho động cơ M khởi động động cơ M1 làm việc, tiếp điểm thường mở K1 (6;17) đóng lại, đèn xanh sáng báo động cơ 1 làm việc. 88 + Ấn M2(11;13) CTT K2 (13;4) có điện các tiếp điểm thường mở K2(11;13) (6;23) đóng lại duy trì. Đồng thời các tiếp điểm mạch động lực K2 (14;20), (16;22), (18;24) đóng động cơ 2 làm việc, tiếp điểm thường mở K2 (6;19) đóng lại, đèn vàng sáng báo động cơ 2 làm việc + Muốn dừng động cơ ta ấn nút D. + Bảo vệ quá tải cho động cơ dùng rơ le nhiệt RN. + Để bảo vệ ngắn mạch ta dùng Aptomat TA + Nếu động cơ 1 chưa làm việc, ta điều khiển chạy động cơ 2 thì động cơ 2 không thể làm việc do bị khóa bởi tiếp điểm K1 * Xác định mối quan hệ logic của tín hiệu đầu vào và đầu ra : - Lựa chọn thiết bị điều khiển: Nút ấn M1 , M2: thường mở Nút ấn D: thường đóng. Tiếp điểm rơ le nhiệt RN: thường đóng Sơ đồ kết nối với như sau: Hình 4.33: Sơ đồ lựa chọn kết nối tín hiệu điều khiển với CPU Ta có quan hệ lô gic của tín hiệu vào/ra theo giản đồ thời gian sau : 89 Hình 4.34: Giản đồ thời gian biểu diễn quan hệ giữa các đại lượng. * Bước 2: Khai báo địa chỉ đầu vào- đầu ra. - Địa chỉ đầu vào I1 : M ( nút ấn mở máy, thường mở. ) I2 : D( nút dừng động cơ – Thường đóng ) I3 : RN ( tiếp điểm thường đóng của rơle nhiệt để bảo vệ quá tải động cơ) Q1 : K1 ( cuộn dây của công tắc tơ K1 ) Q2 : K2 ( cuộn dây của công tắc tơ K2 ) * Bước 3 : Chương trình điều khiển mạch điều khiển. Trên cơ sở Quy trình làm việc, giản đồ thời gian và địa chỉ vào/ra ta tiến hành viết chương trình trên phần mềm Logo ! soft như sau: - Phương pháp 1: sử dụng các hàm cơ bản. 90 - Phương pháp 1: sử dụng các hàm cơ bản và hàm ghi xóa. * Bước 4: Kết nối cơ cấu chấp hành, nạp chương trình chạy cơ cấu chấp hành. - Kết nối cơ cấu chấp hành : Với Logo ! có các tín hiệu vào 220V xoay chiều, cổng ra rơ le, ta kết nối với cơ cấu chấp hành theo sơ đồ sau. Hình 4.35: Kết nối Logo ! với cơ cấu chấp hành. 91 - Nạp chương trình chạy cơ cấu chấp hành Sau khi thực hiện việc kết nối Logo ! với ngoại vi, ta tiến hành down load chương trình đã viết trên máy tính xuống Logo ! và chạy cơ cấu chấp hành . D2. Mạch điều khiển hai động cơ làm việc tuần tự theo thời gian. * Bước 1: Phân tích quy trình làm việc. - Xác định quy trình làm việc của phụ tải : Chúng ta xác định quy trình làm việc của phụ tải thông qua mạch động lực và điều khiển 2 động cơ 3 pha làm việc tuần tự, dùng rơ le thời gian như sau : Hình 4.36: Mạch động lực, điều khiển 2 động cơ làm việc tuần tự . - Quy trình làm việc : - Quy trình làm việc được mô tả như sau : + Ấn M1 (3;5) Công tắc tơ K1 (7;4) có điện, tiếp điểm thường mở K1(3;5) đóng lại duy trì, đồng thời rơle thời gian có điện, chuẩn bị cấp nguồn cho CTT K2. Các tiếp điểm K1 (2;8), (4;10), (6;12) trên mạch động lực đóng lại cấp nguồn cho động cơ M khởi động động cơ M1 làm việc, tiếp điểm thường mở K1 (6;15) đóng lại, đèn xanh sáng báo động cơ 1 làm việc. + Sau thời gian chỉnh định của rơle thời gian, tiếp điểm T1(9 ;11) đóng lại CTT K2 (13;4) có điện các tiếp điểm thường mở K2(11;9) đóng lại duy trì. Đồng thời các tiếp điểm mạch động lực K2 (14;20), (16;22), (18;24) đóng động cơ 2 làm việc, tiếp điểm thường mở K2 (6;17) đóng lại, đèn vàng sáng báo động cơ 2 làm việc + Muốn dừng động cơ ta ấn nút D. + Bảo vệ quá tải cho động cơ dùng rơ le nhiệt RN. 92 + Để bảo vệ ngắn mạch ta dùng Aptomat TA + Nếu động cơ 1 chưa làm việc, ta điều khiển chạy động cơ 2 thì động cơ 2 không thể làm việc do bị khóa bởi tiếp điểm T1 + Ấn D dừng máy. * Xác định mối quan hệ logic của tín hiệu đầu vào và đầu ra : - Lựa chọn thiết bị điều khiển: Nút ấn M: thường mở Nút ấn D: thường đóng. Tiếp điểm rơ le nhiệt RN: thường đóng Sơ đồ kết nối với như sau: Hình 4.37: Sơ đồ lựa chọn kết nối tín hiệu điều khiển với CPU Ta có quan hệ lô gic của tín hiệu vào/ra theo giản đồ thời gian sau : 93 Hình 4.38: Giản đồ thời gian biểu diễn quan hệ giữa các đại lượng. * Bước 2: Khai báo địa chỉ đầu vào- đầu ra. - Địa chỉ đầu vào I1 : M ( nút ấn mở máy, thường mở. ) I2 : D( nút dừng động cơ – Thường đóng ) I3 : RN ( tiếp điểm thường đóng của rơle nhiệt để bảo vệ quá tải động cơ) Q1 : K1 ( cuộn dây của công tắc tơ K1 ) Q2 : K2 ( cuộn dây của công tắc tơ K2 ) * Bước 3 : Chương trình điều khiển mạch điều khiển. Trên cơ sở Quy trình làm việc, giản đồ thời gian và địa chỉ vào/ra ta tiến hành viết chương trình trên phần mềm Logo ! soft như sau: - Phương pháp 1: sử dụng các hàm cơ bản. 94 - Phương pháp 2: sử dụng các hàm cơ bản và hàm ghi xóa. * Bước 4: Kết nối cơ cấu chấp hành, nạp chương trình chạy cơ cấu chấp hành. - Kết nối cơ cấu chấp hành : Với Logo ! có các tín hiệu vào 220V xoay chiều, cổng ra rơ le, ta kết nối với cơ cấu chấp hành theo sơ đồ sau. Hình 4.39: Kết nối Logo ! với cơ cấu chấp hành . 95 - Nạp chương trình chạy cơ cấu chấp hành Sau khi thực hiện việc kết nối Logo ! với ngoại vi, ta tiến hành down load chương trình đã viết trên máy tính xuống Logo ! và chạy cơ cấu chấp hành . 2.3.5. Mô hình mạch điện động cơ 2 cấp tốc độ. E1. Mạch điện thay đổi tốc độ ∆/YY bằng nút bấm. * Bước 1: Phân tích quy trình làm việc. - Xác định quy trình làm việc của phụ tải : Chúng ta xác định quy trình làm việc của phụ tải thông qua mạch động lực và điều khiển động cơ thay đổi tốc độ với hai cấp tốc độ bằng nút bấm như sau: Hình 4.40: Mạch động lực điều khiển động cơ hai cấp tốc độ bằng bộ nút bấm Mạch hoạt động như sau : + Cấp nguồn cho mạch điện : Đóng AP. + Chạy tốc độ thấp: Ấn M1(3;5) Công tắc tơ K1 (9;4) có điện, tiếp điểm thường mở K1 (3;5) đóng lại duy trì, đèn xanh sáng, tiếp điểm thường đóng K1 (13;15) mở ra khống chế khoá chéo K2, K3 (15;4). Đồng thời các tiếp điểm mạch động lực K1 (2;8), (4;10), (6;12) đóng cấp nguồn cho động cơ M làm việc ở chế độ nối bộ dây. + Chạy tốc độ cao: Ấn M2 (5;7) Công tắc tơ K1 (9;4) mất điện, tiếp điểm thường đóng K1 (13;15) đóng lại. Công tắc tơ K2, K3 (15;4) có điện, tiếp điểm thường mở K2(11;13) đóng lại duy trì, (đèn vàng sáng), tiếp điểm thường 96 đóng K2(7;9) mở ra khống chế khoá chéo tốc độ thấp. Đồng thời tiếp điểm mạch động lực K2 (2;26), (4;24), (6;22), K3 (14;20), (16;20), (18;20) đóng, động cơ M chuyển sang làm việc với chế độ nối YY bộ dây. + Dừng máy: Muốn dừng máy ấn D ngắt điện toàn mạch điều khiển, động cơ dừng hoạt động. Muốn kết thúc quá trình làm việc ta ngắt AP + Thiết bị bảo vệ: Khi xảy ra quá tải, tùy vào tốc độ làm việc của động cơ ( tương ứng với chế độ đấu ∆ hoặc YY) rơle nhiệt RN1, RN2 tác động, tiếp điểm thường đóng RN(8;N) mở ra ngắt mạch điều khiển. Khi có sự cố ngắn mạch AP tác động, cắt điện toàn bộ hệ thống. * Xác định mối quan hệ logic của tín hiệu đầu vào và đầu ra : - Lựa chọn thiết bị điều khiển: Nút ấn M1 , M2: thường mở Nút ấn D: thường đóng. Tiếp điểm rơ le nhiệt RN: thường đóng Sơ đồ kết nối với như sau: Hình 4.41: Sơ đồ lựa chọn kết nối tín hiệu điều khiển với CPU Ta có quan hệ lô gic của tín hiệu vào/ra theo giản đồ thời gian sau : 97 Hình 4.1: Giản đồ thời gian biểu diễn quan hệ giữa các đại lượng. * Bước 2: Khai báo địa chỉ đầu vào- đầu ra. - Địa chỉ đầu vào I1 : M1 ( nút ấn mở máy, thường mở. ) I2 : M2 ( nút ấn mở máy, thường mở. ) I3 : D( nút dừng động cơ – Thường đóng ) I4 : RN ( tiếp điểm thường đóng của rơle nhiệt để bảo vệ quá tải động cơ) Q1 : K1 ( cuộn dây của công tắc tơ K1, động cơ chạy tốc độ thấp ) Q2 : K2 ( cuộn dây của công tắc tơ K2 , động cơ chạy tốc độ cao) Q3 : K3 ( cuộn dây của công tắc tơ K3 , động cơ chạy tốc độ cao) * Bước 3 : Chương trình điều khiển mạch điều khiển. Trên cơ sở Quy trình làm việc, giản đồ thời gian và địa chỉ vào/ra ta tiến hành viết chương trình trên phần mềm Logo ! soft như sau: - Phương pháp 1: sử dụng các hàm cơ bản. 98 - Phương pháp 2: sử dụng các hàm cơ bản và hàm ghi xóa. * Bước 4: Kết nối cơ cấu chấp hành, nạp chương trình chạy cơ cấu chấp hành. - Kết nối cơ cấu chấp hành : Với Logo ! có các tín hiệu vào 220V xoay chiều, cổng ra rơ le, ta kết nối với cơ cấu chấp hành theo sơ đồ sau. 99 Hình 4.2: Kết nối Logo ! với cơ cấu chấp hành . - Nạp chương trình chạy cơ cấu chấp hành Sau khi thực hiện việc kết nối Logo ! với ngoại vi, ta tiến hành down load chương trình đã viết trên máy tính xuống Logo ! và chạy cơ cấu chấp hành . E2. Mạch điện thay đổi tốc độ ∆/YY có khống chế thời gian. * Bước 1: Phân tích quy trình làm việc. - Xác định quy trình làm việc của phụ tải : Chúng ta xác định quy trình làm việc của phụ tải thông qua mạch động lực và điều khiển động cơ thay đổi tốc độ với hai cấp tốc độ như sau: 100 Hình 4.3: Mạch động lực, điều khiển động cơ thay đổi tốc độ với 2 cấp tốc độ. - Quy trình làm việc : + Cấp nguồn cho mạch điện : Đóng AP. + Chạy tốc độ thấp: Ấn M Công tắc tơ K1 (A;5) có điện, tiếp điểm thường mở K1 (1;3) đóng lại duy trì, đèn xanh sáng, tiếp điểm thường đóng K1 (1;6) mở ra khống chế khoá chéo K2, K3 (1;6) Đồng thời các tiếp điểm mạch động lực K1 (2;8), (4;10), (6;12) đóng cấp nguồn cho động cơ M làm việc ở chế độ nối ∆ bộ dây. + Chạy tốc độ cao: Khi công tắc tơ K1 (A;5) có điện, tiếp điểm thường mở K1 (1;3) đóng lại duy trì đồng thời rơle thời gian T(2;7) có điện. Sau thời gian đặt tiếp điểm thường đóng mở chậm T(5;8) mở ra công tắc tơ K1 (A;5) mất điện, tiếp điểm thường đóng K1 (1;6) đóng lại. Tiếp điểm thường mở đóng chậm T(6;8) đóng lại Công tắc tơ K2, K3 (1;6) có điện (đèn vàng sáng), tiếp điểm thường đóng K2(A;5) mở ra khống chế khoá chéo tốc độ thấp. Đồng thời tiếp điểm mạch động lực K2 (2;18), (4;16), (6;14), K3 (8;20), (10;20), (12;20) đóng động cơ M chuyển sang làm việc với chế độ nối YY bộ dây. + Dừng máy: Muốn dừng máy ấn D ngắt điện toàn mạch điều khiển, động cơ dừng hoạt động. Muốn kết thúc quá trình làm việc ta ngắt AP + Thiết bị bảo vệ: Khi xảy ra quá tải, tùy vào tốc độ làm việc của động cơ ( tương ứng với chế độ đấu ∆ hoặc YY) rơle nhiệt RN1, RN2 tác động, tiếp điểm thường đóng RN(8;N) mở ra ngắt mạch điều khiển. Khi có sự cố ngắn mạch AP tác động, cắt điện toàn bộ hệ thống. * Xác định mối quan hệ logic của tín hiệu đầu vào và đầu ra : - Lựa chọn thiết bị điều khiển: Nút ấn M: thường mở 101 Nút ấn D: thường đóng. Công tắc hành trình: thường đóng. Tiếp điểm rơ le nhiệt RN: thường đóng Sơ đồ kết nối với như sau: Hình 4.42: Sơ đồ lựa chọn kết nối tín hiệu điều khiển với CPU Ta có quan hệ lô gic của tín hiệu vào/ra theo giản đồ thời gian sau : Hình 4.43: Giản đồ thời gian biểu diễn quan hệ giữa các đại lượng. 102 * Bước 2: Khai báo địa chỉ đầu vào- đầu ra. - Địa chỉ đầu vào I1 : M ( nút ấn mở máy, thường mở. ) I2 : D( nút dừng động cơ – Thường đóng ) I3 : RN ( tiếp điểm thường đóng của rơle nhiệt để bảo vệ quá tải động cơ) Q1 : K1 ( cuộn dây của công tắc tơ K1 ) Q2 : K2 ( cuộn dây của công tắc tơ K2 ) Q3 : K3 ( cuộn dây của công tắc tơ K3 ) * Bước 3 : Chương trình điều khiển mạch điều khiển. Trên cơ sở Quy trình làm việc, giản đồ thời gian và địa chỉ vào/ra ta tiến hành viết chương trình trên phần mềm Logo ! soft như sau: - Phương pháp 1: sử dụng các hàm cơ bản. - Phương pháp 2: sử dụng các hàm cơ bản và hàm ghi xóa. 103 * Bước 4: Kết nối cơ cấu chấp hành, nạp chương trình chạy cơ cấu chấp hành. - Kết nối cơ cấu chấp hành : Với Logo ! có các tín hiệu vào 220V xoay chiều, cổng ra rơ le, ta kết nối với cơ cấu chấp hành theo sơ đồ sau. Hình 4.44: Kết nối Logo ! với cơ cấu chấp hành . K1 Q1 K3 Q3 220V L AI2I4 K2 I1 I3 Q4 AI1 RN 0V 220V M 0V I5M Q2 D I2 I6 104 - Nạp chương trình chạy cơ cấu chấp hành Sau khi thực hiện việc kết nối Logo ! với ngoại vi, ta tiến hành down load chương trình đã viết trên máy tính xuống Logo ! và chạy cơ cấu chấp hành .
File đính kèm:
giao_trinh_dieu_khien_lap_trinh_co_nho_phan_1.pdf